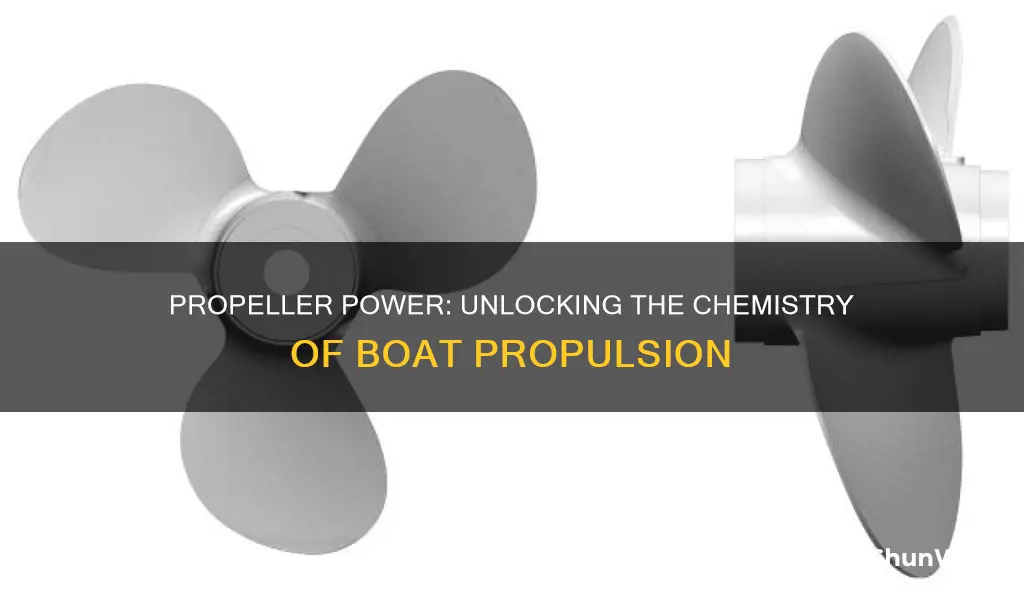
A propeller is a crucial component of a boat's propulsion system, and its operation is rooted in the principles of fluid mechanics and chemistry. When a boat's engine rotates the propeller, it creates a spinning motion that generates a forward thrust. This thrust is produced by the interaction between the propeller blades and the water. The blades are designed with a specific angle and shape to efficiently displace water, creating a pressure difference that propels the boat forward. The chemistry of this process involves the physical and chemical properties of water, such as its density and viscosity, which affect the propeller's performance. Understanding these principles is essential for optimizing boat propulsion and ensuring efficient and effective operation.
What You'll Learn
- Propeller Design: Aerodynamic blades generate thrust by creating pressure differences in water
- Hydrodynamics: Propellers convert rotational energy into forward motion through fluid dynamics
- Cavitation: Bubble formation and collapse due to low pressure can damage propeller surfaces
- Propeller Efficiency: Optimizing blade angle and pitch enhances thrust and fuel efficiency
- Material Science: Advanced materials improve propeller durability and performance in corrosive environments
Propeller Design: Aerodynamic blades generate thrust by creating pressure differences in water
The design of a propeller is a fascinating interplay of fluid dynamics and engineering, where the goal is to efficiently convert the rotational energy of a boat's engine into forward motion through the water. At the heart of this process are the propeller blades, which are meticulously crafted to optimize thrust generation. These blades are not just simple flat surfaces but are carefully shaped to create an aerodynamic profile. The key to their functionality lies in the way they interact with the water, specifically in the creation of pressure differences.
As the propeller rotates, it moves through the water, creating a flow of water around and over its blades. The design of these blades is such that they are curved and angled, with a shape that resembles an airfoil, similar to those found in airplane wings. When the water flows over the curved surface of the blade, it follows the contour, creating a region of lower pressure above the blade and a region of higher pressure below. This pressure difference is a fundamental principle of fluid dynamics, known as Bernoulli's principle. The lower pressure above the blade creates a lift force, which acts in the direction of the blade's rotation, pushing it forward.
The angle at which the blades are set, known as the pitch, is critical to the propeller's performance. A higher pitch means the blades are more steeply angled, which increases the lift force but also the drag. Conversely, a lower pitch results in less lift but reduced drag, allowing for more efficient propulsion at lower speeds. The pitch angle is carefully calculated to balance the need for thrust with the requirement to minimize energy loss due to drag.
The efficiency of a propeller is further enhanced by its ability to create a smooth flow of water over the entire blade surface. This is achieved through a design feature called the 'pitch angle variation' or 'blade twist'. The blades are twisted along their length, with the tip angle increasing as you move towards the blade's root. This twist ensures that the flow of water over the blade is smooth and continuous, reducing turbulence and energy loss.
In summary, the propeller's blades are designed to be aerodynamic, creating a pressure gradient in the water as they rotate. This pressure difference generates thrust, pushing the boat forward. The careful selection of blade shape, angle, and twist ensures that the propeller operates efficiently, converting the engine's power into forward motion with minimal energy waste. This intricate design process showcases the remarkable engineering required to harness the principles of fluid dynamics for practical applications in marine propulsion.
Replacing a Lost Boat Title in Georgia: A Simple Guide
You may want to see also
Hydrodynamics: Propellers convert rotational energy into forward motion through fluid dynamics
The operation of a propeller on a boat is a fascinating application of hydrodynamics, where the principles of fluid motion are harnessed to generate forward propulsion. At its core, a propeller is a rotating device that utilizes the principles of fluid dynamics to move a vessel through water. When a boat's engine rotates the propeller, it creates a series of intricate fluid interactions that result in the boat's forward motion.
The key to understanding this process lies in the concept of 'lift' and 'drag'. As the propeller blades rotate, they create a pressure differential between the front and back of the blade. This pressure difference generates a lift force, which acts in the direction of the blade's angle of attack. The lift force is a result of the fluid (water) being accelerated over the curved surface of the blade, creating a region of lower pressure at the front and higher pressure at the back. This lift force is what propels the boat forward.
Simultaneously, the propeller also experiences a drag force, which acts in the opposite direction to the lift. Drag is caused by the friction and resistance of the water as it flows over and around the propeller. The design of the propeller blades, including their shape, angle, and pitch, plays a crucial role in optimizing the lift-to-drag ratio. Propeller blades are typically designed with a curved leading edge and a straight trailing edge, forming an angle of attack that maximizes lift while minimizing drag.
The rotational energy of the propeller is thus efficiently converted into forward motion. The angle and pitch of the blades determine the direction and magnitude of the lift force, allowing for control over the boat's speed and direction. By adjusting the engine's speed, the propeller's rotational speed can be varied, enabling the boat to accelerate or decelerate. This intricate dance of fluid dynamics and mechanical energy conversion is what makes propeller-driven boats such efficient and versatile modes of transportation on water.
In summary, the propeller's ability to convert rotational energy into forward motion is a testament to the power of hydrodynamics. Through the clever manipulation of fluid flow, lift, and drag, propellers enable boats to navigate through water with precision and efficiency. Understanding these principles is essential to appreciating the engineering marvel that is the propeller-boat system.
Mastering Boat Sailing with Fluctuating Currents: Miles Traveled
You may want to see also
Cavitation: Bubble formation and collapse due to low pressure can damage propeller surfaces
Cavitation is a fascinating yet potentially destructive phenomenon that occurs in the intricate world of boat propulsion. It is a process where the formation and subsequent collapse of bubbles play a crucial role in the performance and longevity of a boat's propeller. This intricate process is a result of the unique interplay between fluid dynamics and the intense forces within the propeller's operating environment.
When a boat's propeller rotates, it creates a region of low pressure in front of it, while the rear section experiences high pressure. This pressure differential is a key factor in the cavitation process. As the propeller blades move through the water, they displace water, creating a region of low pressure ahead of the propeller. This low-pressure area is less dense than the surrounding water, leading to the formation of small bubbles. These bubbles are essentially pockets of air or vapor that form within the water due to the rapid decrease in pressure.
The fascinating yet destructive nature of cavitation becomes apparent as these bubbles continue their journey with the propeller. As the propeller blades move further, the pressure increases again, causing the bubbles to collapse. This collapse occurs rapidly, resulting in a shockwave of energy that can have detrimental effects on the propeller's surface. The intense pressure change during bubble collapse can lead to the formation of small, sharp pits and craters on the propeller blades, a process known as cavitation erosion.
The damage caused by cavitation is particularly concerning due to its cumulative nature. Over time, the repeated bubble formation and collapse can lead to significant wear and tear on the propeller. This erosion weakens the propeller's structure, potentially leading to reduced performance, increased fuel consumption, and even the need for premature replacement. The impact of cavitation is a critical consideration for boat owners and operators, especially those who operate in high-speed or high-load conditions.
To mitigate the effects of cavitation, engineers have developed various strategies. One approach is to design propeller blades with specific shapes and angles that minimize the pressure differentials and reduce the likelihood of bubble formation. Additionally, the use of materials with excellent resistance to cavitation erosion, such as specialized alloys, can help extend the propeller's lifespan. Understanding and managing cavitation is essential to ensuring the efficiency and durability of boat propulsion systems.
The Easy Guide to Replacing Boat Hatch Gas Lift Struts
You may want to see also
Propeller Efficiency: Optimizing blade angle and pitch enhances thrust and fuel efficiency
The efficiency of a propeller in a boat's propulsion system is a critical factor in achieving optimal performance and fuel economy. Propeller efficiency is primarily influenced by two key design elements: blade angle and pitch. These parameters play a significant role in determining how effectively the propeller can convert the engine's power into forward motion.
Blade angle, often referred to as the 'pitch angle,' is a crucial consideration. It defines the angle at which the propeller blades are set relative to the direction of the boat's motion. When the blade angle is optimized, it ensures that the propeller generates maximum thrust. This is achieved by maximizing the angle of attack, where the air or water flows over the blades at the optimal angle, creating a strong lift force. A higher blade angle can increase thrust, but it may also lead to increased drag, especially at lower speeds. Therefore, finding the right balance is essential.
Pitch, on the other hand, refers to the distance a propeller blade travels in one complete revolution. A higher pitch means that the blades are designed to move a greater distance with each turn, resulting in increased thrust. Propellers with higher pitch values are often used for high-speed applications, as they provide better acceleration and top speed. However, higher pitch can also lead to increased fuel consumption, especially at lower speeds, as the propeller may not be as efficient in water flow.
Optimizing both blade angle and pitch is a delicate process. Marine engineers and designers use advanced computer simulations and testing to find the ideal settings for a specific propeller and boat combination. By adjusting these parameters, they can ensure that the propeller delivers the required thrust while minimizing fuel wastage. This optimization process takes into account various factors, including boat speed, water conditions, and the specific requirements of the vessel's propulsion system.
In summary, propeller efficiency is a complex interplay of blade angle and pitch. By carefully adjusting these design elements, engineers can enhance the propeller's ability to generate thrust, resulting in improved fuel efficiency and overall performance. This optimization process is a key aspect of modern boat design, ensuring that vessels can navigate efficiently and economically through the water.
Show Boat's Musical Legacy: Impacting American Theater
You may want to see also
Material Science: Advanced materials improve propeller durability and performance in corrosive environments
The evolution of propeller technology in marine applications has been significantly influenced by advancements in material science, particularly in the development of advanced materials that enhance durability and performance in corrosive environments. Propellers, being in constant contact with water and often exposed to harsh conditions, require materials that can withstand the challenges of marine environments while maintaining efficiency and reliability.
One of the key materials that have revolutionized propeller design is advanced alloys. These alloys are specifically engineered to offer superior resistance to corrosion, fatigue, and abrasion. For instance, the use of nickel-based superalloys, such as Inconel, has become prevalent in propeller manufacturing. These alloys provide excellent resistance to seawater corrosion, making them ideal for applications where the propeller is in direct contact with saltwater. The addition of elements like chromium and molybdenum further enhances their ability to form protective oxide layers, which significantly reduces the impact of corrosive elements.
Composite materials have also played a pivotal role in improving propeller performance. Fiber-reinforced composites, such as those made from carbon fiber or glass fiber, offer a unique combination of strength, stiffness, and lightweight properties. These materials can be tailored to specific applications, allowing engineers to optimize the propeller's design for maximum efficiency. For example, carbon fiber composites can be used to create lightweight yet robust propeller blades, reducing the overall weight of the propeller while maintaining structural integrity. This not only improves the boat's fuel efficiency but also enhances its overall performance.
Additionally, the development of advanced coatings has been instrumental in protecting propellers from the detrimental effects of marine environments. Ceramic coatings, for instance, provide a protective barrier against corrosion and erosion. These coatings are applied to the propeller's surface, creating a durable and non-stick layer that prevents the accumulation of marine growth and reduces friction. By minimizing the contact between the propeller and corrosive elements, these coatings significantly extend the lifespan of the propeller and reduce maintenance requirements.
The use of advanced materials in propeller design has led to significant improvements in both durability and performance. Propellers made from these materials can withstand the harsh conditions of saltwater environments, including exposure to salt spray, chlorine, and other corrosive substances. This increased resistance to corrosion ensures that propellers maintain their structural integrity over extended periods, even in the most challenging marine conditions. Furthermore, the lightweight nature of some of these materials contributes to improved fuel efficiency and overall boat performance.
In conclusion, the integration of advanced materials in propeller design has been a game-changer for the marine industry. From corrosion-resistant alloys to lightweight composites and protective coatings, these materials have revolutionized propeller technology. By addressing the specific challenges posed by marine environments, engineers can now create propellers that are not only more durable but also more efficient, contributing to the overall success and sustainability of marine operations.
Boat Insurance and Hurricanes: Are You Covered?
You may want to see also
Frequently asked questions
A propeller works by converting the rotational energy from the boat's engine into a forward thrust. It consists of blades that are shaped and angled to create a pressure difference between the front and back of the blade as it rotates. This pressure difference creates a lift force, similar to an airplane's wing, which pushes the propeller and the boat forward. The angle and design of the blades determine the efficiency and direction of the thrust.
The pitch of a propeller refers to the distance a blade would travel in one complete revolution if it were straight and not curved. It is a critical factor in determining the propeller's performance. A higher pitch means the blades are more curved, creating a stronger lift force and higher thrust. Lower pitch propellers are more efficient at lower speeds and provide better control, while higher pitch propellers are suitable for higher speeds and maximum thrust.
Cavitation is a process that occurs when the pressure inside a fluid (water in this case) drops to its vapor pressure, causing the formation of vapor bubbles. This phenomenon is common around propellers due to the high-speed flow and pressure changes. As the propeller blades pass through the water, they create regions of low pressure, which can lead to cavitation. Cavitation can result in reduced efficiency, noise, and even damage to the propeller and boat structure. Engineers design propellers to minimize cavitation by optimizing blade shape and angle to maintain a more uniform pressure distribution.