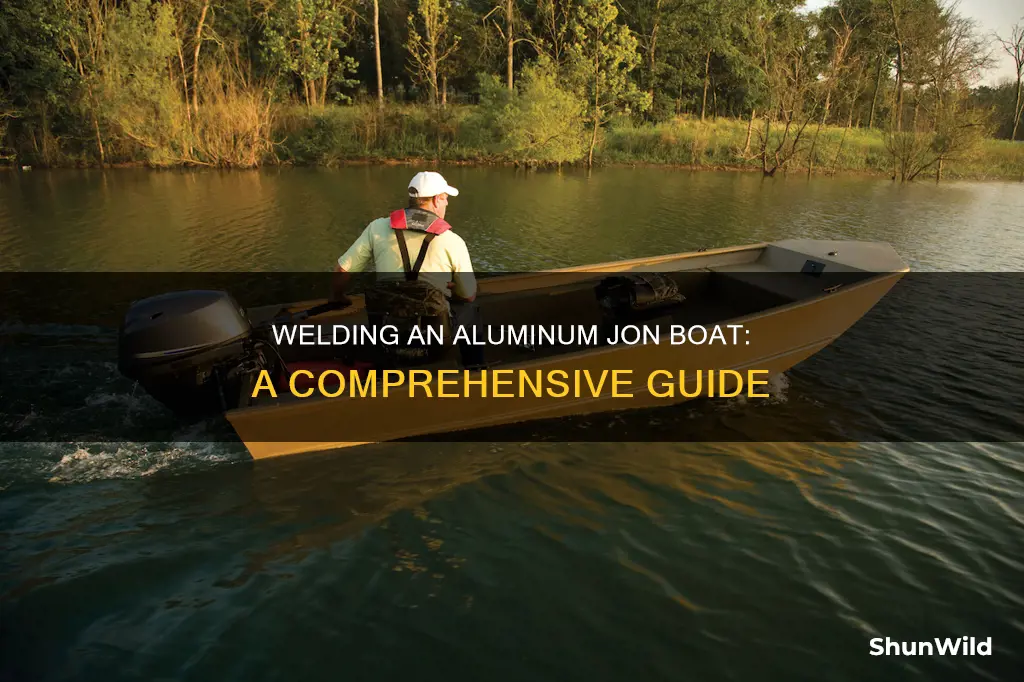
Welding an aluminium Jon boat can be a challenging task, especially for beginners. It requires specific tools, such as a MIG or TIG welder, and the ability to control heat input to avoid warping or burn-through. Aluminium boats are also very thin, which makes the welding process even more delicate. When welding aluminium, it is crucial to prepare the surface by cleaning it thoroughly to remove any dirt, grease, or oxide layers. Additionally, using the correct filler material is essential, with 5356 and 4043 filler materials commonly used for marine-grade aluminium.
Characteristics | Values |
---|---|
Welding equipment | MIG or TIG welder |
Surface preparation | Clean with a stainless steel brush to remove dirt, grease or oxide layers |
Filler material | 5356 and 4043 filler materials |
Welding environment | Clean, controlled environment; use a portable welding shelter if outdoors |
Technique | Maintain consistent travel speed, use a push technique, practice steady hand movements |
What You'll Learn
Selecting the right welding equipment
When it comes to welding aluminium boats, selecting the right equipment is crucial. Aluminium requires specific welding tools, such as a MIG or TIG welder. This setup ensures a stable wire feed and reduces the risk of contamination, which can compromise weld quality.
If you're using a MIG welder, you'll need a spool gun as the standard MIG setup cannot push the soft wire through the cable. Additionally, make sure your welder has a gas solenoid to run pure Argon gas. Argon is necessary for welding aluminium and will protect your welds from contamination.
For thin aluminium sheets, TIG welding is often recommended as it offers greater control over the heat input, reducing the risk of burning through the metal. TIG welding is slower than MIG welding but is ideal for creating watertight welds.
If you're new to welding aluminium, it's essential to practice on scrap pieces first. Aluminium is a porous metal with a low melting point, so it's crucial to work fast and maintain a stable wire feed to prevent bird-nesting and wire jams.
Before welding, ensure your aluminium boat is free of any dirt, grease, or oxide layers. Use a stainless steel brush to clean the surface, and if necessary, use a flap wheel to remove paint, silicone, or other contaminants.
Remember, welding aluminium boats can be challenging, and it's easy to make mistakes that compromise the integrity of your boat. If you're unsure or inexperienced, consider seeking the help of a professional welder with boat experience.
Sailing Solo: California to Texas
You may want to see also
Preparing the aluminium surface
Before you begin welding your aluminium Jon boat, it is crucial to prepare the aluminium surface adequately. Here is a step-by-step guide to help you through the process:
- Clean the aluminium surface: Use a stainless steel brush specifically designed for aluminium to scrub the surface and remove any dirt, grease, paint, or oxide layers. Ensure you clean the surface thoroughly and right before welding to prevent contamination.
- Remove all contaminants: After scrubbing, use a stainless steel wire brush to remove any remaining aluminium oxide. It is essential to understand that aluminium, unlike steel, is not forgiving of contamination. Therefore, ensure the surface is immaculate and free of any substances.
- Ensure a clean weld pool: By properly cleaning the aluminium surface, you will ensure a clean weld pool, which is crucial for achieving strong welds. Any contaminants left on the surface can lead to "popcorn gobble," which results in burnt and porous welds instead of solid welds.
- Use a flap wheel: If there is paint on the aluminium surface, use a flap wheel to remove it completely. This step ensures that the welds are clean and strong.
- Prepare the base material: If you are repairing a crack or hole in your Jon boat, ensure that you drill the ends of the crack to prevent it from spreading further. This step is crucial, especially if the crack is due to fatigue.
- Consider the environment: Environmental factors can impact the quality of your welds. Ideally, weld in a clean, controlled environment to prevent contaminants like wind, dust, and moisture from affecting your welds.
Remember, proper surface preparation is key to successful aluminium welding. Taking the time to prepare the aluminium surface will ensure that your welds are strong, clean, and durable.
Revamping Boat Seat Cushions: A DIY Guide
You may want to see also
Controlling heat input
Aluminium's high thermal conductivity can make welding challenging. It heats up and cools down quickly, leading to warping or burn-through. To avoid these issues, it is important to control the heat input. Here are some tips to help you achieve this:
- Use short welds and allow the material to cool between passes.
- Preheat the aluminium slightly to help manage the heat flow and create more consistent welds.
- Maintain a consistent travel speed to ensure even heat distribution along the weld.
- Practice steady hand movements and keep a close watch on the weld pool.
- Use a push technique rather than a pull technique when welding aluminium. This helps keep the shielding gas in the weld pool and reduces the risk of contamination.
- Ensure your gun lead is as straight as possible. Any bends or kinks can cause bird-nesting of the soft aluminium wire.
- Use a teflon liner in the MIG gun. Unlike the coiled wire liner used for steel, the teflon liner doesn't have internal edges that tend to shave aluminium as it passes through, reducing jams.
Boat Driving Age Requirements in New Hampshire
You may want to see also
Choosing the right filler material
When welding an aluminium jon boat, it is important to select the right filler material to ensure strong and durable welds. The choice of filler material depends on various factors, including the thickness of the aluminium sheets, the welding process being used, and the desired weld quality. Here are some considerations to help you choose the right filler material for your aluminium jon boat project:
Welding Process:
The welding process you plan to use will influence the choice of filler material. For MIG welding, you will need a spool gun to feed the soft aluminium wire, as pushing it through a standard hose/cable can cause issues. TIG welding, on the other hand, offers greater control over the heat input, making it a preferred method for welding aluminium. However, it is slower than MIG welding and puts more heat into the metal, potentially causing warpage.
Thickness of Aluminium Sheets:
The thickness of the aluminium sheets in your jon boat will play a crucial role in selecting the appropriate filler material. Thinner sheets, such as those around 0.10" thick, require a welding process that can be controlled precisely to avoid burning through the metal. TIG welding is often recommended for such applications. Heavier-gauge material, on the other hand, may be more suitable for MIG welding, but it is crucial to ensure that the equipment can handle the increased thickness.
Filler Metal Alloy:
When welding aluminium, it is essential to use a filler metal alloy specifically designed for this purpose. One commonly recommended alloy for welding aluminium boats is ER5356, which is a 5000-series alloy rated for marine use. Another option mentioned is ER4043, a 4000-series alloy that is softer and not recommended for marine applications. It is crucial to select a filler alloy that meets the required specifications and is suitable for the intended environment.
Gas Selection:
When MIG welding aluminium, the choice of shielding gas is crucial. Pure argon gas is typically recommended for this process, as it provides the necessary protection from contamination. Using a blend of argon and CO2, or other gas mixtures, may not yield optimal results and can lead to weld defects.
Practice and Experience:
Welding aluminium boats requires skill and experience. It is essential to practice on scrap pieces of similar thickness to your jon boat to get a feel for the process and make adjustments as needed. This will help you understand the characteristics of aluminium welding and make more informed decisions about filler material selection.
Professional Assistance:
If you are unsure about the welding process, filler material selection, or equipment setup, it is advisable to seek professional assistance. Experienced welders who specialise in aluminium boat repairs can provide valuable insights and help you avoid common pitfalls. They can also recommend specific filler materials based on their knowledge and expertise.
Boat Shoes and Rain: A Watery Grave?
You may want to see also
Practicing proper technique
- Maintain a consistent travel speed – This ensures even heat distribution along the weld.
- Practice steady hand movements – Keep your hands steady and move them at a consistent speed to ensure the weld pool is even and consistent.
- Keep a close watch on the weld pool – Monitor the weld pool closely to ensure that it is the correct size and shape, and make adjustments as necessary.
- Use a push technique – When welding aluminium, use a push technique instead of a pull technique. This helps to keep the shielding gas in the weld pool and reduces the risk of contamination.
- Use short welds – Aluminium heats up and cools down quickly, so use short welds to avoid warping or burn-through.
- Allow the material to cool between passes – Give the aluminium time to cool down between weld passes to maintain control over the heat input and create more consistent welds.
- Preheat the aluminium – Preheating the aluminium slightly can help manage the heat flow and create more consistent welds.
- Practice on scrap aluminium – Get some scrap pieces of aluminium and practice your welding technique before attempting to weld your Jon boat. This will help you refine your technique and improve the quality and appearance of your welds.
Best Situations to Use a Plow Boat Anchor
You may want to see also
Frequently asked questions
Aluminium boats are often very thin, which makes them difficult to weld without burning through. Aluminium also has a lower melting point than steel, so it's important to work quickly. The metal must be thoroughly cleaned before welding to ensure a strong weld.
TIG welding is recommended for repairing aluminium boats because it offers greater control over the heat input, reducing the risk of warping or burning through the thin metal. However, it is a slow process and requires a lot of practice to master. MIG welding can also be used, but it is less controllable and has a higher risk of contamination.
The filler material should match the base material to ensure compatibility and strength. For most marine-grade aluminium, 5356 and 4043 filler materials are commonly used.