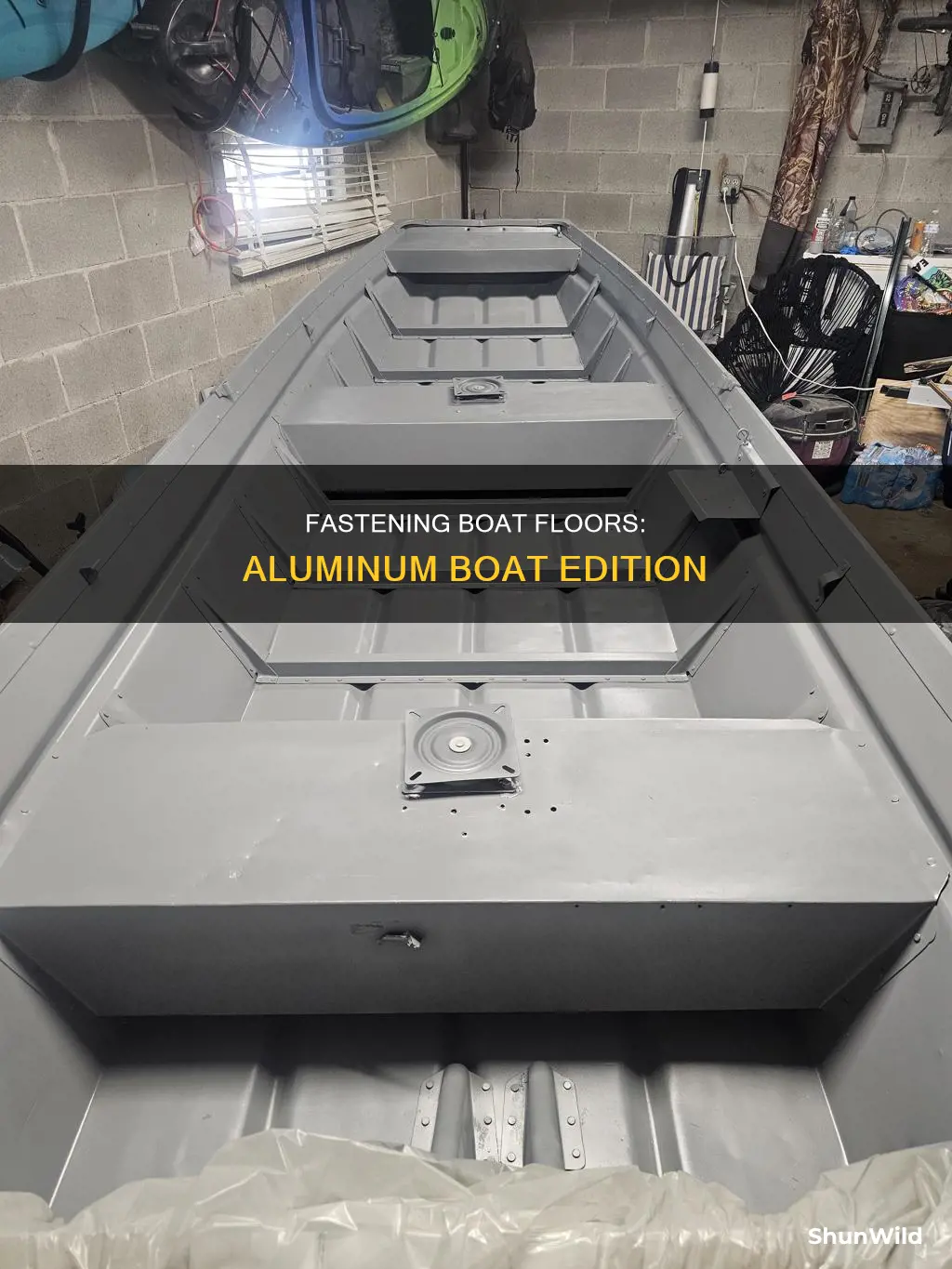
There are several methods for fastening a boat floor to an aluminium boat. One of the most popular methods is to use rivets, specifically 3/16 aluminium wide flange rivets. Some people also recommend using stainless rivets with large heads. Another option is to use screws, such as 1/2 stainless steel screws. It is also possible to use a combination of both rivets and screws. Additionally, some people suggest using Velcro or nutserts to attach the boat floor. When choosing a fastening method, it is important to consider the ease of installation and removal, as well as the durability and safety of the connection.
Characteristics | Values |
---|---|
Materials | Aluminium, plywood, oil-based paint, pop rivets, solid aluminium rivets, stainless steel staples and screws, marine-grade silicone, vinyl or carpet, floor covering glue, leather gloves, safety glasses, hearing protection, marine-grade plywood, EVA or foam pads, mild detergent, denatured alcohol, aluminium pop rivets, sheet metal screws |
Installation methods | Screws, rivets, welding, velcro, gluing |
Advantages | Anti-skid, noise cancellation, comfort, ease of installation, easy maintenance, decorative value, protection for the aluminium boat floor |
What You'll Learn
Screws, rivets, or welding?
When it comes to fastening the floor of an aluminum boat, there are several options to consider: screws, rivets, or welding. Each method has its advantages and limitations, so it's essential to understand their characteristics before making a decision.
Screws:
Screws are a popular choice for attaching the floor of an aluminum boat. They offer the advantage of being easy to install and providing a strong and secure connection. Stainless steel screws, in particular, are recommended for their durability and resistance to corrosion. However, screws may work loose over time due to vibration, especially if they are not properly secured or if the wrong type of screw is used. It is also important to consider the environment in which the boat will be used, as stainless steel fasteners can cause galvanic corrosion in aluminum boats used in brackish or saltwater.
Rivets:
Rivets are another common method for fastening the floor of an aluminum boat. They are favored for their ease of use, lightweight, corrosion resistance, and high construction efficiency. Closed-end rivets, in particular, offer excellent waterproofing capabilities and are widely used in aluminum boat construction. Additionally, riveting does not require specialized welding equipment or strong welding skills, making it a more accessible option for boat builders and repairers. However, one potential drawback of rivets is that they may loosen or come loose over time, requiring drilling and reinstallation.
Welding:
Welding is a permanent solution for fastening the floor of an aluminum boat. It provides a strong and secure connection that will not come loose over time. However, welding requires specialized equipment and skills, and it may not be suitable for all boat designs or materials. Additionally, welding can cause thermal impact on aluminum, affecting its performance and lightweight characteristics. Therefore, welding is often used in conjunction with other fastening methods, such as rivets, to ensure a sturdy and reliable connection.
In conclusion, when deciding between screws, rivets, or welding for fastening the floor of an aluminum boat, it is essential to consider the specific requirements of the boat, the environment in which it will be used, and the level of expertise available. Each method has its advantages and limitations, so it is crucial to weigh the benefits against the potential drawbacks before making a decision.
Dragon Boat Races: A Cultural Festival of Boat Racing
You may want to see also
Pros and cons of using screws
When it comes to fastening a boat floor, there are several options to consider, each with its own advantages and drawbacks. One option is to use screws, which offer both pros and cons.
Using screws to secure a boat floor has several benefits. Screws are easy to install and can be tightened if they become loose over time. They are also less likely to pull through the material than other fasteners, providing a strong and secure hold. Additionally, screws can be easily removed if the floor needs to be replaced or repaired. This makes them a good choice for areas that may require access in the future, such as over a fuel tank.
However, there are also some potential drawbacks to using screws. One concern is that screws can back out or loosen over time, particularly in wooden applications. To mitigate this, it is recommended to use stainless steel screws and apply red thread-locking compounds like Loctite to prevent loosening. Screws can also be more challenging to install in certain materials, such as fiberglass, as pilot holes need to be drilled with precision to avoid binding and breakage.
Another consideration when using screws is the potential for electrolysis or corrosion due to dissimilar metals. This is especially relevant when fastening an aluminum boat floor, as the combination of aluminum and stainless steel screws can lead to corrosion. To address this, it is important to use high-quality stainless steel screws and apply a coating or sealant to protect against corrosion.
Overall, screws can be a good option for fastening a boat floor, but it is important to carefully consider the specific application and take the necessary steps to ensure a strong and secure hold while mitigating potential drawbacks.
Deer Creek Boat Ramps: Open or Closed?
You may want to see also
Pros and cons of using rivets
When it comes to fastening an aluminum floor to an aluminum boat, there are several options to consider, each with its own set of advantages and disadvantages. One of the most common methods is the use of rivets, specifically solid rivets. Here are some pros and cons of using rivets for this application:
Pros of Using Rivets:
- Strong and Durable: Solid rivets are designed to resist external forces such as vibrations. They are typically made of strong and durable materials such as titanium, aluminum alloy, or nickel alloy.
- No Re-Tightening Required: Unlike traditional fasteners like nuts and bolts, solid rivets are permanent and do not require re-tightening over time. Once installed, they are designed to last.
- Cost-Effective: Rivets feature a simple design consisting of a head and a shank, which makes them less expensive to produce than more complex fasteners. This can be a budget-friendly option.
Cons of Using Rivets:
- Access to Both Sides Required: Solid rivets require access to both sides of the parts being joined. If you only have access to one side, blind rivets might be a better option as they are designed for single-side installation.
- Tooling Required: Special tools such as a compression tool or a pneumatic riveting gun are needed to install solid rivets. This can add to the overall cost and complexity of the installation process.
- Limited Reusability: Solid rivets are challenging to remove and reuse once installed due to their deformation during installation. If you anticipate the need to remove the floor panels in the future, other fasteners might be more suitable.
When deciding whether to use rivets or other fasteners like screws, it is important to consider the specific application, the ease of installation and removal, the cost, and the long-term maintenance requirements. While rivets offer strength and permanence, they may not be the best option if you anticipate the need for frequent adjustments or access to the underlying structure.
Who Really Owns the King Baby Boat?
You may want to see also
Welding: a permanent solution
Welding is a permanent solution for fastening an aluminium floor to a boat. However, it is not a simple process and requires a great deal of skill and experience. Welding aluminium is notoriously difficult, as the metal is extremely sensitive to heat and will burn through very quickly. It also requires absolute cleanliness, as any contamination can compromise the weld.
If you are an inexperienced welder, it is highly recommended that you do not attempt to weld an aluminium boat floor. Even experienced welders who are unfamiliar with aluminium welding should proceed with caution. It is important to understand the parameters of aluminium welding before attempting to weld an aluminium boat. The use of incorrect tools or techniques can result in a botched repair that will be costly and time-consuming to fix.
To weld aluminium, you need the right equipment. Aluminium welding is typically done using the TIG (Tungsten Inert Gas) method, which allows for greater control over the heat. MIG (Metal Inert Gas) welding can be used, but it is not ideal for thin aluminium as it runs hot and fast. Using the wrong type of welder can result in burning through the metal.
Before welding, the aluminium must be thoroughly cleaned with a stainless steel brush and acetone. Any tools that have been used for steel, such as grinding wheels or wire brushes, must not be used as they can contaminate the aluminium. It is best to keep tools used for aluminium welding separate to avoid contamination.
When welding, move quickly and be prepared to respond to the fast pace of aluminium welding. Aluminium runs hot and fast, and you need to be able to control the heat to avoid burning through the metal. Practice on aluminium coupons or scrap pieces of metal before attempting to weld your boat.
If you are not confident in your welding abilities, it is best to seek the help of a professional welder with experience in aluminium boat welding. They will be able to repair your boat properly and avoid any further damage.
Firefighters' Boat Mystery: What Kind of Vessel?
You may want to see also
Using Velcro for easy access
Using Velcro to fasten your boat floor can be a great option if you're looking for easy access and maintenance. Here are some detailed instructions and tips for using Velcro in your aluminum boat:
Advantages of Using Velcro:
- Easy installation and removal: Velcro allows for simple and tool-free installation and removal of your boat floor. You can easily lift and adjust the floor whenever needed without the hassle of drilling or screwing.
- Accessibility: Velcro provides excellent accessibility to the underside of your boat for maintenance tasks such as waterlogged foam, steering cable issues, or fuel tank access.
- No rattling or vibration: Unlike screws or rivets, Velcro won't come loose and cause rattling or vibration. It provides a secure and quiet hold.
- Flexibility: Velcro can accommodate any flex in your boat's structure. It's an excellent option if you're concerned about the rigidity of your boat's floor.
Step-by-Step Guide to Using Velcro for Your Boat Floor:
- Prepare the Surface: Clean the aluminum surface of your boat floor and the underside of your boat thoroughly. Ensure there is no dirt, grease, or debris that may interfere with the adhesion of the Velcro.
- Measure and Cut the Velcro Strips: Measure the length and width of your boat floor accurately. Cut the Velcro strips to size, allowing for a slight overlap on all sides.
- Adhere the Velcro Strips: Following the manufacturer's instructions, carefully adhere the Velcro strips to the boat floor and the corresponding areas on the underside of your boat. Apply firm and even pressure to ensure a strong bond.
- Allow for Drying and Curing: Depending on the type of adhesive used, allow the Velcro to dry and cure for the recommended amount of time. This step is crucial for ensuring maximum bonding strength.
- Test and Adjust: Once the adhesive has cured, carefully place your boat floor back in position and test the hold. If needed, you can adjust and reposition the floor until you achieve the desired fit.
- Maintenance: Periodically inspect the Velcro strips for any signs of wear or degradation. Depending on the conditions and frequency of use, you may need to replace the Velcro after a few years to maintain its holding strength.
Tips for Using Velcro:
- Choose a high-quality, marine-grade Velcro product that is suitable for outdoor use and can withstand moisture and UV exposure.
- Consider using a combination of Velcro and other fasteners for added security. For example, you can use Velcro along the perimeter of your boat floor and screws or rivets in strategic locations to provide extra strength.
- If you're concerned about the weight capacity or structural integrity, consider adding additional supports to the underside of your boat. This will reduce the load on the Velcro and ensure a sturdy floor.
- Keep in mind that Velcro may not be suitable for all boat floor materials. It works best with smooth surfaces, so if your boat floor has a textured or carpeted finish, you may need to make adjustments or explore other fastening options.
Boat Seats: Sewn, Safe, and Snazzy
You may want to see also
Frequently asked questions
There are a few methods to fasten a floor to the ribs of an aluminium boat. One option is to use stainless steel sheet metal screws, preferably with red locktite. Another option is to use aluminium pop rivets, which are easy to install and can be drilled out and replaced if they come loose over time. Welding the floor in place is also an option if you have access to a welder.
It is recommended to use 3/16" aluminium wide flange rivets. Dissimilar metals in contact are not good, especially in a marine environment, so it is important to use the correct type of rivets to avoid corrosion.
A boat floor kit can improve safety by providing a non-slip surface, reduce noise, and increase comfort with a soft and smooth foot touch. It is also easy to install and maintain, and can enhance the appearance of the boat.
To replace an aluminium boat floor, first remove the existing flooring material. Inspect the boat's floor structure for any damage or weak spots and address any issues. Measure the dimensions of the floor and cut marine-grade plywood to size. Apply a marine-grade adhesive to the boat's floor and place the plywood, using stainless steel screws for reinforcement. Seal any gaps or openings with a marine-grade sealant and allow it to dry completely before exposing the boat to water.