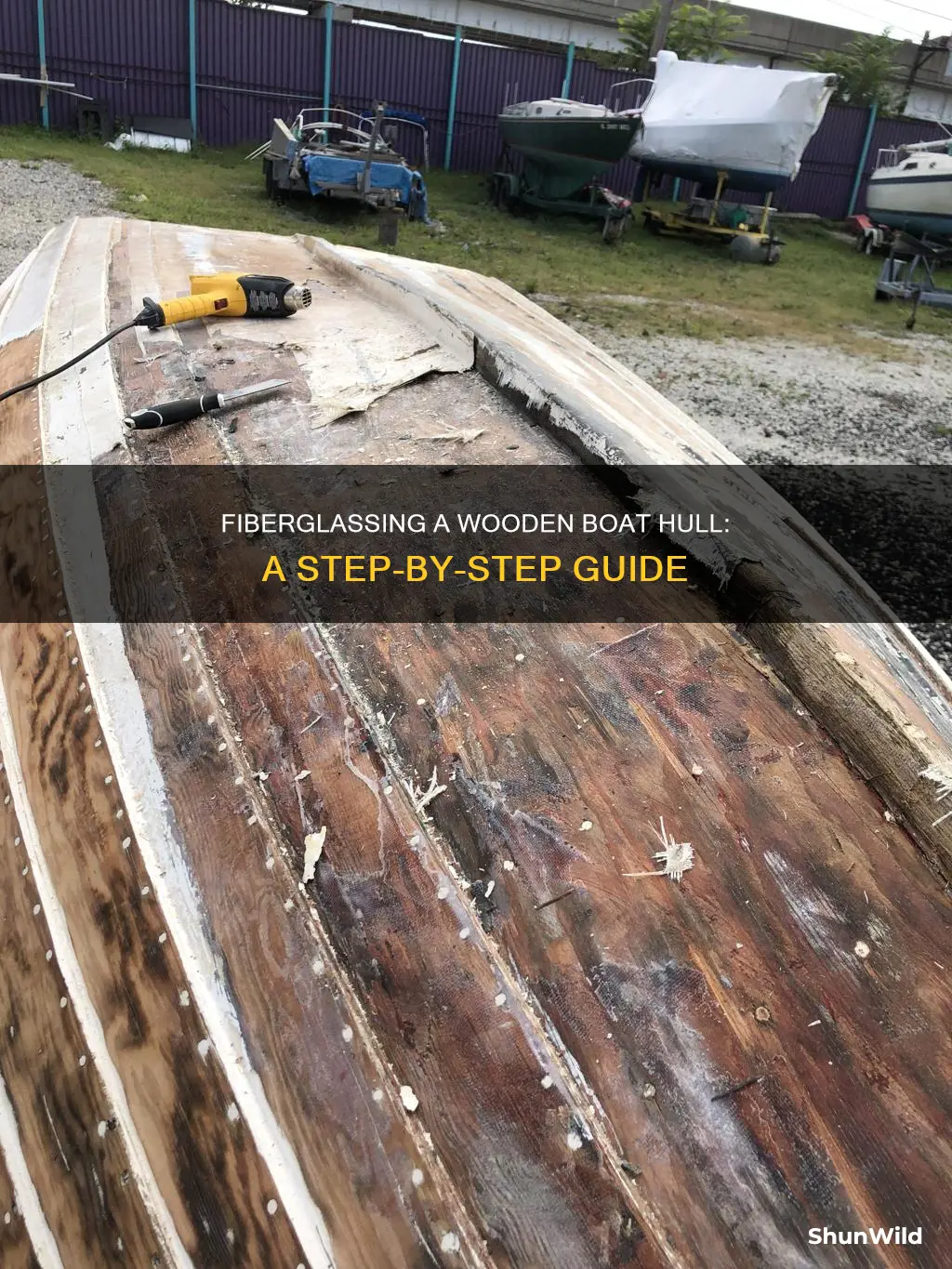
Fiberglassing a wooden boat hull is a crucial step in restoring or customizing wooden boats, offering protection against the elements and enhancing structural integrity. This process involves carefully applying layers of fiberglass cloth and resin to the wooden hull, creating a strong, lightweight, and durable shell. It requires skill and precision to ensure a seamless finish that blends the natural beauty of wood with the strength of fiberglass. The process typically begins with preparing the wood surface, removing any old paint or gelcoat, and ensuring the hull is clean and smooth. Then, the fiberglass is applied in layers, starting with a base coat and building up with multiple layers of cloth and resin to create a sturdy and waterproof hull. Proper preparation and attention to detail are key to achieving a high-quality finish that will protect the boat for years to come.
What You'll Learn
- Prepare the Wood: Sand and clean the hull for a smooth surface
- Choose the Right Fiberglass: Select the appropriate type and thickness
- Apply a Bonding Agent: Ensure strong adhesion between wood and fiberglass
- Lay Up the Fiberglass: Use a mold or form to shape the hull
- Finish and Sand: Smooth the surface and remove any imperfections
Prepare the Wood: Sand and clean the hull for a smooth surface
Preparing the wooden boat hull for fibreglassing is a crucial step to ensure a strong and durable bond between the wood and the fibreglass. This process involves sanding and cleaning the surface to create a smooth, even base for the fibreglass to adhere to. Here's a detailed guide on how to prepare the wood effectively:
Sand the Hull: Start by thoroughly sanding the entire surface of the wooden hull. Use a high-grit sandpaper, typically 120-150 grit, to remove any rough patches, old paint, or existing fibreglass. Sanding is essential to create a smooth texture that allows the fibreglass to bond properly. Work in small sections, applying gentle pressure and following the natural grain of the wood. Pay close attention to areas where the wood may have been damaged or where you plan to apply additional layers of fibreglass for reinforcement. After sanding, use a shop vac or a damp cloth to remove all the dust and debris from the surface, ensuring a clean and dust-free environment.
Remove Old Finishings: If the hull has any existing paint, varnish, or other finishes, it's crucial to remove them before fibreglassing. These finishes can interfere with the bonding process and may not adhere well to the fibreglass. Use a paint scraper or a sharp knife to carefully remove the old finishings, being mindful not to damage the wood beneath. For stubborn areas, you might need to use a heat gun to soften the finish and make it easier to peel off. Once all the old finishes are removed, sand the surface again to ensure a clean and smooth base.
Clean and Inspect: After sanding, give the hull a thorough cleaning. Use a mild detergent or a specific wood cleaner to remove any dirt or grime that may have accumulated during the sanding process. Rinse the hull with water to ensure all cleaning agents are removed. Inspect the surface closely for any remaining imperfections or rough spots. If you notice any, use a finer-grit sandpaper (e.g., 180-220 grit) to smooth them out. This step is vital to guarantee a professional-looking finish and a strong bond for the fibreglass.
Prepare for Fibreglassing: Once the hull is thoroughly cleaned and sanded, it's ready for the fibreglass application. Ensure that the surface is completely dry before proceeding. You can use a tack cloth or a damp cloth to wipe away any remaining dust or debris. This preparation ensures that the fibreglass will adhere properly and creates a seamless transition between the wood and the fibreglass layers.
Boat Registration in New Jersey: A Comprehensive Guide
You may want to see also
Choose the Right Fiberglass: Select the appropriate type and thickness
When fiberglassing a wooden boat hull, selecting the right type and thickness of fiberglass is crucial for a successful and durable repair. The goal is to create a strong, lightweight, and flexible layer that will bond well with the wood and withstand the rigors of the water. Here's a guide to help you make the right choice:
Fiberglass Types:
- Epoxy Resin: This is the most common and versatile choice for boat hull repairs. Epoxy resins provide excellent bonding strength and flexibility, making them ideal for creating a strong bond between the fiberglass and the wood. They are available in various forms, including liquid resins and pre-mixed systems, which offer convenience and ease of use.
- Polyester Resin: Polyester resins are known for their ease of use and lower cost. They are less expensive than epoxy resins and can be a good option for beginners or those on a budget. However, polyester resins may not provide the same level of strength and flexibility as epoxy, so they might be more suitable for non-structural repairs or as a topcoat.
- Vinylester Resin: Vinylester resins offer a balance between strength and cost. They are more resistant to water absorption compared to polyester, making them a better choice for marine applications. Vinylester resins are often used as a core material in fiberglass boat construction.
Consider the Application:
- Structural Repairs: For critical structural repairs, such as reinforcing weak areas or replacing damaged sections, epoxy resins are highly recommended. Their superior strength and bonding properties ensure a robust and long-lasting repair.
- Non-Structural Repairs: If the repair is primarily cosmetic or to restore the boat's appearance, polyester resins can be a suitable choice. They are easy to work with and can provide a smooth finish, making them ideal for touch-ups and minor repairs.
Fiberglass Thickness:
The thickness of the fiberglass layer depends on the specific requirements of your repair. Here's a general guideline:
- Thin Layer (0.0625" to 0.125"): This is suitable for minor repairs, cosmetic touch-ups, or as a topcoat to protect the wood. Thin layers are easier to work with and can provide a smooth surface.
- Medium Layer (0.125" to 0.25"): Medium-thick fiberglass is often used for structural repairs and reinforcement. It offers a good balance between strength and flexibility, allowing for easy shaping and bonding to the wood.
- Thick Layer (0.25" or more): Thick fiberglass layers are reserved for major structural repairs or when significant reinforcement is required. They provide maximum strength and durability but may be more challenging to work with due to their weight and rigidity.
Remember, the choice of fiberglass should always consider the specific needs of your boat hull repair. Consulting with experienced boat builders or fiberglass specialists can provide valuable insights tailored to your project.
Boat Race Televised: May 19's Unmissable Sporting Event
You may want to see also
Apply a Bonding Agent: Ensure strong adhesion between wood and fiberglass
When preparing a wooden boat hull for fiberglassing, one of the most critical steps is applying a bonding agent to ensure a strong and durable bond between the wood and the fiberglass. This process is essential to guarantee the structural integrity and longevity of the boat. Here's a detailed guide on how to effectively apply a bonding agent:
Step 1: Surface Preparation
Before applying the bonding agent, ensure the wooden hull is clean and free of any debris, dirt, or old paint. Use a wire brush or sandpaper to gently scrub the surface, removing any loose fibers or old finish. This step is crucial as it creates a rough surface for the bonding agent to adhere to, promoting better adhesion. Pay extra attention to areas where the fiberglass will be applied, ensuring an even and thorough preparation.
Step 2: Choose the Right Bonding Agent
Selecting the appropriate bonding agent is vital for a successful bond. There are various types available, such as epoxy resins, polyurethane adhesives, or specialized marine bonding agents. For fiberglassing a wooden boat, epoxy-based bonding agents are commonly used due to their excellent adhesion properties and ability to withstand marine environments. Choose a bonding agent that is compatible with both wood and fiberglass to ensure a strong and long-lasting bond.
Step 3: Application Technique
Apply the bonding agent in a thin, even layer over the prepared wooden surface. You can use a brush, roller, or spray gun for this process, depending on your preference and the accessibility of the areas. Start in an inconspicuous spot and test the adhesion to ensure the bonding agent is working as expected. Apply multiple thin coats rather than a thick one to avoid drips and ensure complete coverage. Allow each coat to dry according to the manufacturer's instructions before applying the next layer.
Step 4: Priming (Optional but Recommended)
Consider applying a primer after the bonding agent to provide an additional layer of protection and enhance adhesion. A marine-grade primer can help seal the wood and create a smoother surface for the fiberglass cloth. This step is especially useful if the wood has been previously treated or if there are any areas of concern regarding adhesion.
Step 5: Allow Adequate Drying Time
After applying the bonding agent and any primer, allow sufficient time for the surface to dry completely. Follow the instructions on the bonding agent's packaging for optimal drying times. Proper drying ensures that the bonding agent cures and forms a strong bond with the wood.
By following these steps and giving careful attention to surface preparation and the choice of bonding agent, you can ensure a robust and long-lasting bond between the wood and fiberglass, contributing to the overall strength and durability of your wooden boat hull.
Attaching a Ski Rope to Your Bass Boat
You may want to see also
Lay Up the Fiberglass: Use a mold or form to shape the hull
When it comes to fiberglassing a wooden boat hull, using a mold or form is a crucial step to ensure a smooth and accurate shape. This process involves creating a temporary structure that mimics the desired contour of the hull, allowing you to lay up the fiberglass in the correct places. Here's a step-by-step guide to mastering this technique:
Creating the Mold:
Start by carefully measuring and marking the wooden hull to determine the placement of the mold. Typically, a mold is made from a sturdy material like balsa wood or foam, which is cut to the exact shape of the hull. Ensure the mold is slightly larger than the hull to allow for some material thickness. Secure the mold in place using clamps or temporary fasteners to keep it from shifting during the lay-up process.
Preparing the Mold and Hull:
Before beginning the lay-up, ensure both the mold and the hull are clean and free of any debris. Use a mild detergent or soap solution to wash the surfaces, ensuring no dirt or grime interferes with the bonding process. Allow the surfaces to dry completely; this step is crucial as any moisture can affect the fiberglass's adhesion.
Laying Up the Fiberglass:
Now, it's time to begin the lay-up process. Start by applying a thin layer of fiberglass cloth (mat or weave) over the entire surface of the hull, ensuring it overlaps the mold's edges. This initial layer, known as a "gelcoat," provides a smooth surface for subsequent layers and protects the hull from UV damage. Use a brush or roller to ensure the cloth is evenly distributed and free of wrinkles.
Next, carefully pour or spray the resin onto the fiberglass cloth, following the manufacturer's instructions for mixing ratios. Work quickly but methodically, ensuring the resin is evenly distributed. Apply additional layers of fiberglass cloth, building up the thickness as required by your design or the boat's specifications. Each layer should be slightly offset from the previous one to create a strong, lightweight structure.
Finishing the Lay-Up:
Once you've reached the desired thickness and coverage, allow the lay-up to cure according to the resin manufacturer's guidelines. This process may take several hours or even days, depending on the type of resin used. After curing, carefully remove the mold, ensuring it doesn't damage the freshly laid-up fiberglass. Smooth any rough areas with a sharp blade or a heat gun, and consider adding a final gelcoat layer for added protection and a professional finish.
Remember, patience and precision are key during this stage. Taking the time to carefully measure, prepare, and lay up the fiberglass will result in a high-quality boat hull that showcases your craftsmanship.
Mastering the Art of Fiberglass Boat Flooring: A Comprehensive Guide
You may want to see also
Finish and Sand: Smooth the surface and remove any imperfections
When it comes to finishing and sanding a fiberglassed wooden boat hull, the goal is to achieve a smooth, seamless surface that is free from any imperfections. This process is crucial for the overall appearance and longevity of the boat. Here's a step-by-step guide to ensure a professional finish:
Step 1: Prepare the Surface
Before you begin sanding, ensure that the fiberglass surface is clean and free from any debris or old filler. Use a wire brush or a scraper to remove any loose fibers or residue. This step is essential to allow the sandpaper to grip the surface effectively. Additionally, check for any remaining imperfections, such as small holes or bubbles, and fill them with a suitable fiberglass repair compound. Allow the compound to cure according to the manufacturer's instructions before proceeding.
Step 2: Choose the Right Sandpaper
Selecting the appropriate sandpaper is critical to achieving a smooth finish. Start with a coarse grit (e.g., 80-grit) sandpaper to remove any visible imperfections and roughen the surface. This initial step helps the finer grit sandpaper adhere better during the subsequent stages. Gradually progress to finer grits (e.g., 120-grit, 150-grit, and 180-grit) for a smoother finish. For delicate areas, consider using a finer grit like 220 or 240 grit.
Step 3: Sanding Technique
Apply light, even pressure while sanding to avoid scratching the surface. Work in small sections, following the direction of the fiberglass weave. For curved surfaces, use a circular motion, and for flat areas, sand with the grain. Take your time and be patient, as rushing can lead to uneven sanding. After each grit, wipe away the dust with a damp cloth to reveal the progress and ensure no debris remains.
Step 4: Inspect and Refine
As you progress through the grits, regularly inspect the surface for any remaining imperfections. If you notice any high spots or uneven areas, gently sand them down with a finer grit. Pay close attention to the edges and corners, as these areas can be more prone to imperfections. The goal is to create a seamless transition between the fiberglass and the underlying wood.
Step 5: Final Touches
Once you've achieved a smooth surface, consider using a fine-grit sandpaper (e.g., 320-grit or higher) to create a slightly finer finish. This step can enhance the appearance and prepare the surface for the next stage, which might involve painting or further customization. Always work with the grain and take your time to ensure a professional-looking result.
Repairing a Fibreglass Boat Hull: A Comprehensive Guide
You may want to see also
Frequently asked questions
Fiberglassing a wooden boat hull involves several steps to reinforce and protect the wooden structure. First, the hull is typically cleaned and prepared by removing any old paint, rust, or debris. Then, a layer of epoxy resin is applied to the wood to provide a bonding surface for the fiberglass. Next, a layer of fiberglass cloth or mat is laid over the epoxy, ensuring complete coverage of the hull's surface. This process is repeated with additional layers of fiberglass and epoxy to build up strength and durability. Finally, the fiberglass is cured according to the manufacturer's instructions, often involving heat and/or UV light exposure.
Selecting the appropriate fiberglass depends on various factors, including the boat's intended use, desired strength, and aesthetic preferences. For boat hulls, woven fiberglass cloth is commonly used, available in different weights and weaves. Heavier weights provide more structural strength, while lighter weights offer flexibility and ease of installation. You can also find pre-impregnated fiberglass, where the resin is already mixed with the fiberglass, making it easier to work with. Consider the boat's design, the level of protection needed, and the environmental conditions it will encounter to determine the best fiberglass type.
Fiberglassing requires several specialized tools and equipment to ensure a successful and professional finish. Essential tools include a variety of brushes for applying resins and fillers, roller brushes for smoothing out layers, and spray equipment for efficient resin application. You'll also need a heat gun or heat lamp for curing the fiberglass, as well as protective gear like gloves, respirators, and safety goggles. Additionally, having a well-ventilated workspace and proper disposal methods for resins and waste materials is crucial for a safe and healthy working environment.