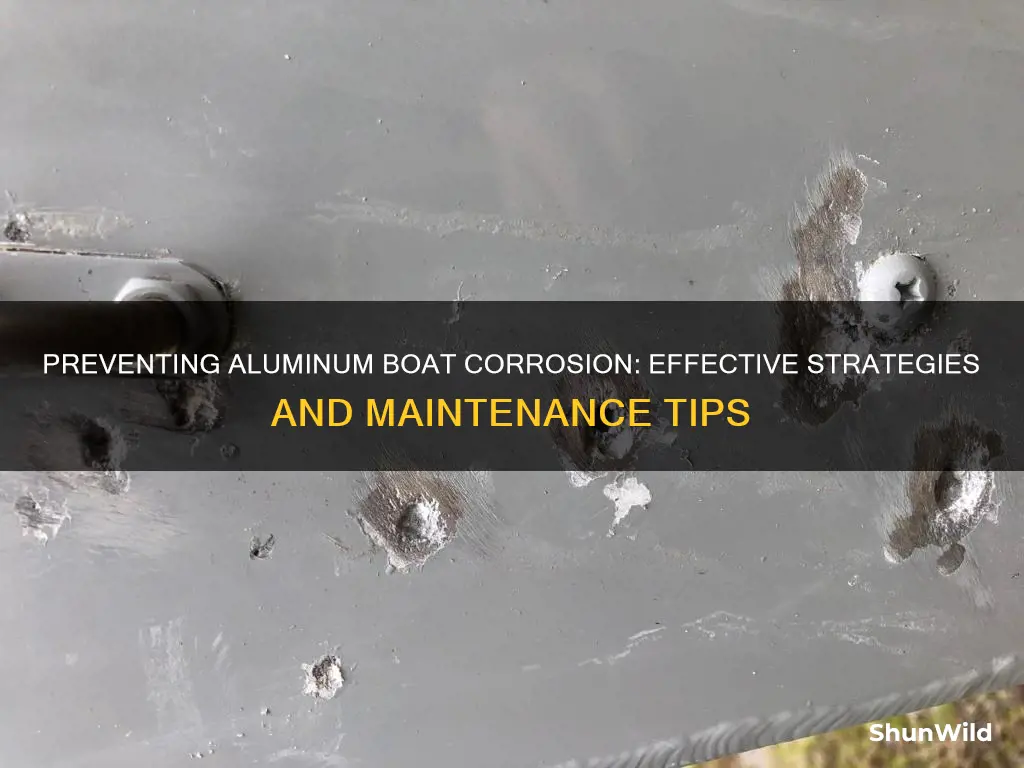
Aluminium boats are not corrosion-proof, and if they are not set up correctly and maintained, they can quickly become corrosive nightmares. Corrosion in aluminium boats typically starts from the inside out, so by the time it is visible on the outside, it has likely already caused significant damage. To prevent aluminium boat corrosion, it is important to regularly clean and dry the boat, flush the hull with fresh water after each use, and repair any cracks or scratches that expose the bare aluminium. Additionally, sacrificial anodes, such as zinc blocks, can be attached to the aluminium to protect it from galvanic corrosion.
What You'll Learn
Rinse the boat with freshwater after use
Rinsing your aluminium boat with freshwater after use is a crucial step in preventing corrosion. While aluminium boats are designed to be corrosion-resistant, they are not entirely corrosion-proof, especially when exposed to saltwater.
Freshwater rinsing helps to remove saltwater residue, which contains sodium chloride, a highly corrosive substance. By rinsing your boat, you can reduce the corrosive effects of saltwater and slow down the corrosion process. This is because freshwater is not as corrosive as saltwater and helps to dilute and wash away salt deposits.
To effectively rinse your boat, use a freshwater hose to flush out the hull after each fishing or boating trip. Remove the bung, let the saltwater drain, and then fill the hull with freshwater. It is recommended to do this before you trailer your boat home so that the freshwater can swish around inside the hull during transportation. Once you reach your destination, open the bung to allow the freshwater to drain completely.
Always remember to park your boat with the bow high and the bungs open. This enables the hull to drain and breathe, preventing moisture buildup and sweating. Additionally, ensure that all internal drainways are free from scum, leaves, and other debris that could trap moisture and contribute to corrosion.
By incorporating this simple step into your boat maintenance routine, you can significantly reduce the chances of corrosion and extend the lifespan of your aluminium boat.
Understanding Boat Battery Explosions: Causes and Prevention
You may want to see also
Avoid using dissimilar metal fittings
Aluminium boats are not entirely corrosion-proof, especially if low-grade aluminium is used. While aluminium naturally develops a hard outer coating that protects against corrosion (an oxide layer), saltwater can break this layer down, allowing corrosion to develop.
One way to prevent corrosion in aluminium boats is to avoid using dissimilar metal fittings. Dissimilar metals cause galvanic corrosion when immersed together in saltwater. This occurs when two dissimilar metals are brought together in an electrolyte solution, which could be freshwater or saltwater. When this happens, the connection is called a bimetallic couple, and a galvanic couple occurs when one of the metals becomes an anode and the other a cathode. The anode, or the less noble metal, corrodes faster, and the cathode, or the more noble metal, corrodes slower than they would if not coupled. This creates a galvanic response.
To avoid galvanic corrosion, it is important to understand the galvanic relationship between metals. This can be determined by the anionic scale, with gold scoring 0.00, brass -0.40, iron -0.85, aluminium -0.90, zinc -1.25, and magnesium -1.75. When galvanically coupled, the metal with the lower number will corrode faster. This information can be used to determine the need for and degree of protection to be applied to lessen the expected potential interactions.
One way to prevent galvanic corrosion is to isolate each dissimilar metal contact point. This can be done by using a sealing product such as Sikaflex or Duralac to provide a moisture barrier between the two metals.
Boat IPO Launch: When Will It Set Sail?
You may want to see also
Use sacrificial anodes
Sacrificial anodes are an effective way to prevent corrosion in aluminium boats. Anodes are made of different types of metal, such as zinc, aluminium, or magnesium, and they work by attracting corrosive ions, thereby protecting the metal parts of your boat. They are called "sacrificial" because they wear away quicker than your boat's metal, corroding faster to preserve your metal parts for longer.
Sacrificial anodes are particularly important for underwater metal parts, which are constantly exposed to metal ions in the water. These parts include propellers, shafts, rudders, and other submerged components. Anodes are placed underneath the boat, attached to all metal parts, and must remain submerged to perform their function. They can be welded, bolted, or tied with brackets to keep them in place.
It's important to note that anodes should be free of paint and other solvents when attached to metal parts, or they will lose conductivity. Additionally, they should be replaced before they are about half-used, which is usually every year, or every six months if your boat is used in saltwater.
Zinc anodes are commonly used, but they are not suitable for freshwater as they require saltwater to ensure a gradual corrosion process. Aluminium anodes, on the other hand, are more versatile and can be used in both saltwater and freshwater. They create a higher voltage and have a higher capacity than zinc anodes. However, it's important not to overdo it with aluminium anodes as too many can cause a crust to develop, rendering them ineffective.
Magnesium anodes are the most powerful option and are best used with the advice of a specialist. They are only suitable for freshwater applications and can cause rapid corrosion if used in saltwater due to their low resistance to salt.
When choosing the right anode for your boat, consider factors such as the type of water you'll be boating in, the specific metals used in your boat's construction, and the recommendations of the boat manufacturer.
Boat Launch Season: Potato Creek's Ramps Open Up
You may want to see also
Seal any exposed areas of the hull
Aluminium boats are susceptible to corrosion, especially when in contact with saltwater. While aluminium naturally develops a hard outer coating that protects itself against corrosion (an oxide layer), saltwater can break this layer down. Therefore, it is important to seal any exposed areas of the hull to prevent corrosion.
If your hull is painted, any chips, scratches, or holes drilled will leave the aluminium exposed to the environment. This will allow moisture to get between the paint and the hull, causing the paint to blister and peel off. To prevent this, seal any exposed areas with a suitable product, such as a sealing product like Sikaflex or Duralac. These products provide a moisture barrier between the aluminium hull and any stainless steel fittings.
It is also important to use paints and coatings designed for use with aluminium. Repair any cracks, scratches, or other damage that exposes the bare aluminium to prevent corrosion. Acid washing can also be used to clean the aluminium surface before applying a paint system or surface protection polymeric resin. However, it is important to seek professional advice before using this method.
In addition to sealing exposed areas, it is crucial to regularly flush out the hull of your boat with freshwater after each use. This helps remove any saltwater and prevent corrosion. Always leave the boat parked bow-high and the bungs open to allow the hull to drain and breathe, preventing sweating.
Keep Your Boat Afloat: Trickle-Charging Boat Batteries
You may want to see also
Avoid using automotive or car battery chargers
While aluminium boats are corrosion-resistant, they are not entirely corrosion-proof, especially if low-grade aluminium is used. Corrosion in aluminium boats starts from the inside out, so by the time it is visible on the outside, it is usually much worse than a pinhole and will require professional repair.
One of the most important things to do after each fishing trip is to flush out the hull of your boat with fresh water. Remove the bung, let the saltwater drain out, and then put a freshwater hose in to fill it up. Always leave the boat parked bow-high with the bungs open, enabling the hull to completely drain and breathe, preventing sweating.
Electric currents accelerate corrosion, so it is important not to use a car battery charger on board a boat. Always use an isolation transformer if you connect to AC shore power. Metal debris in the bilge or sitting in the bottom of the boat can also lead to galvanic corrosion, so be sure to clean up bottle tops and fishing gear such as hooks and sinkers.
Corrosion is caused by a chemical reaction when a material comes into contact with a liquid or dissimilar metal. In the case of aluminium boats, saltwater can break down the protective oxide layer that forms on the aluminium, allowing corrosion to develop. Dissimilar metal fittings incorrectly installed on the hull can also cause corrosion when combined with moisture.
To prevent corrosion, only use paint and coatings designed for use with aluminium, and always rinse the boat of saltwater after use. Repair any cracks and scratches that expose the bare aluminium, and avoid exceeding 1,300 millivolts of impressed voltage when protecting the aluminium.
Exploring Gibbs' Voyage: Coasting Along on His Boat Trail
You may want to see also
Frequently asked questions
If you have a leak on the outside of your boat, there is likely something more serious happening on the inside. If you can, lift the floor of your boat and flush it with fresh water. If you see a white paste on the surface of the aluminium or a white powder forming in the joints, then it is a sign that corrosion is taking place.
Always rinse your boat of saltwater after use. Do not exceed 1,300 millivolts of impressed voltage when protecting the aluminium. Repair cracks and scratches that expose the bare aluminium. Do not use an automotive battery charger on the boat.
You can't entirely repair corroded areas on the boat, but you can prevent major corrosion from happening. Nyalic has a coating system that covers repairs and prevents further corrosion.