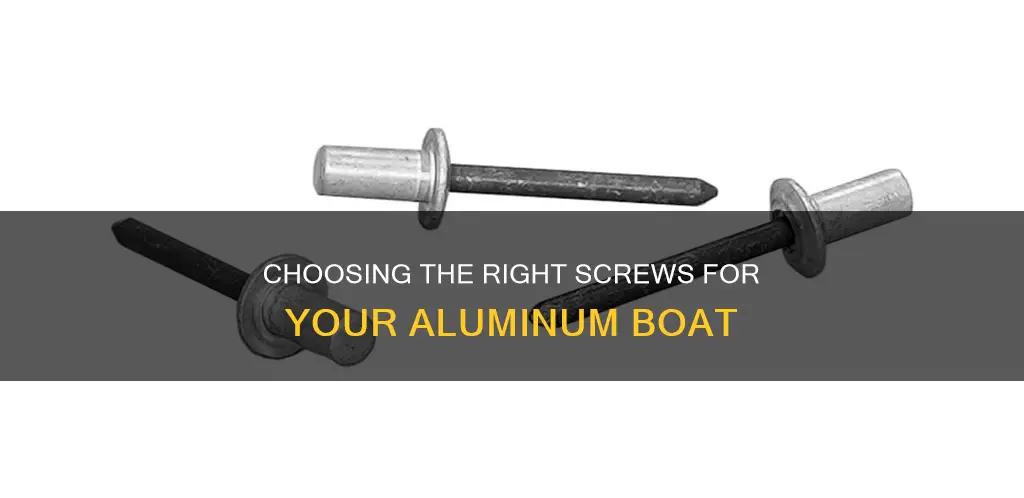
When it comes to choosing the right screws for an aluminium boat, there are a few factors to consider. The type of environment the boat will be used in, such as saltwater or freshwater, plays a crucial role in determining the suitable screw material. While stainless steel screws are a popular choice, they can cause corrosion in aluminium boats, especially in saltwater environments. To prevent this, it is recommended to use a sealant or insulating material, such as Tef-Gel, between the two dissimilar metals. Another option is to use aluminium screws, which are less likely to cause corrosion but may not provide the same level of strength as stainless steel. Additionally, the type of application, whether structural or cosmetic, should be considered when selecting the grade of stainless steel screws. For cosmetic applications, 316 stainless steel is recommended, while for structural purposes, 304 stainless steel can be used. It is also important to consider the availability and cost of the screws, as some grades of stainless steel and aluminium screws may be more expensive and challenging to source.
What You'll Learn
- Stainless steel screws are suitable for aluminium boats
- Tef-Gel can be used to prevent corrosion between stainless steel and aluminium
- Aluminium screws are the best option for preventing corrosion
- Steel screws should be avoided as they stain aluminium boats
- Sacrificial anodes can be used to prevent corrosion
Stainless steel screws are suitable for aluminium boats
When using stainless steel screws with aluminium, it is essential to prevent direct contact between the two dissimilar metals to avoid galvanic corrosion. This can be done by using nylon washers, plastic washers, or plastic insert bushings. Additionally, a sealant or thread locker, such as Tef-Gel, can be applied to the threads of the screw to provide further protection.
It is worth noting that stainless steel screws are more expensive than other options, and the cost can add up quickly, especially if you need a large quantity. Buying in bulk from a hardware supplier or a "boat store" may help to get a better deal.
Another important consideration is the type of water the boat will be used in. Freshwater and saltwater can have different effects on the compatibility of stainless steel and aluminium. Some boaters suggest using bronze screws below the waterline in saltwater, while others recommend stainless steel for both freshwater and saltwater applications.
Finally, it is recommended to avoid using the boat hull as a ground, as this can accelerate corrosion and damage the boat.
Best Foam Weight for Boat Flooring: Choose the Right One
You may want to see also
Tef-Gel can be used to prevent corrosion between stainless steel and aluminium
When it comes to aluminium boats, stainless steel is the best choice for screws and bolts. However, using two dissimilar metals in close contact can lead to electrolysis and galvanic corrosion, especially in saltwater environments. This is where Tef-Gel comes in.
Tef-Gel is a PTFE-based paste that can be applied to the surfaces of stainless steel screws and bolts to prevent corrosion when they come into contact with aluminium. It acts as a friction barrier, impeding the galvanic series voltage difference that would otherwise drive the corrosion process. By creating high resistance between the metals, Tef-Gel effectively reduces the rate of corrosion.
To use Tef-Gel, simply coat all the stainless steel surfaces that will be in contact with aluminium, such as the threads of bolts. Then, tighten the bolts as usual, being careful not to strip the aluminium threads. It is important to note that Tef-Gel should not be used with plastic, as it can cause embrittlement and failure. Additionally, do not expose Tef-Gel to temperatures above 230°C.
Tef-Gel is an effective solution for preventing corrosion in aluminium boats when using stainless steel screws and bolts. It is easy to apply and provides long-lasting protection, ensuring that your boat's hardware remains in good condition even in saltwater environments.
In addition to using Tef-Gel, sacrificial anodes can also be used as a corrosion prevention method. Zinc, for example, possesses a higher potential voltage in the galvanic series and will corrode instead of aluminium, acting as a sacrificial anode. This provides additional protection and helps to ensure the longevity of your boat's hardware.
Boat Paint: Unique Qualities and Essential Features
You may want to see also
Aluminium screws are the best option for preventing corrosion
Aluminium is a popular choice of metal thanks to its lightweight, flexible, and strong properties. However, it tends to react negatively with other metals, leading to corrosion. To avoid corrosion on your aluminium boat, you have several options for screws.
Firstly, you could use aluminium screws. This avoids the two-metal reaction that causes corrosion. However, aluminium screws do not offer adequate shearing resistance for all but light-duty use.
Another option is to use stainless steel screws. Stainless steel is one of the least reactive metals, so even if the coating peels away, it is still relatively safe from corrosion.
You could also use coated steel fasteners. This involves encasing a reactive metal in a thick coating to prevent corrosion. However, it is best to avoid very reactive metals such as brass and opt for less reactive metals like stainless steel.
Finally, you could use non-metal fasteners such as high-strength plastic. These are not as strong as metal varieties but are suitable for light-duty applications.
While aluminium screws may not be the strongest option, they are still the best choice for preventing corrosion in aluminium boats. By using the same metal throughout your project, you can avoid the issues caused by two-metal reactions. Additionally, aluminium's natural strength and flexibility make it a good choice for boat construction.
To further prevent corrosion, you can use a clear coat finish or anodize the aluminium parts before assembly. This will provide a uniform protective layer that can be replaced if needed.
In summary, while there are several options for screws that won't corrode when in contact with aluminium, aluminium screws are the best choice for preventing corrosion in aluminium boats. By using aluminium throughout the project, you can avoid the negative reactions caused by mixing metals. Additionally, aluminium's natural strength and flexibility make it a well-suited material for boat construction.
Replacing Pop Rivets: A Boat Owner's Guide
You may want to see also
Steel screws should be avoided as they stain aluminium boats
Steel screws should be avoided as they can stain aluminium boats. This is due to the galvanic corrosion that occurs when these two metals are in contact with each other. Galvanic corrosion is the result of the dissimilar nature of these two metals, and it can lead to the destruction of both materials.
To prevent this corrosion, it is crucial to separate the two metals, especially in environments with salty water or similar substances. One effective method is to use plastic washers as a barrier between the steel screws and aluminium boat, creating a non-reactive layer that seals their point of contact. Additionally, connecting points can be protected using tape or paint to reduce exposure to water.
Another important consideration is the surface area of the metals in contact. It is recommended that the aluminium part has a larger surface area than the steel screws. This is because aluminium has an anodic nature and will quickly disintegrate when exposed to salty water or when its surface area is smaller than that of the steel screws.
For aluminium boats, stainless steel screws are generally considered a better option than steel screws. While stainless steel is not entirely immune to corrosion when in contact with aluminium, it is a more suitable choice for fastening aluminium boats. However, it is still important to take precautions, such as using barrier materials and reducing exposure to water, to minimise the risk of corrosion.
In summary, steel screws should be avoided when working with aluminium boats due to the potential for staining and corrosion. By selecting appropriate fasteners, such as stainless steel screws with proper precautions, you can effectively reduce the risk of corrosion and ensure the longevity of your aluminium boat.
Glastron Boats: Worth the Buy?
You may want to see also
Sacrificial anodes can be used to prevent corrosion
When it comes to aluminium boats, stainless steel is the best choice for screws and bolts. However, it's important to note that not all types of stainless steel play well with aluminium. Therefore, it is recommended to use 316 or 316L stainless steel, which are "marine-grade" alloys.
Now, onto the topic of corrosion prevention using sacrificial anodes.
Sacrificial anodes are an effective method for preventing corrosion in aluminium boats. They work on the principle of electrolysis, where a sacrificial metal rod or electrode is introduced to attract corrosion away from the boat. This process occurs via "galvanic corrosion". When two dissimilar metals with different electrical activities are immersed in a conductive liquid like seawater, a weak electric current flows between them. The more active metal (the anode) gives up electrons to the less active one (the cathode) and slowly dissolves.
In the context of an aluminium boat, a third type of metal, such as zinc or magnesium, can be used as a sacrificial anode. These metals are more electrically active than aluminium and will sacrifice themselves while preserving the boat's metal components. As long as these sacrificial anodes are regularly replaced, the boat's metal parts will remain protected.
Sacrificial anodes are available in various shapes and sizes, including flat, cylindrical, bracelet, and tubular designs. They can be secured to the boat using bolts, welds, or brackets. It is important to ensure good electrical contact between the anode and the metal being protected, and to regularly replace the anodes as they corrode.
Zinc has traditionally been used as a sacrificial anode material due to its ease of availability. However, it is ineffective in freshwater and brackish water. Aluminium anodes, on the other hand, are lightweight, work in both saltwater and brackish waters, and can last up to 50% longer in saltwater. They are also more environmentally friendly than zinc anodes. Magnesium anodes are ideal for freshwater use but do not perform well in saltwater or brackish water.
The choice of anode material depends on the type of boat and the water environment. For aluminium boats, aluminium anodes are generally recommended for saltwater and brackish water, while magnesium anodes are suitable for freshwater. It is also important to consider the size and number of anodes, as overprotection can occur with too many anodes.
In summary, sacrificial anodes are a crucial component in preventing corrosion in aluminium boats. By selecting the appropriate anode material, shape, and size, and regularly replacing them, boat owners can effectively protect their vessels from the damaging effects of corrosion.
Best Boat Engines: Powering Your Water Adventure
You may want to see also
Frequently asked questions
Stainless steel screws are the best choice for fastening to an aluminum hull. Use 316 or 316L stainless steel hardware, which is "marine grade" and suitable for the job.
To prevent corrosion, it is recommended to use a sealant, grease, or washers to minimize the contact area between the metals. Products such as Tef-Gel, Duralac, and 5200 sealant are specifically designed to isolate dissimilar metals and prevent corrosion.
Aluminum screws can be used, but they are not as strong as stainless steel. If you want to use aluminum fasteners, it is recommended to put wax on the threads before tightening to prevent galling and breakage.
Regular deck screws or stainless steel self-tapping screws can be used. For 1/2" marine plywood, use 1" screws. For 3/4" plywood, use 1-1/4" screws. Drilling pilot holes and using trim washers will make installation and future removal easier.
No, do not use zinc-coated hardware or galvanized fasteners in saltwater as they will not hold up.