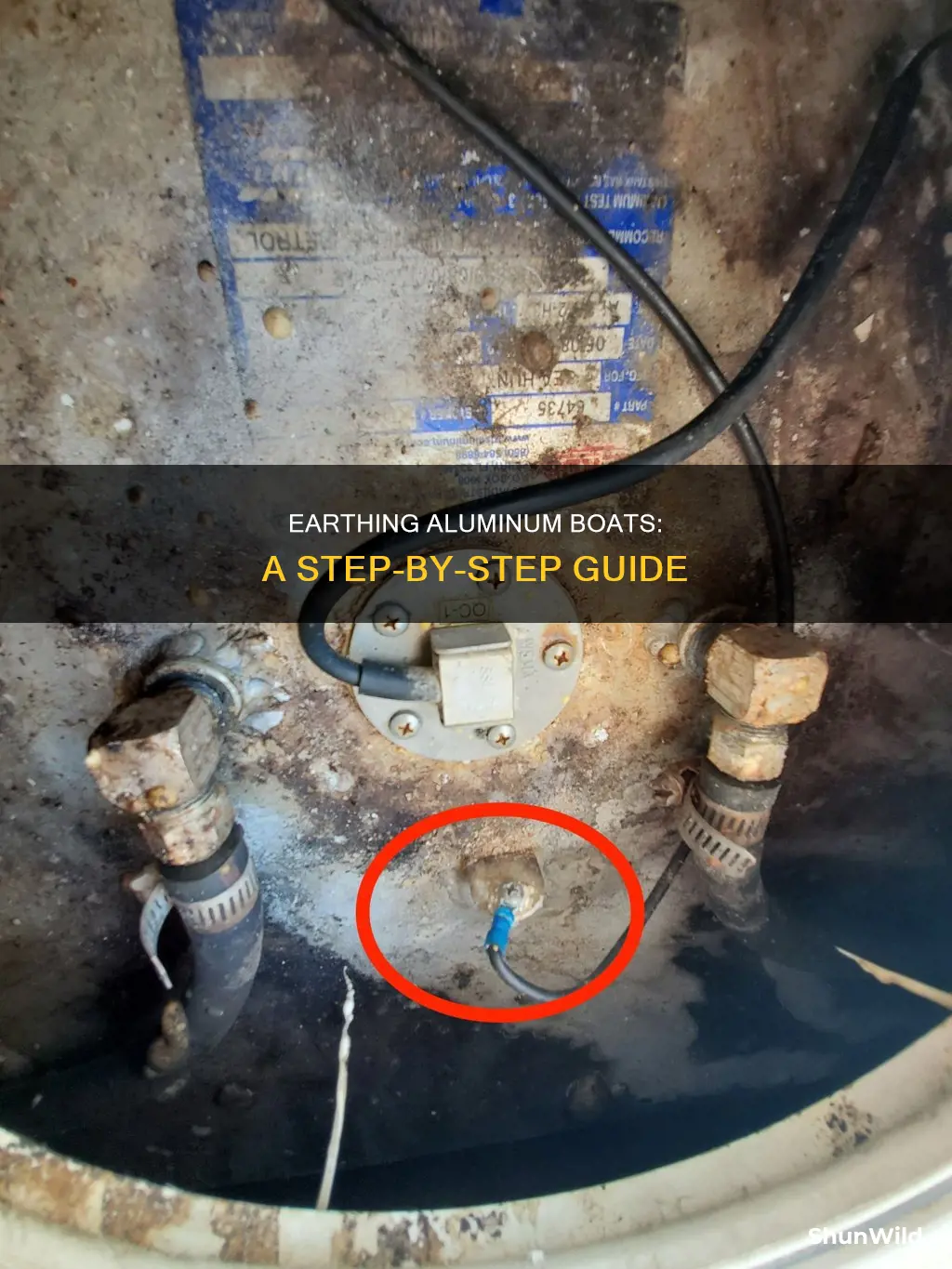
Grounding an aluminium boat is a complex process that requires careful consideration. The electrical system of an aluminium boat must be properly bonded to the hull to avoid any voltage potential issues. While some people suggest grounding the electrical system directly to the hull, others advise against it to prevent corrosion and electrolysis. Instead, it is recommended to have a dedicated grounding attachment point from the DC negative to the hull. This ensures that the electrical system is bonded to the hull without causing any damage to the boat.
What You'll Learn
Use the right aluminium grade
Aluminium alloys are not all created equal, and choosing the right grade for your boat is essential. The most common alloys used in the marine industry are 5052, 5083, 5086, and 6061. Each alloy has unique properties that make it better suited for specific boat components.
If you're building an aluminium boat, you'll want to use an alloy that is strong, yet easy to work with. The 5000 series alloys are a good choice as they contain magnesium, which makes the aluminium easier to weld and more resistant to cracking during the forming process.
For interior parts of the boat, such as cabins, decks, and gunwales, 5052 aluminium alloy is a popular choice. It is the "softest" of the four common marine alloys and is also the least expensive.
However, for the hull, which requires excellent corrosion resistance, you'll want to choose a stronger alloy. Both 5083 and 5086 aluminium alloys are commonly used for hull bottoms and side sheets. They offer superior corrosion resistance, especially in saltwater, and can withstand extremely cold temperatures without becoming brittle. 5086 is considered the superior alloy for marine environments due to its added strength.
If you're looking for a general-purpose alloy for structural components or exterior hull reinforcement, 6061 aluminium alloy is a good option. It has more strength than the 5000 series alloys, excellent finishing characteristics, but is more difficult to form and is prone to fracturing.
When choosing an aluminium alloy for your boat, it's important to consider the specific requirements of each component and select an alloy that offers the best combination of strength, workability, and corrosion resistance.
Boat Shoes and Bony Ankles: A Fashion Faux Pas?
You may want to see also
Choose the right cutting method
There are several cutting methods you can use to cut aluminium for your boat. Each method has its own pros and cons, so it's important to consider which one will work best for your specific project. Here's an overview of the most common cutting methods:
- Laser Cutting: This method provides very precise cuts but is limited by table size. If you have large parts, you may need to cut them into smaller pieces.
- Waterjet Cutting: Waterjet cutting can handle big sheets of aluminium but leaves behind sand particles that require extra preparation before welding.
- Router Table Cutting: Router tables can accommodate large sheets and don't require much edge work before welding. However, they may struggle with detailed or complex cuts.
When choosing the right cutting method, consider the design of your boat, the tools you have available, and your personal preferences. If you have complex or detailed cuts, for example, you may need to opt for laser cutting or waterjet cutting. If you're working with large sheets of aluminium and don't require extremely precise cuts, a router table could be the best option.
Additionally, it's worth noting that aluminium oxide is detrimental to your welding surfaces. Untreated aluminium oxidises when exposed to air for extended periods, making welding more difficult. Therefore, it's recommended to cut aluminium pieces immediately before welding and to remove any aluminium oxide from the welding surfaces using a clean, stainless steel brush.
Identifying Boat Types: Decoding Hull Numbers
You may want to see also
Avoid TIG welding
When it comes to earthing an aluminum boat, it is important to avoid TIG welding. Here are some detailed instructions on why and how to avoid it:
- Warping and Distortion: TIG welding on aluminum can cause warping and distortion due to the metal's high thermal conductivity. Aluminum heats up and cools down quickly, and TIG welding can lead to uneven heat distribution, resulting in unwanted deformation.
- Complexity and Cost: TIG welding is a complex process that requires a high level of expertise. It is also expensive, often costing as much as your firstborn child (jokingly stated by a boat builder).
- Alternative Methods: There are alternative welding methods better suited for aluminum boats, such as pulse MIG welding or using a spool gun attachment for your welder. These methods provide more control over the heat input, reducing the risk of warping and burn-through.
Tips for Avoiding TIG Welding:
- Choose the Right Equipment: Select a welder specifically designed for aluminum welding, such as a MIG welder or a specialized pulse MIG machine. These machines provide a stable wire feed and reduce the risk of contamination, resulting in cleaner and stronger welds.
- Prepare the Aluminum Surface: Properly clean and prepare the aluminum surface before welding. Use a stainless steel brush to remove any dirt, grease, or oxide layers. Ensure you clean just before welding to prevent contamination.
- Control the Heat Input: To avoid warping and burn-through, use short welds and allow the aluminum to cool between passes. Preheating the aluminum slightly can also help manage the heat flow and create more consistent welds.
- Select the Right Filler Material: Choose a filler rod or wire that matches your marine-grade aluminum. For example, 5356 and 4043 filler materials are commonly used for most marine-grade aluminum.
- Weld in a Controlled Environment: Environmental factors can impact the quality of your welds. Aim to weld in a clean, controlled environment to prevent contaminants from compromising your work. If welding outdoors, consider using a portable welding shelter.
- Practice Proper Technique: Master the technique of aluminum welding by maintaining a consistent travel speed and steady hand movements. Use a push technique when welding aluminum to keep the shielding gas in the weld pool and reduce contamination.
- Consider Professional Help: Aluminum boat welding is a specialized skill. If you're new to welding or aluminum boats, consider hiring a professional or consulting an expert to ensure your project's success.
Boat Batteries: Understanding Drawdown and Its Impact
You may want to see also
Set up the jig
Setting up the jig is one of the most important steps in building your boat. Boat hulls can be constructed in many ways, but this article will focus on a design from MetalBoatKits.com.
The design files come with a jig. You can put the jig on custom-built sawhorses. You don't need to do this; you can work off the floor. But it's very important that the jig can't move and is completely square. Level the sawhorses with a laser, bolt them to the floor, bolt the jig to the sawhorses and then tack-weld the boat to the jig. Some builders choose not to tack weld the jig. If it's your first build, tacking the boat to the jig is recommended, as this will help you control distortion from welding.
For more on this step, refer to the blog: How to Build an Aluminum Boat – Part One: Setting up the Jig.
Opening Your Boat's Gas Tank: A Step-by-Step Guide
You may want to see also
Understand the 'incremental backstep' process
The incremental backstep welding technique is an important process in building an aluminum boat. It is used to reduce distortion and warping of the aluminum panels. This technique is started from the center of the boat, working outward in 6-inch steps, and welding towards the center. This spreads heat evenly to avoid warping or distortion of the aluminum panels. Working in small steps keeps the boat’s frame strong and the finish smooth.
The benefits of using the incremental backstep welding technique for aluminum boat building are:
- Less distortion and warping of aluminum panels
- More control over heat during welding
- Stronger and more durable boat frame
- Consistent and efficient welding results
The primary idea behind backstep welding is to eliminate distortion as much as possible. Starting from the center of the boat, work your way out in 6” increments, but weld towards the center. It’s important to work your way out in all directions, skipping every other weld in the process. Try to keep the heat from being concentrated in one area for too long.
The incremental backstep welding technique is a key step in building an aluminum boat. It helps prevent warping and distortion, making the boat stronger and more durable. By following the incremental backstep process, you will achieve a high-quality, long-lasting boat.
Dead Island Riptide: Boat Disaster Explained
You may want to see also
Frequently asked questions
No, it is not safe to ground an aluminum boat to the hull. This will cause the alloy to corrode. Instead, run your grounds to ground blocks and then to the batteries.
Ensure that you have current flowing through the hull by having a negative wire for each application. Keep an eye on your sacrificial anodes and if they are getting eaten up quickly, you might have a problem.
Grounding is when a metal boat is connected to the negative terminal of a battery. Bonding is when underwater metals are wired together to equalize differences in potential between different kinds of metal.