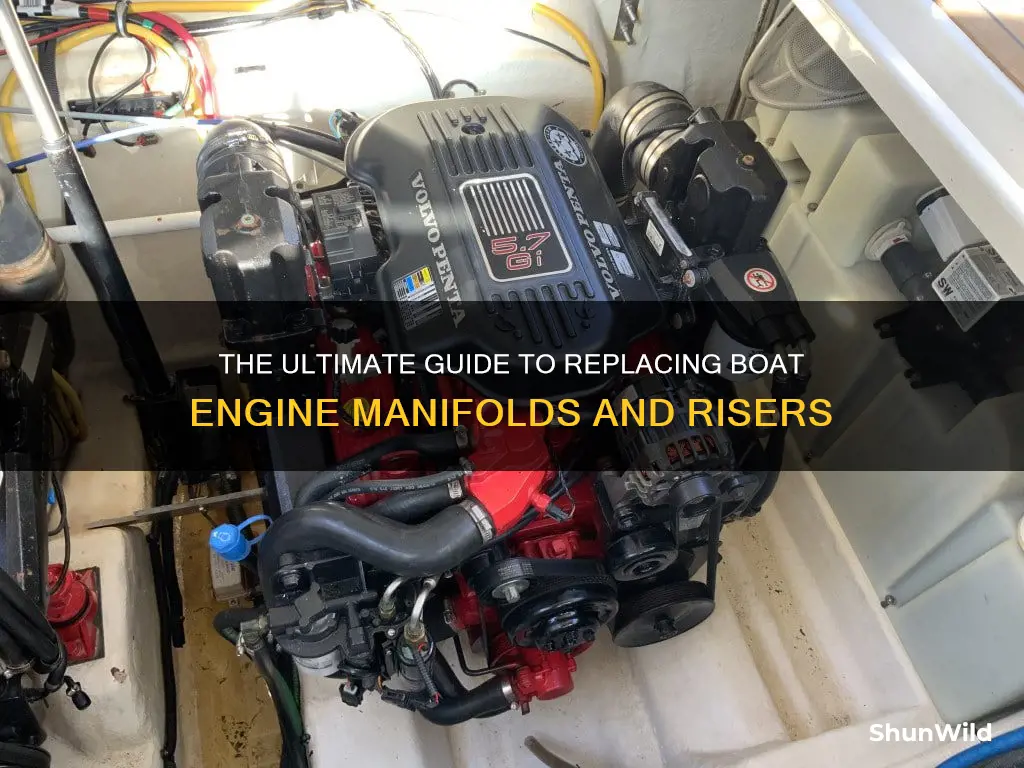
Replacing manifolds and risers on a boat engine is a complex task that requires mechanical knowledge and expertise. The process involves removing and inspecting the components, identifying any issues, and making necessary replacements. Manifolds and risers are crucial for guiding exhaust gases out of the engine and cooling them down. Over time, these components can break down, clog, or develop holes due to rust and corrosion, especially in saltwater environments. It is important to inspect and replace them periodically to prevent engine damage. The replacement procedure includes removing the shift linkage plate, loosening clamps, and disconnecting hoses, among other steps. It is recommended to use new gaskets during reinstallation.
Characteristics | Values |
---|---|
Purpose | Guide exhaust gases out of the engine block to the exterior of the boat |
Engine type | Inboard and inboard/outboard (I/O) engine |
Engine examples | V-8 and V-6 engines |
Risers' shape | Often shaped like an inverted U |
Placement | Located at the aft end or centred on top of the manifold |
Maintenance | Should be inspected and replaced if deteriorated |
Inspection frequency | Annually, after 3-5 years in saltwater, and biannually in freshwater |
Replacement procedure | 1. Remove the shift linkage plate from the starboard riser. 2. Loosen the clamps holding the rubber exhaust bellows. 3. Remove the nuts holding the riser in place. 4. Remove the riser and exhaust pipe assembly. 5. Remove the water hose from the manifold. 6. Remove bolts holding the manifold to the block, and then remove the manifold. |
Inspection process | 1. Check for blockages in the water passages. 2. Check for deteriorating walls to ensure water does not leak into the exhaust passage or to the exterior of the manifold or riser. 3. Ensure gasket surfaces are intact and free from damage or rust. |
What You'll Learn
Understand the differences between petrol and diesel engines
Petrol and diesel engines are classified based on the fuel they use. An engine that uses petrol is called a petrol engine, and one that uses diesel is called a diesel engine. Petrol engines are also called Spark Ignition engines, while diesel engines are called Compression Ignition engines.
Petrol engines are internal combustion engines that work on the principle of the Otto cycle. They use a carburetor to create an air-petrol mixture that enters the cylinder. Due to the low flashpoint of petrol, it can ignite at low temperatures, resulting in a low compression ratio and lower power output compared to diesel engines.
On the other hand, diesel engines are internal combustion engines that work on the principle of the Diesel cycle. They use a fuel injector to inject diesel directly into the cylinder, and the air-fuel mixture is not prepared beforehand. Diesel has a high flashpoint, resulting in a high compression ratio. Diesel engines do not use spark plugs for combustion; instead, they rely on the heat of the compressed air to ignite the fuel.
One significant difference between petrol and diesel engines lies in the injection process. Petrol engines use a combination of port injection and direct fuel injection. Port injection is used at lower engine speeds, while direct injection is employed at higher speeds to provide more power and reduce knocking. In contrast, diesel engines only use direct fuel injection, injecting the fuel directly into the cylinder.
Another difference is in the maintenance requirements. Petrol engines require frequent overhauling, while diesel engines have lower maintenance needs. Additionally, petrol engines have higher fuel consumption compared to diesel engines, which are more fuel-efficient.
The choice between petrol and diesel engines depends on various factors, including the type of vehicle, power requirements, fuel efficiency, and maintenance considerations.
Show Boat's Musical Legacy: A Genre-Defining Musical
You may want to see also
Learn about the function of manifolds and risers
Manifolds and risers are large metal castings that carry hot exhaust gases away from the engine on inboard engines. They are used to collect exhaust gases from the engine, cool them down, and allow cooling water to exit. They are pipes within another pipe, with hot exhaust gases in the internal pipe and water in the external pipe, which is called a water jacket. At the aft end of the riser, water from the water jacket combines with and cools the hot exhaust gases before continuing out the exhaust overboard discharge.
The double-wall arrangement is crucial to the function of manifolds and risers. If water finds its way into the gas-only chamber before the end of the riser, it can seep into the cylinders when the engine is at rest and either seize the pistons with rust or create a "hydrolock" condition. This is because water cannot be compressed in the cylinders, so the engine suffers massive and sometimes irreparable damage when you try to start it. Both result in the premature death of your engine.
Manifolds and risers are exposed to very high temperatures, saltwater, and vibration, and are then left idle for long periods while rust and corrosion eat away at the metal and clog water passages.
The two main styles of manifolds and risers are "wet joint" and "dry joint", which determine where water flows. Dry joint means the water flows between the manifolds and risers, implying it's gasketed separately from the exhaust gases. Wet joint typically uses one gasket between the exhaust and water, making it more prone to leaking water back into the engine.
The distinction between the two designs lies in how close the water channels are to the exhaust pathways. In "Dry Joint" exhaust systems, the water passages are positioned at a greater distance from the exhaust than in "Wet Joint" systems.
The two most common manifolds and risers found in Australia are Mercruiser and Volvo Penta. Mercruiser “dry joint” manifolds and risers were introduced in the early 2000s and are a longer-lasting and lower-risk alternative to “wet joint”.
Repairing Corroded Boat Zippers: DIY Guide
You may want to see also
Learn how to identify corrosion
Corrosion is a serious issue that can lead to engine failure, so it's important to be able to identify it. Here are some signs of corrosion in manifolds and risers:
- Difficulty starting the engine and an unfamiliar knocking sound are two common signs of a leak, but by the time these issues occur, the damage has usually already been done.
- Overheating at high speeds or under load may indicate that the water jacket of the manifold or riser is clogged with scale and corrosion, leading to potential leaks. However, overheating can also be caused by other issues such as a damaged impeller, clogged raw-water filter, or restricted raw-water intake screen.
- Rust on the outside of a manifold or riser is often an indication of damaging rust on the inside as well.
- Hot spots on the manifold or riser can be detected by comparing the temperature of two risers by hand. If one side feels relatively hot, it may indicate clogged water passages.
- Corrosion at the joint between the manifold and riser indicates that the gasket between them has failed, and water may be leaking.
- External signs of corrosion on the manifold or riser, such as rust or pitting, are a clear indication that it's time to replace them.
- For stainless steel manifolds, keep an eye on the anodes and replace them regularly as recommended.
To properly inspect for corrosion, it is recommended to remove the risers and possibly the manifold for a closer look. This should be done periodically, especially if your boat is used in saltwater. Remember that manifolds and risers don't have an expiration date, so regular inspections are crucial to prevent unexpected engine failure.
Cruise Boat Aton Ownership in 2006: Who Was at the Helm?
You may want to see also
Learn how to remove manifolds and risers
Step 1: Remove the shift linkage plate from the starboard riser
The plate is bolted to the riser with three 7/16" bolts. You can use a combination of a socket and wrench to remove these depending on the clearance. A tip is to put the boat in gear with the shifter to move the shift cable out of the way to access some of the bolts.
Step 2: Loosen the clamps holding the rubber exhaust bellows
This will be the second coupler from the riser that joins the pipes in the vertical direction. Splitting the exhaust at this point will help as the risers will have to be pulled in the upward direction when being removed from the manifolds. This is the same motion needed to separate the exhaust at this position. Use a flathead screwdriver to work the bellows off the exhaust pipe.
Step 3: Remove the nuts holding the riser in place
Using a breaker bar and 9/16" socket, loosen the nuts holding the riser in place. There will be a total of eight nuts, four per riser and manifold combination. Once loose, a standard ratchet can be used to remove them fully.
Step 4: Remove the riser and exhaust pipe assembly
Once all the nuts have been removed, give the riser a few taps with a rubber mallet to break it loose from the manifold. It will likely be stuck in place, but a few firm hits will break it free. Once the riser can be moved slightly, pull it straight up and out.
Step 5: Remove the water hose from the manifold
Loosen the hose clamp with an 8mm socket or flathead screwdriver, then use a flathead screwdriver to work the hose off the 90-degree fitting on the manifold. This hose may need to be wiggled and twisted to be removed from the fitting. Inspect the hose for damage and dry rot while it is disconnected.
Step 6: Remove the bolts holding the manifold to the block
Remove the bolts going through the manifold into the engine block with a 9/16" socket. Once loosened, hit the manifold with a rubber mallet if it does not move freely. It is recommended to do this while the bolts are backed out slightly and not fully out, as the bolts will prevent the manifold from dropping when it is loose. When removing the manifold, it is easiest to have a second pair of hands, but it can be done by one person. Once the manifold is held in position, the last bolt can be removed, and the manifold will be free. Take care when removing the last bolt as the manifold will come free from the engine and is heavy.
Tips:
- Before starting, drain the water from the engine's risers and manifolds to perform a visual inspection.
- If you are removing the risers only, step 4 is the last step.
- If you are replacing the risers and manifolds, new gaskets will be required.
- If you are inspecting the risers and manifolds, check for blockages in the water passages, check for deteriorating walls, and ensure gasket surfaces are intact.
Checking Bass Boat Trim Levels: A Step-by-Step Guide
You may want to see also
Learn how to install new manifolds and risers
Step 1: Prepare the engine
Before you begin the installation process, it is important to ensure that your engine is properly prepared. This includes draining the water from the engine's risers and manifolds to perform a visual inspection. Remove the shift linkage plate from the starboard riser, loosen the clamps holding the rubber exhaust bellows, and remove the nuts holding the riser in place.
Step 2: Remove the old manifolds and risers
To remove the old manifolds and risers, start by taking off the water hose from the manifold. Then, use a flat-head screwdriver to remove the bolts holding the manifold to the block. Tap the manifold with a rubber mallet if necessary to loosen it. Once the manifold is removed, you can inspect it for any signs of damage or deterioration.
Step 3: Inspect the old parts
Inspect the removed parts for any signs of damage or deterioration. Check the water passages for any blockages or restrictions in water flow. Also, examine the walls of the manifolds and risers to ensure they are not thinning or forming holes. If there is any significant damage, it is recommended to replace the parts with new ones.
Step 4: Install the new manifolds and risers
When installing the new manifolds and risers, follow the removal process in reverse. Ensure that all gaskets and bolts are properly secured. Reattach the water hose to the manifold and tighten the clamps on the rubber exhaust bellows.
Step 5: Test the installation
Once the new manifolds and risers are installed, it is important to test the engine to ensure that the new parts are functioning properly. Start the engine and check for any signs of leaks or unusual noises. If everything appears to be working correctly, take the boat for a test run to ensure that the engine is performing optimally.
Additional tips:
- It is recommended to replace both risers at the same time for consistent performance.
- Always use new gaskets when reinstalling or replacing risers and manifolds.
- Regularly inspect and maintain your boat's engine to prevent unexpected failures.
- Seek professional assistance if you are unsure about any part of the installation process.
Strut Replacement: Prefab Options for Boat Owners
You may want to see also
Frequently asked questions
Manifolds and risers are typically made of iron and are exposed to hot, acidic exhaust gas and seawater, so they need to be replaced every few years. In saltwater, they usually last 3-5 years, and in freshwater, they can last indefinitely. However, it's important to inspect them regularly for any signs of corrosion or damage.
Some warning signs of potential manifold or riser failure include hard starting, unfamiliar knocking sounds, and engine overheating. If you notice rust on the outside of the manifold or riser, it's likely that there is also damaging rust on the inside. It is recommended to remove and inspect the risers, and possibly the manifold, every 3-5 years in saltwater and every 2 years in freshwater.
To replace the manifolds and risers on your boat engine, you will need a flat-head screwdriver, new gaskets, and possibly new manifolds and risers if the old ones are damaged. You may also need a breaker bar, socket set, ratchet, and rubber mallet, depending on the specific engine configuration.