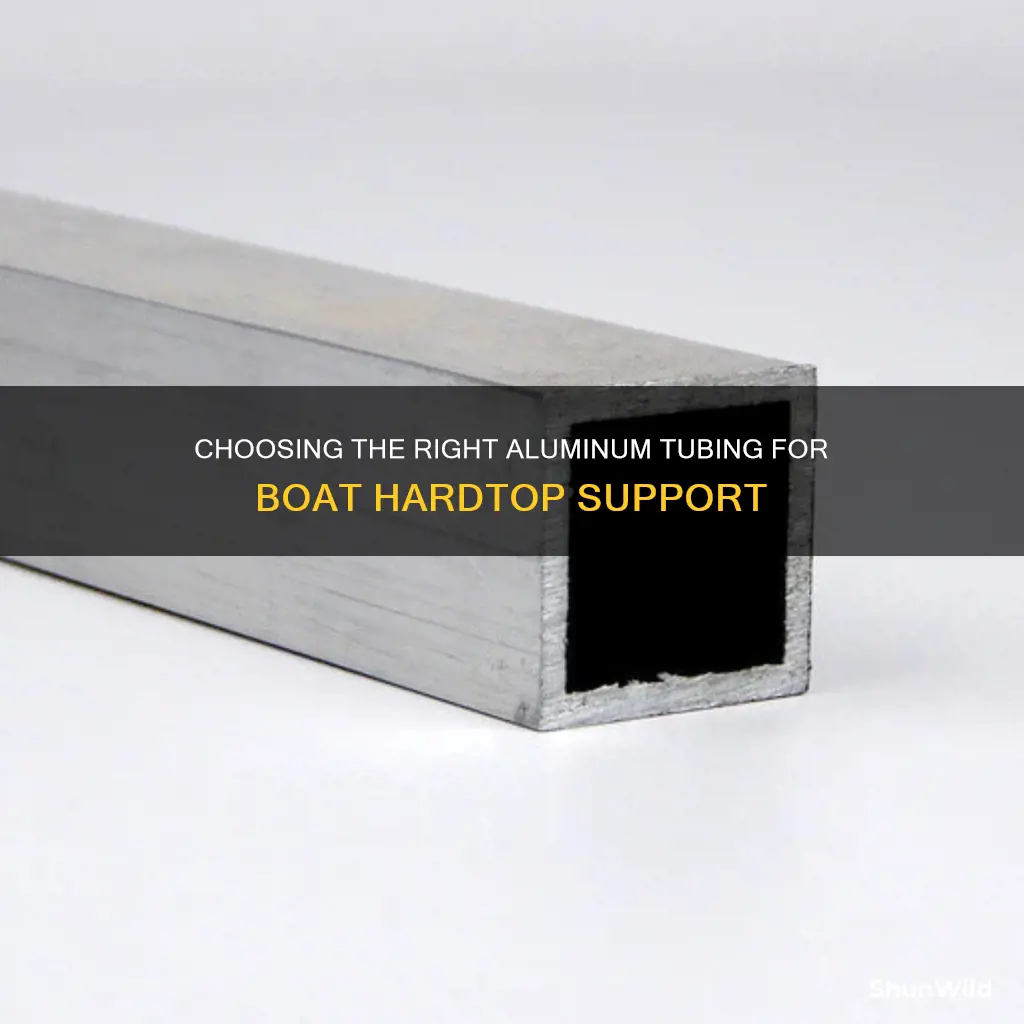
Aluminum tubing is a popular choice for boat hardtops due to its affordability, ease of manufacture, and corrosion resistance when anodized. When selecting aluminum tubing for a boat hardtop, it is essential to consider the tubing's dimensions, material grade, and intended use. The tubing should be thick enough to support the weight of the hardtop and any additional accessories while also accounting for the boat's handling and stability.
The type of aluminum alloy used is also crucial. 6061 aluminum is commonly available and can be welded, but it is not suitable for bending without breaking. On the other hand, 6063 aluminum is more corrosion-resistant and can be bent without cracking, making it a better choice for custom hardtop frames.
When welding aluminum tubing, it is essential to ensure that the welding process does not compromise the material's structural integrity. TIG welding is often recommended for aluminum due to its precision and ability to minimize heat input. Additionally, proper surface preparation, such as removing the anodized layer in the weld area, is crucial for achieving strong welds.
In summary, building a boat hardtop using aluminum tubing requires careful consideration of the tubing's dimensions, alloy type, and welding process to ensure a safe and durable structure.
What You'll Learn
Aluminium tubing for a boat hardtop should be marine-grade
When choosing aluminium tubing for a boat hardtop, it is important to select a product that is marine-grade. Marine-grade aluminium tubing is crafted from robust alloys, such as 6463, and offers durability and corrosion resistance in marine environments. It is also important to consider the diameter of the tubing, which typically ranges from 3/4" to 1".
Marine-grade aluminium tubing is ideal for boat hardtops as it provides both strength and corrosion resistance. This type of tubing is commonly used for applications such as T-Tops, tuna towers, bimini towers, poling platforms, and bow rails. By selecting a marine-grade product, you can be confident that your boat hardtop will withstand the harsh conditions of the marine environment.
In addition to selecting marine-grade tubing, it is also important to consider the welding process. Welding aluminium can be challenging, and it is crucial to ensure that the anodized surface is properly protected during the welding process. Improper welding can result in a brittle weld joint and remove the protective anodized layer, compromising the corrosion resistance of the tubing.
Furthermore, the choice between aluminium and stainless steel tubing should be considered. While aluminium tubing is commonly used for aftermarket items due to its ease of manufacture, stainless steel is stronger and more corrosion-resistant. Stainless steel is often used in boat railings, steering wheels, bow rails, side rails, and grab bars because of its superior strength and corrosion resistance.
When selecting aluminium tubing for a boat hardtop, it is important to consider the specific marine environment and the level of corrosion resistance required. In saltwater environments, for example, the high 'galvanic potential' of aluminium can lead to galvanic corrosion between dissimilar metals. In such cases, stainless steel may be a more suitable choice.
Overall, when choosing aluminium tubing for a boat hardtop, selecting a marine-grade product is essential to ensure durability and corrosion resistance. Additionally, careful consideration should be given to the welding process and the choice of material, with stainless steel being a stronger and more corrosion-resistant alternative.
Attaching Dock Wheels to a Boat Lift: Easy Steps
You may want to see also
Anodized aluminium tubing is a whole different ball game
Anodized aluminium tubing is often used for aftermarket items as it is relatively soft, easy to cut, bend, machine, and drill. It is also easy to weld, and shops with minimal equipment can manufacture aftermarket items that look very nice. Anodized aluminium tubing is also lightweight and corrosion-resistant. It is commonly used for grab rails, canvas top frames, leaning posts, and plumbing.
However, there are some challenges to working with anodized aluminium tubing. To weld anodized aluminium, you must first remove the anodized layer, which can be difficult to do without affecting the surrounding area. The extreme heat required to weld anodized aluminium can also make the weld joint brittle and remove the anodized surface protection. As a result, anodized aluminium welds can be prone to hydrogen cracking and corrosion.
Additionally, anodized aluminium tubing may not be as strong as other materials. Stainless steel, for example, is 2-3 times stronger than anodized aluminium. Anodized aluminium also has a finite fatigue life, which means that it will eventually break with repeated use.
When choosing whether to use anodized aluminium tubing for your boat's hardtop, it is important to consider the trade-offs between ease of manufacture, weight, and corrosion resistance, and strength, weldability, and longevity.
Gel Cell Batteries: Better Boat Battery Option?
You may want to see also
TIG welding is the best method for aluminium tubing
When it comes to welding aluminium tubing, TIG welding is the best method for several reasons.
Firstly, TIG welding (Tungsten Inert Gas welding) is ideal for aluminium because it requires extremely clean base materials for a quality weld, and TIG welding is well-suited to this. Aluminium also has to be pre-heated, and TIG welding can be used to achieve this, burning off the anodized layer and pre-heating the metal.
Secondly, TIG welding is a precise method that allows the welder to reach spots that are more difficult to access. This is particularly important when working with tubing, as welders need to be able to reach the joints and seams of the tubing.
Thirdly, TIG welding is a strong and clean method of welding, which is important when working with aluminium. It is a slow process, but the precision and strength of the weld are worth the time taken. TIG welding produces minimal splatter and a strong, clean weld, which means less time is needed for grinding and finishing.
Finally, TIG welding is versatile and can be used on a wide range of material thicknesses, which is an advantage when working with aluminium tubing of varying thicknesses.
While other methods such as MIG welding and spool guns can be used on aluminium, TIG welding is the best option for a strong, clean, and precise weld. It may be more expensive and require more skilled operators, but the results are superior and worth the investment, especially for applications like boat hardtops that require both strength and a clean finish.
Exploring Alexander's Lake Buchanan Boat Dock Construction
You may want to see also
Aluminium tubing should be cleaned before welding
Aluminium tubing is a popular choice for boat hardtops, but it's important to ensure you're using the right size and type of tubing for your needs. The tubing needs to be strong enough to support the weight of the hardtop and any accessories, and it should also have some flexibility to withstand the waves and pounding of the ocean.
When it comes to welding aluminium tubing, it's crucial to clean the metal before beginning the weld. Here are some reasons why:
Grease and Impurities
The first step in cleaning aluminium for welding is removing any grease, oil, or other impurities. These substances can impact the quality of the weld and lead to defects. While you might think a simple wipe-down with a rag or brush is enough, it's often not sufficient. Grease and oil can be spread around and pushed deeper into the metal, making the situation worse. Instead, use a liquid degreaser like acetone or methyl ethyl ketone. Apply it with a lint-free rag and let it evaporate before fitting any parts together.
Oxide Removal
The next step is removing any oxides from the aluminium surface. Oxides can interfere with the welding process and need to be stripped away. You can use a wire brush with soft bristles to physically remove the oxides, but make sure the brush is clean and only used for aluminium to avoid contamination. Another option is chemical removal with a strong alkaline solution, which may require immersing the aluminium pieces in the solution or applying it with a spray bottle.
Drying Time
After cleaning, it's crucial to let the aluminium dry completely before starting the weld. Even a few hours are enough for airborne grease and impurities to settle back onto the metal, so if more than a day has passed since cleaning, it's best to start the process over again.
Welding Technique
Welding aluminium also requires proper technique. It has a low melting point and high thermal conductivity, so it's easy for inexperienced welders to burn through the metal. Aluminium's softness can also cause the feeder wire to tangle during the weld. Additionally, the weld-affected area is likely to be weaker than the original metal, so it's important to choose the right alloy and welding technique for your project.
In conclusion, cleaning aluminium tubing before welding is essential to ensure a strong and defect-free weld. By removing grease, impurities, and oxides, you can set yourself up for success and create a high-quality finished product.
Exploring Lake Louise: Boat House Opening Times
You may want to see also
Aluminium tubing is available in different sizes
The thickness of the tubing will affect the strength and durability of the hardtop. A thicker tube will be stronger and more resistant to bending or damage. The diameter of the tubing will also impact the overall strength and appearance of the hardtop. A larger diameter tube will provide more support and create a bulkier look, while a smaller diameter tube will be less noticeable but may not provide as much structural support.
When purchasing aluminium tubing, it is important to specify the outside diameter (OD) and the wall thickness. The wall thickness is measured in inches or millimetres and refers to the distance between the outside and inside surfaces of the tube. Standard wall thicknesses for aluminium tubing can range from 0.035 inches to 0.5 inches, but custom thicknesses are also available.
Another factor to consider when selecting aluminium tubing is the type of finish. Aluminium tubing can be anodized, painted, or powder-coated to protect the surface and improve corrosion resistance. Anodizing is a process that creates a hard oxide layer on the surface of the aluminium, providing a durable and corrosion-resistant finish. Painting or powder coating can also enhance the appearance and protect the tubing from the elements.
When building a boat hardtop, it is essential to use high-quality materials and construction techniques to ensure the structure's strength and longevity. Aluminium tubing is a popular choice due to its lightweight, corrosion resistance, and ease of fabrication. However, it is important to consider the specific size, thickness, and finish of the tubing to ensure it meets the structural requirements of the hardtop while also achieving the desired aesthetic look.
Painting Your Inflatable Boat's Rubber Strake: A Step-by-Step Guide
You may want to see also
Frequently asked questions
The size of the aluminum tubing depends on the size and weight of the hardtop and the intended use of the boat. Aluminum tubing typically ranges from 1" to 4.5" in outer diameter with varying wall thicknesses. It is important to consider the strength and corrosion resistance of the aluminum grade when selecting the appropriate size.
The most commonly recommended aluminum grades for boat hardtops are 6061 and 6063. 6061 aluminum is stronger and more corrosion-resistant, making it ideal for marine environments. However, it cannot be bent without breaking. On the other hand, 6063 aluminum is softer and more suitable for bending but has lower strength and corrosion resistance.
Aluminum tubing is widely used for boat hardtops due to its lightweight and corrosion-resistant properties. It is also relatively easy to work with, making it a cost-effective option for custom fabrications. Additionally, aluminum tubing can be anodized to improve its corrosion resistance and aesthetic appeal.
To achieve strong welds on aluminum tubing, it is crucial to start with clean and anodization-free surfaces. Use a TIG welding technique with a combination of argon and helium gas as the shielding agent. Ensure that you have the appropriate welding equipment and techniques to avoid cracking and weak welds.