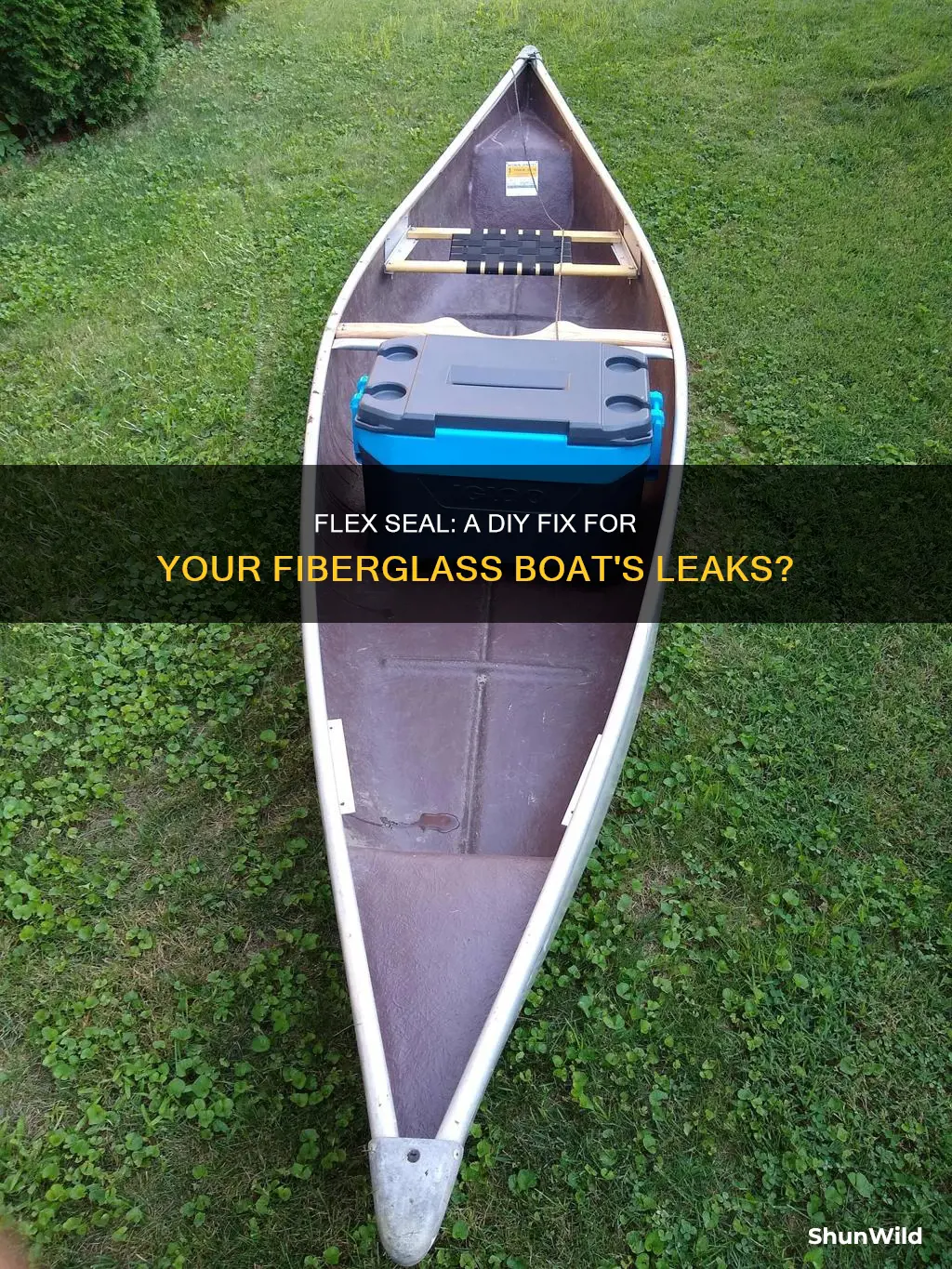
Flex Seal is a popular product known for its versatility in sealing various surfaces, but its effectiveness on fiberglass boats is a common question among boat owners. This paragraph introduces the topic by addressing the concerns and providing a brief overview:
For those considering using Flex Seal on their fiberglass boat, it's important to understand the product's capabilities and limitations. While Flex Seal has proven effective in sealing gaps and cracks in various materials, its application to fiberglass boats requires careful consideration. This introduction aims to explore the potential benefits and challenges of using Flex Seal on fiberglass, offering insights into its suitability for this specific use case.
What You'll Learn
- Flex Seal Application: Follow manufacturer's instructions for best results
- Fiberglass Boat Surface: Ensure surface is clean, dry, and free of debris
- Durability Testing: Perform tests to assess long-term effectiveness on fiberglass
- Environmental Factors: Consider temperature, UV exposure, and water conditions
- Maintenance and Care: Regularly inspect and maintain treated fiberglass boat
Flex Seal Application: Follow manufacturer's instructions for best results
When it comes to applying Flex Seal to a fiberglass boat, it's crucial to follow the manufacturer's instructions for optimal results. Flex Seal is a versatile product known for its ability to provide a temporary fix for various issues, but it's essential to use it correctly to ensure long-lasting protection. Here's a step-by-step guide to help you get the most out of your Flex Seal application:
Preparation: Before applying Flex Seal, ensure the surface of your fiberglass boat is clean and dry. Remove any dirt, grease, or old sealants to create a smooth and receptive base for the product. If there are any small holes or cracks, consider filling them with a suitable filler to ensure a seamless application.
Application Process: Start by reading the manufacturer's instructions carefully, as the process may vary slightly depending on the specific Flex Seal product you are using. Typically, you will need to apply a generous layer of Flex Seal to the desired area, ensuring complete coverage. Allow the initial coat to dry for the recommended time, which is usually a few hours. This initial coat acts as a primer, preparing the surface for the final application.
Multiple Coats: For best results, apply multiple thin coats of Flex Seal rather than a single thick layer. This technique ensures better adhesion and a more even finish. Allow each coat to dry thoroughly before applying the next one. The manufacturer's instructions will provide guidelines on the drying time between coats.
Curing and Protection: After the final coat of Flex Seal has been applied, allow sufficient time for it to cure. The curing process may take several days, depending on the product and environmental conditions. Once cured, your Flex Seal application will provide a protective barrier against water, corrosion, and other elements. Remember to follow the manufacturer's guidelines for post-application care to ensure the longevity of the seal.
By adhering to the manufacturer's instructions, you can maximize the effectiveness of Flex Seal on your fiberglass boat. This approach ensures that the product is applied correctly, providing the desired protection and results. Always prioritize safety and consult the product's guidelines for any specific precautions or recommendations.
Mastering Small Boat Sailing: A Guide to Efficient Sailing
You may want to see also
Fiberglass Boat Surface: Ensure surface is clean, dry, and free of debris
Before applying any sealant, it's crucial to ensure the surface of your fiberglass boat is in optimal condition. Start by thoroughly cleaning the area where you plan to apply the Flex Seal. Fiberglass is a porous material, and any dirt, grime, or old sealant residue can prevent the new sealant from adhering properly. Use a mild detergent mixed with water to scrub the surface gently. Rinse thoroughly with clean water to remove all traces of the detergent. Ensure that the surface is completely dry before proceeding. Moisture can interfere with the bonding process, leading to potential issues with the sealant's effectiveness.
After cleaning, inspect the surface for any remaining debris or imperfections. Fiberglass can sometimes have small pores or imperfections that need to be addressed. Use fine-grit sandpaper (around 400-600 grit) to gently smooth out any rough spots and create a more uniform surface. This step is essential to ensure that the Flex Seal adheres evenly and effectively. Once the surface is smooth and free of debris, wipe it down with a clean cloth to remove any dust or particles that may have been generated during sanding.
Drying is another critical aspect of preparing the fiberglass boat surface. Ensure that the area is completely dry before applying the sealant. Moisture can cause the sealant to lift or peel off over time. If the surface feels damp to the touch, allow it to air dry for a few more hours or use a hairdryer on a low setting to speed up the process. Patience is key here; rushing the drying process can lead to issues with the sealant's performance.
Additionally, pay attention to any existing damage or repairs on the fiberglass. If there are any holes, cracks, or other significant imperfections, it's best to address them first. Flex Seal is not a structural repair material and should not be used to fill large gaps or holes. Consider using a suitable fiberglass repair kit for such issues, ensuring a smooth and solid surface before applying the sealant.
By following these steps, you'll create an ideal environment for the Flex Seal to bond effectively with the fiberglass boat surface, ensuring a durable and long-lasting repair or protection. Remember, proper preparation is key to achieving the best results with any sealant application.
Boat Registration Renewal in Tennessee: Who to Contact
You may want to see also
Durability Testing: Perform tests to assess long-term effectiveness on fiberglass
When considering the use of Flex Seal on a fiberglass boat, it's crucial to understand the long-term effectiveness and durability of this product. Fiberglass, being a composite material, requires specific care and attention to ensure its longevity and structural integrity. Here's a detailed guide on how to perform durability tests to assess the suitability of Flex Seal for your fiberglass boat:
Environmental Exposure Testing:
Subject the boat to various environmental conditions to simulate real-world usage. Expose the Flex Seal application to different temperatures, humidity levels, and UV radiation. This can be done by placing the boat in a controlled environmental chamber or by outdoor exposure tests over an extended period. Observe and record any changes in the Flex Seal's appearance, such as cracking, peeling, or discoloration.
Water Resistance:
Perform a water resistance test by submerging the boat in water for an extended duration. Ensure that the Flex Seal is fully submerged and exposed to water pressure. Observe if there is any seepage or leakage through the sealed areas. This test will help determine if the Flex Seal can effectively prevent water intrusion, which is crucial for boat maintenance.
Flexibility and Movement:
Fiberglass structures can experience movement and expansion due to temperature changes and structural stress. Perform tests to assess the Flex Seal's flexibility and ability to accommodate these movements. Apply controlled stress to the sealed areas and observe if there is any delamination or separation of the Flex Seal from the fiberglass surface. This test ensures that the product can adapt to the boat's dynamic nature.
Abrasion Resistance:
Simulate the wear and tear that the boat might experience during its lifetime. Use abrasive materials or tools to create controlled scratches or scuffs on the Flex Seal-treated areas. Observe the surface for any signs of damage, such as wear or loss of material. This test will help determine the product's ability to withstand the boat's operational environment.
Long-Term Observation:
Conduct regular inspections of the Flex Seal-treated fiberglass over an extended period. Look for any signs of degradation, such as chalking, fading, or loss of adhesion. Monitor the boat's performance and note any changes in its structural integrity. Long-term observation will provide valuable insights into the product's durability and its ability to maintain the boat's appearance and functionality.
By conducting these durability tests, you can make an informed decision about the suitability of Flex Seal for your fiberglass boat. It is essential to consider the specific requirements of your boat's design and the potential environmental factors it will encounter. Proper testing will ensure that the chosen sealing solution provides the necessary protection and longevity for your fiberglass vessel.
Testing a Boat Starter: A Step-by-Step Guide
You may want to see also
Environmental Factors: Consider temperature, UV exposure, and water conditions
When considering the application of Flex Seal to a fiberglass boat, it's crucial to take into account various environmental factors that can influence its effectiveness and longevity. Temperature plays a significant role in the performance of any sealant, and Flex Seal is no exception. Extreme temperatures, whether hot or cold, can affect the material's flexibility and adhesion properties. In very cold conditions, the sealant may become brittle, leading to potential cracking or peeling over time. Conversely, high temperatures can cause the sealant to become soft and lose its structural integrity, especially in areas with intense sunlight. Therefore, it is essential to apply Flex Seal when the temperature is moderate, ensuring optimal curing and performance.
UV exposure is another critical factor to consider. Fiberglass boats are often exposed to direct sunlight, which contains ultraviolet (UV) rays. These rays can cause degradation of the sealant's polymer components, leading to a loss of flexibility and adhesion. Flex Seal, being a rubber-based sealant, is generally resistant to UV radiation, but prolonged and intense exposure can still impact its performance. To mitigate this, it is advisable to apply a UV-resistant clear coat or topcoat after sealing to provide an additional layer of protection against the sun's harmful rays.
Water conditions are particularly important for boat owners, as they directly affect the boat's integrity and the sealant's performance. Fiberglass boats are inherently porous, and any sealant applied must be able to withstand the constant exposure to water. Flex Seal, when properly applied and cured, can create a barrier that helps prevent water absorption and intrusion. However, in areas with high water pressure or frequent immersion, the sealant's ability to maintain its integrity becomes crucial. Reinforcing the sealed areas with additional layers or using a marine-grade sealant can provide added protection against water damage.
Additionally, the salinity of the water should be considered, especially if the boat is used in saltwater environments. Salty water can accelerate the degradation of certain sealants, so it is essential to choose a sealant that is compatible with marine conditions. Flex Seal, being a general-purpose sealant, may not offer the same level of resistance to saltwater corrosion as specialized marine sealants. Therefore, combining Flex Seal with appropriate marine-grade products can ensure a more robust and long-lasting solution.
In summary, when applying Flex Seal to a fiberglass boat, environmental factors such as temperature, UV exposure, and water conditions should be carefully evaluated. Proper temperature control during application, considering UV protection, and addressing specific water-related challenges will contribute to a successful and durable sealant job. Understanding these factors will help ensure the longevity and performance of the Flex Seal on your fiberglass boat.
Galley Boats: History, Design, and Purpose Explained
You may want to see also
Maintenance and Care: Regularly inspect and maintain treated fiberglass boat
When it comes to maintaining a fiberglass boat, regular inspection and maintenance are crucial to ensure its longevity and performance. Fiberglass is a popular material for boat construction due to its durability and lightweight nature, but it requires specific care to prevent damage and maintain its structural integrity. Here's a comprehensive guide on how to regularly inspect and maintain your treated fiberglass boat:
Visual Inspection: Start by performing a thorough visual inspection of the boat's exterior and interior. Look for any signs of damage, such as cracks, chips, or delamination. Pay close attention to areas that are more prone to wear and tear, including the hull, deck, and cabin. Check for any visible signs of water infiltration, such as discolored or warped surfaces, as these could indicate underlying issues. Regularly inspect the boat's seams and joints, as these areas can be susceptible to damage over time. Look for any signs of corrosion or rust, especially around metal fittings and hardware.
Surface Maintenance: Keep the fiberglass surface clean and free from debris. Use a soft-bristled brush or a non-abrasive pad to gently remove any dirt or grime. Avoid using harsh chemicals or abrasive cleaners that can damage the gelcoat. Instead, opt for mild detergents or specialized fiberglass cleaners. Regularly wax the boat's surface to protect the gelcoat and maintain its shine. This simple step can help prevent UV damage and keep the boat looking its best.
Structural Integrity Checks: Inspect the boat's structural components, including the hull, stringers, and bulkheads. Check for any signs of structural damage, such as delamination or voids between layers. These issues can compromise the boat's strength and stability. Ensure that all fasteners and hardware are tight and secure. Regularly check the condition of the boat's core, especially if it's made of foam or balsa wood, as these materials can absorb moisture and weaken over time.
Sealing and Repair: Fiberglass boats often require sealing to protect against water intrusion. Inspect all seams, hatches, and openings to ensure they are properly sealed. If you notice any gaps or damage, use a high-quality marine-grade sealant to repair and seal the affected areas. Flex Seal, for example, can be an effective temporary fix for small gaps, but for more permanent solutions, consult a professional boat repair specialist. Remember that sealing should be done regularly, especially after any repairs or modifications.
Regular Maintenance Schedule: Establish a regular maintenance routine to stay on top of your boat's care. Create a checklist to ensure you inspect all critical areas during each maintenance session. Consider keeping a logbook to record the inspections, repairs, and any issues encountered. This documentation will help you track the boat's condition over time and provide valuable reference points for future maintenance.
Moor Your Sailing Boat: A Step-by-Step Guide
You may want to see also
Frequently asked questions
Yes, Flex Seal can be applied to fiberglass surfaces. It is a versatile product that can bond to various materials, including composites like fiberglass. However, it's important to ensure the surface is clean and dry before application.
While Flex Seal can be used on boats, it is not specifically designed for marine applications. Marine environments often require products that are more resistant to saltwater and UV rays. For best results, consider using marine-grade sealants or coatings.
Flex Seal can be used for temporary repairs, but it is not a structural adhesive. For more permanent solutions, it's recommended to use specialized boat repair kits or seek professional help. Flex Seal can provide a protective barrier and help prevent further damage.
The durability of Flex Seal on a boat depends on various factors, including the quality of the product, application, and environmental conditions. It may provide temporary protection, but for long-term solutions, consider marine-specific sealants or coatings.
Absolutely! Proper preparation is key. Clean the surface to remove dirt and grime. Ensure the area is dry and free of any moisture. You might also want to sand the surface slightly to create a better bond. Always follow the manufacturer's instructions for the best results.