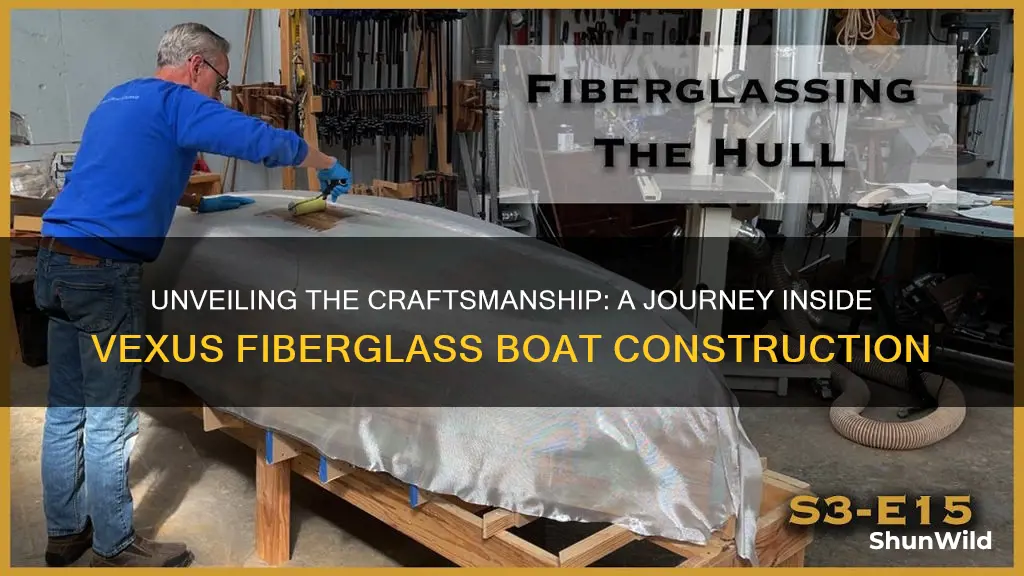
Vexus fiberglass boats are meticulously crafted using a combination of advanced materials and innovative construction techniques. The process begins with a detailed design phase, where engineers and designers work together to create a blueprint that maximizes performance and durability. Once the design is finalized, the boat's hull is constructed using a vacuum-bagging process, where a layer of fiberglass cloth is laid over a mold and a vacuum is applied to draw the resin into the cloth, creating a strong and lightweight structure. This method ensures a smooth and seamless exterior. The interior compartments are then fitted with various components, including the engine, electrical systems, and seating, all while maintaining the boat's structural integrity. Finally, the boat undergoes rigorous testing to ensure it meets the highest safety and performance standards before it is ready for delivery to the owner.
Characteristics | Values |
---|---|
Construction Material | Fiberglass |
Hull Design | Typically features a deep-V or plan-bottom design for stability and performance |
Construction Process | Involves a series of steps: layup, curing, and finishing. The layup process includes placing layers of fiberglass cloth and resin, creating a strong and lightweight structure. |
Gelcoat | A protective outer layer made of epoxy resin and fiberglass, providing a smooth finish and protection against UV rays and chemicals. |
Core Material | Often uses a core material like balsa wood or foam for added buoyancy and structural integrity. |
Construction Techniques | Includes hand layup, spray-up, and vacuum bag molding. These methods ensure precise control over the boat's shape and strength. |
Weight | Vexus fiberglass boats are known for their lightweight construction, making them easy to tow and maneuver. |
Strength | Fiberglass offers excellent strength-to-weight ratios, providing a sturdy yet lightweight boat. |
Customization | Allows for various customization options, including color choices, interior layouts, and additional features. |
Maintenance | Requires regular maintenance to protect the gelcoat and ensure longevity. This includes cleaning, waxing, and occasional repainting. |
What You'll Learn
- Design: Computer-aided design (CAD) software is used to create detailed blueprints
- Fiberglass Layup: Layers of fiberglass cloth are carefully laid and bonded with resin
- Core Insertion: Foam or balsa wood cores are inserted for strength and buoyancy
- Molding: The boat is molded around a steel or aluminum mold to shape
- Finishing: Sanding, painting, and polishing are applied to achieve a smooth, durable finish
Design: Computer-aided design (CAD) software is used to create detailed blueprints
The process of designing a Vexus fiberglass boat begins with the use of advanced computer-aided design (CAD) software, which plays a pivotal role in bringing the vessel to life. This software is an essential tool for marine engineers and designers, allowing them to create highly detailed and precise blueprints. With CAD, the design team can meticulously plan every aspect of the boat, ensuring optimal performance, aesthetics, and functionality.
In the initial stages, designers input the desired specifications and requirements into the CAD system. This includes dimensions, weight constraints, engine specifications, and any unique features or modifications requested by the client. The software then generates a 3D model, providing a comprehensive view of the boat's structure, including its hull, deck, and interior layout. This virtual representation allows designers to identify potential issues early in the process, making adjustments before any physical construction takes place.
The CAD software offers a wide range of tools to create intricate details. Designers can define the shape and form of the hull, specifying the number of chines, the depth of the hull, and the placement of stringers and bulkheads. They can also design the deck layout, including the arrangement of seats, consoles, and storage compartments. With precise measurements and angles, the software ensures that every component is accurately represented, leaving no room for errors during the manufacturing phase.
Furthermore, CAD enables the integration of various systems and components. Designers can model the electrical wiring, plumbing, and mechanical systems, ensuring they are strategically placed and function harmoniously. This level of detail is crucial for the boat's overall performance and safety, as it allows for the identification of potential interference or system conflicts. The software's ability to simulate real-world conditions also aids in optimizing the boat's design, ensuring it meets the intended purpose.
Once the design is finalized, the CAD blueprints serve as a comprehensive guide for the manufacturing process. They provide precise instructions for the construction team, ensuring that every component is built according to the exact specifications. This level of accuracy is vital in the production of high-quality fiberglass boats, as it contributes to the vessel's overall performance, durability, and aesthetic appeal.
Mastering Work Boat Civ 5: Tips for Fun and Profit
You may want to see also
Fiberglass Layup: Layers of fiberglass cloth are carefully laid and bonded with resin
The construction of a Vexus fiberglass boat involves a meticulous process known as fiberglass layup, which is an art and science of creating a strong, lightweight, and durable vessel. This method utilizes layers of fiberglass cloth, meticulously arranged and bonded with resin to form the boat's structure. The process begins with carefully selecting the appropriate type of fiberglass cloth, which is typically composed of woven glass fibers. These fibers are available in various sizes and weights, allowing for customization based on the specific requirements of the boat's design.
During the layup process, the fiberglass cloth is laid out on a mold or a temporary form, ensuring it conforms to the desired shape of the boat. The resin, often an epoxy-based compound, is then applied to the cloth. This resin acts as a binding agent, hardening and fusing the glass fibers together. The application of resin is a critical step, requiring precision and skill to ensure an even distribution. Skilled technicians use brushes, rollers, or spray guns to apply the resin, taking care to avoid air bubbles and ensure complete coverage.
Multiple layers of fiberglass cloth are carefully added, creating a sandwich-like structure. Each layer is positioned at a slight angle to the previous one, known as biasing, which adds strength and rigidity to the boat. This layering technique is repeated until the desired thickness and strength are achieved. The layup process demands precision and attention to detail, as each layer must be carefully aligned and bonded to the previous one.
After the final layer of cloth and resin is applied, the layup is left to cure, typically in a controlled environment with specific temperature and humidity conditions. This curing process allows the resin to harden and bond the fiberglass layers together, creating a solid and rigid structure. Once cured, the boat is removed from the mold, and any necessary finishing touches, such as sanding and fairing, are applied to ensure a smooth and sleek exterior.
The fiberglass layup technique offers numerous advantages for boat construction. It provides excellent structural integrity, making the boat sturdy and resistant to impact. The lightweight nature of fiberglass contributes to the boat's overall performance, allowing for better fuel efficiency and handling. Additionally, the ability to customize the fiberglass layers and resin types enables boat manufacturers to tailor the vessel's characteristics to specific marine environments and intended uses.
The Basics of Revving Boat Engines While in Neutral
You may want to see also
Core Insertion: Foam or balsa wood cores are inserted for strength and buoyancy
The core insertion process is a critical step in the construction of a Vexus fiberglass boat, ensuring both structural integrity and buoyancy. This technique involves the strategic placement of lightweight, yet robust materials within the boat's hull to reinforce its framework. The primary materials used for this purpose are foam and balsa wood, both of which offer unique advantages.
Foam cores, typically open-cell or closed-cell, are favored for their ability to provide excellent buoyancy while maintaining a lightweight profile. Open-cell foam, with its interconnected air pockets, offers superior buoyancy and is often used in the construction of high-performance boats. It also has the added benefit of being more flexible, allowing for easier molding and shaping during the boat-building process. Closed-cell foam, on the other hand, is denser and provides better structural support, making it ideal for areas requiring additional strength.
Balsa wood, a lightweight and durable natural material, is another popular choice for core insertion. It is highly buoyant and, when combined with resin, forms a strong and lightweight core. Balsa wood cores are often used in the construction of high-performance boats due to their ability to provide excellent structural support without adding excessive weight. The wood's natural properties make it an ideal choice for areas requiring both strength and buoyancy, such as the hull's center section.
The insertion process begins with the careful preparation of the foam or balsa wood pieces to ensure a precise fit within the boat's hull. These cores are then meticulously positioned, often using specialized tools and techniques to ensure optimal alignment. Once in place, the cores are securely fastened, typically using epoxy resin, which bonds the material to the fiberglass hull, creating a unified and robust structure.
This method of core insertion is a key factor in the exceptional performance and longevity of Vexus fiberglass boats. It allows for the creation of a lightweight yet sturdy vessel, capable of withstanding the rigors of marine environments while maintaining buoyancy and stability. The careful selection and placement of the core materials contribute significantly to the overall quality and safety of the boat.
Alan Jackson's Hullbilly: A Boat With a Country Twang
You may want to see also
Molding: The boat is molded around a steel or aluminum mold to shape
The construction of a Vexus Fiberglass boat involves a meticulous process, with molding being a critical step in shaping the vessel. This process begins with the creation of a steel or aluminum mold, which serves as the foundation for the boat's structure. The mold is carefully designed to ensure it matches the desired shape and dimensions of the boat, taking into account factors such as hull design, interior layout, and any additional features or accessories.
Once the mold is ready, the molding process commences. This involves carefully placing the mold in a controlled environment, typically a mold room or a specialized facility. The mold is then filled with a liquid resin, often a specialized epoxy-based compound, which is carefully mixed and measured to ensure the correct consistency. This liquid resin is the key component that will eventually harden and form the boat's structure.
As the resin is poured into the mold, it is carefully distributed to ensure an even and precise fill. This step requires skill and precision to avoid any air bubbles or imperfections. The resin is typically left to set for a specified period, during which it gradually hardens due to a chemical reaction, forming a solid structure around the mold. This process is carefully monitored to ensure the resin reaches the desired hardness and strength.
After the resin has set, the mold is carefully removed, revealing the shaped hull of the boat. This initial molded form is then used as a base for further construction. The molded hull is inspected for any defects or imperfections, and any necessary adjustments or reinforcements are made. This step is crucial to ensure the boat's structural integrity and safety.
The molding process is a fundamental aspect of Vexus Fiberglass boat construction, as it sets the foundation for the boat's overall structure and shape. It requires precision, attention to detail, and a controlled environment to ensure the final product meets the highest standards of quality and craftsmanship. This method of construction allows for the creation of sturdy and durable boats, tailored to the specific requirements of the manufacturer and the intended use.
Finding Anchors: Best Places to Look on a Boat
You may want to see also
Finishing: Sanding, painting, and polishing are applied to achieve a smooth, durable finish
The finishing process is a crucial step in the construction of a Vexus fiberglass boat, as it not only enhances the boat's appearance but also ensures its durability and longevity. This phase involves a series of meticulous tasks that transform the raw fiberglass structure into a sleek and refined vessel.
Sanding is an essential initial step in the finishing process. It begins with using coarse-grit sandpaper to remove any excess resin, imperfections, or rough spots from the fiberglass surface. This step is vital to create a smooth base for subsequent finishing techniques. After the initial sanding, finer-grit sandpaper is employed to achieve a finer finish, ensuring that the surface is smooth to the touch and ready for the final coat of paint. The sanding process requires careful attention to detail, especially around curves and contours, to maintain the boat's overall aesthetics.
Painting is the next critical phase in the finishing process. The boat's exterior is prepared by cleaning the surface to remove any dust or debris, ensuring optimal adhesion of the paint. A primer is then applied, providing a base for the paint and enhancing its durability. The choice of paint is crucial; marine-grade paints are recommended due to their resistance to UV rays, salt, and other environmental factors. The painting process involves multiple coats, allowing sufficient drying time between each layer to ensure a smooth and even finish. The final coat may be clear to protect the color and add a glossy sheen.
Polishing is the final step in achieving a smooth, durable finish. After the paint has cured, the boat's surface is polished to a high shine. This process involves using fine-grit compounds and polishing pads to remove any minor imperfections and create a smooth, reflective surface. Polishing also helps to protect the paint, adding an extra layer of durability. The polishing technique requires precision, especially when working around intricate details and trim, to ensure a flawless and professional-looking finish.
In summary, the finishing process is a multi-step journey that transforms a raw fiberglass boat into a masterpiece. Sanding, painting, and polishing are essential techniques that, when executed with care, result in a smooth, durable, and aesthetically pleasing vessel. Each step contributes to the overall quality and longevity of the Vexus fiberglass boat, ensuring it remains a reliable and beautiful companion on the water.
Tri-Hull Boat Identification: Which One Is Mine?
You may want to see also
Frequently asked questions
Vexus boats are primarily constructed using high-quality fiberglass, a composite material known for its strength and durability. The process begins with a lightweight, durable fiberglass cloth, which is then reinforced with a matrix of resin and hardeners. This mixture is carefully applied to a mold, creating a sturdy structure.
The hull, which is the main body of the boat, is crafted through a process called 'molding'. A detailed hull mold is created using a combination of wood, aluminum, or steel, depending on the design. The fiberglass cloth is laid over this mold, and the resin is carefully applied and cured, resulting in a smooth, seamless hull.
One of the key features of Vexus boat construction is the attention to detail and precision. Each boat is meticulously handcrafted, ensuring that every component is carefully measured, cut, and fitted. The construction process involves multiple layers of fiberglass, creating a strong, lightweight structure that can withstand various water conditions.
Yes, after the hull is formed, additional components such as the deck, cabin, and other accessories are added. The interior fittings, including seats, consoles, and storage compartments, are then installed. Finally, a thorough inspection and quality control process ensures that the boat meets the highest standards before it is delivered to the customer.