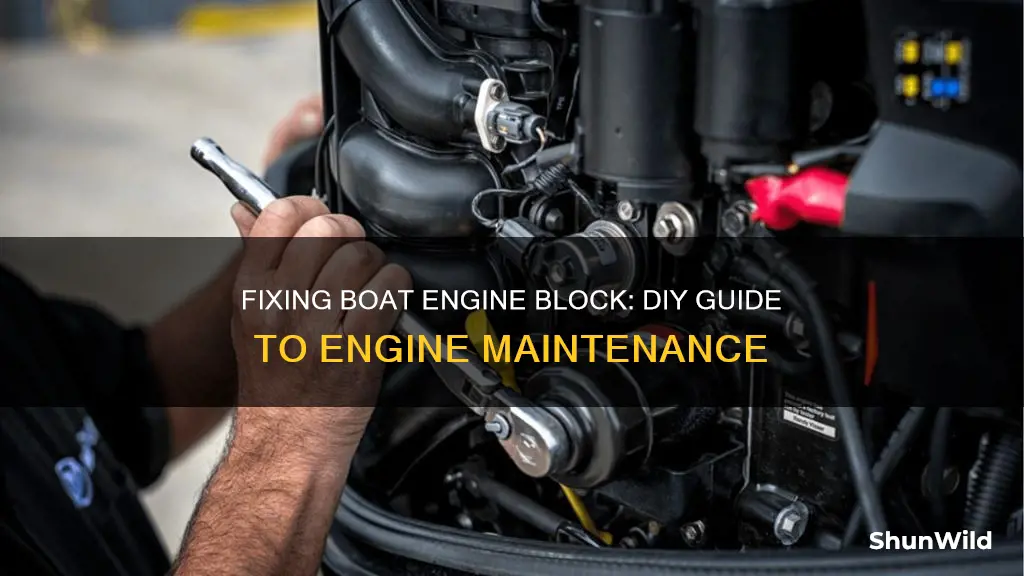
A cracked engine block is a serious issue that can affect the performance of your boat. While cracks in the engine block may not be common, they are among the most devastating problems boats face, especially older ones. If left unresolved, a cracked engine block can lead to poor efficiency due to a decrease in combustion pressure. This article will explore the signs of a cracked engine block and provide an overview of potential repair options, including welding, epoxy, and replacement.
Characteristics | Values |
---|---|
Signs of a cracked engine block | Engine smoke in the boat cabin, leaking oil or coolant, cloudy (discoloured) oil, poor fuel efficiency |
Causes of a cracked engine block | Excess heat, poor storage, faulty water pump, manufacturer error |
Fixing a cracked engine block | Welding, pinning, gluing, epoxy, replacement |
What You'll Learn
Welding cast iron
Step 1: Engine Disassembly
First, the engine must be disassembled to access the bare block. This step is crucial as it ensures that the welding process is focused only on the affected area.
Step 2: Preheating the Block
Cast iron needs to be heated to a specific temperature range before welding. The recommended temperature is around 300 to 700 degrees Fahrenheit. This preheating step is essential to prevent cracking caused by rapid temperature changes.
Step 3: Welding Technique
When welding cast iron, it is important to use the correct welding technique and consumables. One common method is to use a stick welder with special electrodes designed for cast iron welding, such as those with high nickel content. It is also crucial to gradually apply weld beads and allow the part to cool between passes to avoid large temperature swings.
Step 4: Peening Technique
Utilising the "peening" technique can be beneficial when welding cast iron. This involves tapping the freshly welded joint with a ball peen hammer to flatten the weld and seal the bond, enhancing the strength of the weld.
Step 5: Controlled Cooling
After welding, it is crucial to allow the engine block to cool slowly and naturally. Do not force rapid cooling as it may cause additional stress and cracking. Covering the block with heat-retaining blankets can help achieve a controlled cooling rate.
Step 6: Final Assembly
Once the welded area has cooled completely, the engine can be reassembled. Ensure that all components are properly torqued and secured before starting the engine.
It is important to note that welding cast iron requires experience and skill. It is always recommended to consult a professional welder with expertise in cast iron welding to ensure a safe and effective repair. Additionally, consider comparing the cost of welding with the cost of replacing the engine block to make an informed decision.
Exploring Sailing Boat Laws in Biscayne Bay
You may want to see also
Using epoxy to seal cracks
If you want to try using epoxy to seal cracks in your boat engine block, there are a few steps you should follow. First, park your vehicle on a flat surface and engage the parking brake. Turn off the engine and wait for one to two hours for it to cool. Then, locate the cracked area of the block. Use a wire brush to remove any paint or rust from the area around the crack, at least one to two inches away from the crack in all directions. Wipe away all paint, rust, and dust from the crack and the surrounding area. Apply rubbing alcohol to a clean rag and wipe down the entire area, including inside the crack. Wait a few minutes for the alcohol to dry.
Next, you will need to mix your epoxy. For JB Weld Epoxy, squeeze half a tube of resin and then half a tube of hardener onto a clean surface. Use a stir stick to mix the two components until the epoxy is one colour. Slide a flat scraper under the mixed epoxy and spread it into the crack, pressing downward to force the epoxy into the crack. Apply the remaining epoxy to the one- to two-inch area around the crack, pressing it into the crack and the surrounding area. Leave the epoxy to harden overnight.
The following day, inspect the hardened epoxy to ensure it has set around the crack. Crank the engine and let it heat up to operating temperature. Inspect the epoxy again to ensure it stays welded to the block. Turn the engine off.
It is important to note that this is a temporary fix and that if the epoxy is not mixed or applied properly, it will not work. You should also regularly check the epoxy to ensure it remains hardened to the block.
Carnival Pride: A Fun and Fabulous Cruise Experience?
You may want to see also
Drilling and tapping holes
Tools Required:
- Tap and die set: This includes taps and dies for various thread sizes.
- Drill bits: Ensure you have drill bits that match the tap size for precise holes.
- Drill: Depending on the project complexity, you may need a hand drill or a drill press.
- Rotation tools: T-style handle, specific holders, or a ratchet for rotating the tap.
- Lubrication: Use cutting fluid, rapid tap, or motor oil for a smooth operation.
- Center punch and hammer: These are used to mark the drilling spot and prevent the drill from wandering.
Understanding Bolt Anatomy:
Before drilling and tapping, it is crucial to understand the design of a bolt. Familiarize yourself with the major and minor diameters, thread diameter, crest, thread angle, and pitch. This knowledge will help you select the appropriate tap and drill bit for the job.
Step-by-Step Process:
Prepping the Workpiece:
- Use a center punch and hammer to mark the drilling spot.
- Consider deburring the hole for a smoother drilling experience.
Choosing the Right Drill Bit:
- Refer to a tap-and-die chart to find the correct drill bit size.
- Ensure the drill bit matches the tap size for optimal thread engagement.
- Apply lubrication to the drill bit before drilling.
- Maintain a low speed, especially with larger drill bits, to prevent overheating.
Drilling the Hole:
- Drill the hole, keeping the drill perpendicular to the surface.
- Apply tapping fluid to the tap.
- Use a T-handle or other rotation tools to rotate the tap into the hole slowly and steadily.
- Back off periodically to clear chips and lubricate the tap.
Cleaning the Threads:
Use brake clean or a similar solution to remove oil and metal chips from the threads.
Tapping on a Drill Press:
For larger projects or when precision is crucial, a drill press can be used. Securely clamp the workpiece, drill the hole, and then use the drill press to tap with controlled speed and torque.
Tips for Beginners:
If you are new to drilling and tapping, here are the bare minimum tools you will need: a center punch, tap, drill, a means to rotate the drill bit (such as a T-handle), and lubrication. Investing in a complete tap-and-die kit will offer versatility for various projects.
Best Practices and Considerations:
When drilling and tapping, it is important to choose the appropriate tap and drill bit sizes based on the thread standard, material compatibility, hole diameter, and thread depth. Failure to consider these parameters may lead to structural instability and functional inefficiency. Additionally, ensure that you use enough lubrication during the process to reduce friction and heat, which can affect the quality of the threads and the lifespan of your tools.
A Weekend in Panama City: Me and the Boys on a Boat
You may want to see also
Replacing the engine block
Step 1: Assess the Damage
Before deciding to replace the engine block, it is crucial to determine the extent of the damage. In some cases, cracks in the engine block may be repairable without the need for a replacement. Minor cracks can be sealed to prevent coolant or oil leaks. However, if the cracks are severe, replacing the engine block may be the only viable option.
Step 2: Seek Professional Advice
Consulting a professional boat mechanic or diesel engine expert is highly recommended, especially if you are unsure about the condition of your engine block. They can provide valuable insights and help you make an informed decision. Professionals can also identify any underlying issues that may have contributed to the problem.
Step 3: Prepare for the Replacement
If you decide to replace the engine block, it is important to gather the necessary tools and resources. This may include purchasing a new or used engine block, as well as any additional components required for the replacement. Ensure that you have a suitable work area and all the necessary safety equipment.
Step 4: Disconnect and Remove the Old Engine Block
Before removing the old engine block, carefully disconnect all attached components, such as the drive, steering, and exhaust manifolds. This process can be complex, and it is important to refer to a shop manual or seek assistance from someone with hands-on experience. Completely draining the engine of fluids and removing the pistons and crankshaft may also be necessary.
Step 5: Install the New Engine Block
Once the old engine block is removed, carefully position and install the new engine block, ensuring all connections are secure. Refer to the engine manual or seek guidance from an experienced individual to ensure proper installation.
Step 6: Reassemble and Test
After installing the new engine block, carefully reassemble all the components that were previously disconnected. Check for any fluid leaks and ensure that all parts are securely fastened. Finally, test the engine to ensure it is functioning correctly.
Benefits of Replacing the Engine Block:
- Improved Performance: A newer engine block can enhance power and efficiency, resulting in a smoother and faster ride.
- Increased Fuel Efficiency: Modern engine blocks are designed to be more fuel-efficient, potentially saving you money on fuel costs.
- Easier Maintenance: Replacing the engine block can simplify routine maintenance and help keep your boat in top condition.
- Extended Engine Lifespan: A new engine block can prolong the lifespan of your boat, allowing you to enjoy many more years of boating.
Remember to consult experts, carefully plan each step, and prioritize safety throughout the replacement process.
Boat Broker Licensing: Which States Require It?
You may want to see also
Troubleshooting engine issues
One of the most devastating problems boats face, especially older ones, is a cracked engine block. This can lead to poor engine efficiency and decreased combustion pressure. Some symptoms of a cracked engine block include visible engine smoke, engine overheating, and compromised performance, including decreased engine power and increased fuel consumption.
If you suspect a cracked engine block, it is essential to act quickly to prevent further damage. One way to troubleshoot a cracked engine block is to check the colour of the oil. If the oil appears milky-white, it indicates that the antifreeze has mixed with the oil due to a crack in the engine block.
Another way to check for a cracked engine block is to look for signs of oil leaks. The leak can be internal or external, depending on the location of the damage. Even a small oil leak should not be ignored, as it could indicate a larger problem.
If you have confirmed that your boat has a cracked engine block, there are several possible repair options. Minor cracks can sometimes be repaired by pinning, gluing, or welding the crack shut. However, it is important to consult a professional to determine the best course of action, as not all cracks are repairable, and attempting to repair a cracked engine block without the proper knowledge can result in further damage.
In some cases, the best option may be to replace the engine block or install a new engine. This can be a costly repair, so it is important to carefully consider the repair and replacement costs before making a decision.
The Penny v Boat Incident: What Really Happened?
You may want to see also
Frequently asked questions
There are several signs that your boat engine block is cracked. These include visible smoke in the cabin, a leaking oil or coolant, discoloured oil, and poor fuel efficiency.
Engine blocks crack due to excess heat, which is usually caused by a problem with the coolant. Poor storage of your boat in the fall can also lead to a cracked engine block.
It is not recommended to fix a cracked boat engine block yourself, especially if you are not knowledgeable about how the system works. It is best to let a professional handle the repairs.
Repair options depend on the severity of the cracks. If the cracks are not too severe, repairs such as pinning, gluing, and welding can be done to seal the damage and prevent coolant or oil leaks. However, not all cracks are repairable, and you may need to replace the engine block or get a new engine.