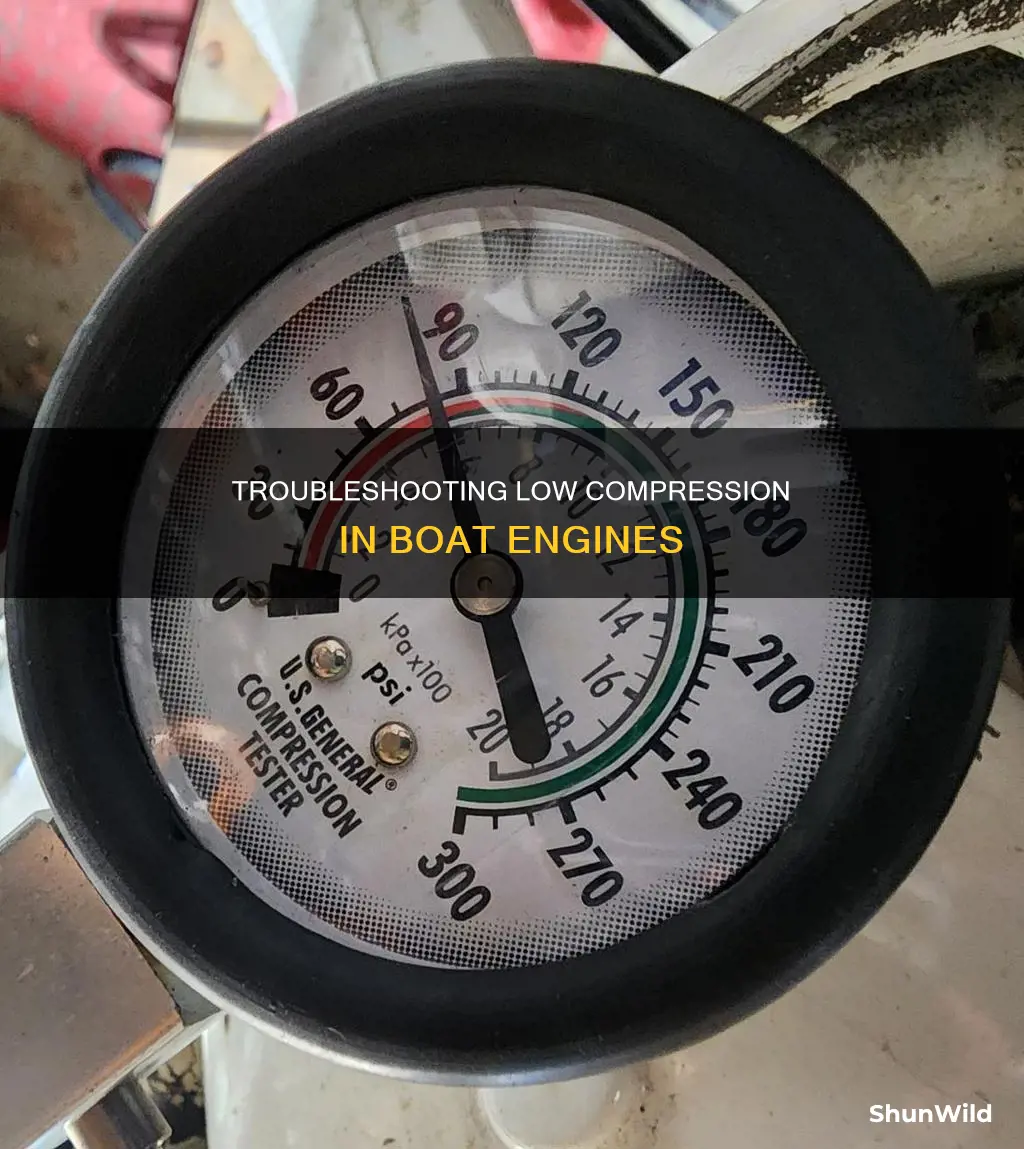
Low compression in a boat engine can be a serious issue, indicating that the engine is not running well and may need to be replaced. A compression check can reveal a lot about the health of an outboard engine, and it is important to understand how it works to evaluate what a mechanic tells you. This test measures the pressure built up by the motion of the piston inside the cylinder, given in pounds per square inch (PSI). A two-stroke cylinder engine should have a compression reading of 110-130 PSI, and any rate below 90 is considered low. Low compression can be caused by various factors, including head gasket failure, leaking or worn-out head gaskets, carbon-clogged piston rings, broken or worn piston rings, valve issues, a worn timing belt, or a cracked cylinder wall. If you suspect low compression in your boat engine, it is recommended to consult a professional mechanic, as attempting repairs without proper knowledge may cause further damage.
Characteristics | Values |
---|---|
What is low engine compression? | When an engine has low or no compression in all cylinders, it won't start. |
Why does it happen? | It could be due to a number of reasons such as a blown head gasket, issues with pistons, or problems with valves. |
How to fix it? | Identify the root cause and replace the damaged parts. If you don't have the time or budget, add an engine compression restoration treatment product. |
How much does it cost? | A professional mechanic will charge $100 to $200 for fixing low compression in one cylinder. Other repairs can cost up to $8000. |
How to test for low compression? | Use a compression tester to check the pressure built up by the motion of the piston inside the cylinder. |
How to prevent it? | Regular maintenance of the engine and its various parts. |
What happens if left untreated? | The engine won't run well, if at all. It may misfire when starting and perform poorly. |
What are the signs of low compression? | The engine may not start, or it may misfire and perform poorly. |
What to do if low compression is detected? | Address the problem immediately. Identify the cause and replace the faulty parts. |
What are the potential causes of low compression in boat engines? | Head gasket failure, leaking head gasket, worn-out head gasket, carbon-clogged piston rings, broken or worn piston rings, valve issues, camshaft issues, worn timing belt, cracked cylinder wall, etc. |
What You'll Learn
Check for a blown head gasket
A blown head gasket is a common issue with boat engines. The head gasket is located between the engine block and the cylinder head, and its purpose is to seal in the internal combustion process and prevent coolant and oil from mixing together. Over time, head gaskets can develop leaks due to exposure to varying temperatures.
There are several ways to check for a blown head gasket:
- White steam and smoke coming from the exhaust accompanied by a sweet smell when the engine is running at a normal temperature. This indicates coolant in the exhaust, which could be the result of a leaky head gasket.
- Coolant leaks. If you notice low coolant levels in your reservoir or radiator, first check for external leaks. If no leaks are found, it is likely that your head gasket is blown.
- The presence of combustion gases in the engine coolant. This method requires a warm engine and involves removing the radiator cap and placing a funnel in its place. Start the engine and watch the coolant; if you see an excessive amount of bubbles, it indicates gasket failure. Caution: Be very careful when performing this test as hot coolant may spray out.
- Coolant leaking from the exhaust or engine overheating. These issues may also indicate a blown head gasket, and it is recommended to have a mechanic check the engine.
While diagnosing a blown head gasket may be straightforward, replacing it is a complex task that often requires professional assistance. Regular maintenance and monitoring of the cooling system are crucial to prevent head gasket failure, which can lead to costly repairs.
Doral Boats: Worth the Investment?
You may want to see also
Test for piston issues
The piston is responsible for compressing the air-fuel mixture and then forcing it from the exhaust. It can overheat and suffer damage from a number of reasons. Here are some tests you can perform to check for piston issues:
- Check for any burning at the top of the piston.
- Inspect the side walls of the crown and ring grooves for any wear.
- Look for any cracking at the top due to thermal and mechanical stress, as well as high-temperature corrosion.
- Check for signs of hot corrosion at the top surface and acidic corrosion at the lower part.
- Ensure the piston rings have free movement.
- Check the ring clearance and groove clearance.
- Inspect the piston rings for any wear, stepping, or scuffing.
- Check the piston skirt and sidewall for any rubbing marks.
- Look for any wear down of wear rings.
- Check for any scale in the cooling water passage due to poor water treatment or choking due to high temperature.
- Inspect the locking bolts, wires, studs, and 'O' ring condition.
If you find any issues with the piston during your inspection, you may need to replace it or seek the help of a trained outboard mechanic.
Firming Up: Fixing Soft Boat Floors
You may want to see also
Inspect exhaust and air intake valves
Inspecting the exhaust and air intake valves is an important step in diagnosing low compression in a boat engine. Here are some detailed steps to guide you through the process:
Visual Inspection of Valves:
- Remove the cylinder head(s) for a thorough inspection of the valves.
- Check the valves for smooth movement and proper seating. Ensure they can move freely and seat correctly without any obstructions.
- Inspect the guides for any signs of wear and tear.
- Examine the lifters and rocker arms for damage or abnormalities.
- Pay close attention to the top of the valve stem; look for any damage or pancaking.
- Check the camshaft lobes for excessive wear or any signs of damage.
Valve Leakdown Test:
- For this test, you will need an air compressor capable of delivering at least 90 PSI, a wooden block with a 9⁄16-inch hole drilled through it, and water.
- Start by preparing the cylinder head. Remove the cams and lifters, and flip the cylinder head(s) upside down.
- Insert a used spark plug into the chamber to seal it, then pour water into each of the combustion chambers.
- Take the wooden block and press it firmly against either the intake or exhaust port to create an airtight seal.
- Insert the air hose into the hole in the wooden block and release compressed air into the cylinder port.
- Observe for any bubbles forming past a bent valve on the intake or exhaust side. Larger leaks will produce bigger bubbles.
Checking Valve Health:
- A healthy valve will typically display a symmetrical pattern on its face.
- Look for red or orange deposits left by unburned byproducts of combustion. These deposits are normal and tend to be thicker in the centre of the valve, where temperatures are cooler.
- If you see an asymmetric pattern of deposits, it could indicate a problem with the valve not seating properly, allowing ultra-hot gases to leak and create hot spots.
- Valve faces that turn yellow or green indicate abnormally high temperatures. If any part of the exhaust valve turns green, replace it immediately, as it is severely burned and weakened.
- Ensure proper alignment of the rocker arm to prevent valve guide wear and improper valve seating, which can lead to premature valve wear.
Other Considerations:
- Keep in mind that cylinder head valves typically only bend if the engine has experienced some form of trauma or a timing belt failure, causing the valves to strike the pistons.
- If you suspect internal engine damage, such as a broken piston ring or scored cylinder, you may need to consult a qualified mechanic or machine shop for further diagnostics and repairs.
Luke Bryan's Boat: A Luxurious Watercraft
You may want to see also
Check for a dropped valve seat
A dropped valve seat is a common issue that mechanics encounter and can lead to severe problems if not addressed quickly. It is caused by inadequate valve size, excessive valve-spring pressure, poor-quality valve-seat material, or an insufficient seal between the valve face and seat. Other causes include extended high-revving engine operation, improper valve adjustment, or foreign material in the combustion chamber. Overheating is a significant factor, as it causes thermal expansion, which weakens the seat.
To check for a dropped valve seat, start by performing a compression check. If the engine is misfiring or there is a noticeable knock, a dropped valve seat could be the culprit. Remove the valve cover and check if all the valve stem tips are at the same height. If a seat has dropped, the corresponding cylinder will have little to no compression, resulting in a misfire.
If you suspect a dropped valve seat, the next step is to remove the cylinder head for further inspection. This will require a jack, jack stand, and a torque wrench to loosen the head bolts safely. Once the cylinder head is off, inspect the valve seat for any warping or cracks. If the seat is damaged, it will need to be replaced.
Before installing a new valve seat, measure the seat bore to determine the correct valve size. You may need to rebore the cylinder head if the bore diameter is not standard. Resurface the valve surface using an abrasive stone, ensuring precision and cleanliness. Install the new valve at the desired angle, ensuring a proper fit. Torque the valve pairs adequately, as this step is crucial for a successful repair.
Finally, reinstall the cylinder head, adhering to the manufacturer's instructions, and test the system. This may involve filling the cylinders with oil and cranking the engine. Always follow safety protocols when working on engine components.
Bottom Paint: A Boat Owner's Dilemma?
You may want to see also
Look for a broken valve spring
If your boat engine compression is too low, there are several potential causes. One of them is a broken valve spring. Valve springs are responsible for keeping the valves closed, which control the inlet and exhaust of the internal combustion engine. A broken valve spring can cause various problems, including excessive valve noise, compression loss, and severe internal engine damage.
To diagnose a broken valve spring, you can start by performing a visual inspection. Look for any irregularities in the spring's shape or any signs of physical damage. A broken valve spring may be visibly shorter than the others, or you may notice metal fragments around the valve train area.
The next step is to perform a compression test. This test will help you check for inconsistencies in cylinder pressure. If one cylinder shows significantly lower pressure than the others, it could indicate an issue with a valve spring. However, keep in mind that a normal compression test might not always catch a broken valve spring, especially if the break is small.
Finally, it is recommended to perform a leak-down test. This test is more detailed than a compression test and can help identify whether a broken valve spring is causing compression loss. By introducing air into each cylinder and measuring the amount of escape, you can pinpoint the issue. If there is a significant amount of air escaping through the intake or exhaust, it could indicate that a broken valve spring is allowing the valve to remain open.
If you suspect a broken valve spring, it is essential to consult a professional mechanic for an accurate diagnosis and repair. They will have the experience and tools to properly address the issue and prevent further damage to your boat engine.
- Visual Inspection: During the visual inspection, look for any visible signs of damage or irregularities in the valve spring. Pay attention to the length of the spring and compare it to the other springs. A broken spring may appear visibly shorter. Also, check for any metal fragments or debris around the valve train area, which could indicate a broken spring.
- Compression Test: The compression test will help you check the cylinder pressure in your engine. If one cylinder shows significantly lower pressure than the others, it could be a sign of a broken valve spring. However, keep in mind that a normal compression test might not always detect a broken valve spring, especially if the break is minor.
- Leak-Down Test: The leak-down test is a more detailed and comprehensive test that can help identify compression loss. By introducing air into each cylinder and measuring the amount of air that escapes, you can determine if there is an issue with the valves not closing properly due to a broken valve spring. This test will help you pinpoint the exact location of the problem.
- Consult a Professional Mechanic: Given the complexity of boat engine components, it is always recommended to consult a professional mechanic. They will have the necessary tools, experience, and expertise to accurately diagnose and repair a broken valve spring. A mechanic can also perform a thorough inspection to identify any other underlying issues that may be contributing to the low compression.
- Get a Detailed Inspection: A professional mechanic will be able to perform a detailed inspection beyond a visual check. They will have the knowledge to identify any other potential issues with your boat engine and ensure a comprehensive repair.
- Discuss the Repair Process: When consulting a mechanic, ask them to explain the repair process. Understanding the steps involved in replacing a broken valve spring and any necessary adjustments will help you make an informed decision and ensure a smooth repair process.
- Assess Your Skills and Tools: If you are considering a DIY repair, honestly assess your mechanical skills and the tools you have available. Replacing a valve spring requires specific tools, such as a valve spring compressor, and a deep understanding of engine mechanics.
- Research Thoroughly: If you decide to proceed with a DIY repair, conduct thorough research and look for reliable guides or tutorials specific to your boat engine's make and model. Having detailed, step-by-step instructions will be crucial for a successful repair.
- Safety First: Always prioritize safety when working on your boat engine. Follow all safety guidelines, including disconnecting the battery and ensuring the engine is cool before starting any repair work.
The Perfect Guide to Titling Your Jon Boat
You may want to see also
Frequently asked questions
You can check your boat's engine compression by using a compression tester. Remove the spark plugs and insert the compression tester into the first cylinder. Crank the engine with a starter or pull cord and note the reading. Repeat this process for each cylinder. If your engine is warm, you can begin by running the engine until it warms up to normal operating temperature.
If your boat engine has low compression, you should take it to a mechanic to get it repaired. The mechanic will identify the cause of the low compression and replace the necessary parts. Common causes of low compression include head gasket failure, leaking head gasket, worn-out head gasket, carbon-clogged piston rings, and broken or worn piston rings.
It is not recommended to drive your boat if one cylinder has low compression as it can cause further damage to the engine. However, your boat will still run but not as fast, and it will stop from time to time.