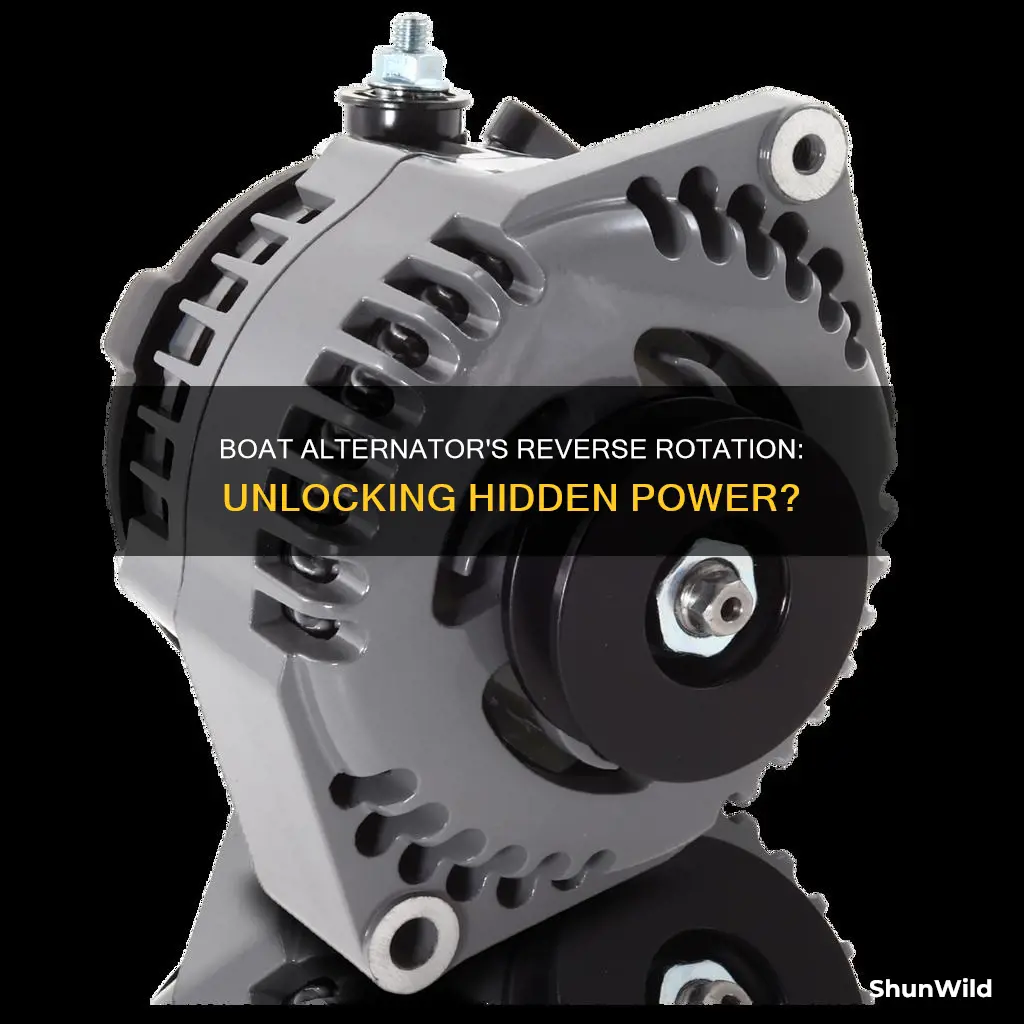
The concept of a boat alternator working in reverse rotation is an intriguing one, especially for those interested in marine engineering and electrical systems. This topic delves into the functionality of alternators, which are crucial components in power generation for boats. Understanding whether an alternator can function in reverse rotation is essential for maintenance and troubleshooting, as it can provide insights into potential issues and help optimize the performance of the electrical system. By exploring this subject, we can uncover the mechanisms behind alternator operation and their adaptability to different rotational scenarios.
Characteristics | Values |
---|---|
Functionality | A boat alternator can function in reverse rotation, but it may not be efficient or safe. |
Power Output | The power output may be reduced or reversed, depending on the design and load. |
Voltage Regulation | Voltage regulation might be affected, leading to potential voltage fluctuations. |
Current Direction | Current will flow in the opposite direction, which could impact battery charging and electrical systems. |
Motor/Generator | Some alternators can act as motors when connected to a power source, allowing for reverse rotation. |
Applications | Reverse rotation can be useful in specific scenarios, such as emergency backup or unique mechanical systems. |
Safety Considerations | Operating an alternator in reverse rotation may require additional safety measures to prevent damage or hazards. |
Maintenance | Regular maintenance is essential to ensure optimal performance and longevity, regardless of rotation direction. |
What You'll Learn
- Alternator Basics: Understanding alternator function and how it works in a boat
- Reverse Rotation: Exploring the concept of reversing alternator rotation and its implications
- Mechanical Considerations: Analyzing the mechanical aspects of alternator operation in reverse
- Performance Impact: Investigating the performance effects of reversing alternator rotation
- Safety Measures: Identifying safety protocols for working with a reversed alternator
Alternator Basics: Understanding alternator function and how it works in a boat
An alternator is a crucial component in a boat's electrical system, responsible for generating the electrical power needed to run various systems and accessories. It is essentially a device that converts mechanical energy into electrical energy, ensuring a steady supply of power for the boat's operations. Understanding how an alternator functions is essential for boat owners and operators to maintain and troubleshoot their vessel's electrical system effectively.
The alternator's primary role is to charge the battery while providing power to the boat's electrical circuits. When the engine is running, the alternator uses the mechanical energy from the engine's rotation to generate an alternating current (AC) electrical charge. This process is similar to what you might observe in a car, where the alternator keeps the battery charged and powers the vehicle's electrical components. In a boat, this function becomes even more critical as it relies solely on the engine for power generation.
The alternator's operation is based on the principle of electromagnetic induction. It consists of a rotor (or armature) and a stator. The rotor is typically connected to the engine's crankshaft, which rotates it. Inside the alternator, there are coils of wire (the stator) that are positioned around the rotor. As the rotor spins, it creates a magnetic field that induces an electric current in the stator coils, thus generating electrical power.
One important aspect of alternator function is its ability to adjust its output based on the engine's speed. As the engine's RPM (revolutions per minute) increases, the alternator's output voltage and current also increase, ensuring a consistent power supply. This feature is vital for maintaining the stability of the boat's electrical system, especially during varying engine speeds.
In the context of your question, regarding the alternator working in reverse rotation, it is essential to understand that the alternator's functionality is designed around the engine's rotation. If the alternator were to rotate in the opposite direction, it would not generate power in the intended manner. The alternator's design and internal components are optimized for a specific rotational direction to ensure efficient power generation and battery charging. Attempting to reverse the alternator's rotation might lead to damage or malfunction, highlighting the importance of proper installation and maintenance.
Unveiling the Mechanics: How Boat Gas Stations Fuel Watercraft
You may want to see also
Reverse Rotation: Exploring the concept of reversing alternator rotation and its implications
The concept of reversing the rotation of an alternator in a boat is an intriguing one, and it delves into the heart of electrical systems and their functionality. When we talk about alternators, they are typically designed to operate in a specific direction, generating electricity based on the rotation of the engine. However, the idea of reversing this rotation opens up a world of possibilities and considerations.
In a boat's electrical system, the alternator is a crucial component, responsible for converting mechanical energy from the engine into electrical power. It operates in a specific rotational direction, often synchronized with the engine's rotation. This synchronization ensures that the alternator efficiently charges the battery and powers the various electrical components on board. But what happens when we consider reversing this rotation?
Reversing the alternator's rotation implies altering the direction of power generation. Instead of the alternator spinning in the normal direction, it would rotate in the opposite way. This concept might seem counterintuitive, as it challenges the fundamental design and purpose of the alternator. However, understanding the implications of such a reversal is essential for anyone working with boat electrical systems.
One of the key considerations is the impact on the battery charging process. When the alternator rotates in the normal direction, it efficiently charges the battery by converting mechanical energy into electrical power. If the rotation is reversed, the alternator might not be able to charge the battery effectively, leading to potential issues with power supply. Ensuring that any reversed rotation setup can still provide adequate power to the battery is crucial.
Additionally, reversing the alternator's rotation could affect the overall performance and functionality of the boat's electrical system. Many electrical components are designed to work in harmony with the alternator's normal rotation. Altering this rotation might require adjustments or modifications to ensure compatibility and prevent damage to sensitive electronics. It is a delicate balance between exploring innovative concepts and maintaining the reliability of the system.
In conclusion, exploring the concept of reversing alternator rotation in boats opens up a fascinating discussion on electrical system design and functionality. While it may present challenges and require careful consideration, understanding these implications is vital for anyone working with boat electrical systems. It highlights the importance of adhering to the manufacturer's specifications and the potential need for customization to accommodate unique or experimental setups.
The Mystery of Bryan Baumer's Boat: What Went Wrong?
You may want to see also
Mechanical Considerations: Analyzing the mechanical aspects of alternator operation in reverse
When considering the mechanical aspects of an alternator operating in reverse rotation, several key factors come into play. Firstly, the alternator's design and construction play a crucial role in determining its ability to function in reverse. Most alternators are designed to operate in a specific direction, typically clockwise or counterclockwise, depending on the application. The internal components, such as the rotor and stator, are carefully arranged to optimize power generation in this intended direction.
In reverse rotation, the mechanical stress on the alternator's components can be significant. The rotor, which is responsible for generating the magnetic field, may experience increased wear and tear due to the reversed direction of rotation. This can lead to potential issues such as rotor imbalance, increased vibration, and reduced overall efficiency. Additionally, the bearings and mounting systems that support the rotor must be able to withstand the additional forces and stresses caused by the reverse rotation.
Another important consideration is the impact on the electrical output. Alternators are designed to convert mechanical energy into electrical energy through electromagnetic induction. When operating in reverse, the alternator may not be able to produce the same level of electrical power as it would in the forward direction. This is because the magnetic flux and the rate of change of flux may not align optimally with the stator's windings, resulting in reduced voltage and current output.
Furthermore, the mechanical linkage between the engine and the alternator becomes crucial. In a boat application, the engine's crankshaft is typically connected to the alternator via a pulley system. When operating in reverse, the pulley system must be designed to handle the additional torque and ensure smooth power transmission. This may require modifications or adjustments to the pulley sizes, belt or rope tension, and overall system design.
To ensure the alternator operates reliably in reverse, it is essential to consider the specific requirements of the boat's electrical system. This includes evaluating the load demands, voltage regulation, and the overall electrical configuration. Proper grounding, wiring, and protection mechanisms should be in place to handle any potential issues arising from reverse operation. Additionally, regular maintenance and inspection of the alternator and its associated components are vital to identify and address any mechanical or electrical problems that may occur.
Step Brothers' Boat: A Cinematic Adventure
You may want to see also
Performance Impact: Investigating the performance effects of reversing alternator rotation
The concept of reversing the rotation of a boat alternator is an intriguing one, and it can have significant implications for the overall performance of the vessel. When an alternator operates in reverse rotation, it essentially functions as a generator, converting mechanical energy back into electrical energy. This phenomenon is often explored in experimental setups and can provide valuable insights into the behavior of electrical systems.
In a typical boat alternator setup, the alternator is designed to rotate in a specific direction, generating electrical power from the engine's mechanical energy. However, when the rotation is reversed, the alternator becomes a generator, and its performance characteristics change. The primary performance impact lies in the voltage and current output. As the alternator spins in the opposite direction, it will produce a voltage with a reversed polarity, which can affect the charging system's efficiency and the overall electrical load on the boat.
The performance of the boat's electrical system is closely tied to the alternator's rotation. When the alternator is driven in reverse, it may result in a decrease in charging efficiency, as the system might struggle to maintain optimal voltage levels. This can lead to undercharging batteries, affecting their overall capacity and lifespan. Additionally, the current output might change, potentially causing issues with sensitive electronic components or requiring adjustments to the wiring and circuit protection.
Furthermore, the mechanical aspects of the alternator should be considered. Reversing the rotation could impact the alternator's lifespan and reliability. The bearings and internal components might experience increased wear and tear due to the reversed stress, potentially leading to premature failure. It is crucial to ensure that the alternator is designed to handle such reverse rotation, especially in marine environments where corrosion and moisture can further accelerate component degradation.
In summary, reversing the alternator rotation on a boat has a direct impact on its performance and overall electrical system efficiency. It can affect voltage and current output, potentially causing issues with charging and electrical loads. Additionally, the mechanical aspects of the alternator should be carefully evaluated to ensure longevity and reliability. Understanding these performance implications is essential for marine engineers and enthusiasts who aim to optimize the electrical systems of their boats.
Crestliner Boat: Kick-Starting Your Adventure
You may want to see also
Safety Measures: Identifying safety protocols for working with a reversed alternator
When dealing with a boat alternator, it's crucial to understand the implications of reversing its rotation, as it can significantly impact performance and safety. Before attempting any work, it's essential to consult the manufacturer's guidelines and understand the specific requirements of your alternator. Reversing the alternator's rotation can lead to several potential issues, including reduced efficiency, increased wear and tear, and even damage to the electrical system. Therefore, it's imperative to approach this task with caution and adhere to strict safety protocols.
One of the primary safety measures is to ensure that the alternator is properly secured and mounted. When reversing the rotation, the alternator's mounting system may need to be adjusted to accommodate the new orientation. This process requires careful attention to detail to prevent the alternator from becoming loose or shifting during operation, which could lead to accidents or damage. It is recommended to use appropriate fasteners and ensure they are tightened according to the manufacturer's specifications.
Before starting any work, it is imperative to disconnect the battery and the alternator from the electrical system. This step is crucial to prevent any accidental electrical shocks or short circuits. By cutting the power supply, you minimize the risk of electrical hazards and ensure a safer working environment. Additionally, it is advisable to wear personal protective equipment (PPE), such as insulated gloves and safety goggles, to protect against potential electrical arcs or sparks.
Another critical safety protocol is to inspect the alternator's wiring and connections. Reversing the rotation may require reconfiguring the wiring harness to ensure proper functionality. It is essential to double-check all connections to avoid loose or damaged wires, which could lead to electrical malfunctions. Pay close attention to the ground connections and ensure they are secure and properly insulated to prevent any short circuits.
Furthermore, it is recommended to test the alternator's performance after reversing its rotation. This can be done by connecting a load tester or an oscilloscope to monitor the alternator's output voltage and current. By comparing the results with the original settings, you can identify any deviations or issues caused by the reversal. This testing process helps ensure that the alternator functions correctly and safely, meeting the required specifications.
In summary, working with a reversed boat alternator requires a systematic approach to safety. By following the manufacturer's guidelines, securing the alternator properly, disconnecting the power supply, wearing PPE, inspecting wiring, and testing performance, you can minimize risks and ensure a successful outcome. Always prioritize safety and seek professional assistance if you are unsure about any aspect of the process.
Boat in Peril: When the Propeller Fails
You may want to see also
Frequently asked questions
Yes, a boat alternator can still function even when rotated in reverse. The alternator's ability to generate power is not dependent on the direction of rotation but rather on the speed and efficiency of its internal components. Reverse rotation may not provide optimal performance, but it won't cause any damage to the alternator itself.
Alternator rotation is crucial for the proper functioning of the electrical system in a boat. The alternator's primary role is to convert mechanical energy into electrical energy, which is then used to power various components and charge the battery. The direction of rotation ensures that the alternator can efficiently produce AC (alternating current) electricity, which is essential for the boat's electrical needs.
Testing an alternator's functionality through reverse rotation is a common method. When the alternator is running in reverse, it will produce a voltage, which can be measured using a multimeter. If the alternator is faulty, it may not produce any voltage or a significantly lower voltage compared to when it is running in the correct direction. This test can help diagnose issues with the alternator's internal components or its connection to the battery.
While running an alternator in reverse is generally safe, it may not provide the expected performance. The alternator's efficiency and output power might be reduced, leading to insufficient charging of the battery. Additionally, if the alternator is not designed to handle reverse rotation, it could potentially cause damage to the internal components over time. It is always recommended to use the alternator as per the manufacturer's guidelines to ensure optimal performance and longevity.