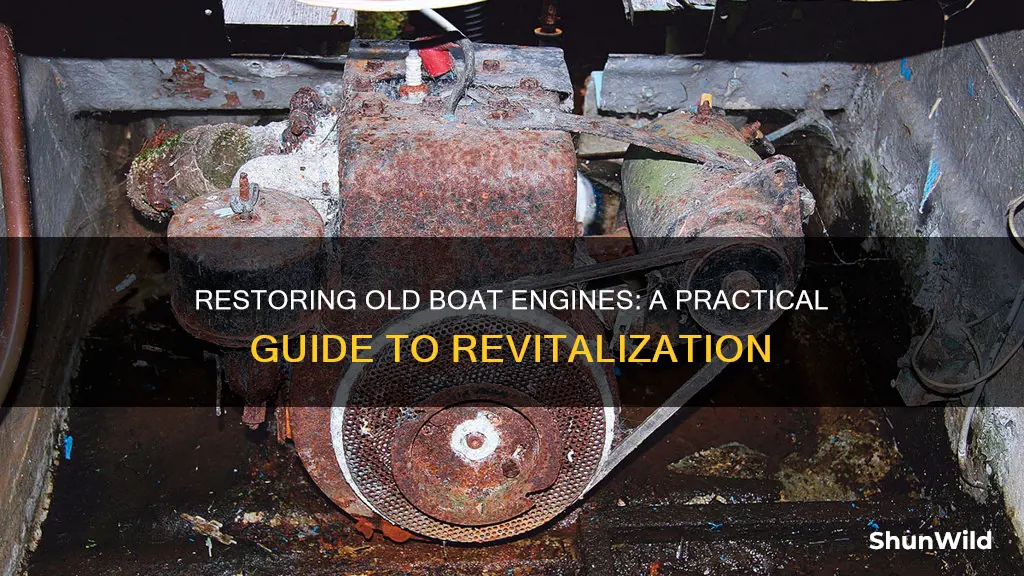
Refurbishing an old boat engine can be a daunting task, but with the right knowledge and maintenance practices, it is possible to bring new life to your old engine. Before embarking on this journey, it is essential to assess the engine's condition and determine if it is worth repairing or replacing. This involves performing a compression test to check for leaky valves or worn pistons and inspecting for issues such as oil leaks, coolant leaks, and exhaust blockages.
If the engine is deemed salvageable, the next step is to address the specific problems it may have. Common issues with old boat engines include fuel system deterioration, water pump problems, propeller damage, and spark plug issues. Regular maintenance, such as flushing the engine, checking fuel lines and pumps, and keeping the engine lubricated, is crucial to prevent major breakdowns.
Additionally, it is important to consider the costs and benefits of refurbishing versus replacing the engine. Refurbishing can be a more affordable option, but it may require significant time and expertise. On the other hand, replacing the engine with a newer model can offer improved fuel efficiency and reduced emissions but at a higher cost.
In conclusion, fixing up an old boat engine requires a combination of mechanical skills, maintenance know-how, and prudent decision-making. By following the right steps and staying vigilant, you can extend the life of your old boat engine and enjoy many more nautical adventures.
What You'll Learn
Inspecting the engine for basic issues
Initial Visual Inspection:
Begin by performing a thorough visual inspection of the engine. Check for any signs of catastrophic failure, such as a holed casing or a failed connecting rod that has punched a hole in the crankcase. These issues usually indicate extensive damage and may render the engine beyond repair. Also, check for the presence of oil in the sump, ensure the oil filter is in place, and verify that no external oil pipes have been tampered with or disconnected.
Manual Rotation of the Engine:
Try to turn the engine over manually. This can often be done using a socket spanner on the crankshaft pulley nut at the front of the engine. Turn it clockwise as hard as you like, but turn it anticlockwise gently to avoid undoing the nut. Some engines may have a large flywheel that can be turned instead. If the engine won't turn over, there could be severe mechanical damage, stuck valves, or water ingress causing rusted rings to the bores.
Oil and Oil Filter Check:
Check the oil by pulling out the dipstick. If the oil has a strong burnt smell, it indicates the engine has been overheating. Wipe the dipstick on a white napkin; if the oil is thick and spreads slowly, it suggests the presence of fuel, which can cause premature wear on bearings, rings, and pistons. Additionally, check the oil filler cap and inside the valve cover for signs of condensation or rust, as these can lead to serious engine problems.
Compression Test:
A compression test will help identify leaky valves or worn pistons. Consult your engine manufacturer for specific guidelines, but generally, if the average compression is within 10% of the recommended level and all cylinders are within 5% of each other, there is no significant compression issue. It's important to use a diesel compression tester for diesel engines, as they have higher pressure requirements than petrol engines.
Exhaust System Inspection:
The exhaust elbow is prone to perforation or blockage, so inspect it carefully. Any signs of perforation or excessive blockage could lead to exhaust gases leaking into the cooling system, causing significant engine trouble.
Engine Mounts and Accessories:
Check the condition of the engine mounts. Broken or damaged engine mounts will need to be replaced. Additionally, assess the condition of the alternator, starter motor, and electrics. Any issues with these components could impact the engine's performance and reliability.
Cooling System and Hoses:
Inspect the cooling system, including the hoses, for any signs of damage or leaks. Check for restrictions in water flow through the manifold and risers, as this can lead to overheating issues. Ensure the seawater strainer is not clogged, as this is a common cause of engine failure, especially in inboard diesel engines.
Battery and Electrical System:
Always use a marine battery when replacing the engine cranking battery, as it is designed to withstand the vibration and pounding of a boat. Secure the battery with a sturdy battery tray and regularly check the battery terminal connections for tightness and corrosion. If the boat is used infrequently, use a maintenance-type battery charger to keep the battery charged.
Fuel System:
Avoid fuel-related issues by using gasoline without ethanol or, if unavailable, fuel with no more than 10% ethanol (E10). Install a 10-micron water-separating fuel filter to keep water and debris out of the engine, and carry a spare filter element.
Prop Shaft and Propeller:
For outboard and sterndrive engines, remove the propeller(s) periodically to inspect the prop shaft. Look for fishing line or other debris that may have wrapped around the shaft, as this can lead to water ingress and potential catastrophic failure.
Remember, if you're unsure about any of these steps or the engine's condition, it's best to consult a marine mechanic or surveyor for a professional assessment.
Boat Watch: Is It Worth Your Time?
You may want to see also
Deciding whether to refurbish or replace
When deciding whether to refurbish or replace an old boat engine, there are several factors to consider. Firstly, it is important to assess the condition of the engine and determine if it is beyond repair. This involves performing a comprehensive survey of the engine, including a compression test to check for leaky valves or worn pistons. If the engine is found to be irreparable, the next step is to consider the options for replacement.
Refurbishing an old engine can be a cost-effective solution, especially if the necessary parts are readily available and the engine can be easily accessed and removed. It is also important to consider who will be doing the refurbishment, as DIY skills may not always be up to the task. In such cases, it may be more feasible to hire a professional, which will incur additional labour costs.
On the other hand, replacing an old engine with a new one can be a more reliable option, although it tends to be more expensive. When considering a replacement, it is worth exploring both new and remanufactured engines. New engines offer the latest technology and can be more fuel-efficient and environmentally friendly, but they come at a higher price point. Remanufactured engines, on the other hand, are rebuilt to factory specifications using a mix of new and old parts, and can be a more affordable alternative.
The decision to refurbish or replace ultimately depends on the specific circumstances, including budget, availability of parts and labour, and the desired level of reliability and performance. For those with mechanical skills and the time to invest, refurbishing can be a rewarding project. However, for those seeking peace of mind and a more long-term solution, replacing the engine may be the preferred option.
Michigan Boat Titles: What You Need to Know
You may want to see also
Compression testing
To perform a compression test, follow these general steps:
- Warm up the engine to operating temperature, if possible.
- Disable the fuel flow for a diesel engine or disable the ignition for a gas engine.
- Remove all the fuel injectors, glow plugs, or spark plugs, depending on your engine type.
- Install a threaded fitting into one of the holes for the injector, glow plug, or spark plug.
- Crank the engine for 6 to 8 revolutions. The pressure gauge will automatically hold the needle at the highest pressure.
- Record the pressure for that cylinder.
- Press the release button on the pressure gauge to return the reading to zero.
- Repeat the process for each of the other cylinders.
When interpreting the results, it is important to consult the specific parameters provided by the engine manufacturer. As a general rule of thumb, if the average compression is within 10% of its recommended level and all cylinders are within 5% of each other's compression values, there is no compression issue. However, it is worth noting that compression testers can vary in their results due to factors such as the quality of the seal and the rpm of the starter motor. Therefore, marine engineers often value consistency across cylinders more highly than the overall values.
Storing Your Pelican Paddle Boat: Tips and Tricks
You may want to see also
Servicing the fuel system
Primary and Secondary Filters
The primary filter catches any water and dirt that might be in the fuel. It typically has a sealed glass bowl beneath the filter, where dirt and water are trapped. To replace the primary filter, first, make sure the tank fuel stopcock is closed. Diesel can be harmful to the skin, so wear protective gloves and have some rags or paper towels ready in case of spillage. Use a suitable container to catch the fuel that will drain from the filter and bowl. Undo the drain screw at the base of the bowl, then remove the central retaining bolt that holds the bowl and filter in place. Clean all the parts, paying close attention to the contact surfaces. Reassemble with new parts, including new seals, and smear some diesel on the seals. Finally, open the fuel stopcock and check for leaks.
The secondary filter, or fine filter, is needed to separate the extra fine particles in diesel fuel that could damage the injectors. It does not need to be replaced as often as the primary filter. Manufacturers usually recommend replacing it after 200 hours of use. There are two main types of secondary filters: spin-on style and cartridge type. The replacement procedure for a spin-on filter is similar to the primary filter, but instead of draining fuel, hold a plastic bag around the filter as you unscrew it to catch any fuel.
Bleeding the Fuel System
When you replace the fuel filters or run out of fuel, air gets trapped in the fuel system, which can prevent the engine from starting. To bleed the fuel system, first, turn the fuel tank stopcock on and have a container ready to catch any drips. Identify the hand priming lever on the fuel lift pump and the bleed screws on the filter bodies and injection pump. If the primary filter is lower than the fuel in the tank, undo the bleed screw. Hold a container beneath the filter to catch the drips, and when the fuel runs clear, close the bleed screw. Wipe the primary filter dry, then repeat the process for the secondary filter. Work the priming lever until clear fuel comes out with no bubbles, then tighten the bleed screw. Wipe the secondary filter dry. If the engine still doesn't start, you may need to bleed the injection pump and high-pressure line, and possibly the injector pipes.
Fuel Tank, Lines, and Pump
The fuel tank should be adequately secured and vented to prevent spillage and ensure proper operation. Regularly inspect the fuel lines for any signs of cracks, wear, or damage, and replace them if necessary. The fuel pump should also be checked regularly to ensure proper operation and prevent leaks.
Fuel Stabilizer and Biocide
When storing your boat for long periods, add a high-quality fuel stabilizer to the tank to slow the loss of octane and counteract the effects of ethanol or water. For diesel fuel, add a biocide during storage to prevent microbial growth.
By following these steps and performing regular maintenance, you can help ensure that your old boat engine's fuel system is in good working condition.
Understanding the Intricacies of Sailboat String Sewing
You may want to see also
Checking the water pump
To check the water pump, you will need a bucket of clean water, a hose, and some basic tools. With the boat on a trailer, place the bucket of water near the engine and connect the hose to the pick-up line. Ensure an airtight connection to the pick-up line, as the pump won't be able to suck up the water without it. You may also need to prime the pick-up line by using a bit of water pressure from the hose. Once the setup is ready, start the boat's engine. You should see that the water pump is sucking water from the bucket into the pick-up line. If there is no or little suction, then your cooling system will require further checks or servicing to correct the issue.
You can also check the cooling system when you are out on the water. When the motor is running, you should be able to quickly run your hand along the side of the water-cooled manifolds without burning your hand. If the cooling system isn't working properly, the manifolds will get hot. Another sign that the water pump may need attention is when the boat accelerates and there is a noticeable drop in engine noise after a few seconds. As the cooling water running through the exhaust pipes impacts the engine noise, a problem with the water pump can cause this change in noise.
If your boat has a cam-driven water pump, pay attention to any engine oil discolouration. In this case, water can be forced through the pump seals if they are worn and need to be replaced.
To change the water pump impeller, follow these steps:
- Close the water inlet valve, usually located next to the water pump.
- Remove the pump cover by taking out the screws and using a mallet to gently remove the cover.
- Remove the paper seal.
- Take out the old impeller from the pump using two screwdrivers for leverage.
- Clean the inside of the pump and the closing plate, scraping off any residue with a cutter blade. Inspect the impeller for cracks or flat fins, which indicate the need for a replacement.
- Grease the central axis and wet the fin tips with soapy water or dishwashing liquid before installing the new impeller.
- For reassembly, turn the wheel in the direction of the motor's rotation to ensure the fins are installed correctly. Press the wheel firmly into the bottom of the housing.
- Replace the paper seal, using joint compound to ensure a perfect seal.
- Reattach the water pump cover and tighten the bolts securely.
- Open the water valve and start the motor, checking for any leaks.
Pinwheel Boat: A Wicked Tuna Vessel Explored
You may want to see also
Frequently asked questions
Before deciding to refurbish an old, non-working engine, it's important to assess whether it's beyond repair. Start by performing a thorough visual assessment to identify any obvious signs of catastrophic failure. Check for oil in the sump, and ensure the oil filter is in place and that no external oil pipes are cut or disconnected. If there is water in the sump, it's best to abandon the engine as it is likely to be extensively damaged. If the engine appears to be in decent condition, try to turn it over manually. If it doesn't turn, there could be severe mechanical damage, or water may have entered the engine and rusted the rings to the bores.
One of the most common problems with old boat engines is overheating, which may be resolved by installing a new water pump impeller. Other potential issues include faulty fuel systems, clogged fuel lines, faulty spark plugs, and problems with the water pump or propeller.
Fixing an old boat engine can be a complex and costly endeavour, so it's important to weigh the pros and cons before proceeding. Assess the engine's condition by performing a compression test to check for leaky valves or worn pistons. Consider the age and type of engine, as older engines may have outdated technology and scarce parts. Additionally, evaluate your budget and skill level, as repairs can be expensive and time-consuming, especially for older engines.