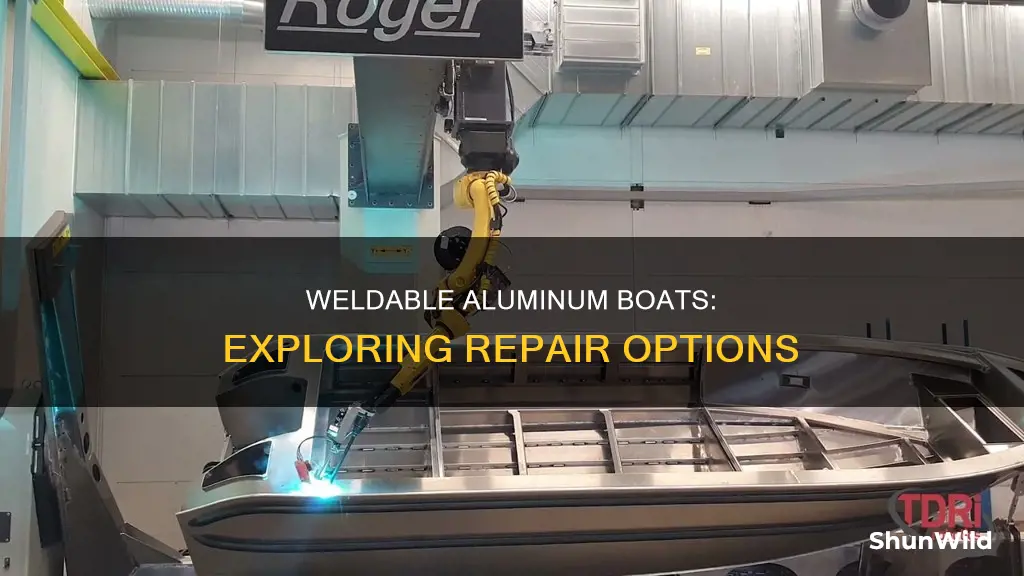
Welding an aluminum boat is a challenging task that requires expertise and specialized equipment. Aluminum's high thermal conductivity, low melting point, and fast heat dissipation make it prone to warping or burn-through during the welding process. Proper surface preparation is crucial, and the use of a MIG or TIG welder is essential for achieving stable wire feed and clean welds. While it is possible for an inexperienced welder to attempt repairs on an aluminum boat, it is important to understand the parameters of aluminum welding and have the right tools to avoid further damage. Seeking advice from experienced welders or considering alternative methods like riveting or aluminum brazing may be more feasible options for beginners.
Welding equipment
Welding aluminium boats is challenging and requires specific tools and expertise. Aluminium is sensitive to impurities and porosity, so it's essential to have the right welding equipment and ensure proper surface preparation. Here are some key considerations for selecting the appropriate welding equipment:
- MIG or TIG Welder: Aluminium welding typically employs MIG (Metal Inert Gas) or TIG (Tungsten Inert Gas) welding. These methods ensure a stable wire feed and help prevent contamination, resulting in solid and clean welds. TIG welding offers greater control and is suitable for thinner aluminium sheets, while MIG welding is more efficient for thicker materials.
- Spool Gun: When using a MIG welder, consider a spool gun to feed the soft aluminium wire, as it is too soft to push through a standard MIG hose/cable.
- HF (High Frequency) Machine: For MIG welding aluminium, you will need a machine with HF, which tends to be more expensive than a regular MIG welder.
- Argon Gas: Argon is necessary for shielding gas when welding aluminium. It prevents contamination and ensures weld quality.
- Filler Material: Choose a filler rod or wire that matches the base aluminium material. For marine-grade aluminium, 5356 and 4043 filler materials are commonly used.
- Welding Environment: Weld in a clean, controlled environment to prevent contaminants. If welding outdoors, use a portable welding shelter to protect the area from wind, dust, and moisture, ensuring a stable welding environment.
- Practice and Technique: Aluminium welding requires mastering specific techniques, such as maintaining a consistent travel speed and using a push technique to keep the shielding gas in the weld pool. Practice on scrap aluminium pieces to refine your technique and achieve strong, durable welds.
Boat Shoes for Women: Styling Tips and Tricks
You may want to see also
Surface preparation
Cleaning the Aluminum Surface:
- Use a stainless steel brush designed specifically for aluminum to scrub the surface. This step helps remove any dirt, grease, or oxide layers that may be present.
- Ensure the cleaning process is done just before welding to maintain a clean surface.
- Consider using acetone as a cleaning agent to ensure a thorough removal of contaminants.
- Avoid using any tools that have been previously used for steel, such as grinding wheels, discs, or wire brushes, as this can lead to contamination.
Segregating Tools:
It is recommended to keep tools specific to aluminum welding separate from those used for other materials to prevent cross-contamination.
Understanding Aluminum's Properties:
- Aluminum has a lower melting point than steel, but it dissipates heat much faster. Therefore, you will need to use higher heat settings than you would with steel to create a weld puddle.
- Aluminum heats up and cools down rapidly, so it is crucial to control the heat input to avoid warping or burn-through.
Preheating:
Preheating the aluminum surface slightly before welding can help manage heat flow and create more consistent welds.
Practice and Technique:
- Before attempting to weld your boat, practice on similar aluminum pieces or scraps to gain experience with the unique properties of aluminum.
- When welding, maintain a consistent travel speed to ensure even heat distribution along the weld.
- Use steady hand movements and closely monitor the weld pool.
- Employ a push technique rather than a pull technique when welding aluminum to keep the shielding gas in the weld pool, further reducing the risk of contamination.
Remember, proper surface preparation is key to successful aluminum boat welding. Taking the time to prepare the surface will help ensure strong and durable welds, enhancing the overall quality and appearance of your project.
Designing a Boat Hull Using Fusion 360: A Comprehensive Guide
You may want to see also
Heat input
Aluminium is a complicated metal to weld, especially for beginners. Its high thermal conductivity means it heats up and cools down quickly, leading to warping or burn-through. To avoid these issues, it is important to control the heat input during the welding process. Here are some tips for managing heat input when welding aluminium boats:
- Use short welds: To prevent overheating, it is recommended to use short welds and allow the aluminium to cool between passes. This helps to maintain control over the heat input and prevents warping.
- Preheat the aluminium: Slightly preheating the aluminium can help manage the heat flow and create more consistent welds. This technique is useful for managing the rapid temperature changes that aluminium undergoes during welding.
- Choose the right welding equipment: Selecting a welder designed for aluminium welding, such as a MIG or TIG welder, is crucial. These welders ensure a stable wire feed and reduce the risk of contamination, which is essential for achieving solid and clean welds.
- Maintain consistent travel speed: When welding, it is important to maintain a consistent travel speed to ensure even heat distribution along the weld. Steady hand movements are crucial for controlling heat input and achieving strong and durable welds.
- Use a push technique: Using a push technique, instead of a pull technique, when welding aluminium helps keep the shielding gas in the weld pool. This reduces the risk of contamination and ensures a clean weld.
- Practice on scrap pieces: Before welding an aluminium boat, it is advisable to practice on scrap pieces of aluminium to familiarise yourself with the metal's characteristics and the welding process. This will help you refine your technique and manage heat input effectively.
- Avoid using oxy-fuel: Oxy-fuel contains oxygen, which can lead to oxidation in your welds. Instead, use a stainless steel brush and acetone to clean the aluminium surface and remove any aluminium oxide.
- Choose the right filler material: The filler rod or wire should match the base aluminium material. For marine-grade aluminium, 5356 and 4043 filler materials are commonly used.
By following these tips and controlling the heat input, you can achieve successful welds on your aluminium boat and prevent issues like warping and burn-through.
V-Drive Boats: Turning Basics Explained
You may want to see also
Filler material
It is crucial to use the correct filler alloy when welding aluminium. The wrong filler alloy can lead to weak welds, cracking, or corrosion issues. Aluminium alloys used as filler materials are typically wrought alloys, meaning they are workable and can be welded or forged. Common wrought alloys used as filler materials include the 1xxx, 4xxx, 5xxx, and 6xxx series alloys.
The 1xxx series alloys, also known as the commercially pure aluminium group, contain a minimum of 99% aluminium. These alloys are often used as filler materials for aluminium boats due to their excellent corrosion resistance and formability. However, they have relatively low strength compared to other alloys.
The 4xxx series alloys are aluminium-silicon alloys, which have good corrosion resistance and are commonly used for welding aluminium boats. They are known for their strong weldability and are often used as filler alloys for the 6xxx series alloys.
The 5xxx series alloys, or aluminium-magnesium alloys, are widely used as filler materials for marine-grade aluminium. They offer excellent corrosion resistance and are commonly used for welding aluminium boats operating in saltwater environments.
The 6xxx series alloys, or aluminium-magnesium-silicon alloys, are commonly used as base materials in aluminium boats. They have good corrosion resistance and are often welded using 4xxx or 5xxx series alloys as filler materials.
When selecting a filler alloy for your aluminium boat, it is important to consider factors such as the alloy series, corrosion resistance, weldability, and the intended operating environment. Consulting with a welding expert or referring to alloy selection guides can help you make an informed decision.
Taking Apart a Boat Lift: Step-by-Step Guide
You may want to see also
Welding environment
Welding aluminium can be challenging due to its high thermal conductivity. It quickly heats up and cools down, often resulting in warping or burn-through. To successfully weld aluminium, it is crucial to control the heat input. This can be achieved by using short welds and allowing the material to cool between passes. Preheating the aluminium slightly can also aid in managing the heat flow and creating more consistent welds.
When welding aluminium, it is essential to work in a clean and controlled environment to prevent contaminants from compromising the weld. Welding outdoors can be tricky, but using a portable welding shelter can help shield the area from wind, dust, and moisture. This helps to maintain a stable welding environment and improves the overall quality of the welds.
Additionally, the welding environment should be well-ventilated to remove any fumes produced during the welding process. Proper ventilation ensures the safety of the welder and prevents the buildup of hazardous gases. It is also important to ensure that the welding area is free from any flammable materials or substances that could ignite due to the heat and sparks generated during welding.
Furthermore, the welding environment should be free from drafts and air currents that could affect the shielding gas used in the welding process. Proper shielding gas coverage is crucial for successful aluminium welding, as it helps to protect the weld pool from contamination and ensures strong and clean welds.
To summarise, controlling the heat input, working in a clean and controlled environment, ensuring proper ventilation, and maintaining stable shielding gas coverage are key factors in creating a suitable welding environment for aluminium boats. These considerations will help produce high-quality welds and ensure the safety of the welder.
Boat Registration Renewal: Florida's Rules and Requirements
You may want to see also
Frequently asked questions
Welding an aluminum boat is challenging and requires specific tools and expertise. It is not recommended for beginners. If you are inexperienced, it is best to seek professional help to ensure the job is done correctly and safely.
Aluminum has a low melting point and high thermal conductivity, so it heats up and cools down quickly. It is also very easy to burn through aluminum, especially thin sheets, compared to steel.
You will need a welder designed specifically for welding aluminum, such as a MIG or TIG welder. A spool gun is also necessary, as aluminum wire is too soft to push through a standard MIG cable.
Proper surface preparation is crucial. The aluminum surface must be thoroughly cleaned to remove any dirt, grease, or oxide layers. Use a stainless steel brush designed for aluminum, and clean just before welding to prevent contamination and ensure a clean weld pool.