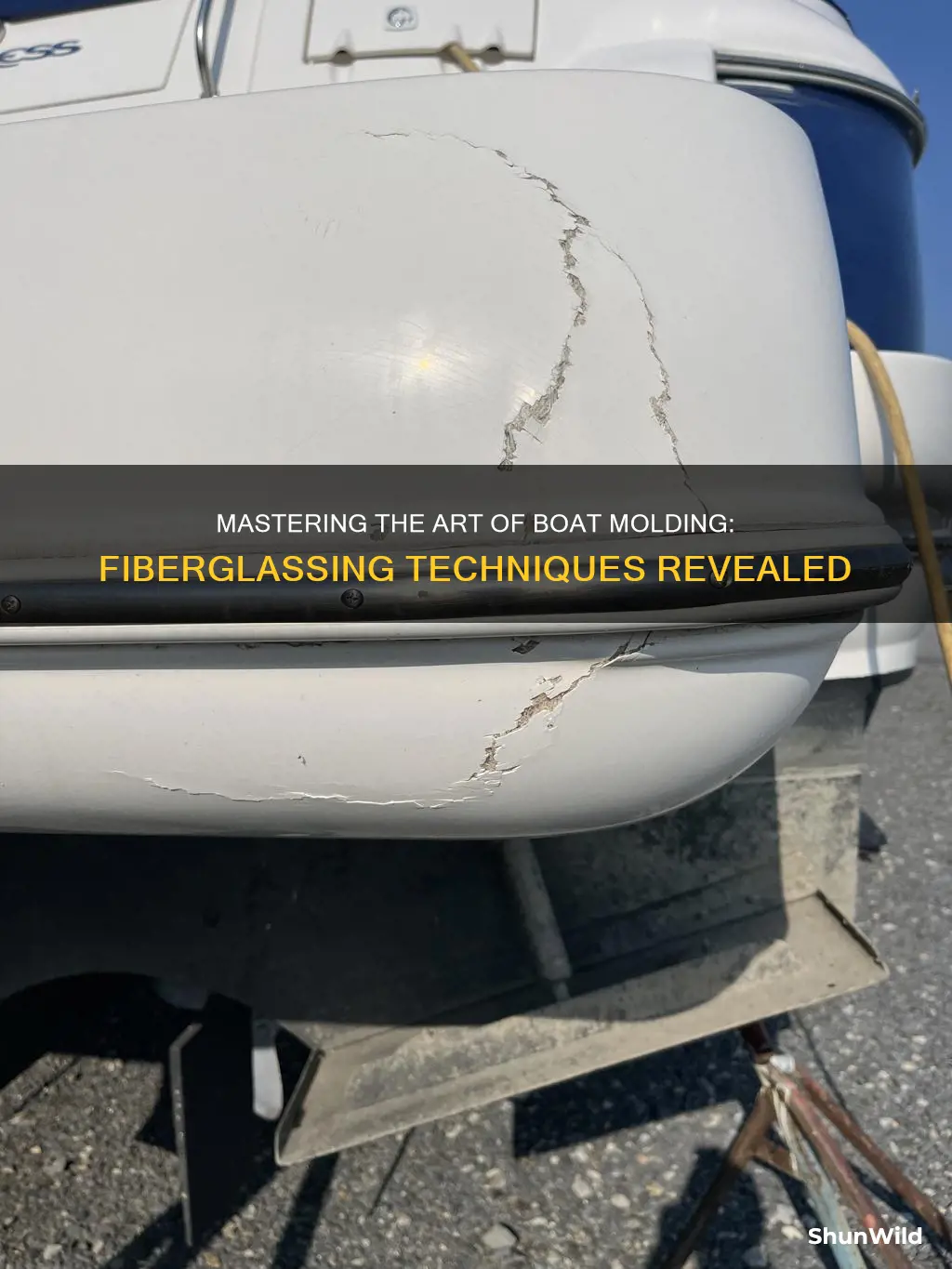
Fiberglassing a boat mold is a crucial step in the boat-building process, allowing you to create a sturdy and lightweight structure. This technique involves applying a layer of fiberglass fabric over a mold, which serves as a template for the boat's shape. By carefully laying and bonding the fiberglass, you can ensure a smooth and durable surface that will withstand the rigors of the water. The process requires precision and attention to detail, as the fiberglass must be applied evenly and securely to create a seamless and strong boat hull. With the right tools and techniques, you can master the art of fiberglassing and build a boat that is both beautiful and functional.
What You'll Learn
- Design Mold: Create a detailed plan for the boat's shape and size
- Prepare Materials: Gather and prepare fiberglass, resin, and hardener
- Layup Technique: Apply layers of fiberglass with resin, ensuring a smooth surface
- Reinforcement: Add glass cloth and tape for strength and durability
- Curing Process: Allow the mold to cure properly for a strong, rigid structure
Design Mold: Create a detailed plan for the boat's shape and size
When designing a mold for your boat, it's crucial to create a detailed plan that accurately reflects the desired shape and size. This initial step is fundamental as it sets the foundation for the entire boat-building process. Here's a step-by-step guide to help you through this process:
- Conceptualize the Boat Design: Begin by visualizing the boat you want to build. Consider factors such as the type of boat (e.g., fishing boat, yacht, or small vessel), its intended use, and the overall style. Sketching out initial ideas on paper can help you refine your concept. Decide on the overall dimensions, including length, width, and depth, keeping in mind the materials you plan to use and the desired performance characteristics.
- Create Detailed Drawings: Convert your concept into precise technical drawings. Use computer-aided design (CAD) software or traditional drafting tools to create 2D and 3D models. Pay close attention to every detail, including the hull shape, deck layout, cabin or cockpit design, and any specific features or accessories. Ensure that all measurements are accurate and consistent. These drawings will serve as the blueprint for your mold.
- Consider Mold Construction Techniques: Different boat-building techniques may influence your mold design. For instance, if you plan to use a vacuum bag molding process, you'll need to account for the placement of the bag and the access points for the vacuum system. If you're using a spray-up technique, consider the ease of access for the resin and the placement of the reinforcement materials. The chosen construction method will impact the mold's design and complexity.
- Define Mold Components: Break down the boat's structure into individual mold components. This could include a hull mold, deck mold, and any specialized molds for specific features. Each component should be designed to capture the desired shape and fit together seamlessly. Consider the materials and techniques required for each part, ensuring they are compatible with the overall boat design.
- Material Selection: Choose the appropriate materials for your mold based on the boat's construction. For example, if you're using fiberglass, select a mold material that can withstand the resin and curing process. Wood, aluminum, or even custom-made mold materials like epoxy foam can be used, depending on your preferences and budget. Ensure that the mold material is durable and can be easily removed from the final boat product.
- Drafting and Engineering: Pay close attention to the mold's draft, which refers to the angle at which the mold releases the boat's surface. Proper drafting ensures easy removal of the boat from the mold and prevents damage during the manufacturing process. Engineering calculations may be required to ensure structural integrity, especially for larger or more complex boats.
By following these steps, you'll create a comprehensive design mold that serves as the blueprint for your boat's construction. This detailed plan will guide the mold-making process and ensure that the final product meets your vision and specifications. Remember, accuracy and precision are key to successful boat-building using fiberglass molding techniques.
Best Time for a Napali Boat Tour
You may want to see also
Prepare Materials: Gather and prepare fiberglass, resin, and hardener
Before you begin the process of fiberglassing your boat mold, it's crucial to gather all the necessary materials and ensure they are in optimal condition. This step is fundamental to the success of your project, as using the right materials and preparing them correctly will result in a strong, durable boat hull.
First, you'll need to acquire high-quality fiberglass. This material is the primary component of your boat's structure, providing strength and rigidity. When selecting fiberglass, consider the type and thickness required for your specific application. For a boat hull, you typically want a mat or cloth made of fiberglass, available in various weights and weaves. Choose a grade suitable for the load-bearing requirements of your boat. For instance, a heavier-weight fiberglass might be more appropriate for structural elements like the hull sides and bottom.
In addition to fiberglass, you must have the right resin and hardener. Resin acts as a binding agent, holding the fiberglass together and providing structural integrity. It's essential to use a resin specifically designed for marine applications, as it must withstand the harsh conditions of the water. Hardener, on the other hand, is a catalyst that initiates the curing process of the resin. Always use the hardener recommended by the resin manufacturer, as different combinations can lead to inconsistent results.
When gathering these materials, ensure you have enough to cover the entire surface area of your boat mold. Calculate the required quantity based on the dimensions of your mold and the thickness of the fiberglass you plan to use. It's better to have a little extra than to run out during the project.
Before applying the fiberglass, it's a good practice to prepare the surface of your mold. Clean the mold thoroughly to remove any dirt, grease, or old paint. You can use a mild detergent and water solution for this task. Additionally, consider using a primer to ensure better adhesion of the fiberglass to the mold's surface. This step will contribute to a stronger and more durable bond between the fiberglass and the underlying structure.
Adjusting Your Boat Dock: A Step-by-Step Guide
You may want to see also
Layup Technique: Apply layers of fiberglass with resin, ensuring a smooth surface
The layup technique is a crucial process in boat molding, especially when using fiberglass, as it directly impacts the boat's structural integrity and aesthetic appeal. This method involves carefully applying layers of fiberglass cloth or mat with a resin matrix to create a strong, lightweight, and durable shell for the boat. Here's a detailed guide on how to execute this technique effectively:
Preparation: Before beginning the layup, ensure you have all the necessary materials and tools ready. This includes the fiberglass cloth or mat, epoxy or polyester resin, a catalyst (if using epoxy), a mixing container, brushes, rollers, and protective gear like gloves and a respirator. Prepare the resin by mixing it with the catalyst according to the manufacturer's instructions. This mixture will be your bonding agent, so accuracy is key.
Surface Preparation: The boat's mold should be clean and free of any debris or old resin. Ensure the surface is smooth and level, as any imperfections will show through the fiberglass. If there are any small holes or imperfections, fill them with a suitable filler and sand it smooth before proceeding.
Laying the First Layer: Start by applying a thin layer of resin to the mold's surface using a brush or roller. This initial layer, known as a 'gel coat,' provides a smooth base for the fiberglass and adds a protective layer. Allow it to gel slightly, then carefully lay the first layer of fiberglass cloth, ensuring it's saturated with the resin. Smooth out any wrinkles or bubbles using a wet cloth or roller.
Subsequent Layers: For subsequent layers, apply a thicker coat of resin and allow it to gel before laying the fiberglass. Each layer should be applied in a specific direction to create a strong, unidirectional structure. Use a roller to ensure a smooth, even application, and avoid any air bubbles. After each layer, inspect the work and smooth out any imperfections.
Ensuring Smoothness: Smoothness is critical in the layup technique. After each layer, inspect the surface for any wrinkles, bubbles, or imperfections. Use a wet cloth or a heat gun to gently smooth out any issues. Take your time with this process, as rushing can lead to visible imperfections. The goal is to create a seamless, smooth surface that will reflect the boat's overall quality.
Curing and Finishing: Once all the layers are applied, allow the layup to cure according to the resin manufacturer's instructions. This process may take several hours or days, depending on the resin type. After curing, inspect the boat's surface and make any necessary touch-ups. You can further enhance the finish by applying additional layers of gel coat or using specialized products to create a high-gloss or matte finish.
Allen Edmonds Eastport Boat Shoes: Comfort and Fit Review
You may want to see also
Reinforcement: Add glass cloth and tape for strength and durability
When it comes to reinforcing a boat mold with fiberglass, adding glass cloth and tape is a crucial step to ensure the structure's strength and durability. This process involves carefully laying the glass cloth over the mold, securing it with tape, and then applying the fiberglass resin to create a robust and lightweight shell. Here's a detailed guide on how to execute this reinforcement technique:
Preparing the Glass Cloth: Start by selecting the appropriate glass cloth, typically a woven fiberglass mat or cloth, which is available in various weights and weaves. The choice depends on the specific areas you want to reinforce. For structural elements like the hull and deck, a heavier-weight cloth is often preferred for added strength. Ensure the cloth is clean and free of any debris before proceeding.
Laying the Glass Cloth: Begin by carefully draping the glass cloth over the mold, ensuring complete coverage of the desired areas. Smooth out any wrinkles or creases, as these can lead to weak spots in the final product. Pay close attention to corners and edges, as these areas require extra care and precision. Use a wet sponge to wet the cloth slightly, allowing it to conform to the mold's contours. This step is crucial for creating a seamless bond between the cloth and the mold.
Securing with Tape: After laying the glass cloth, it's essential to secure it temporarily with masking or duct tape. This step prevents the cloth from shifting during the resin application process. Carefully apply the tape along the edges and any areas where the cloth might lift or move. Ensure the tape is firmly pressed onto the cloth to create a temporary bond.
Applying the Resin: Once the glass cloth is securely in place, it's time to apply the fiberglass resin. Follow the manufacturer's instructions for mixing the resin and hardener. Typically, you'll need to mix a small batch at a time to ensure freshness. Carefully pour the mixed resin over the glass cloth, ensuring an even distribution. Use a brush or roller to smooth out any air bubbles and create a seamless finish. Allow the resin to set partially, following the resin's curing time guidelines.
Adding Additional Layers: For maximum strength, consider adding multiple layers of glass cloth and resin. Each additional layer will further reinforce the structure. Ensure that the layers are applied in a crisscross pattern to create a strong bond between the layers. This technique is especially useful for critical areas like the boat's core and structural joints.
Curing and Finishing: After the final layer of resin is applied, allow the fiberglass to cure completely according to the resin's instructions. Once cured, carefully remove the tape and any excess resin. Sand the surface to create a smooth finish, ready for further customization or painting.
By following these steps, you can effectively reinforce a boat mold using glass cloth and tape, resulting in a sturdy and durable fiberglass structure. This process is a fundamental aspect of boat-building, ensuring the vessel's longevity and performance on the water.
The First Historic Boat Race: Oxford vs. Cambridge
You may want to see also
Curing Process: Allow the mold to cure properly for a strong, rigid structure
The curing process is a critical step in creating a strong and durable boat mold using fiberglass. Once the fiberglass layers are applied, it's essential to provide the material with the necessary time and conditions to set and harden. This process ensures that the mold will have the required structural integrity to withstand the pressures of the boat's shape and the forces exerted during construction.
After the fiberglass is applied, it needs to be left undisturbed for a specified period. This waiting time allows the resin to polymerize and the fibers to bond together, creating a rigid network. The duration of curing can vary depending on the type of resin used and the environmental conditions. Typically, it ranges from a few hours to several days. It's crucial to follow the manufacturer's guidelines for the specific resin you are using to ensure optimal results.
During this curing period, it's important to maintain a controlled environment. Ideal conditions include a stable temperature and humidity level. Extreme temperatures or rapid changes in temperature can affect the curing process and the overall quality of the mold. Humidity should also be kept at an appropriate level to prevent the resin from drying out too quickly, which can lead to cracking.
Once the initial curing period is complete, the mold may require additional steps to ensure its strength and rigidity. This could involve applying a second layer of fiberglass or using a reinforcing material to enhance structural integrity. The specific techniques used will depend on the complexity of the boat design and the desired level of strength.
After the curing process, it is essential to inspect the mold thoroughly. Check for any visible defects, such as voids or delaminations, which could compromise the mold's performance. Proper curing and attention to detail during this stage will result in a high-quality mold, ready for the next steps in boat construction.
Choosing the Right Depth for Your Porta-Dock Boat Lift
You may want to see also
Frequently asked questions
Before you begin, ensure the mold is clean and free of any debris or contaminants. Inspect the surface for any damage or imperfections and make necessary repairs. This step is crucial to ensure a smooth and even application of the fiberglass.
The choice of fiberglass depends on various factors, including the boat's design, intended use, and desired finish. For a typical boat, you can opt for a standard woven fiberglass cloth, available in different weights (ounces) to control the thickness of the layer. For more intricate designs or structural reinforcement, consider using a specialized fiberglass material like a pre-impregnated cloth (also known as "prepreg") or a matrix system.
Yes, using a spray gun is a common and efficient method for applying fiberglass resin. It allows for a more even and controlled distribution of the resin, especially in hard-to-reach areas. However, ensure you have the necessary equipment and ventilation, as working with resins can release fumes. Practice on a test panel first to get a feel for the spray technique.
Fiberglass cloth or tape is used to reinforce the resin and create a strong, durable shell. It provides structural integrity to the boat's hull and helps prevent cracking or delamination. Apply the cloth in overlapping layers, ensuring good adhesion to the mold and between layers. The choice of cloth weight and type depends on the specific area of the boat you are working on.
After the initial application of fiberglass, it's essential to follow the manufacturer's guidelines for curing and handling. Typically, you'll need to cover the mold with a protective layer or wrap to prevent dust and debris from settling. Avoid handling the mold roughly, and ensure it is stored in a controlled environment to maintain its shape and integrity until the final stages of construction.