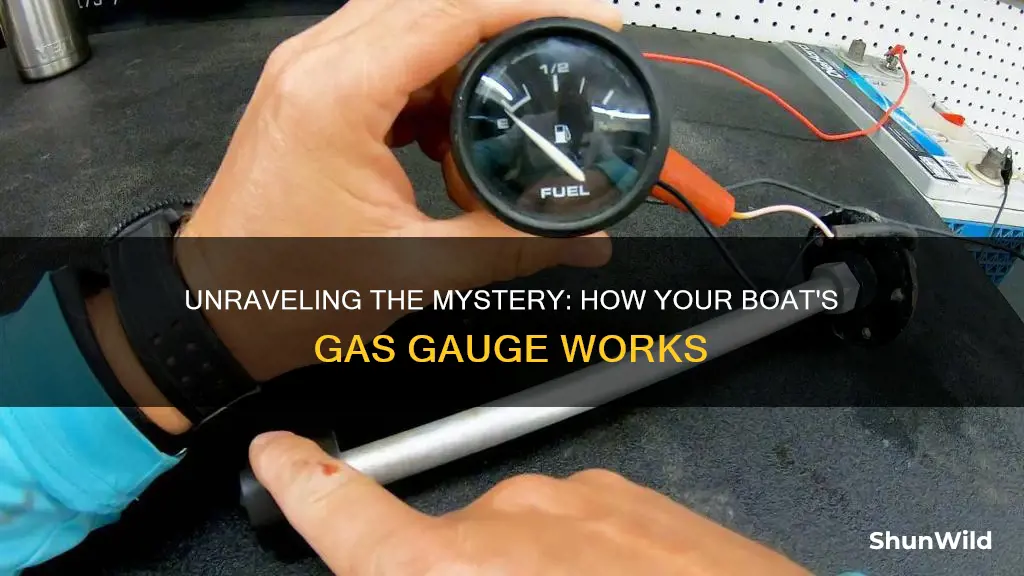
A boat's gas gauge is a crucial component for monitoring fuel levels, ensuring safe navigation, and efficient operation. Understanding how it works is essential for boaters to maintain their vessel's performance and avoid unexpected breakdowns. The gauge operates by measuring the pressure in the fuel tank, which is then converted into a readable display, typically a needle or digital readout. This system provides real-time feedback on the amount of fuel remaining, allowing boaters to make informed decisions about refueling and trip planning. By comprehending the mechanics behind this gauge, boaters can ensure they have the necessary fuel for their journey and avoid the inconvenience and potential hazards of running out of gas.
What You'll Learn
- Pressure Sensors: Sensors measure the pressure in the fuel tank, indicating the amount of fuel
- Float Mechanism: A float rises with fuel level, triggering a switch for the gauge
- Analog vs. Digital: Analog gauges use needles, while digital displays fuel level numerically
- Fuel Send: Sends electrical signals to the gauge based on fuel level
- Calibration: Adjustments ensure accurate readings at different fuel levels
Pressure Sensors: Sensors measure the pressure in the fuel tank, indicating the amount of fuel
The concept of measuring fuel levels in a boat's tank is an essential feature for any vessel owner, ensuring they stay informed about their fuel reserves while navigating. This is where pressure sensors come into play, a critical component in the mechanism of a boat's gas gauge. These sensors are strategically placed within the fuel tank, designed to detect and measure the pressure of the fuel. The principle behind this technology is straightforward: as fuel is consumed, the pressure inside the tank decreases, and this change in pressure is what the sensor reads.
The operation of these pressure sensors is a delicate balance of precision and accuracy. When the boat's engine is running or even when it's stationary, the sensor continuously monitors the fuel pressure. This real-time data is then transmitted to the gas gauge, which is typically located in the boat's dashboard or console. The gauge displays the fuel level, often in a percentage or a bar-graph format, giving the operator a clear visual representation of the remaining fuel. This system ensures that boat owners can make informed decisions about their fuel usage and plan their journeys accordingly.
The design of these pressure sensors is crucial to their functionality. They are often small, compact devices that can fit discreetly within the fuel tank without causing any significant disruption to the fuel flow. This design consideration is vital to maintaining the boat's performance and ensuring that the fuel system operates efficiently. Modern boats often utilize advanced pressure sensor technology, offering more accurate readings and improved reliability.
In addition to their primary function, pressure sensors also contribute to the overall safety of the boat. By providing real-time fuel level data, they help prevent situations where the boat might run out of fuel unexpectedly. This is particularly important for long-distance voyages or when navigating in remote areas where fuel stations might be scarce. The sensors' ability to detect pressure changes allows for early warnings, prompting boat owners to refuel or adjust their routes as necessary.
The integration of pressure sensors in boat gas gauges is a sophisticated system that has evolved over time. Modern boats often feature digital displays, offering more detailed information than traditional analog gauges. This includes not only the fuel level but also additional data such as fuel type, temperature, and even estimates of remaining range based on the boat's speed and engine usage. This comprehensive approach ensures that boat owners have all the necessary information at their fingertips, enhancing their overall boating experience.
Docking a Boat: Maneuvering into a Tight Spot
You may want to see also
Float Mechanism: A float rises with fuel level, triggering a switch for the gauge
The float mechanism is a simple yet effective method used in boat gas gauges to indicate the fuel level. This system relies on a small, buoyant float that is designed to rise as the fuel level increases. Here's how it works:
Inside the fuel tank, a hollow float is attached to a slender rod or arm. This float is typically made of a lightweight, buoyant material like plastic or foam, which allows it to float on the surface of the fuel. The rod or arm is connected to a mechanical linkage or a potentiometer, which is the component that sends the signal to the gauge. As the boat's fuel level rises, the float displaces the fuel, causing it to rise as well. This displacement is directly proportional to the fuel level.
The key to this mechanism is the connection between the float and the gauge. When the float rises, it comes into contact with a switch or a contact point. This switch is typically a simple mechanical device with a moving part that is activated by the float. As the float moves upward, it triggers the switch, which completes an electrical circuit. This action sends a signal to the gauge, indicating the current fuel level. The gauge then displays this information, often with a needle or a digital readout, providing the boat owner with a clear indication of the remaining fuel.
This float-switch combination is a reliable and cost-effective way to measure fuel levels, especially in marine applications where space and weight are limited. The simplicity of the design ensures that it can withstand the harsh marine environment, and the mechanical nature of the float mechanism makes it less susceptible to electrical issues that might occur in more complex systems.
In summary, the float mechanism in a boat gas gauge is a straightforward yet ingenious solution. By utilizing the principle of buoyancy, it provides an accurate representation of the fuel level, ensuring that boat owners can monitor their fuel supply effectively while out on the water.
Bass Baby Boat: Unveiling the Mystery Inside
You may want to see also
Analog vs. Digital: Analog gauges use needles, while digital displays fuel level numerically
The boat's fuel gauge is an essential instrument for monitoring the vessel's fuel levels, ensuring safe navigation and preventing unexpected runouts. It operates on the principle of measuring the electrical current flowing through the fuel tank, which is directly proportional to the amount of fuel present. This method is commonly used in both analog and digital fuel gauges.
Analog Gauges:
Analog fuel gauges have been traditional for many years and are easily recognizable by their spinning needle. These gauges provide a visual representation of the fuel level. When the boat is fueled, the needle moves towards the 'full' mark, and as the fuel decreases, it returns to the 'empty' position. The speed of the needle's movement is proportional to the fuel consumption rate. For instance, a rapid needle movement indicates a high rate of fuel usage, while a slow movement suggests a lower consumption rate. This type of gauge is simple and intuitive, allowing boaters to quickly assess their fuel status.
Digital Displays:
In contrast, digital fuel gauges offer a more modern approach to fuel monitoring. These gauges provide a numerical display of the fuel level, often accompanied by additional information such as the total fuel capacity and estimated range. Digital displays are highly accurate and provide real-time updates, ensuring boaters have up-to-date information about their fuel status. The numerical representation is easy to read and interpret, especially in low-light conditions or for those with visual impairments. Some digital gauges also feature additional features like low-fuel alerts and fuel-saving tips, enhancing the overall boating experience.
The choice between analog and digital fuel gauges often comes down to personal preference and the specific needs of the boater. Analog gauges are known for their simplicity and quick response, making them a favorite for those who prioritize ease of use and a traditional boating experience. On the other hand, digital displays offer advanced features and improved accuracy, catering to boaters who require more detailed information and a modern interface.
In summary, both analog and digital fuel gauges serve the critical function of monitoring a boat's fuel levels. Analog gauges rely on a spinning needle to provide a visual indication, while digital displays offer numerical precision and additional features. Understanding the principles behind these gauges is essential for boaters to ensure they are well-prepared for their journeys and can make informed decisions regarding their fuel management.
Revamping Jet Boat Seats: A DIY Guide
You may want to see also
Fuel Send: Sends electrical signals to the gauge based on fuel level
The fuel send unit is a critical component in the system that monitors and displays the fuel level in a boat's tank. This device is responsible for sending electrical signals to the gauge, providing real-time information about the fuel level. When the boat's engine is running or when the fuel level changes, the fuel send unit detects these variations and translates them into electrical signals. These signals are then transmitted to the gauge, which interprets them to display the current fuel level accurately.
This process is made possible through a small float or sensor that is designed to move in response to the fuel level. As the fuel level rises or falls, the float or sensor moves accordingly. This mechanical movement is then converted into an electrical signal by a transducer or a similar device. The electrical signal is proportional to the fuel level, allowing the gauge to provide an accurate representation of the remaining fuel.
The electrical signals sent by the fuel send unit are typically in the form of a voltage or current that varies with the fuel level. This variation is carefully calibrated to match the specific gauge's requirements. For instance, a 12-volt system might have a specific voltage range that corresponds to different fuel levels. When the fuel level is low, the voltage might drop, and when it's high, the voltage could increase, providing a clear indication of the remaining fuel.
Modern boat gauges often feature digital displays, which further enhance the accuracy and readability of the fuel level information. These digital gauges can quickly update the fuel level reading as the electrical signals are received and interpreted. This real-time feedback ensures that the boat's operator has the most current information about the fuel status, allowing for better decision-making regarding fuel management and trip planning.
In summary, the fuel send unit plays a vital role in the boat's fuel monitoring system by translating mechanical changes in the fuel level into electrical signals. These signals are then used by the gauge to display the current fuel level accurately. This setup ensures that boat owners and operators have a reliable and efficient way to monitor their fuel consumption and make informed decisions to ensure a safe and enjoyable boating experience.
Waterproofing Painted Wood for Boats: Expert Tips and Tricks
You may want to see also
Calibration: Adjustments ensure accurate readings at different fuel levels
Calibration is a critical process in ensuring the accuracy and reliability of a boat's gas gauge. It involves fine-tuning the gauge's settings to provide precise fuel level readings, regardless of the boat's current fuel status. This adjustment is essential for safe navigation and efficient fuel management.
The calibration process typically begins with a basic setup, where the gauge's initial settings are determined. This includes programming the gauge to recognize the boat's fuel tank capacity and the unit of measurement (e.g., gallons or liters). During this stage, the gauge's sensitivity and response time are also set, ensuring it reacts appropriately to fuel level changes.
To perform the calibration, the boat's fuel tank is filled to its maximum capacity, and the gauge's reading is noted. This initial reading serves as a reference point. Then, the tank is gradually emptied, and the gauge's readings are carefully monitored. By comparing the gauge's measurements with the actual fuel level, adjustments can be made to the gauge's settings. For instance, if the gauge reads higher than the actual fuel level, a sensitivity adjustment might be required to make the gauge more responsive.
Advanced calibration techniques may involve using specialized tools or software. These tools can precisely control the fuel level and provide real-time feedback to the gauge, allowing for more accurate adjustments. This process ensures that the gauge provides consistent and reliable readings, even when the fuel level fluctuates.
Regular calibration is recommended, especially after any significant fuel consumption or when the gauge's readings become inconsistent. By calibrating the boat gas gauge, boat owners can maintain a safe and efficient fuel management system, ensuring they have accurate information about their vessel's fuel status during their journeys.
Choosing the Right Battery Size for Your Boat Lift
You may want to see also
Frequently asked questions
The boat's gas gauge operates through a sender unit, typically a float or a pressure sensor, which is connected to the fuel tank. This sender unit sends a signal to the gauge, indicating the fuel level. The gauge then displays this information, often with a needle or digital readout, showing the percentage of fuel remaining.
Yes, calibration is possible and important to ensure the gauge provides accurate readings. Calibration involves adjusting the gauge's settings to match the actual fuel capacity and the sender unit's performance. This process can be done by a professional or, in some cases, by following the manufacturer's instructions for at-home calibration.
If the gas gauge is not functioning correctly, it can lead to potential issues. The gauge may show incorrect fuel levels, causing the boat owner to run out of fuel unexpectedly. In such cases, it's essential to inspect the connections and the sender unit for any blockages or damage. If the problem persists, seeking professional assistance is recommended to ensure a safe and reliable fuel monitoring system.
Regular maintenance and checking for any signs of wear and tear are essential. Over time, the sender unit's float or sensor can become dirty or damaged, affecting accuracy. Cleaning or replacing these components may be necessary. Additionally, ensuring that the gauge's wiring is secure and free from corrosion is vital for proper functioning. It's also a good practice to regularly check the fuel tank's condition and top up the fuel as needed to avoid any gauge-related complications.