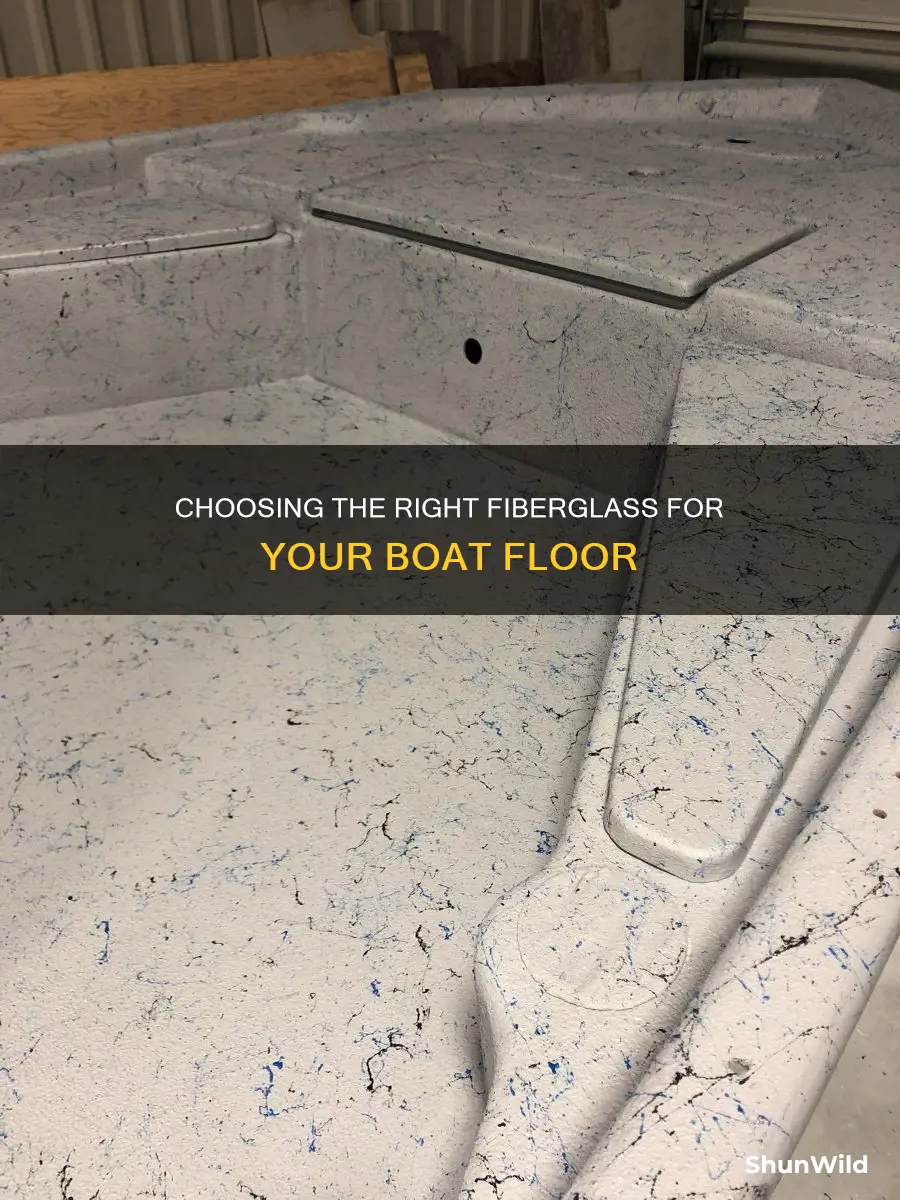
Fiberglass is a popular material for boat construction, but choosing the right type of fiberglass for a boat floor can be challenging. There are several factors to consider when selecting the appropriate fiberglass material, including the desired thickness, strength, and ease of handling.
Fiberglass cloth, a woven fabric, is commonly used for its strength and lightweight properties. It comes in various weave styles, such as plain, satin, and twill, each offering different advantages in terms of handling and pliability. On the other hand, chopped strand mat, also known as fiberglass mat, is a more affordable option with short strands of fibers held together by a resin binder. While it lacks strength, it is excellent for building thickness and conforming to tight curves.
When selecting the right fiberglass for a boat floor, it's essential to consider the specific requirements of the project, such as the need for strength, ease of installation, and cost-effectiveness. Additionally, the type of resin used, such as polyester, vinylester, or epoxy, plays a crucial role in determining the final outcome.
Characteristics | Values |
---|---|
Materials | Fiberglass, Resin, Composites, Cores |
Types of Fiberglass Resin | Polyester, Vinylester, Epoxy |
Types of Fiberglass Cloth | Woven Fabrics, Roving, Mat, Kevlar, Carbon Fiber, Uni-Directional Fibers, Bi-Axial, Tri-Axial |
Weight | 4-15 ounces per square yard |
Weave Patterns | Twill, Satin, Matt |
Types | E-Glass, S-Glass |
Binder | Resin-Soluble |
Weight | 17 oz |
Types of Resin | Polyester, Vinylester, Epoxy |
What You'll Learn
Removing old flooring
Disconnect Electrical Components
Before you start removing the old boat floor, it is essential to disconnect any electrical components to eliminate the risk of electric shock or damage. Start by turning off the boat's main power source, which could involve shutting off the battery or disconnecting the boat from shore power. Once the power is off, carefully remove any wiring connected to the floor. Take note of the wiring connections and consider labelling them to make reinstallation easier. Handle the electrical components with care and avoid pulling or tugging on the wires to prevent damage.
Remove Fixtures and Hardware
Next, you'll need to remove any fixtures and hardware attached to the floor, such as seats, railings, cabinets, and accessories. Begin by unscrewing or unbolting these items and keep track of the hardware for later reinstallation. Taking pictures or making notes of the original positioning of the fixtures will also be helpful during reassembly.
Detach the Old Floor
Once the electrical components and fixtures have been removed, it's time to detach the old boat floor itself. The floor is typically attached with screws, bolts, adhesive, or a combination of these. Using appropriate tools, carefully remove all fasteners securing the floor. Ensure that all screws and bolts are completely extracted. If the floor is held down with adhesive, you may need to gently pry it up using a putty knife or scraper. Be cautious of any hidden obstacles, such as wiring or plumbing, and take precautions to avoid damaging them.
Inspect the Subflooring
After removing the old floor, it's crucial to inspect the underlying subflooring for any signs of damage or rot. Look for areas near the edges and corners, as they are more prone to damage. Use a flashlight to thoroughly examine the subflooring for any issues. If you find any damage or rot, it's important to repair or replace the affected areas before proceeding with the installation of the new boat floor.
By following these detailed steps, you can successfully remove the old flooring from your boat and prepare for the next phase of the boat floor replacement process.
The Unique Design of Tri-Hull Boats Explained
You may want to see also
Replacing boat stringers
Overview
Boat stringers are the wood underneath your boat deck that supports said deck. They are the backbone of your boat's hull, preventing twisting and flexing. Over time, they can rot away or suffer structural damage, which can be unsafe for the boat.
This guide will take you through the process of replacing your boat stringers.
Step 1: Cut off the Deck
This can be a stressful part of the job, as you need to be careful not to cut too deep and pierce the hull. Delicately drill a hole in the deck to measure its thickness, then set your saw blade to cut through that depth. If your boat has a fuel tank built-in, be careful not to cut into the tank or its lines.
Step 2: Measure and Cut the New Stringers
You want to duplicate the old stringers as closely as possible. Make an initial rough cut, then modify it as needed by putting the new stringer core next to the old one. Don't forget that the fiberglass skin will increase the size of the stringer. Cut away a sample of the old fiberglass stringer skin to measure the thickness and number of layers.
Step 3: Remove the Old Stringers
The wood inside the old stringers will likely have turned into a gelatinous mess, so you'll mostly be dealing with the fiberglass shell. Depending on how well the boat was laminated, you may be able to simply rip or bang them out. Otherwise, you'll need to shave them down along the hull and grind away the remnants.
Step 4: Grind and Sand the Inside of the Hull
To get a good secondary bond between the new stringers and the hull, you need to create a clean surface. Grind away all the glass from the old stringers, then sand the area thoroughly. Be careful not to apply too much pressure in one spot for too long, as you may grind through the hull.
Step 5: Prepare the Surface for Bonding
Choose solvents and prep methods following the fiberglass resin manufacturer's instructions. Pre-prep a jig to support the stringers as the bedding dries.
Step 6: Install the New Stringers
Bed the ply core in thickened epoxy or fiberglass putty, then put the stringers in place, adding the jig pieces to support them. While the epoxy or putty is still pliable, form a "fillet" (a radius) along both bottom edges of the plywood, as fiberglass doesn't make sharp bends very well.
Step 7: Apply the Fiberglass Stringer Skin
Cut fiberglass cloth to wrap the stringer and extend to either side. When applying multiple layers, make each consecutive layer about a half-inch smaller than the previous one. Wet out the stringer cores with fiberglass resin, then center the first cloth layer and wet it out as well. Apply additional layers while the resin is still tacky.
Step 8: Finishing Touches
Once the fiberglass has cured, sand or grind away any jagged edges or fiberglass hairs.
Tips
- It's generally best to mimic the boat's original construction when replacing stringers.
- Complete stringer replacement is often easier than partial replacement.
- Regularly inspect and maintain your boat stringers to ensure they stay strong and last longer.
- If you suspect damage to your stringers, cut "access holes" to get a good look at them.
- If your stringers are damaged by rot, use a product like Git-Rot to address the problem.
- If you're unsure about the type of wood used in your stringers, consult a professional.
- When cutting away the old stringers, be careful not to cut into the hull laminate.
Esurance Boat Insurance: What You Need to Know
You may want to see also
Installing new flooring
First, remove any loose items and clear out the furniture and any old, damaged items like plywood from the boat. This includes taking out the center console and cables. It is recommended to make a list of everything that has been disconnected to ensure proper reassembly.
Next, consider replacing the boat stringers if they are faulty. This step is not necessary but can be done alongside the flooring work to save time and effort.
After that, take extensive measurements of the deck to determine the amount of flooring needed. Cut the new flooring into individual supported segments if necessary. Be mindful of any cables or connections that will need to be reconnected once the new flooring is in place.
Once the measurements are done, install the new deck sheets, screwing them into place. Then, apply fiberglass matting and ensure it is properly sealed with a high-quality sealant to create a water-tight barrier.
Finally, reattach the center console and seats, reconnecting all the cables and wires according to your list. Clean the area and start the engine in a secure location to test the connections.
By following these steps, you can ensure that your new boat flooring is installed correctly and will last for many years.
Legacy Boat Registration: Arizona's Process and Requirements
You may want to see also
Applying fiberglass matting
Applying fibreglass matting is a delicate process that requires careful preparation. Here is a step-by-step guide to help you apply fibreglass matting effectively:
Prepare the Surface:
Start by ensuring that the surface is clean, dry, and free from any dust, grease, or existing paint. Sand the surface with a coarse sandpaper and power sander to create a smooth base. Clean the area with acetone to remove any remaining dust or grease. This step is crucial for achieving strong adhesion between the fibreglass and the surface.
Cut the Fibreglass Matting to Size:
Measure the area where you will be applying the fibreglass matting and cut the matting to size. It is recommended to cut the matting approximately 10% larger than the designated area to ensure full coverage. Prepare the matting in advance, as the resin has a short shelf life once catalysed.
Mix the Resin and Catalyst:
In a separate container, mix the resin and catalyst according to the manufacturer's instructions. Typically, you will need around 20 ml of catalyst per kilogram of resin. Use a clean instrument to stir the mixture thoroughly, ensuring that the catalyst is evenly distributed. The amount of catalyst added will depend on the temperature—use less catalyst in warmer temperatures and more in colder temperatures.
Apply the First Layer of Resin:
Using a polyester roller or a paintbrush, saturate the surface with the catalysed resin. Make sure to work in a well-ventilated area as the resin gives off strong fumes. Wear protective gear, including gloves, eye protection, and a respirator mask.
Apply the Fibreglass Matting:
Once the surface is saturated with resin, carefully lay the fibreglass matting onto the surface. Use a roller to smooth out any air bubbles and ensure the matting adheres properly to the resin. If you are working with corners or curved surfaces, you may need to cut and manipulate the matting to ensure a snug fit.
Apply the Second Layer of Resin:
Repeat the process by applying another layer of resin over the fibreglass matting. Use a paddle roller to consolidate the layers and create a consistent surface. This step helps to strengthen the bond and ensure a uniform finish.
Allow the Resin to Cure:
Fibreglass resin typically takes around 30 minutes to cure and several hours to fully harden. Refer to the manufacturer's instructions for specific curing times. Do not disturb the surface until it is fully cured to avoid any imperfections.
Sand and Finish (Optional):
Once the resin has cured, you may choose to sand the surface to create a smoother finish. You can also apply a topcoat or flow coat for added protection and aesthetics. Follow the manufacturer's instructions for applying any additional coatings.
Remember to work in a well-ventilated area and always wear the appropriate protective gear when working with fibreglass and resin. By following these steps, you can effectively apply fibreglass matting to create a strong and durable surface.
Bass Boats: Expensive, Impractical, and a Bad Investment
You may want to see also
Reattaching seats and consoles
Step 1: Remove Old Seats and Consoles
Before beginning the reattachment process, carefully remove any existing seats, consoles, or other fixtures from the boat's deck. This step ensures a clean slate for the new installations.
Step 2: Prepare the Area
Inspect the area where the new seats and consoles will be installed. Ensure that the surface is clean, dry, and free from any debris or residue. If necessary, sand or treat the surface to create a suitable base for the new fixtures.
Step 3: Gather Materials and Tools
Collect all the necessary materials and tools for the reattachment process. This may include items such as marine-grade plywood, resin, fiberglass cloth, epoxy, screws or bolts, and any other hardware required for secure installation.
Step 4: Measure and Mark
Using the old seat placements as a guide, measure and mark the exact locations for the new seats and consoles. This step ensures that the new fixtures will align perfectly with the existing structure and any necessary screw holes.
Step 5: Drill and Attach
Drill holes in the marked locations, taking care to use the appropriate drill bit size for the screws or bolts you will be using. Carefully align the seats and consoles with the drilled holes and securely fasten them in place.
Step 6: Seal and Finish
Once the seats and consoles are firmly in place, apply a suitable sealant around the edges to protect against water intrusion and to give a smooth finish. Allow the sealant to dry completely before proceeding.
Step 7: Reinstall Additional Components
If you had to remove any wiring, hoses, or other components during the process, now is the time to carefully reinstall them, ensuring that everything is securely connected and fastened.
Step 8: Test and Adjust
Finally, test the reattached seats and consoles by applying weight and simulating typical usage conditions. Make any necessary adjustments to ensure optimal stability, comfort, and safety.
Remember to consult a professional or a detailed boat building guide for specific instructions and safety precautions, especially if you are new to boat building or renovation projects.
The Daughter in Fresh Off the Boat: Unveiling the Actress
You may want to see also
Frequently asked questions
There are three types of resin: polyester, vinylester, and epoxy. Epoxy resin is the most high-performance option, but it is also the most expensive. Polyester resin is the most common and inexpensive option, but it has a strong odour and a short working time. Vinylester resin is a good middle ground as it has better stretch characteristics than polyester and is more resistant to water.
Fiberglass cloth is a woven fabric that comes in plain, 4-harness satin, and 8-harness satin weave styles. The plain weave is the easiest to handle as it does not unravel when cut. The satin weaves are stronger and more pliable, making them easier to conform to curved surfaces, but they are more difficult to handle.
Chopped strand mat, also known as fiberglass mat, is made of short strands of fibres held together with a resin binder. It is compatible with polyester and vinyl ester resin but not with epoxy resin. It is the least expensive type of fiberglass and is often used to build thickness or as the first layer in a laminate.
First, remove any damaged flooring and clear out anything loose. Then, measure the size of your deck to determine how much flooring you need. Install the new flooring and apply fiberglass matting, ensuring it is properly sealed. Finally, reattach the seats and centre console and test the engine in a secure location.