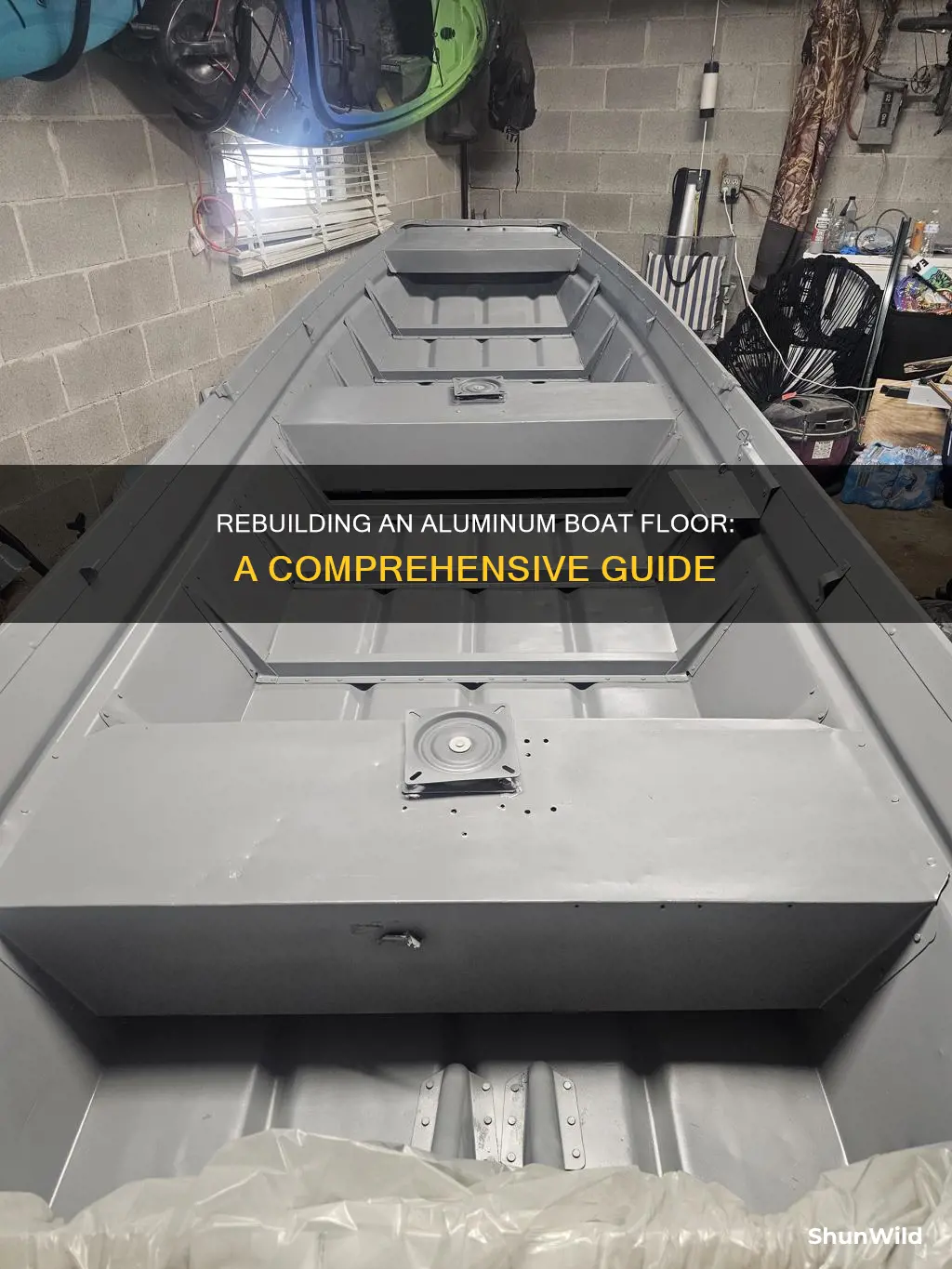
Rebuilding an aluminum boat floor is a complex task that requires careful planning and execution. The process typically involves several steps, including the removal of the old floor, selection and preparation of new materials, and the installation of the new floor. One of the critical aspects is choosing the right type of wood and treatment to prevent future rotting and ensure the structural integrity of the boat. This includes considerations such as using marine-grade plywood, applying epoxy resin and fiberglass cloth for reinforcement and protection, and deciding on the best method for attaching the new floor, such as adhesive, screws, or rivets. Additionally, decisions about carpeting and ventilation play a role in the overall functionality and comfort of the boat.
What You'll Learn
Use exterior-grade plywood for the floor
When rebuilding an aluminium boat floor, it is important to use exterior-grade plywood for the floor. This is because exterior-grade plywood is designed to withstand the elements and will be more resistant to moisture and rot than other types of plywood. It is also important to seal the wood properly before installation to protect it from moisture. This can be done by giving the wood two coats of polyester or epoxy resin, followed by a layer of 6 to 9 oz fiberglass cloth soaked in resin. This will add structural strength to the floor and help to prevent cracking.
There are several options for attaching the plywood to the boat. Some people use PL adhesive, while others use stainless steel screws or rivets. It is important to pre-drill the holes and squirt epoxy down the hole before installing the fastener to create a watertight seal. The carpeting can be attached using snaps, velcro, or glue, depending on personal preference.
When selecting carpeting, it is important to choose a type that is suitable for marine applications. Marine carpeting is designed to shed water and has a rubber backing that prevents moisture from reaching the wood. This can help to prevent rot and extend the life of the floor.
Overall, using exterior-grade plywood for the floor of an aluminium boat is a crucial step in ensuring the durability and longevity of the boat. By properly sealing and installing the plywood, you can create a strong and watertight surface that will provide a solid foundation for years to come.
Boat Dock Sales Tax: Ohio's Unique Levy
You may want to see also
Seal the plywood with epoxy resin and fibreglass cloth
Sealing the plywood with epoxy resin and fibreglass cloth is a crucial step in rebuilding an aluminium boat floor to ensure its longevity and structural integrity. Here is a detailed guide on how to effectively complete this process:
Preparation:
Before applying the epoxy resin, it is essential to prepare the surface of the plywood. Start by removing any existing deck fittings and decorative coatings, such as paint, from the plywood. If the screws holding the fittings are stuck, use a small blowtorch or the tip of a soldering iron to heat and expand the metal, making it easier to remove. Be cautious, as this can scorch the wood. Once the fittings are removed, wash off any residual paint stripper with fresh water.
Next, abrade the plywood thoroughly with 80-grit paper. This step prepares the wood to better receive the epoxy coating. If there are any soft or rotten areas, chisel out the rot and dry the void with a hot air gun. For smaller voids, use epoxy mixed with an additive like colloidal silica to create a filler. For larger voids, cut out the damaged sections and insert a new piece of hardwood glued with epoxy and colloidal silica.
Applying Epoxy Resin:
Choose a day with no risk of rain or high temperatures, as epoxy is best applied in cooler conditions. Mix the epoxy resin with a hardener, following the manufacturer's instructions. For example, you can use WEST SYSTEM 105 Epoxy Resin with WEST SYSTEM 205 Fast Hardener. Mix only the amount you can safely apply within 20 minutes. Pour the mixture into a roller tray and begin to roll it onto the bare plywood.
It is important to apply the epoxy in the evening or during cooler periods to prevent out-gassing, which can cause air bubbles in your coating. Smooth out any air bubbles that appear with a brush or a piece of cut roller. Allow each coat to dry before applying the next. Apply at least three coats of epoxy resin, alternating the direction of tipping off (first coat vertical, second coat horizontal, etc.).
Laminating with Fibreglass Cloth:
Before working with fibreglass, always wear safety equipment, including safety glasses, gloves, and a respirator. Ensure the area is well-ventilated. Use Acetone to wipe down the epoxy-coated plywood, removing any dust or grease. Cut the fibreglass cloth slightly larger than the surface area to ensure full coverage without distorting the edges.
Measure out the required amount of general-purpose laminating resin and add a catalyst, such as MEKP, following the manufacturer's instructions. Mix thoroughly. Spread a thin layer of resin onto the plywood, then place the fibreglass cloth over it, allowing the resin to soak into the cloth. Add more resin as needed and use a roller to remove any trapped air bubbles. Ensure there is enough resin to fully saturate the cloth.
Curing and Finishing:
Allow the fibreglass and resin to cure. During the "green stage," after the resin has gelled but before it fully cures, trim off any excess fibreglass with a razor blade. Once fully cured, the laminate should be hard. Wash off any amine blush that may appear on the epoxy surface and abrade with 80-grit paper before applying any additional coatings or paint.
By following these steps, you will effectively seal and protect the plywood floor of your aluminium boat, ensuring a long-lasting and sturdy finish.
The Evolution of Mono Hull Boats: Understanding Their Design
You may want to see also
Choose marine-grade carpeting for the floor
When rebuilding an aluminum boat floor, choosing the right carpeting is essential for both functionality and aesthetics. Marine-grade carpeting is specifically designed for boats and offers several advantages over regular carpeting. Here are some reasons why you should opt for marine-grade carpeting for your aluminum boat floor:
Durability and Water Resistance:
Marine-grade carpeting is designed to withstand the unique challenges of a boat environment. It is made with high-quality materials that are resistant to water, mould, stains, and fading. The backing of the carpet is crucial; choose a marine carpet with a durable, rubber backing. This will prevent water from seeping through to the wood, reducing the risk of rot and extending the life of your boat floor.
Comfort and Safety:
The right carpeting can enhance the comfort and safety of your boat. Marine-grade carpeting often provides a softer, more supportive surface underfoot, making it more comfortable for standing or walking. Additionally, the carpet's texture can improve traction, reducing the risk of slips and falls, especially when the floor is wet.
Ease of Installation and Maintenance:
Marine-grade carpeting is typically designed for easy installation. It can be cut to fit the unique contours of your boat floor and attached using marine-grade adhesive or other suitable methods. When it comes to maintenance, some marine carpets can be removed for cleaning and drying, allowing for better care and the ability to restore them to their original appearance.
Aesthetic Appeal:
Marine-grade carpeting comes in various colours, textures, and styles to enhance the appearance of your boat. You can choose from different pile heights, such as 16 OZ, 20 OZ, 24 OZ, or 28 OZ, to find the right balance between durability and a luxurious look and feel. A well-chosen carpet can make your boat more inviting and enjoyable for you and your passengers.
Value for Money:
While marine-grade carpeting may be more expensive upfront, it can save you money in the long run. Its durability and resistance to the elements will reduce the need for frequent replacements. Additionally, by protecting your boat floor from water damage, you can avoid costly repairs or renovations down the line.
Applying for Boat Registration in Mississippi: Easy Steps to Follow
You may want to see also
Seal the wood with a commercial wood sealer
Sealing the wood is an important step in the process of rebuilding an aluminium boat floor. Using a commercial wood sealer is an effective method to protect the wood from moisture and ensure its longevity.
There are a variety of commercial wood sealers available on the market, and you can typically find them at hardware stores or home improvement retailers, such as Home Depot. These sealers are designed to form a protective barrier on the wood's surface, preventing water absorption and subsequent rotting.
When selecting a commercial wood sealer, opt for one that is specifically designed for outdoor use and offers long-lasting protection. It is essential to follow the manufacturer's instructions for application carefully. Typically, you will need to clean and dry the wood surface thoroughly before applying the sealer. Ensure you apply the sealer evenly and generously to the wood, using a brush, roller, or sprayer, depending on the product's instructions. Allow adequate drying time between coats, and consider applying multiple coats for added protection.
Additionally, it is crucial to seal any holes or intrusions made into the wood during the installation process. Epoxy is an excellent option for this, as it creates a strong, waterproof seal that will protect the wood from moisture damage. By taking the time to properly seal the wood, you can be confident that your new aluminium boat floor will withstand the elements and provide you with a durable and long-lasting surface.
Boat Fire Extinguishers: Mounting Requirements and Safety
You may want to see also
Use marine-grade vinyl instead of carpeting
When it comes to choosing flooring for your boat, there are several options to consider. One popular option is marine-grade vinyl, which offers a range of benefits that make it a great alternative to traditional carpeting.
One of the biggest advantages of marine vinyl flooring is its durability. Vinyl is highly resistant to stains, fading, and mildew, making it a much lower-maintenance option than carpet. Drinks and spills can be easily wiped up, and juices and wines won't leave behind stubborn stains. Marine vinyl is also waterproof and dries quickly in the sun, so you don't have to worry about moisture being absorbed and retained for long periods. This also helps to prevent the growth of bacteria, which thrive in damp conditions.
In addition to its practical benefits, marine vinyl flooring can also enhance the aesthetics of your boat. It has a crisp, sleek look and comes in various shades and colors, allowing you to find an option that complements your seat fabric. The flooring also has a slip-resistant finish, providing a safe and secure surface for you and your passengers.
Another advantage of marine vinyl is its ability to maintain a comfortable temperature. Unlike carpet, which can absorb and hold heat, making it uncomfortable to walk on with bare feet, marine vinyl stays cool and pleasant to stand on. This is especially beneficial during hot summer days, as you won't need to wear shoes on the boat to protect your feet from hot surfaces.
Finally, marine vinyl flooring can help preserve the resale value of your boat. Its durability and resistance to fading and staining mean that it will maintain its immaculate condition over time. Potential buyers will appreciate not having to replace the flooring soon after purchasing the boat, and the overall value of your boat is likely to be higher.
Overall, marine-grade vinyl is a highly recommended option for boat flooring due to its durability, aesthetic appeal, comfort, and ability to maintain its condition over time. It is a practical and attractive choice that can enhance your boating experience and reduce the need for frequent flooring replacements.
Malibu Boat Troubleshooting: Unfreezing the Screen
You may want to see also
Frequently asked questions
You should use exterior grade plywood, marine-grade plywood, or marine ply. You will also need Polyester or Epoxy resin, fiberglass cloth, and marine carpeting.
You can use PL adhesive, stainless steel screws, or rivets.
You can attach the carpet with snaps, velcro, or glue.
You should seal the wood with epoxy or a commercial wood sealer to protect it from moisture.