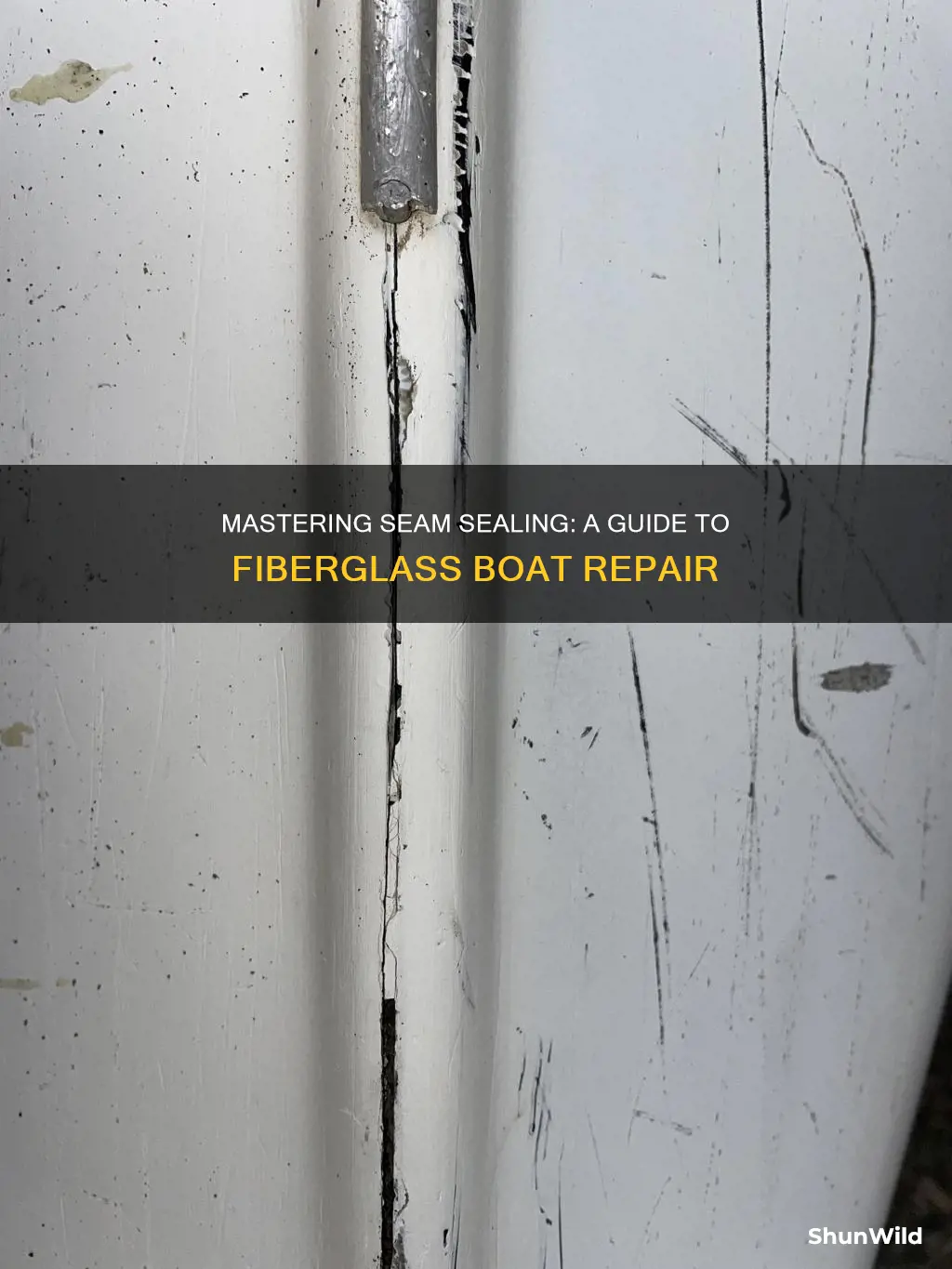
Sealing the seams on a fiberglass boat is a crucial step in ensuring its durability and longevity. Properly sealing these seams can prevent water infiltration, corrosion, and structural damage. This process involves several steps, including cleaning the surfaces, applying a suitable adhesive or sealant, and ensuring a tight fit. The right materials and techniques are essential to achieve a secure and long-lasting bond. This guide will provide a comprehensive overview of the process, offering tips and best practices to help boat owners and enthusiasts master the art of sealing fiberglass seams effectively.
Characteristics | Values |
---|---|
Sealing Materials | Epoxy resins, polyurethane, or specialized boat sealants. |
Surface Preparation | Clean the seam area, removing dirt, old sealant, and any debris. Ensure the surface is smooth and free of contaminants. |
Reinforcement | Use fiberglass tape or cloth to reinforce the seam, especially for structural repairs. |
Application Technique | Apply the sealant in a thin, even layer, following the manufacturer's instructions. Use a brush, roller, or spray gun for application. |
Curing Time | Allow sufficient time for the sealant to cure, typically following the product's guidelines. |
Weather Conditions | Perform the sealing in dry and moderate weather to ensure optimal results. |
Ventilation | Ensure proper ventilation during the application process to avoid inhaling fumes. |
Safety Gear | Wear protective gear like gloves, goggles, and a respirator when handling chemicals. |
Practice and Experience | Gaining experience with boat repair techniques can improve the quality of the seal. |
Regular Maintenance | Periodically inspect and re-seal the seams to maintain the boat's integrity. |
What You'll Learn
- Prepare the Surface: Clean and roughen the seam area for optimal bonding
- Choose the Right Adhesive: Select a strong, marine-grade epoxy or sealant
- Apply Tape or Strips: Use specialized tape or fiberglass strips for added strength
- Cure Properly: Allow adequate curing time and temperature for a strong bond
- Sand and Finish: Smooth the seam and apply a protective coating for durability
Prepare the Surface: Clean and roughen the seam area for optimal bonding
Preparing the surface of a fiberglass boat's seams is a crucial step in the sealing process, as it ensures a strong and durable bond between the materials. This step involves a thorough cleaning and surface preparation to create an ideal environment for the sealant to adhere effectively. Here's a detailed guide on how to achieve this:
Cleaning the Seam Area: Begin by thoroughly cleaning the entire seam area. Fiberglass surfaces can accumulate dirt, grease, and old sealant residue over time. Use a mild detergent or a specialized fiberglass cleaner to remove any grime. You can apply the cleaner with a soft cloth or a sponge, ensuring you cover the entire seam. Rinse the area with clean water to remove any soap residue, and allow it to dry completely. This initial cleaning step is essential to ensure the sealant doesn't have any contaminants to bond to.
Surface Roughening: The next step is to roughen the surface to provide a better grip for the sealant. Fiberglass is a smooth material, so creating a textured surface will enhance the bond. You can use various methods for this. One common technique is to lightly sand the seam area using fine-grit sandpaper (e.g., 400-grit or higher). Start with light pressure and gradually increase it to create a slightly textured finish. Be careful not to apply too much force, as it might damage the fiberglass. Alternatively, you can use a power tool like a random-orbit sander for a more efficient process, ensuring you follow the direction of the fiberglass weave.
After sanding, inspect the seam. The surface should now have a subtle texture, providing a better surface for the sealant to grip. Any remaining smooth areas should be lightly abraded to create a more uniform texture across the seam. This process ensures that the sealant has a consistent surface to bond to, reducing the risk of gaps or weak spots.
Additional Tips: It's important to work quickly after cleaning and roughening the seam, as moisture can affect the bonding process. If the area is wet, allow it to dry completely before proceeding. Additionally, ensure that the seam is free from any debris or loose fibers that might interfere with the sealant's application.
By following these steps, you'll create a prepared surface that is clean, textured, and ready for the sealant, ensuring a strong and long-lasting bond in your fiberglass boat's seams.
Shaw Indoor/Outdoor Carpet Windsurf: Boat-Friendly Flooring?
You may want to see also
Choose the Right Adhesive: Select a strong, marine-grade epoxy or sealant
When it comes to sealing the seams on a fiberglass boat, choosing the right adhesive is crucial for a durable and long-lasting repair. The harsh marine environment demands a strong and reliable bond, and that's where marine-grade epoxy comes into play. This specialized epoxy is designed to withstand the challenges of saltwater exposure, UV radiation, and the constant movement of boat parts.
Marine-grade epoxy resins are typically two-part systems, consisting of a resin and a hardener. These components should be mixed in the correct proportions to ensure optimal curing. Look for epoxy systems that offer excellent adhesion to fiberglass, providing a strong and flexible bond. The flexibility is essential as it allows the epoxy to accommodate the natural movement and expansion of the boat's materials, preventing cracks and delamination over time.
In addition to the epoxy itself, consider the choice of hardener. Different hardeners can significantly impact the final properties of the bond. For example, amine-based hardeners are known for their fast curing times and excellent resistance to heat and chemicals, making them ideal for marine applications. On the other hand, polyamine hardeners provide a more rapid cure and superior resistance to UV light, which is crucial for outdoor boat repairs.
When selecting an adhesive, ensure that it is specifically formulated for marine use. These products are engineered to resist the corrosive effects of saltwater, providing a long-term solution. They are also typically non-toxic, ensuring that they do not leach harmful chemicals into the water, which could have adverse effects on marine life.
Furthermore, the application process is just as important as the choice of adhesive. Proper surface preparation is essential to achieve a strong bond. Clean the seam area thoroughly, removing any dirt, grease, or old adhesive residue. Sanding the surfaces can also improve adhesion, creating a rougher texture that the epoxy can grip. Take the time to follow the manufacturer's instructions for mixing and application to ensure the best results.
Rolls-Royce Boat Tail: India's Exclusive Owners
You may want to see also
Apply Tape or Strips: Use specialized tape or fiberglass strips for added strength
Sealing the seams on a fiberglass boat is an essential step in maintaining its structural integrity and ensuring a smooth, leak-free interior. One effective method to achieve this is by applying specialized tape or fiberglass strips along the seams. This technique provides an additional layer of protection and reinforcement, making it an excellent choice for both new builds and repairs.
When choosing the right tape or strips, it's crucial to consider the specific requirements of your boat. Look for products designed for marine environments, as they are typically more durable and resistant to the elements. Fiberglass repair tape, often made from reinforced cloth or woven fiberglass, is an excellent option. These tapes are flexible yet strong, allowing them to conform to the shape of the seam while providing excellent bonding strength.
To begin the application process, ensure that the seams are clean and free of any debris or old sealant. Start by laying the tape or strip along the seam, ensuring it is centered and aligned properly. Press the tape firmly onto the seam, making sure there are no air bubbles or wrinkles. This initial step creates a strong bond and prepares the surface for further reinforcement.
For added strength, consider overlapping the tape or strips. This technique creates a layered effect, providing enhanced structural integrity. Overlap the strips by a few inches, ensuring they are properly adhered to each other. This method is particularly useful for larger seams or areas with higher stress points. Remember to apply firm pressure during the overlapping process to create a secure bond.
After applying the tape or strips, allow the recommended curing time for the adhesive to set properly. This ensures that the repair is strong and durable. Regularly inspect the seams and reapply additional layers or touch-ups as needed, especially in areas prone to wear and tear. By following these steps, you can effectively seal and strengthen the seams of your fiberglass boat, ensuring its longevity and performance.
Understanding Boat Engine Thermostats: Water Cooling System
You may want to see also
Cure Properly: Allow adequate curing time and temperature for a strong bond
Sealing the seams on a fiberglass boat is a crucial step in ensuring a durable and long-lasting vessel. One of the key aspects of achieving a strong bond between the fiberglass components is proper curing. This process involves allowing the sealant to set and harden according to the manufacturer's instructions, ensuring optimal adhesion and structural integrity.
When working with fiberglass, it's essential to understand that the curing process is temperature-dependent. The sealant requires a specific temperature range to initiate and complete the curing reaction. Typically, this involves applying heat to the sealed area, which can be done using various methods such as heat guns, heat blankets, or even sunlight on a sunny day. The goal is to maintain a consistent temperature within the recommended range for the specified duration.
Adequate curing time is just as important as temperature control. Different sealants have varying cure times, and it's crucial to respect these guidelines. Rushing the process by applying too much pressure or attempting to use the boat immediately after sealing can compromise the bond. Allow the sealant to cure fully, often requiring several hours or even days, depending on the product and environmental factors.
During the curing process, it's beneficial to keep the boat in a controlled environment, such as a garage or a shaded area, to protect it from direct sunlight and extreme weather conditions. These factors can affect the curing time and the overall quality of the bond. Additionally, ensure that the boat is clean and free of any debris or contaminants that might interfere with the sealant's ability to adhere properly.
By following the manufacturer's instructions for curing time and temperature, you can ensure that the sealant sets correctly, creating a robust and long-lasting seal. This attention to detail will contribute to the overall performance and longevity of your fiberglass boat, providing a reliable and safe marine experience. Remember, proper curing is a critical step in the process of sealing seams, so take the time to get it right.
Starting a Carbureted Boat Engine: A Step-by-Step Guide
You may want to see also
Sand and Finish: Smooth the seam and apply a protective coating for durability
Sealing the seams on a fiberglass boat is a crucial step in ensuring its longevity and structural integrity. Once the seams are properly prepared, the next step is to smooth them out and apply a protective finish to enhance durability. Here's a detailed guide on how to achieve this:
Sand the Seam: Begin by carefully sanding the seam area. Use fine-grit sandpaper, preferably 400-grit or higher, to create a smooth and even surface. Start with gentle, circular motions, gradually increasing the pressure to remove any remaining fibers or imperfections. Pay close attention to the edges of the seam, ensuring a consistent and smooth finish all around. This process helps to create a seamless appearance and prepares the surface for the next steps.
Prepare the Seam: After sanding, inspect the seam thoroughly. Look for any remaining rough spots or areas that require further smoothing. You can use a small file or a sharp blade to carefully remove any high spots. Take your time with this step to ensure the seam is as flat and even as possible. Cleaning the seam is also essential; wipe away any dust or debris using a damp cloth to create a clean and smooth base for the protective coating.
Apply a Filling Compound: Consider using a specialized filling compound designed for marine applications. This compound can help fill in any minor imperfections and create a seamless surface. Follow the manufacturer's instructions for application, typically involving mixing the compound with a catalyst to create a putty-like consistency. Apply this mixture to the seam, ensuring it is level and smooth. Allow it to cure according to the product's guidelines, which may involve covering it with a plastic bag or a temporary sealer.
Smooth and Finish: Once the filling compound has cured, inspect the seam again. If there are any visible imperfections or uneven areas, gently sand them down using finer-grit sandpaper. The goal is to achieve a smooth and seamless appearance. After sanding, wipe away any dust, and the surface is now ready for the final protective coating.
Protective Coating: Choose a marine-grade clear coat or varnish specifically designed for fiberglass. This protective layer will not only enhance the appearance of the boat but also provide a barrier against UV rays, moisture, and general wear and tear. Apply the coating using a brush or spray gun, ensuring an even and thin layer. Allow sufficient drying time between coats, and consider adding multiple thin coats for optimal protection and a professional finish. This final step ensures the seam is not only visually appealing but also well-protected.
Unraveling the Mechanics: How Ferry Boats Work
You may want to see also
Frequently asked questions
Sealing fiberglass seams is a crucial step in maintaining the integrity of your boat. The most common and effective method is to use a two-part epoxy resin and a hardener. This system provides a strong, flexible bond that can withstand the stresses of the marine environment. Start by cleaning the seams thoroughly to remove any dirt or old sealant. Then, apply a thin layer of the epoxy to the seam, ensuring it is well-coated. Allow it to cure slightly, then apply the hardener and mix thoroughly. Use a brush or spatula to spread the mixture along the seam, creating a smooth, even surface. Finally, sand the seam gently with fine-grit sandpaper to ensure a seamless finish.
Cracks in sealed seams can be a result of various factors, including improper application, poor-quality materials, or the natural expansion and contraction of the fiberglass. To prevent cracking, it's essential to use high-quality epoxy products and follow the manufacturer's instructions precisely. Ensure the epoxy is mixed correctly and applied in a thin, even layer. Avoid overloading the seam with too much material, as this can lead to bulging or warping. Additionally, consider using a fiberglass cloth or tape to reinforce the seam, especially in areas prone to stress, such as the hull-keel joint or the transom. Regular maintenance and inspection of the boat's seams are also key to catching any potential issues early.
While epoxy is the industry standard for sealing fiberglass seams, there are alternative methods available. One popular option is using a specialized fiberglass seam sealer, which is typically a two-part system similar to epoxy. These sealers are designed to be easy to apply and provide a strong bond. Another method is to use a butyl rubber tape, which is applied over the seam and then covered with a layer of fiberglass cloth and resin. This technique offers good flexibility and can be a viable option for certain applications. However, it's important to note that the choice of method depends on the specific requirements of your boat and the expertise of the person performing the work.