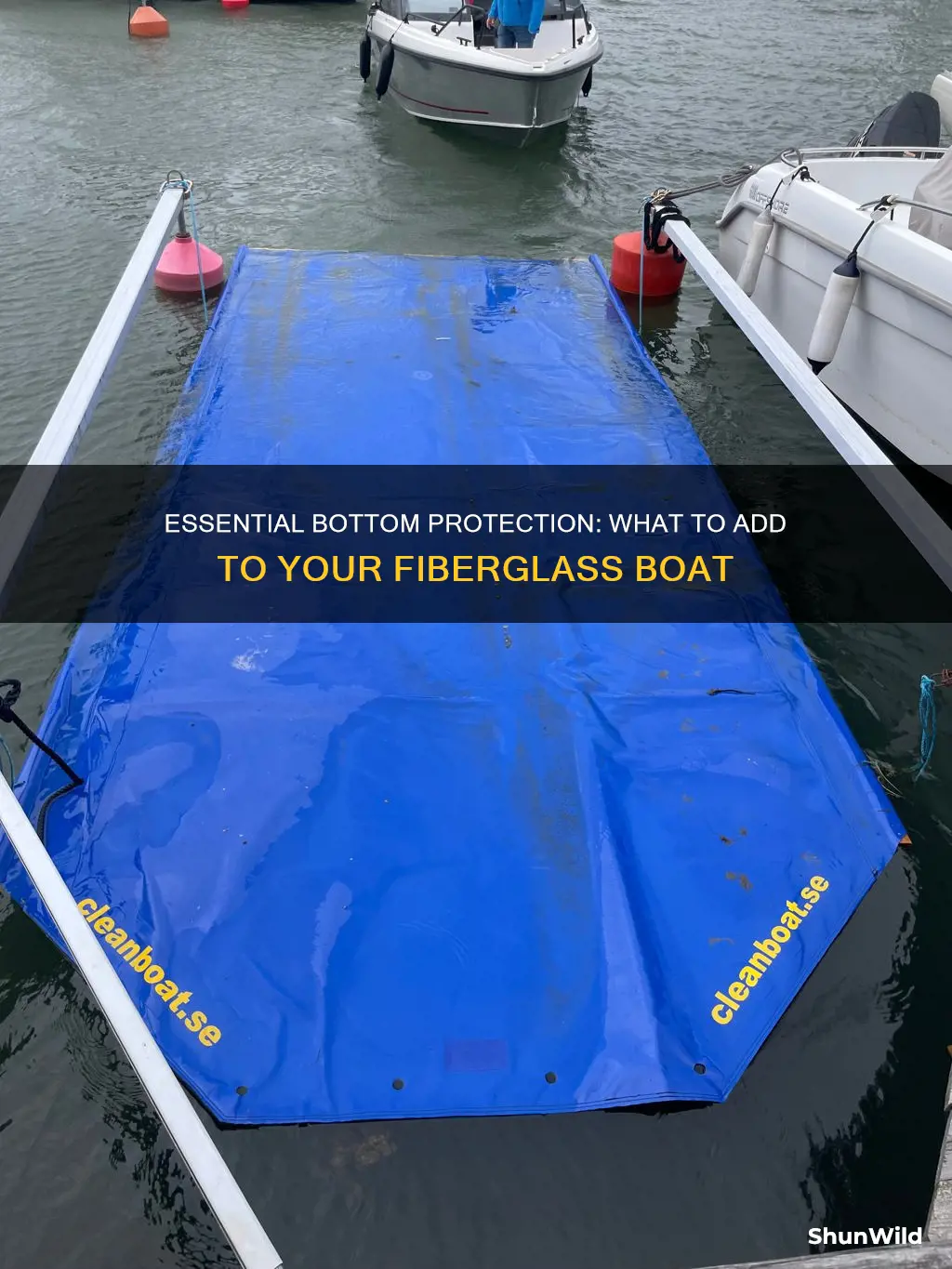
When it comes to the bottom of a fiberglass boat, there are several essential components that contribute to its overall performance and longevity. From providing structural support to enhancing stability and reducing friction, the choice of materials and design considerations play a crucial role. In this article, we will explore the various options available for the bottom of a fiberglass boat, including the use of gelcoat, paint, anti-fouling coatings, and specialized materials like marine-grade epoxy or polyurethane. By understanding the benefits and drawbacks of each option, boat owners can make informed decisions to ensure their vessel remains in top condition.
What You'll Learn
- Non-Skid Surfaces: Textured materials like rubber or carpet for better traction and safety
- Soundproofing: Foam or insulation to reduce engine and wave noise
- Weight Distribution: Balancing materials to ensure stability and prevent sinking
- Corrosion Resistance: Choosing materials that withstand saltwater and marine environments
- Aesthetic Enhancements: Custom paint, graphics, or accessories for a unique look
Non-Skid Surfaces: Textured materials like rubber or carpet for better traction and safety
When it comes to enhancing the functionality and safety of your fiberglass boat, one of the most crucial considerations is the application of non-skid surfaces. These textured materials play a vital role in providing better traction and ensuring the safety of both passengers and the boat's occupants. The primary purpose of non-skid surfaces is to prevent slipping and sliding, especially in wet conditions, which can be extremely dangerous on a moving vessel.
Rubber is an excellent choice for creating non-skid surfaces. It offers a natural texture that provides excellent grip, even when wet. Rubber mats or strips can be easily installed on the boat's deck, steps, and other areas prone to moisture. The flexibility of rubber allows it to conform to the boat's surface, creating a secure and stable footing. Additionally, rubber is durable and resistant to UV damage, ensuring that the non-skid surface remains effective over time.
Carpeting is another popular option for non-skid applications. Boat carpets are specifically designed to mimic the look and feel of traditional carpets while providing excellent traction. These carpets often feature a textured backing that adheres to the boat's surface, creating a secure and non-slip base. Carpeted areas can be strategically placed to cover high-traffic zones, such as the swim platform or the area around the helm station. This not only improves safety but also adds a touch of comfort and style to the boat's interior.
The installation process for non-skid surfaces is relatively straightforward. For rubber, you can opt for pre-cut mats that fit specific areas or customize them to your boat's dimensions. Adhesive backing or double-sided tape can be used for a secure bond. When installing carpet, ensure a proper fit by measuring and cutting the carpet to size. The textured backing of the carpet will provide the necessary grip, and you can choose from various colors and patterns to match your boat's interior design.
Incorporating non-skid surfaces is a simple yet effective way to enhance the overall safety and functionality of your fiberglass boat. By utilizing textured materials like rubber or carpet, you create a more secure environment for passengers and reduce the risk of accidents. Remember to regularly inspect and maintain these surfaces to ensure their effectiveness, especially after exposure to harsh weather conditions or heavy use.
The Ultimate Guide to Replacing Your Boat's Drain Plug
You may want to see also
Soundproofing: Foam or insulation to reduce engine and wave noise
When it comes to soundproofing a fiberglass boat, one of the most effective methods is to use sound-absorbing materials such as foam or insulation. These materials can significantly reduce engine and wave noise, making your boating experience more comfortable and enjoyable. Here's a detailed guide on how to soundproof your boat using foam or insulation:
Understanding the Problem:
Before you begin, it's essential to understand the source of the noise. Engine noise, especially at higher RPMs, can be a significant issue for boat owners. Additionally, the impact of waves hitting the hull can create a lot of noise inside the boat. These two factors are the primary concerns when soundproofing a fiberglass vessel.
Materials and Preparation:
You can use various sound-absorbing materials for soundproofing, but two popular choices are acoustic foam and insulation. Acoustic foam is specifically designed to absorb sound waves and comes in various shapes and sizes. It is lightweight and easy to install, making it a popular choice for boat owners. Insulation, on the other hand, can be made from materials like fiberglass, mineral wool, or foam. It is excellent at blocking sound transmission and can be used to line the interior of the boat.
Installation Process:
Start by cleaning the bottom of the boat to ensure a smooth surface for installation. Measure and cut the foam or insulation to fit the specific areas where you want to reduce noise. Typically, you'll want to cover the engine bay and the hull's interior surface. Use a strong adhesive or marine-grade tape to secure the material to the boat's surface. Ensure that the foam or insulation is tightly fitted to prevent any gaps that could allow sound to pass through.
Benefits of Foam:
Acoustic foam is an excellent choice for soundproofing due to its lightweight nature and ease of installation. It comes in various colors and textures, allowing you to customize the look of your boat while improving sound absorption. Foam can be cut to fit irregular shapes and contours, making it versatile for different boat designs. Additionally, foam is relatively inexpensive compared to other soundproofing materials, making it an affordable option for boat owners.
Insulation for Comprehensive Soundproofing:
For a more comprehensive soundproofing solution, consider using insulation in conjunction with foam. Insulation can be placed behind the foam or directly on the hull to block sound transmission. This combination approach ensures that both the impact of waves and engine noise are minimized. Insulation is particularly effective at reducing low-frequency sounds, which are often the most challenging to control.
By implementing these soundproofing techniques, you can create a quieter and more comfortable environment inside your fiberglass boat. Remember to choose the right materials, prepare the surface adequately, and ensure proper installation for optimal results. Enjoy your boating adventures with a significantly reduced noise level!
Dagger Axiom: The Perfect Beginner Boat?
You may want to see also
Weight Distribution: Balancing materials to ensure stability and prevent sinking
When it comes to ensuring the stability and longevity of your fiberglass boat, weight distribution is a critical factor. Properly balancing the materials and weight on the bottom of the vessel is essential to prevent sinking and maintain its structural integrity. Here's a detailed guide on how to achieve optimal weight distribution:
The first step is to understand the concept of buoyancy and how it relates to your boat's design. Fiberglass, being a lightweight material, relies on buoyancy to stay afloat. However, the weight distribution must be carefully managed to ensure the boat remains stable on the water. The key is to place heavier components in the center of the boat's bottom, closer to the keel, while lighter materials can be used towards the sides and ends. This distribution mimics the natural buoyancy of a vessel, allowing it to float evenly. For instance, the engine, fuel tanks, and other heavy equipment should be positioned in a central location, often referred to as the "center of gravity." This placement ensures that the boat's weight is distributed evenly, preventing it from listing or capsizing.
To achieve this balance, consider using specialized weight distribution plates or blocks. These are typically made of heavy-duty materials like lead or iron and are designed to be placed at specific points on the boat's bottom. By strategically placing these plates, you can adjust the boat's center of gravity, making it more stable. For example, if your boat tends to list when loaded with passengers, adding a weight distribution plate on the affected side can help correct this issue. It's important to consult the manufacturer's guidelines or seek professional advice to determine the exact placement and amount of weight required for your specific boat model.
In addition to the central weight placement, the sides and ends of the boat's bottom should also be considered. These areas often require additional weight to counterbalance the force of the water and prevent the boat from rolling excessively. One common solution is to use lead or iron weights, strategically placed along the sides and ends. These weights act as counterweights, ensuring that the boat remains stable even when subjected to external forces like waves or wind. The key is to find the right balance, as too much weight in these areas can make the boat feel heavy and sluggish, while too little may result in instability.
Furthermore, the use of specialized materials can contribute to effective weight distribution. For instance, incorporating a layer of lead or iron in the boat's bottom structure can provide additional buoyancy and stability. This material can be strategically placed to counterbalance specific areas, ensuring an even distribution of weight. Additionally, the use of lightweight, yet sturdy, materials for the boat's sides and deck can further enhance stability by reducing overall weight.
In summary, achieving optimal weight distribution on a fiberglass boat involves a careful consideration of materials, placement, and design. By understanding the principles of buoyancy and center of gravity, you can ensure that your boat remains stable and safe on the water. Utilizing specialized weight distribution plates, counterweights, and strategic material placement will contribute to a well-balanced vessel, capable of withstanding various conditions. Always refer to manufacturer guidelines and seek expert advice for the best results.
Larson Boats: Worthy Watercraft or Subpar Ships?
You may want to see also
Corrosion Resistance: Choosing materials that withstand saltwater and marine environments
When it comes to protecting the bottom of a fiberglass boat, corrosion resistance is a critical factor to consider, especially in saltwater and marine environments. The harsh conditions of saltwater exposure can accelerate the degradation of materials, leading to costly repairs and potential safety hazards. Here's a detailed guide on choosing materials that offer superior corrosion resistance for your boat's bottom:
- Fiberglass Reinforcement: Fiberglass itself is a composite material that inherently provides some level of corrosion resistance due to its glass fiber reinforcement. However, to enhance this property, consider using specialized fiberglass weaves or fabrics designed for marine applications. These weaves often include glass fibers treated with corrosion-inhibiting agents, ensuring that the boat's structure remains strong and durable even in saltwater.
- Gelcoat and Resins: The gelcoat, a protective outer layer applied to the fiberglass, plays a vital role in corrosion resistance. Opt for a high-quality, marine-grade gelcoat that is specifically formulated to withstand saltwater environments. These gelcoats often contain additives that create a barrier against corrosion, preventing the metal components beneath from coming into contact with saltwater. Additionally, using epoxy resins with corrosion inhibitors can further enhance the boat's resistance to corrosion.
- Bottom Paint: Choosing the right bottom paint is essential for corrosion protection. Traditional anti-fouling paints, while effective, can sometimes contain harmful chemicals. Instead, consider eco-friendly alternatives like biocide-free paints or those with natural antifouling properties. These paints create a barrier on the boat's hull, preventing saltwater and marine organisms from damaging the underlying materials. Look for paints specifically designed for saltwater applications, as they offer superior corrosion resistance.
- Stainless Steel and Aluminum: Incorporating stainless steel or aluminum components in the boat's bottom can significantly improve corrosion resistance. Stainless steel, with its inherent corrosion-resistant properties, is an excellent choice for critical parts like rudders, propellers, and hardware. Aluminum, a lightweight metal, is also highly resistant to saltwater corrosion and can be used for structural components. These materials ensure that the boat's bottom remains protected, even in the most challenging marine conditions.
- Composite Materials: Modern composite materials, such as advanced polymers and reinforced plastics, offer excellent corrosion resistance. These materials are engineered to mimic the strength of traditional metals while providing the lightweight benefits of composites. By utilizing these advanced composites, boat manufacturers can create a robust and corrosion-resistant bottom structure.
In summary, achieving corrosion resistance in a fiberglass boat's bottom requires a multi-faceted approach. From selecting the right fiberglass weaves and gelcoats to incorporating specialized paints and metals, each component contributes to the overall protection. By prioritizing corrosion-resistant materials, boat owners can ensure the longevity and safety of their vessels in saltwater environments.
Dragon Boat Festival: Celebrating in the Summer Solstice
You may want to see also
Aesthetic Enhancements: Custom paint, graphics, or accessories for a unique look
When it comes to enhancing the aesthetics of your fiberglass boat, there are numerous ways to make it stand out on the water. One popular approach is to focus on the bottom, as it often receives less attention compared to the upper parts of the vessel. By adding a unique touch to the bottom, you can create a one-of-a-kind appearance that will turn heads.
Custom paint is an excellent way to transform the appearance of your boat's bottom. You can opt for a vibrant color scheme that contrasts with the rest of the boat, creating a striking visual effect. Consider a bold, high-contrast paint job with a deep, rich color that will make your boat memorable. Alternatively, you could go for a more subtle approach with a custom design, such as a water-themed pattern or a unique color gradient that flows from the bow to the stern. The possibilities are endless, and you can work with professional boat painters to bring your vision to life.
Graphics are another creative way to customize the bottom of your fiberglass boat. Decals and stickers can be used to add intricate designs, logos, or even personalized messages. You can choose from a wide range of pre-made designs or create your own custom graphics. Consider adding a nautical-themed pattern, such as waves, anchors, or fish, to give your boat a fun and playful look. Alternatively, you could go for a more minimalist approach with a single, large graphic that becomes an instant conversation starter.
In addition to paint and graphics, accessories can also contribute to the overall aesthetic appeal. Consider adding custom-made boat skirts or fender covers that not only protect the bottom but also add a stylish element. You can choose from various materials and colors to match your desired theme. Another idea is to install LED lights along the bottom of the boat, creating a stunning visual effect when the boat is in motion or at night. These lights can be customized to your preferred color and intensity, providing both functionality and a unique aesthetic.
Remember, when customizing the bottom of your fiberglass boat, it's essential to consider the overall design and color scheme of the vessel. Ensure that the enhancements you choose complement the existing aesthetics to create a cohesive and visually appealing boat. With the right combination of custom paint, graphics, and accessories, you can transform your boat into a true masterpiece on the water.
Unfastening Your Boat Battery: A Step-by-Step Guide
You may want to see also
Frequently asked questions
A common and effective choice is to use a marine-grade epoxy resin with a glass fiber reinforcement. This provides a strong, durable, and flexible barrier that can withstand the harsh marine environment.
Applying a marine-grade antifouling paint is essential. These paints create a smooth, protective layer that prevents marine growth, barnacles, and other organisms from adhering to the boat's surface. Regular re-painting is necessary to maintain its effectiveness.
Yes, some boaters opt for natural antifoulants like copper-based paints or copper-impregnated paints. These can be effective, but they require careful application and regular maintenance due to the potential environmental impact of copper.
Absolutely! Non-skid surfaces are designed to provide traction and prevent slipping, especially in wet conditions. They can be applied using specialized non-skid paints or by embedding small glass or ceramic particles into the epoxy resin.
Gelcoat is a final layer applied to the fiberglass surface, providing a smooth, colorful finish. It offers some protection against UV rays and minor impacts but is not a primary antifouling measure. It's often used for aesthetic purposes and to enhance the boat's overall appearance.