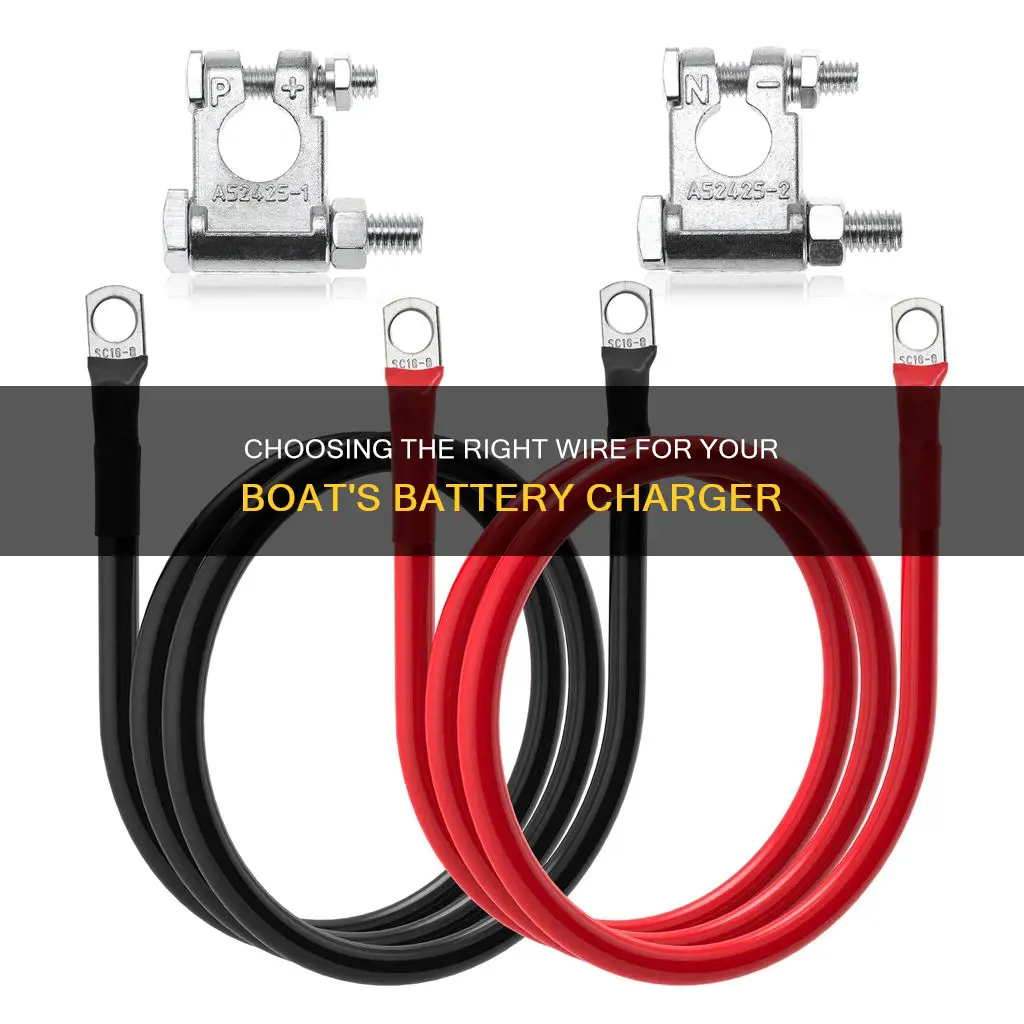
When it comes to wiring a boat, it's important to consult a professional marine electrician. However, if you're looking to wire a boat battery charger, there are a few things to keep in mind.
First, it's crucial to select a charger that follows ABYC and UL 1236 standards to ensure safety and isolation of AC and DC power sources. Additionally, the charger should be able to work with varying input voltages and offer physical on-battery temperature sensing.
When installing the charger, it's important to mount it in a dry location with adequate ventilation, as batteries give off gases that can cause corrosion. The wiring for the charger is straightforward, with DC wiring going from the charger to the batteries, and AC wiring coming from the AC distribution panel to the charger. It's also important to use the correct wire size to avoid voltage drop issues.
Finally, when connecting the wires to the battery, be sure to put the charger wire on top of the big battery cables and use closed barrel terminals to prevent corrosion.
Characteristics | Values |
---|---|
Wire Gauge | Depends on the distance from the charger to the batteries; longer runs require proportionally larger wire. |
Wire Type | Marine-grade |
Wire Colour | Positive wires are red, negative wires are black or yellow |
What You'll Learn
- Wire size matters: Larger wires are better for preventing voltage drop
- Charger placement: Keep it close to the batteries but not too close
- AC wiring: Avoid wire nuts and use crimp-type connections
- DC wiring: Connect the charger to the batteries first
- Battery temperature: Chargers with temperature sensors can adjust the charging voltage
Wire size matters: Larger wires are better for preventing voltage drop
When it comes to boat battery chargers, wire size is a critical factor that can significantly impact the performance and longevity of the charging system. Larger wires are indeed better for preventing voltage drop, and this is why:
Firstly, it's important to understand that voltage drop occurs when there is a loss of electrical power as it travels through a conductor, in this case, the wires. This voltage drop can affect the efficiency of the charging system, and in a marine environment, it is crucial to minimise energy loss. By using larger wires, you decrease the resistance in the circuit, which in turn reduces the voltage drop. This ensures that the battery receives the full voltage from the charger, promoting faster and more effective charging.
Secondly, the distance between the charger and the batteries plays a role in determining the appropriate wire size. Longer runs between the charger and the batteries require the use of proportionally larger wires. If the wires are too small, the voltage drop will be more significant, leading to chronic undercharging of the battery and increased charging times. This is because the charger's output voltage needs to compensate for the voltage drop, and if it fails to do so, the battery will not receive the required amount of voltage to charge effectively.
Additionally, the wire size becomes even more critical when considering the type of battery being charged. Different batteries have different charging requirements, and some batteries benefit from high-current charging. If the wire is too small, it can slow down the charge rate and affect the overall performance of the battery. For example, batteries like Odyssey TPPL AGMs, Northstar TPPL AGMs, and Firefly Carbon Foam require high-current charging (around 40% of installed Ah capacity) for optimal cycle life. Using larger wires helps to accommodate these higher currents without significant voltage drop.
Finally, it's important to consider the presence of any DC loads on the boat that may be drawing power while the battery is being charged. These loads can reduce the amount of current available for charging, and using larger wires can help mitigate this issue. By minimising the voltage drop, you ensure that the battery receives the intended amount of current for effective charging, even with DC loads present.
In summary, larger wires play a vital role in preventing voltage drop, which can have detrimental effects on the performance and longevity of boat battery charging systems. By using larger wires, you reduce resistance, compensate for longer runs, accommodate high-current charging requirements, and ensure sufficient current reaches the battery even with DC loads present. Remember to always refer to the manufacturer's recommendations for wire size and charging guidelines to ensure optimal performance and safety.
Finding Old Boat Registration: A Comprehensive Guide
You may want to see also
Charger placement: Keep it close to the batteries but not too close
When it comes to installing a battery charger on a boat, one of the most common mistakes is placing it too close to the batteries. While it is important to keep the DC cables between the charger and the batteries short, the gases released by the batteries during charging can cause corrosion and shorten the life of the charger, especially if the batteries are of the liquid electrolyte type.
So, what is the ideal placement for a boat battery charger? The answer is a balance between proximity to the batteries and ventilation. Here are some guidelines to help you find the perfect spot:
- Avoid placing the charger directly above the batteries. Instead, look for a location that is relatively close but not directly over them. This will help prevent the charger from being exposed to the gases released during charging.
- Choose a dry and well-ventilated area for the charger. If you must place it in a cockpit locker or lazarette, tuck it away in a dry corner, avoiding direct exposure to moisture.
- Provide adequate breathing room for the charger. Do not stuff it in with life jackets or other gear, as it needs proper ventilation to stay cool and function optimally.
- Consider the weight of the charger when fastening it in place. For heavier chargers, use through-bolting, while screws can be sufficient for lighter chargers if attached to a thick bulkhead or structure. Always use stainless steel fasteners for durability.
- Keep the charger away from the engine space, if possible. Engine compartments tend to remain warm even after the engine has been turned off, and water heaters can further elevate temperatures, impacting the performance and longevity of the charger.
- Avoid mounting the charger directly to the inside of a dark-coloured hull, as temperatures can easily exceed 140°F in direct sunlight.
- Do not install the charger in the battery compartment or engine compartment, as corrosive battery gases can damage the metals in the charger.
- Opt for a location that is clean and free from oils, vapours, or other contaminants. Follow safety guidelines and avoid installing the charger near LPG, gasoline, hydrogen gas, or stored solvents.
- If possible, mount the charger higher in the boat, as areas closer to the bilge tend to have higher humidity and more corrosive environments.
- If there is a risk of water exposure, construct a drip shield to protect the charger while still allowing for proper ventilation.
- Ensure the charger has unobstructed airflow by considering the placement of its inlet and outlet vents, especially if it has a fan.
- If necessary, cut ventilation holes in lockers and cover them with pre-made ventilation grills to balance ventilation and aesthetics.
The Roberts MDL Flats Boat: A Good Buy?
You may want to see also
AC wiring: Avoid wire nuts and use crimp-type connections
When it comes to AC wiring, it is crucial to avoid the use of wire nuts and instead opt for crimp-type connections. This is a critical safety precaution that cannot be overstated.
The dangers of wire nuts lie in their propensity to loosen over time, especially in the constantly vibrating environment of a boat. This can lead to electrical arcing, which poses a severe fire hazard. Additionally, wire nuts are not designed to withstand the harsh marine environment and can corrode, further increasing the risk of electrical issues.
By contrast, crimp-type connections provide a more secure and permanent solution. They create a solid and durable connection that resists loosening due to vibration or other factors. When combined with heat-shrink tubing and corrosion-resistant grease, crimp-type connections offer superior protection against the elements and help ensure the long-term reliability of your boat's electrical system.
It is also worth noting that AC wiring carries a higher risk of electrical faults than DC wiring, making the use of crimp-type connections even more critical for safety. By following these best practices, you can help ensure that your boat's electrical system is safe and reliable for years to come.
When it comes to wiring a boat, it is always advisable to consult a professional marine electrician. They can guide you through the process, ensuring that your boat's electrical system is installed correctly and safely.
Measuring Sail Boats: Finding the Right Model Fit
You may want to see also
DC wiring: Connect the charger to the batteries first
When installing a battery charger on a boat, it is important to follow safety guidelines and manufacturer instructions. Here is a step-by-step guide for DC wiring, specifically connecting the charger to the batteries:
Step 1: Understand Battery and Charger Types
Before beginning any installation, it is crucial to understand the types of batteries and chargers involved. Different batteries, such as flooded, AGM, or gel batteries, may have specific charging requirements. Additionally, the charger should be marine-grade and built to industry standards like ABYC/UL 1236 for safety and isolation of AC and DC.
Step 2: Select Appropriate Wire Size
The wire size, or gauge, between the battery and the charger is critical to the performance of the charging system. Manufacturers usually specify the recommended wire size based on the distance between the charger and the batteries. Using wires that are too small can result in voltage drop and chronic undercharging of the battery. As a general rule, bigger wires are preferable to minimize voltage drop, especially for longer runs.
Step 3: Prepare the Charger and Batteries
Before making any connections, ensure that the batteries are free of corrosion and that the battery posts are clean. The charger should be mounted in a dry location with adequate ventilation and at least 6 inches of clearance. Follow the manufacturer's instructions for mounting and orientation.
Step 4: Connect the Charger to the Batteries
Now, you can connect the charger to the batteries. The positive (+) lead from the charger should be connected to the positive post of the battery, and the negative (-) lead to the negative post, ensuring correct polarity. If the charger has multiple outputs, connect each output to a separate battery. Secure the connections and ensure they are tight.
Step 5: Test the System
Once the connections are made, you can test the system by plugging the charger into an extension cord and then into a GFCI 120-volt AC power outlet. Observe the charger's LED indicators to ensure proper functioning and charging status. If any issues arise, such as a loose connection or reverse polarity, consult the charger's troubleshooting guide.
Remember to disconnect the charger before starting the engine to avoid potential over-voltage situations that could damage sensitive electronic components.
Wet Sanding a Bass Boat: The Ultimate Guide
You may want to see also
Battery temperature: Chargers with temperature sensors can adjust the charging voltage
The temperature of a battery affects how much energy it can absorb during the recharging process. Most charger voltage setpoints are set for room temperature, 25°C [77°F], so if that setpoint is not adjusted for temperature, issues can arise. If the battery gets too warm, it may overcharge and gas, while if it gets too cold, it may undercharge and sulfate. Both of these scenarios can lead to a shortened battery lifespan.
Battery chargers with temperature sensors can adjust the charging voltage to prevent these issues. Some chargers have an internal temperature sensor, while others have remote temperature sensors. Chargers with internal sensors are fine if they are in the same enclosure as the batteries and the internal temperature is similar. If the charger and batteries are in separate enclosures, a remote temperature sensor is more appropriate.
The Sterling ProCharge Ultra, for example, has an on-battery temperature sensor. This sensor is attached to the battery post or case so that it can sense the temperature of the bank correctly. It is important to mount the sensor to the battery that has the most potential to get warmer than the others.
Temperature compensation is especially important in warmer climates, as heat is the worst enemy of most batteries. Chargers exposed to temperature fluctuations should include temperature compensation sensors to adjust the charge voltage for optimum charge efficiency.
Lobster Hulls: Unique Design for Special Boats
You may want to see also
Frequently asked questions
The ideal wire size depends on the distance from the charger to the batteries. Longer runs require proportionally larger wires. The manufacturer's suggested wire size should be used to avoid a voltage drop that can cause the battery to be undercharged and increase charging time.
The AC wiring can be as simple as plugging the charger into an extension cord. For a permanent installation, the charger can be wired from the shore power inlet or an AC distribution panel. Use marine-grade, three-conductor AC cable and follow good wiring practices.
The charger should be mounted in a dry location with adequate ventilation. It should be relatively close to the batteries but not directly above them to avoid exposure to corrosive gasses. Ensure the mounting surface can support the charger's weight and that the DC and AC cords can reach their respective connections.
The positive (red) and negative (black) DC leads from the charger should be connected to the corresponding battery posts, ensuring correct polarity. If the provided leads are too short, you may need to purchase extensions. The connections should be tight and free from corrosion.