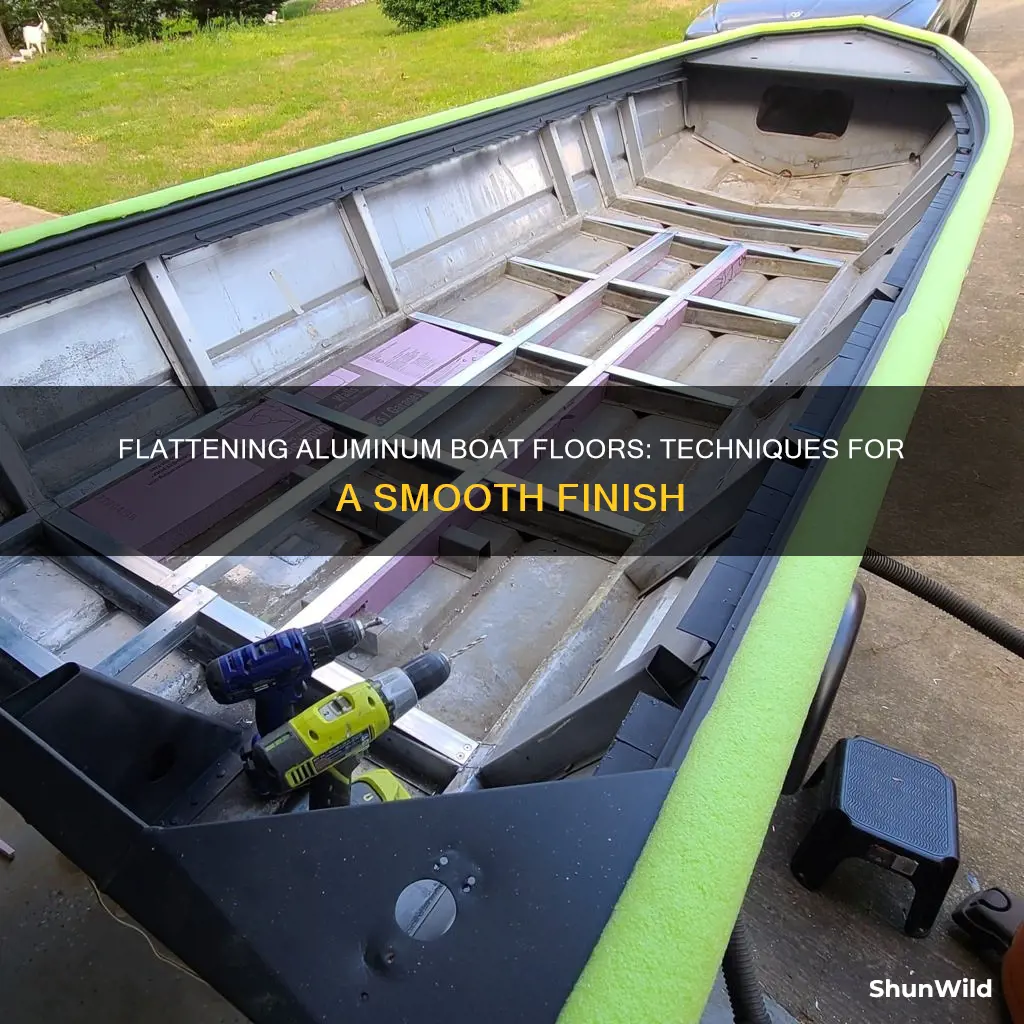
Adding a flat floor to an aluminium boat is a popular topic among boat enthusiasts. Many people opt for a flat floor in their aluminium boat to increase stability and comfort. There are several ways to achieve this, including using marine-grade plywood, aluminium sheeting, or aluminium angle iron. Some people also choose to add extra bracing or supports to ensure the floor can bear weight. It is important to consider the weight of any added material, as well as the potential impact on the centre of gravity and performance of the boat.
What You'll Learn
Using wood for support
Materials and Tools
First, gather your materials and tools. You will need:
- Marine-grade plywood of the same thickness as the previous floor. This ensures the boat seat and hull rivet holes line up. For a 14-foot boat, 1/2” thick plywood should be sufficient.
- 3/16” Pop Rivets with Large Flange, in varying lengths depending on the thickness of your plywood.
- 3/16” Pop Rivet washers for backup support.
- 3/16” Diameter Solid Aluminium Rivets to attach seats, storage compartments, and equipment.
- 1/2” Stainless Steel Staples for reattaching the floor covering.
- 1/2” Stainless Steel Screws to secure seats and storage compartments.
- Marine-grade silicone to seal rivets and screws.
- Floor covering (vinyl or carpet) and appropriate glue.
- Safety glasses, hearing protection, leather gloves, tape measure, drill, air compressor, air hammer, staple gun, pop rivet gun, saw horses, and a jigsaw.
Prepare the Plywood
Start by sealing all surfaces of the plywood with good-quality oil-based paint. Apply two coats to the top and bottom, allowing 24 hours of drying time between coats. This process will take four days in total.
If your boat floor is wider than a standard 4x8-foot plywood sheet, you can cut a 4x10 sheet in half and splice the two pieces together to make a 5x8 foot sheet. Reinforce the plywood seam with a 1/8”x2” aluminium strap secured with large flange pop rivets. Space the rivets 6 to 8 inches apart, ensuring the strap does not touch any keel or cross-member supports.
Prepare the Boat
While waiting for the paint to dry, clean the inside of the boat thoroughly with a pressure washer. Remove any remaining old rivet pins with pliers or a hammer and tapered punch. Mark the locations of the hull cross members on the side of the boat, so you can see them when the new floor is in place.
Install the New Floor
Now, it's time to install the new floor. Dry fit the plywood floor in the boat, leaving a gap of at least 1/8” on each side. Trim or sand the edges as needed for a good fit.
Drill holes in the new floor for the pop rivets to secure it to the cross-member supports. Before inserting the rivets, apply a small dab of marine silicone around each hole. Install the rivets around the perimeter of the floor and in all the identified supports.
Reinstall Boat Seats and Storage Compartments
Finally, reinstall the boat seats and storage compartments. Use tapered punches or a Cleco tool to align the holes in the seat flange with the corresponding holes in the boat's hull. Start by securing the centre rivet, then work outwards. If there is a loose fit between the seat flange and the hull, use a screw and nut to snug the surfaces together before riveting.
Maintenance
Remember to regularly inspect and maintain your boat floor to ensure its longevity. Check for loose rivets, signs of damage, or leaks. With proper care, your new wood-supported aluminium boat floor should serve you well for many years.
Finding Boat Values: The NADA Guide Explained
You may want to see also
Welding the floor
Welding is a permanent solution and works great if you never want to remove the floor again. However, if you use your boat a lot in winter, with leaves, pine needles, and road salt getting inside, welding may be more work than it is worth. If you can't completely seal the water out of the hull, you need to be able to flush it out.
If you are worried about the strength of screws, you can Teflon the screws so two opposite metals won't touch. Another option is to use a strip of 3M adhesive-backed industrial velcro on one end.
One user suggests using 1.5x1.5x1/8 aluminium angle across all ribs, adding more horizontal braces between the original ribs, and then running centre supports parallel with the boat. They then plan to weld everything on the backside for added support.
Another user suggests using 1-1/4" aluminium angle along the sides of the hull, attaching it with pop rivets. They suggest adding vertical supports to the ribs and attaching the angle to the tops of them from left to right to build the skeleton. More bracing equals better structure and stability.
Boat Show Opening Times: Palm Beach Schedule
You may want to see also
Screws
One option is to use self-tapping screws to secure the floor. This method is recommended by some boat builders, who suggest screwing through aluminium square tubing into the ribs of the boat. This provides a strong and secure connection. However, it is important to consider the weight that the floor will need to support and add additional bracing if necessary.
Another approach is to use stainless steel screws. These can be drilled directly into the sides of the ribs, providing a secure hold. This method is suggested for aluminium angle flooring, where screws can be drilled into the side of the ribs near the centre channels.
When using screws, it is important to consider the galvanic corrosion that can occur when different metals come into contact, especially in a marine environment. To avoid this, some boat builders recommend using Teflon on the screws to prevent direct contact between the aluminium and stainless steel. Additionally, using large-headed screws can provide more surface area and a stronger hold.
Overall, screws are a versatile and effective method for securing the floor of an aluminium boat. They can be used in various configurations and provide a strong and durable hold. However, it is important to consider the materials used and the need for additional bracing to ensure a long-lasting and safe installation.
Understanding Draft: How Sailboats Sail Through Water
You may want to see also
Rivets
When it comes to riveting a flat floor in an aluminum boat, there are a few things to consider. Firstly, it is important to use the appropriate type and size of rivets. Aluminum pop rivets are a good option to attach a plywood floor to aluminum ribs or braces. These rivets should be large-headed and large-diameter, with a length that is slightly longer than the thickness of the material being joined. For example, if you are riveting through 1/4" aluminum braces, you might use 1/4" or 5/16" rivets. Using tight-fitting holes and an air riveter will ensure a secure and quick installation.
Another consideration is whether to use rivets or screws. Some people prefer screws because they can be tightened if they come loose, while rivets cannot. Screws with finish or cupped washers are one option, while others prefer stainless steel screws to avoid corrosion between different metals. However, rivets are generally preferred for their strength and ease of use. If you need to remove the floor in the future, you can simply drill off the rivet heads.
Additionally, it is important to consider the placement of the rivets. Some people create a template to mark the locations of the rivet holes, while others simply drill new holes to ensure accuracy. It is also recommended to add aluminum washers behind the ribs to increase the hold of the rivets.
Finally, if you are repairing leaky rivets in an aluminum boat, you can use a product like Muggy Weld's Super Alloy 5 rod and flux, applied with an oxyacetylene torch, to create a watertight and airtight seal.
Sig's Boat: Deadliest Catch's Unfortunate Turn of Events
You may want to see also
Velcro
When installing a flat floor in an aluminium boat, you may want to consider using Velcro. This method is suggested by a boat owner on Reddit, who has used it to secure cedar boards as a removable floor in their duck boat. The boards are friction-fitted, and the Velcro is used as an extra precaution to keep them in place when towing.
To use this method, cut the cedar boards to fit your boat, leaving 1/4" gaps between them. Then, attach a strip of Velcro to one end of each board. The adhesive-backed industrial Velcro will stick to the boards and create a removable floor that can be taken out for cleaning.
This method has the added benefit of avoiding the need to drill into the aluminium boat, which some boat owners prefer to avoid. It also allows for a removable floor that can be taken out and cleaned, and the boards are heavy enough to stay in place during use.
However, it is important to note that this method may not be suitable for all boats, and it is always a good idea to consult with a professional or experienced boat builder before making any modifications. Additionally, as Velcro is not a permanent adhesive, it may not be suitable for floors that need to bear a lot of weight or withstand heavy use.
Boat Insurance: A Must-Have for Peace of Mind
You may want to see also
Frequently asked questions
Marine-grade plywood wrapped in marine carpet is a popular option. You can also use aluminum sheeting, which is lighter than plywood.
You can use pop rivets, stainless steel screws, or self-tapping screws to secure the floor. If you're using aluminum, make sure the rivets are compatible to prevent galvanization.
Yes, you can use aluminum angle iron or tubing to support the floor. You may also need to add vertical supports or braces to ensure the floor can bear weight.
Yes, be careful not to raise the floor too high, as this can change the center of gravity and make the boat unstable. Also, consider adding floatation material, such as pour-foam, to improve buoyancy and provide additional support.