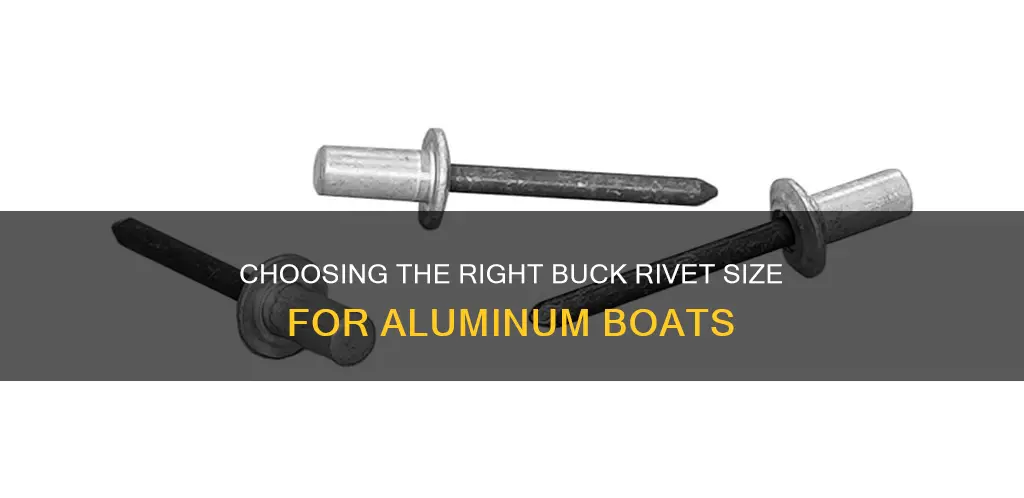
When it comes to repairing an aluminium boat, the type and size of the rivets you use are crucial. Solid rivets are generally preferred over closed-end blind rivets for their superior strength and durability. The most common size for aluminium boat rivets is 3/16 diameter, with varying lengths such as 3/8 or 1/2. It's important to know the thickness of the material where the rivets will be placed to determine the appropriate length. Brazier head rivets are a popular choice for their ability to be deformed with a hammer or rivet gun, forming a secure connection.
What You'll Learn
Solid rivets vs. closed-end blind rivets
When repairing an aluminum boat, it is important to know the differences between solid rivets and closed-end blind rivets.
Solid rivets are the traditional type of rivet, with a solid shaft and a head on one side. They are strong and reliable, and they provide a secure fastening option. Solid rivets are also versatile and can be used in a wide range of applications. However, they require access to both sides of the material being joined, which can be a limitation in some situations.
Closed-end blind rivets, on the other hand, are designed for applications where there is no access to the backside of the joint. They have a unique, cup-shaped end configuration that prevents liquid or gas penetration, making them ideal for watertight applications. Closed-end blind rivets also offer 100% mandrel retention, which means that the head of the mandrel stays inside the rivet, providing a better sealing effect. This type of rivet is commonly used in electronic equipment and electrical applications, as well as in LED signs, scoreboards, and recreational vehicles.
When choosing between solid rivets and closed-end blind rivets for an aluminum boat, there are several factors to consider. Solid rivets offer superior strength and reliability, but they require access to both sides of the material. Closed-end blind rivets are a good choice for watertight applications and where there is limited access, but they may not provide the same level of strength as solid rivets. Additionally, closed-end blind rivets can loosen over time due to vibration and normal working conditions of an aluminum boat.
The size of the buck rivets for an aluminum boat will depend on the thickness of the material being joined. It is important to choose the correct size to ensure a secure fastening. The rivet diameter should be approximately three times the thickness of the material being joined. For example, for a 12' aluminum boat, a common size for solid aluminum rivets is 3/16" x 1/2". Closed-end aluminum blind rivets of the same size are also available and can provide a strong and reliable fastening option.
The Holly Cafe Boat: A Transformative Journey
You may want to see also
Rivet size and thickness
When selecting rivets for an aluminium boat, it is important to consider the thickness of the material that needs to be fastened. The rivet should be long enough to ensure that the bulb end can expand outside of the material being fastened together. For example, if you are fastening two pieces of 1/8" thick aluminium together, a 3/16" x 1/2" rivet would be a suitable choice.
The length of the rivet is crucial, as too short or too long of a rivet can result in the pieces not being held together securely. It is recommended to use a rivet with a body length that is slightly longer than the thickness of the material being fastened. This allows for proper expansion of the rivet and ensures a tight hold.
Additionally, it is important to choose a rivet with the appropriate grip range for the thickness of the material. The grip range refers to the maximum and minimum thickness that the rivet can securely fasten. Using a rivet with the correct grip range will ensure that the rivet is not too loose or too tight.
When replacing rivets in an aluminium boat, it is also important to consider the type of rivet. Solid rivets are commonly used and come in various grades of aluminium. Closed-end blind rivets are another option, especially if you do not have access to the inside of the boat. These rivets are self-sealing and are both vapour and waterproof, making them suitable for use in boat hulls.
To ensure a proper fit and secure fastening, it is recommended to refer to the manufacturer's specifications for the thickness of material that each rivet can securely fasten. Additionally, using a rivet gun or pneumatic rivet tool can make the installation process easier and ensure a tight hold.
Overall, selecting the appropriate rivet size and thickness for an aluminium boat involves considering the thickness of the material, choosing a rivet with the right grip range, and selecting the appropriate type of rivet for the application. By following these considerations, you can ensure a secure and watertight fastening for your aluminium boat.
Boat Requirements in Ohio: What You Need to Know
You may want to see also
Bucking tools
A bucking tool, or bucking bar, acts as an anvil during the installation of a bucked rivet. Bucked rivets are solid rivets that are lightweight, strong, and inexpensive, making them ideal for use in aluminum construction. The rivet is driven by a rivet gun, which strikes the head of the rivet repeatedly. Meanwhile, the bucking bar is held against the tail of the rivet, providing support and ensuring that the rivet is properly formed.
Bucking bars come in various styles, but they typically have multiple faces to accommodate different rivet locations. It is important to keep the faces of the bucking bar clean and corrosion-free. Additionally, the air pressure regulator on the rivet gun should be set to around 90 PSI to ensure optimal riveting.
When riveting, it is common for two people to work together. One person operates the rivet gun, while the other uses the bucking bar to support the rivet. Communication between the two is crucial to ensure the rivet is installed correctly.
Overall, bucking tools are an essential component of the riveting process, and proper use of these tools can result in strong and secure riveted joints in aluminum boats and trailers.
Replacing a Boat Engine: A Step-by-Step Guide for Beginners
You may want to see also
Rivet corrosion and sealing
When it comes to rivet corrosion and sealing in the context of aluminium boats, there are several important considerations to keep in mind. Firstly, corrosion resistance is crucial as rivets are constantly exposed to water and other environmental factors. Aluminium rivets, for instance, require special treatments or coatings to prevent rapid corrosion from saltwater.
One common type of corrosion is galvanic corrosion, which occurs when different metals come into contact in a corrosive environment, such as saltwater. To prevent this, it is important to use rivets that are compatible with the aluminium hull of the boat. For instance, if you are repairing an aluminium boat, it is crucial to use aluminium rivets to avoid galvanic corrosion.
Protective coatings or treatments can also enhance corrosion resistance. Common treatments include anodizing the aluminium or using anti-corrosive sealants like marine-grade silicone. Closed-end rivets are also beneficial for corrosion resistance as they prevent moisture and other corrosive substances from entering the joint, thereby reducing the potential for corrosion and extending the life of the joint.
In addition to corrosion resistance, it is important to consider the strength requirements of the rivets. This includes both tensile strength, which is the maximum stress a rivet can withstand while being stretched or pulled before breaking, and shear strength, which measures the rivet's ability to resist sliding forces.
When replacing rivets, it is recommended to use the same type of rivet that was used by the boat manufacturer. Solid rivets, for example, are commonly used in boat construction due to their high load-bearing capacity and exceptional durability. Pop rivets are also widely used due to their strength and ease of installation, while blind rivets are useful in tight spaces where traditional riveting is impossible.
Overall, by selecting the appropriate rivet type, applying protective coatings or treatments, and regularly inspecting and maintaining rivets, you can effectively manage rivet corrosion and sealing in aluminium boats.
Finding Closest Boat Launch Ramps Made Easy
You may want to see also
Rivet strength
When it comes to rivet strength, several factors come into play, especially when dealing with aluminum boats. The size, type, and material of the rivets all contribute to their overall strength and performance.
Size of the Rivets
Firstly, the size of the rivets is crucial. Larger rivets generally offer greater inherent strength and can handle bigger loads. This is an important consideration for aluminum boats, as the rivets need to bear the weight and stress of the vessel and its contents. When replacing rivets, it's important to match the size of the original rivets or consult a specialist to determine the appropriate size for a specific application.
Types of Rivets and Their Strengths
Different types of rivets are available, each with its own advantages and applications. Here are some common types and their strengths:
- Solid Rivets: Known for their exceptional durability and ability to bear high loads. They are commonly used in critical load-bearing applications and where shear strength is crucial. Solid rivets provide unparalleled structural integrity and are often preferred for joints and connections that ensure the vessel's safety and longevity.
- Pop Rivets: Also known as blind rivets, these are widely used in boat building due to their strength and ease of installation. They offer high tensile strength and are ideal for structural applications in marine environments. Pop rivets can be installed from one side, making them perfect for tight spaces where traditional riveting is impossible.
- Countersunk Rivets: These rivets are designed to achieve a flush finish with the surrounding material. They sit flush after installation, reducing turbulence and drag, which improves the vessel's aerodynamics and overall performance.
- Rosette Rivets: Rosette rivets excel in providing superior vibration resistance, making them ideal for marine applications. They can withstand constant vibrations and shocks, ensuring long-lasting joint integrity. Rosette rivets also offer excellent corrosion resistance, which is crucial in saltwater environments.
Material of the Rivets
The material of the rivets plays a significant role in their strength and corrosion resistance. Aluminum rivets, for example, are strong and corrosion-resistant, making them a popular choice for boat hulls. There are two main types of aluminum rivets: pure aluminum and alloyed aluminum. Alloyed aluminum rivets, mixed with metals like magnesium or silicon, offer greater strength. It's important to match the rivet material with the aluminum alloy of the boat to prevent galvanic corrosion.
Installation and Maintenance
Proper installation and maintenance are key to ensuring the strength and longevity of rivets. Using specialized tools, such as rivet guns, pop rivet tools, and countersinking tools, ensures a secure hold and a flush finish. Regular inspections and timely replacements are crucial to maintaining the structural integrity of the vessel.
Drifting Boats: Uncertain Fate and Uncharted Waters
You may want to see also
Frequently asked questions
The size of the buck rivets you need for an aluminum boat depends on the thickness of the material where the rivets will be going. Common sizes include 3/16" x 3/8", 3/16" x 1/2", and 1/4" x 1/2".
Solid rivets are generally recommended for aluminum boats, as they are stronger than pop rivets. It is also important to use the correct type of aluminum to prevent electrolysis issues.
To install buck rivets in an aluminum boat, you will need a rivet tool such as a pneumatic rivet gun or a two-handled rivet tool. You may also need an air compressor and air hammer. For solid rivets, you will also need a bucking bar or a scrap piece of metal to hold perpendicular to the rivet while hammering.