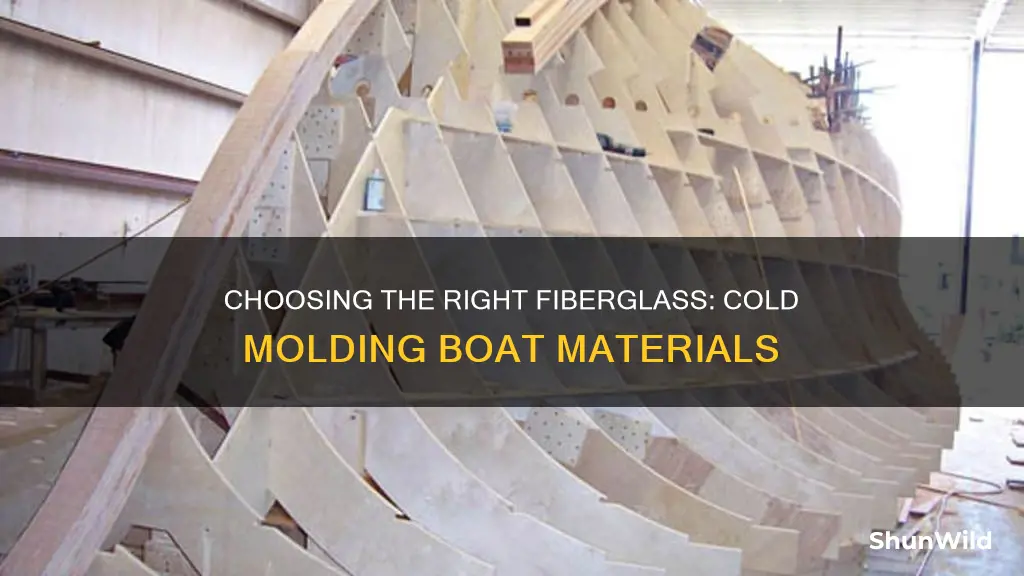
When it comes to building a cold-mold fiberglass boat, choosing the right material is crucial for both performance and durability. The best material for this purpose is typically a combination of epoxy resin and fiberglass cloth, which provides excellent strength, stiffness, and resistance to water. This composite material is known for its ability to withstand the harsh marine environment, offering a lightweight yet robust structure that can handle the stresses of boating. The epoxy resin acts as a binder, bonding the fiberglass fibers together and creating a solid, cohesive shell. This combination is often preferred for its versatility, allowing for intricate designs and custom shapes while maintaining structural integrity.
What You'll Learn
- Fiberglass Types: Compare woven, mat, and chopped strand fiberglass for boat construction
- Resins and Additives: Understand the role of resins and additives in fiberglass boat manufacturing
- Glass Fabric Strength: Evaluate the strength of glass fabric for boat hulls and structures
- Fiberglass Reinforcement: Discover how fiberglass reinforcement enhances boat durability and performance
- Cost and Maintenance: Consider the cost and maintenance requirements of fiberglass boats
Fiberglass Types: Compare woven, mat, and chopped strand fiberglass for boat construction
When it comes to boat construction, especially for cold-mold fiberglass boats, the choice of fiberglass material is crucial for achieving the desired strength, flexibility, and finish. Fiberglass, a composite material made from glass fibers and a resin matrix, is a popular choice for boat building due to its durability, lightweight nature, and ability to be molded into various shapes. The key to success in boat construction lies in understanding the different types of fiberglass available and their unique characteristics.
One of the most common types of fiberglass is woven fiberglass. This method involves weaving glass fibers into a fabric pattern, creating a strong and flexible material. Woven fiberglass is known for its high strength-to-weight ratio, making it an excellent choice for structural components of a boat. The woven pattern provides excellent impact resistance and can be easily molded into complex shapes, ensuring a smooth and seamless finish. This type of fiberglass is often used for the hull and deck of the boat, providing a sturdy foundation for the vessel.
Mat fiberglass, also known as mat or cloth fiberglass, is another popular option. This material consists of randomly arranged glass fibers that are laid out in a mat-like structure. Mat fiberglass offers good strength and flexibility, making it suitable for a wide range of applications. It is often used for the interior and exterior panels of a boat, providing a lightweight yet sturdy structure. Mat fiberglass can be easily cut and shaped, allowing for intricate designs and customization.
Chopped strand fiberglass is a unique type that utilizes glass fibers that are cut into short strands before being combined with the resin. This process creates a material with a different texture and properties compared to woven or mat fiberglass. Chopped strand fiberglass is known for its high strength and impact resistance, making it ideal for structural reinforcements and load-bearing components. It is often used to add extra strength to the boat's hull, providing additional protection against impacts and improving overall structural integrity.
In boat construction, the choice between woven, mat, and chopped strand fiberglass depends on the specific requirements of the project. Woven fiberglass excels in structural integrity and finish, making it perfect for the main hull and deck. Mat fiberglass offers versatility and ease of customization, ideal for interior and exterior panels. Chopped strand fiberglass, with its exceptional strength, is a valuable addition for reinforcing critical areas. By understanding the characteristics of each type, boat builders can make informed decisions to create high-quality, durable vessels.
Finding the Boston Bomber: The Boat's Secrets
You may want to see also
Resins and Additives: Understand the role of resins and additives in fiberglass boat manufacturing
Resins and additives are fundamental components in the manufacturing process of cold-mold fiberglass boats, playing a crucial role in determining the boat's strength, durability, and overall performance. These materials are carefully selected and combined to create a composite structure that is both lightweight and robust, making it ideal for boat construction.
Resins:
Resins are the binding agents in fiberglass composites. They act as the glue that holds the fiberglass fibers together, forming a strong and cohesive structure. There are various types of resins used in boat manufacturing, each with unique properties:
- Epoxy Resins: Epoxy is a popular choice for boat building due to its excellent mechanical properties. It provides high strength, stiffness, and resistance to chemicals and UV radiation. Epoxy resins can be further categorized into various grades, such as bisphenol-A (BPA) and diglycidyl ether (DGE), each offering different performance characteristics.
- Polyester Resins: Polyester resins are known for their ease of use and cost-effectiveness. They offer good adhesion to fiberglass and provide a smooth, glossy finish. While they may not match the strength of epoxy resins, they are still widely used in boat manufacturing, especially for recreational vessels.
- Polyurethane Resins: Polyurethane resins offer superior resistance to abrasion and impact. They provide excellent flexibility and durability, making them ideal for boat hulls and structures that require resistance to wear and tear.
Additives:
Additives are substances mixed with the resins to enhance their performance and tailor the composite material to specific applications. Here's how they contribute:
- Filling Materials: Additives like silica, calcium carbonate, or glass fibers are incorporated into the resin to improve the composite's mechanical properties. These fillers increase strength, reduce weight, and provide structural integrity. For example, adding glass fibers to the resin can significantly enhance the boat's stiffness and load-bearing capacity.
- Catalysts: Catalysts are essential in the curing process of resins. They initiate and accelerate the chemical reaction between the resin and hardener, allowing the composite to set and harden. Common catalysts include amines, acids, and peroxides, each requiring specific mixing ratios for optimal performance.
- Plasticizers and Lubricants: These additives improve the workability of the composite during manufacturing. Plasticizers reduce the viscosity of the resin, making it easier to apply and mold, while lubricants reduce friction between the fibers, ensuring smooth processing.
- UV Stabilizers: In outdoor applications, UV stabilizers are added to protect the boat from sun damage. These additives prevent degradation and yellowing of the composite, ensuring the boat's appearance and structural integrity over time.
Understanding the role of resins and additives is vital for boat builders and enthusiasts. By selecting the right combination of resins and carefully adding modifiers, manufacturers can create fiberglass boats that meet specific performance requirements, ensuring a durable and reliable vessel for various marine applications. The choice of materials directly impacts the boat's overall quality, maintenance needs, and long-term performance in different environmental conditions.
Boat Bottom Paint: The Science Behind Its Magic
You may want to see also
Glass Fabric Strength: Evaluate the strength of glass fabric for boat hulls and structures
Glass fabric is a critical component in the construction of cold-mold fiberglass boats, offering both structural integrity and aesthetic appeal. The strength of the glass fabric directly influences the boat's overall performance, durability, and longevity. When evaluating the suitability of glass fabric for boat hulls and structures, several key factors come into play.
One of the primary considerations is the tensile strength of the glass fabric. Tensile strength measures the fabric's ability to withstand pulling forces without breaking. For boat hulls, a high tensile strength is essential to ensure the fabric can handle the stresses and strains encountered during operation. Modern glass fabrics used in boat construction often have tensile strengths ranging from 300 to 500 pounds per square inch (psi), providing a robust foundation for the hull. This strength is crucial, especially in areas like the hull's core and stringers, where structural integrity is paramount.
The flexibility of the glass fabric is another critical aspect. Boat hulls often require a certain degree of flexibility to accommodate the natural flexing and movement of the vessel. A flexible glass fabric allows for better conformability to the mold, ensuring a smooth and seamless hull shape. This flexibility is particularly important in the design of the boat's stringers and bulkheads, where the fabric must follow the contours of the mold without compromising strength.
The choice of glass fabric also depends on the specific application and design requirements. For instance, in areas where the boat hull requires additional strength, such as along the waterline or in the stern, a higher-modulus glass fabric might be employed. These fabrics offer increased stiffness and strength, contributing to the overall structural integrity of the boat. Conversely, in areas requiring flexibility and lightweight construction, a lower-modulus fabric could be used.
In summary, when evaluating the strength of glass fabric for cold-mold fiberglass boats, it is essential to consider both tensile strength and flexibility. The fabric should provide the necessary structural support while also allowing for the boat's natural movement and flexing. By carefully selecting the appropriate glass fabric, boat builders can ensure that their vessels are not only strong and durable but also aesthetically pleasing and well-suited for their intended purpose.
Painting Boats: The Art of Marine Craft Protection
You may want to see also
Fiberglass Reinforcement: Discover how fiberglass reinforcement enhances boat durability and performance
Fiberglass reinforcement is a critical aspect of boat construction, especially for those building cold-mold fiberglass boats. This technique involves strategically placing fiberglass fibers within the boat's structure to enhance its strength, durability, and overall performance. By incorporating fiberglass reinforcement, boat builders can create a robust and lightweight vessel that can withstand the rigors of marine environments.
The process begins with carefully selecting the appropriate fiberglass type and weave pattern. E-glass, a common choice, offers excellent strength and corrosion resistance, making it ideal for structural reinforcement. The fibers are then laid out in a specific pattern, often using a mold to ensure precise placement. This pattern can vary, with some boats utilizing a unidirectional layup for added strength in critical areas, while others may opt for a more random weave to distribute stress evenly. The key is to tailor the reinforcement to the boat's design and intended use.
During the construction phase, the fiberglass is applied in layers, with each layer serving a unique purpose. The initial layers, known as the "gelcoat," provide a smooth, protective outer surface. Subsequent layers, reinforced with glass fibers, add strength and rigidity. These layers are carefully bonded together using a specialized resin, ensuring a seamless integration that enhances the boat's structural integrity. The reinforcement process can be particularly crucial in areas prone to stress, such as the hull-to-keel joint, the transom, and the stringers.
One of the significant advantages of fiberglass reinforcement is its ability to provide a lightweight yet robust structure. By strategically placing the fibers, boat builders can create a vessel that is both strong and agile. This is especially beneficial for cold-mold fiberglass boats, as it allows for a more efficient use of materials while maintaining the necessary strength to handle various water conditions. The reinforcement also contributes to the boat's overall longevity, reducing the risk of damage from impacts, abrasion, and the corrosive effects of saltwater.
In addition to enhancing durability, fiberglass reinforcement plays a vital role in improving boat performance. The careful placement of fibers can influence the boat's weight distribution, stability, and overall handling characteristics. For instance, reinforcing the hull in specific areas can optimize buoyancy and reduce the boat's draft, making it more maneuverable and efficient in different water conditions. Furthermore, the reinforcement can contribute to a smoother ride by reducing vibrations and providing a more rigid platform for the boat's occupants.
In summary, fiberglass reinforcement is an essential technique in boat construction, particularly for cold-mold fiberglass boats. It involves strategically placing fiberglass fibers to enhance strength, durability, and performance. By carefully selecting the type and pattern of fiberglass and applying it during the construction process, boat builders can create vessels that are not only robust and lightweight but also optimized for their intended use. This reinforcement technique is a key factor in ensuring the longevity and overall success of any boat, making it an indispensable consideration in the world of marine engineering.
Installing a Humminbird Transducer on an Aluminum Boat
You may want to see also
Cost and Maintenance: Consider the cost and maintenance requirements of fiberglass boats
When considering the best material for a cold-mold fiberglass boat, it's essential to evaluate the long-term cost and maintenance implications. Fiberglass, a popular choice for boat construction, offers a balance of strength, durability, and aesthetics. However, its maintenance and repair requirements can vary, impacting the overall ownership experience.
One significant factor is the initial cost. Fiberglass boats can vary widely in price, depending on factors such as size, design complexity, and the quality of materials used. Cold-mold construction, a technique that involves hand-laying fiberglass over a wooden core, often results in a more intricate and detailed boat structure. This method can be more labor-intensive and, consequently, more expensive compared to other fiberglass construction techniques. The cost of materials, including fiberglass cloth, resin, and hardener, can add up, especially for larger boats or those with intricate designs. Additionally, the labor costs associated with skilled craftsmen who specialize in cold-mold construction can contribute to the overall expense.
Maintenance is another critical aspect to consider. Fiberglass boats generally require regular maintenance to ensure their longevity and performance. This includes routine inspections to check for any signs of damage, such as gelcoat fading, osmosis (a condition where water penetrates the gelcoat), or structural issues. Repairing these issues can be costly, especially if they are left unattended. For instance, if a small hole or crack in the gelcoat is not addressed promptly, it can lead to more extensive damage, requiring professional repair or even a full re-glassing of the affected area. Regular cleaning and waxing are also necessary to maintain the boat's appearance and protect the gelcoat from UV damage.
Furthermore, the choice of fiberglass material and construction technique can influence maintenance needs. Some fiberglass resins are more resistant to osmosis and UV degradation, which can reduce the frequency of maintenance and repairs. Additionally, boats constructed using modern techniques, such as vacuum-bagged or hand-laid fiberglass, may have better structural integrity, making them less prone to damage and easier to maintain.
In summary, while fiberglass boats offer excellent performance and aesthetics, the cost and maintenance considerations are essential. The initial investment and ongoing maintenance requirements should be carefully evaluated to ensure that the chosen material and construction method align with the owner's budget and long-term goals. Proper maintenance and timely repairs can help preserve the boat's value and ensure a positive ownership experience.
Boat Race Rivalry: Oxford vs Cambridge
You may want to see also
Frequently asked questions
The ideal material for cold-mold fiberglass boats is a combination of fiberglass cloth and a suitable resin system. Fiberglass cloth, typically made of woven glass fibers, provides strength and rigidity to the boat's structure. When combined with a two-part epoxy or polyester resin, it creates a durable and lightweight hull. The resin acts as a binder, filling the gaps between the glass fibers and creating a solid, cohesive shell.
The resin selection is critical for the boat's performance and durability. Epoxy resins are known for their excellent bonding strength and resistance to chemicals and UV light, making them a popular choice for marine applications. They provide a strong, rigid structure and are often used in high-performance boats. Polyester resins, on the other hand, offer good flexibility and impact resistance, making them suitable for boats that require some give, especially in areas prone to collisions or impact.
Cold-mold construction offers several benefits. It allows for precise control over the boat's shape and thickness, enabling designers to create complex hull forms and incorporate features like stringers and bulkheads for added strength. This method also provides excellent structural integrity due to the resin's ability to penetrate the glass cloth deeply, creating a strong bond. Additionally, cold-mold boats can be built in a mold, ensuring consistency and reducing the risk of errors.
Absolutely! Fiberglass can be tailored to specific needs by using different types of glass fibers and cloth weaves. For example, you can opt for a heavier-weight glass cloth for structural integrity or a lighter-weight cloth for reducing weight. Some boat builders also experiment with woven patterns, such as unidirectional or bidirectional weaves, to optimize strength and stiffness in specific areas of the hull. This customization ensures the boat's material composition meets the required performance and structural demands.