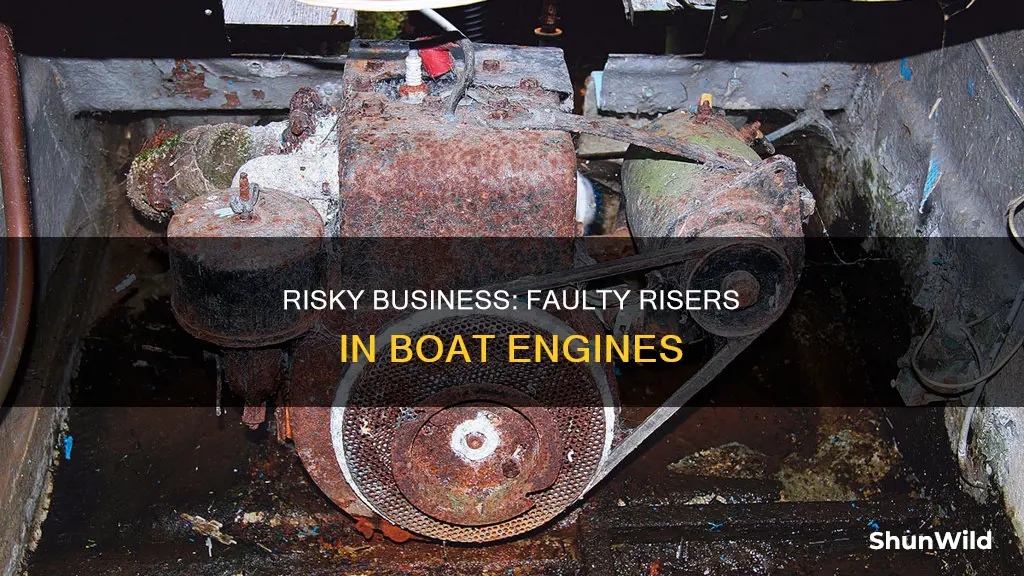
Faulty risers in a boat engine can lead to engine damage and even engine failure. Risers are a crucial component of marine inboard engines, responsible for two main functions: preventing water from backing up into the engine and introducing cooling water into the exhaust exit piping system. However, risers are susceptible to corrosion and design failures, which can result in water leakage into the engine, causing irreparable damage. Therefore, regular inspection and maintenance of risers are essential to prevent costly repairs or replacements. The frequency of inspection depends on the boat's location and usage, with saltwater environments requiring more frequent checks than freshwater areas.
Characteristics | Values |
---|---|
Engine damage | Faulty risers can cause engine damage and even engine failure. |
Engine type | Inboard and inboard/outboard (I/O) engines have exhaust risers. |
Engine cooling | Risers introduce cooling water into the exhaust exit piping system. |
Engine protection | Risers prevent water from backing up into the engine through the exhaust piping. |
Material | Risers are typically made of cast iron, which corrodes over time. |
Lifespan | In saltwater, risers typically last 4-5 years; in freshwater, they can last longer. |
Maintenance | Risers should be inspected regularly and replaced if necessary. |
Failure modes | Riser problems include corrosion failures and design failures. |
Warning signs | Warning signs of potential failure include hard starting, knocking sounds, and rust on the outside. |
What You'll Learn
- Risers are a type of pipe within a pipe, allowing hot exhaust gases to be surrounded by water in an external pipe
- Risers are usually made from cast iron, which corrodes over time
- Corrosion and design failures are the two main types of riser problems
- Risers should be checked annually after two years of use in saltwater and every two years in freshwater
- Faulty risers can cause water to enter the engine, which can be catastrophic
Risers are a type of pipe within a pipe, allowing hot exhaust gases to be surrounded by water in an external pipe
Risers are a crucial component of marine inboard engines. They are essentially a pipe within a pipe, allowing hot exhaust gases to be surrounded and cooled by water in an external pipe. This external pipe is known as a water jacket, and it is crucial in preventing the engine from overheating.
The internal pipe carries the hot exhaust gases away from the engine, while the water jacket cools these gases before they exit through the exhaust overboard discharge. This double-walled arrangement is essential in maintaining the engine's temperature and preventing damage.
However, risers are susceptible to corrosion and failure. As the hot exhaust gases and cooling water come into close contact, the risers experience extreme temperature variations, accelerating corrosion. Over time, corrosion can lead to leaks in the water jacket, allowing water to seep into the gas-only chamber. This can result in water entering the cylinders, causing irreparable engine damage.
To prevent such issues, regular inspection and maintenance of risers are necessary. It is recommended to inspect risers annually or after a few years of use, depending on the environment and operating conditions. Given the critical role risers play in engine cooling, addressing any signs of corrosion or leakage promptly is essential to avoid costly repairs or engine replacements.
Additionally, different types of risers, such as dry joint and wet joint, have varying lifespans and maintenance requirements. Dry joint risers, for example, are designed to reduce the risk of water backing into the engine and typically last longer than wet joint risers. Nevertheless, regular inspection and maintenance are advised to ensure the longevity of the engine and its components.
Boat Insurance: Geico's Towing Service and Its Limitations
You may want to see also
Risers are usually made from cast iron, which corrodes over time
Risers are usually made from cast iron, an inexpensive material that works well in the short term. However, cast iron corrodes over time, making it a less-than-ideal material for risers.
Cast iron corrodes in a unique way, depending on its type. It corrodes with a sort of sheeting or blistering action, leaving layers of heavy scale on the corroded surfaces. This scale can become up to 1/4" thick, blocking water flow and retaining water, which advances the corrosion process. Unlike aluminium or Corten steel, corrosion does not protect the metal; instead, as cast iron corrodes, the rate of corrosion becomes faster.
The thickness of the "jacket" or "jacket wall" (the wall between the exhaust chamber and the cooling water) determines how long the riser will last. The thinner it is, the sooner it will fail. However, there is no way of knowing the thickness of this wall without destroying the riser.
Cast iron is used because it tolerates extremes of temperature, expansion, and contraction better than other materials like stainless steel. It is also a low-cost material. However, due to the way it corrodes, cast iron is not a suitable long-term option for risers.
In summary, while cast iron risers are common due to their low cost and ability to withstand high temperatures, they are prone to corrosion, which can lead to engine damage and failure. This corrosion can be rapid and is often difficult to detect until it is too late, making cast iron a less-than-ideal material for riser construction.
The Ultimate Guide to Changing Boat Seats Easily
You may want to see also
Corrosion and design failures are the two main types of riser problems
Riser problems can be attributed to either corrosion failures or design failures. Corrosion failures occur when the riser material corrodes and fails to withstand the extreme temperatures, expansion, and contraction of the engine. Common materials used for risers, such as cast iron, aluminium, and stainless steel, are susceptible to corrosion and may not be suitable for the harsh environment of the engine.
Design failures, on the other hand, refer to flaws in the design of the riser that make it prone to corrosion or other malfunctions. For example, some riser designs have very narrow water passages that can become blocked by rust or scale buildup, leading to reduced cooling water flow or insufficient cooling of the exhaust system.
To prevent corrosion and design-related issues, it is important to regularly inspect and maintain risers. This includes checking for external signs of corrosion, such as rust or scale buildup, and periodically removing and inspecting the risers internally. Additionally, it is recommended to replace risers every 4-5 years, especially in saltwater environments, as corrosion and failure rates tend to be higher.
By understanding the common issues associated with risers and implementing proper maintenance practices, boat owners can help reduce the risk of engine damage and ensure the safe and reliable operation of their vessels.
The Boys in the Boat: An Epic Journey
You may want to see also
Risers should be checked annually after two years of use in saltwater and every two years in freshwater
Risers are an essential component of inboard and inboard/outboard (I/O) engines. They are large metal castings that carry hot exhaust gases away from the engine. The exhaust riser has two functions: to keep water from backing up into the engine through the exhaust piping, and to introduce cooling water into the exhaust exit piping system.
When checking risers, look for rust stains, which indicate that the gasket is failing, the riser is loose, or the mating surfaces have started to corrode. Drain the water from the engine's risers and manifolds to perform a visual inspection. Remove the bolts securing the risers and look inside for heavy corrosion or material dislodgement, which would warrant replacement. Check the mating surfaces for flatness and look for cracks.
It is also important to check the bolts for proper torque and to replace the gaskets when reinstalling the risers. Additionally, feel each manifold for "hot spots," which indicate internal corrosion. If possible, use an infrared pyrometer to diagnose manifolds more accurately.
By following these inspection and maintenance tips, boat owners can help prevent engine damage and ensure the proper functioning of their vessels.
The Proper Way to Style Boat Names: Italics or Not?
You may want to see also
Faulty risers can cause water to enter the engine, which can be catastrophic
All marine inboard engines have exhaust risers, which serve two functions: to keep water from backing up into the engine through the exhaust piping, and to introduce cooling water into the exhaust exit piping system. If faulty risers fail to perform these functions, water can enter the engine, leading to catastrophic engine damage.
Corrosion is a common issue with risers, especially those made of cast iron, which is used in most common gasoline engines and small auxiliary sailboat engines. Cast iron corrodes quickly, especially when exposed to saltwater, and the rate of corrosion increases over time. This can lead to a build-up of thick layers of scale, which can block water flow and accelerate corrosion. If corrosion causes a hole to form between the water jacket and the exhaust chamber, cooling water can leak into the exhaust manifold, valves, and cylinders, resulting in engine seizure and irreparable damage.
The warning signs of a potential riser failure can be difficult to detect. Hard starting and an unfamiliar knocking sound may indicate a leak, but by then, the damage is often already done. External rust on manifolds or risers is also a sign of internal damage. Additionally, clogged water jackets in manifolds or risers can lead to leaks as the internal walls deteriorate.
To reduce the odds of failure, it is recommended to inspect risers annually or after 2-5 years in saltwater, and every 2-3 years in freshwater. If there are signs of corrosion on the outside, it is likely time for replacement. Replacing risers can be costly, but failure to do so can result in far more expensive engine repairs or replacements.
In summary, faulty risers can cause water to enter the engine, leading to catastrophic consequences. Therefore, regular inspection and maintenance of risers are crucial to prevent engine damage and ensure the safe and reliable operation of marine inboard engines.
Repairing Holes in Your Inflatable Boat: Easy DIY Guide
You may want to see also
Frequently asked questions
Faulty risers in a boat engine refer to issues with the exhaust riser, a component found in all marine inboard engines. The exhaust riser has two crucial functions: firstly, it prevents water from backing up into the engine through the exhaust piping, and secondly, it introduces cooling water into the exhaust exit piping system. Risers can fail due to corrosion or design flaws, leading to costly engine damage or failure.
The warning signs of a potential riser failure can be subtle. Hard starting and an unusual knocking sound on startup may indicate a leak, but by then, the damage is often already done. External rust on the manifold or riser is a telltale sign of internal damage. Other signs include overheating at high speeds or under load, and corrosion at the joint between the manifold and riser, indicating a failed gasket.
The inspection interval depends on the location and usage of the boat. In saltwater environments, risers should be inspected annually or every two years. In freshwater areas, biannual inspections are generally sufficient. It is recommended to replace risers every 4-5 years in saltwater and every 5-7 years in freshwater.
A faulty riser can lead to water intrusion into the engine's cylinders, resulting in seized pistons or a "hydrolock" condition. This occurs when water enters the cylinders and cannot be compressed, causing massive and often irreparable engine damage when attempting to start the engine. Consequently, faulty risers can lead to costly repairs or even engine replacement.
To prevent faulty risers, it is crucial to perform regular inspections and maintenance. Pay close attention to any signs of corrosion or leakage. Consider converting to a freshwater cooling system, which can extend engine life and reduce the risk of raw-water corrosion. Additionally, always use new gaskets when reinstalling or replacing risers.