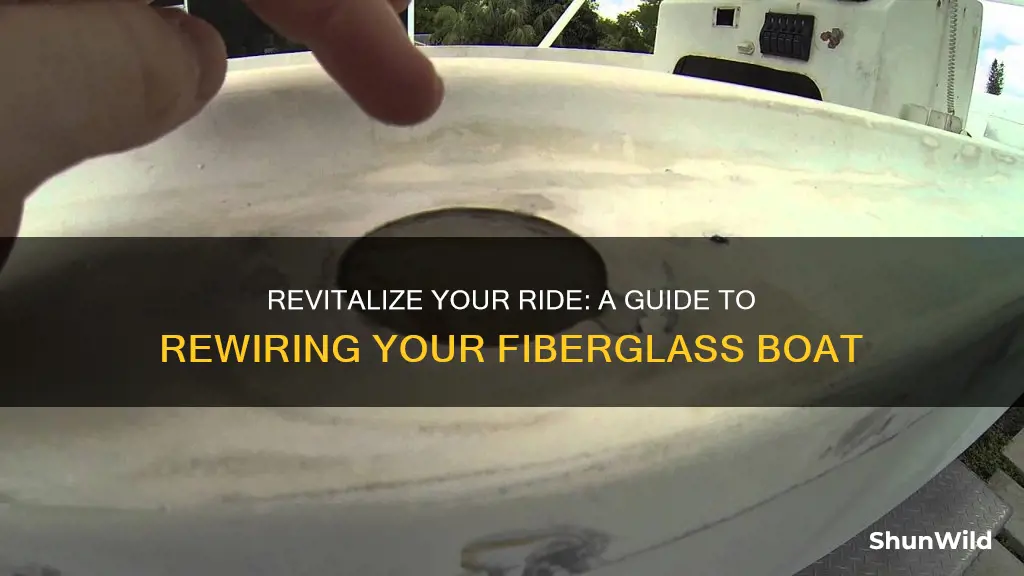
Rewiring a fiberglass boat can be a challenging but rewarding project for those looking to enhance the electrical systems of their vessel. This process involves replacing the existing wiring with new, modern alternatives to improve safety, reliability, and performance. It requires careful planning, specialized tools, and a thorough understanding of electrical systems to ensure the boat's electrical network is up to date and meets current standards. The steps involve identifying the current wiring layout, sourcing the appropriate replacement parts, and carefully disconnecting and reconnecting the wiring while ensuring proper insulation and protection against water damage. This guide will provide a comprehensive overview of the process, offering a step-by-step approach to successfully rewire a fiberglass boat.
What You'll Learn
- Safety Gear: Ensure you have protective gear like gloves, goggles, and a respirator
- Remove Old Wiring: Carefully disconnect and strip the old wiring to prepare for new connections
- Choose Suitable Wire: Select the appropriate gauge and type of wire for your boat's electrical needs
- Grounding: Proper grounding is essential; connect the new wiring to the boat's grounding system
- Waterproofing: Apply marine-grade sealant to protect the wiring from moisture and corrosion
Safety Gear: Ensure you have protective gear like gloves, goggles, and a respirator
When reworking the electrical systems of a fiberglass boat, prioritizing safety is paramount. This involves donning the appropriate protective gear to safeguard yourself from potential hazards. Here's a breakdown of the essential safety gear you should have:
Gloves: Opt for heavy-duty leather or synthetic gloves designed for electrical work. These provide insulation and protect your hands from sharp edges, hot surfaces, and potential electrical shocks. Ensure they fit comfortably, allowing for dexterity when handling wires and components.
Goggles: Safety goggles are crucial to shield your eyes from potential hazards. Fiberglass dust, flying debris, and sparks during soldering or cutting can cause severe eye damage. Choose goggles that offer side protection and a secure fit to prevent any foreign objects from entering your eyes.
Respirator: Working with fiberglass can release airborne particles and fumes, posing a risk to your respiratory system. A respirator mask with a suitable filter will protect you from inhaling these harmful substances. Look for a mask that fits snugly over your nose and mouth, ensuring it doesn't obstruct your vision.
Additionally, consider wearing ear protection, such as earplugs or earmuffs, to safeguard against potential noise hazards from power tools or generators. It's also wise to wear clothing that covers your skin, such as long sleeves and pants, to minimize exposure to fiberglass dust.
Remember, investing in high-quality safety gear is an investment in your well-being. By properly equipping yourself, you'll be better prepared to tackle the challenges of re-wiring your fiberglass boat while minimizing the risk of injury.
Finding Your Boat's Manufacturer: A Comprehensive Guide
You may want to see also
Remove Old Wiring: Carefully disconnect and strip the old wiring to prepare for new connections
When re-wiring a fiberglass boat, the first crucial step is to safely remove the old wiring. This process requires careful attention to detail to ensure a successful and safe re-wiring job. Start by identifying all the wires that need to be replaced or re-routed. This might include wiring for lights, engines, electronics, or any other electrical components. Once identified, carefully disconnect each wire from its respective terminal or connection point. Use the appropriate tools for this, such as wire cutters or crimping tools, to avoid damaging the wires.
As you disconnect the wires, take note of their color-coding and gauge (thickness), as this will help you reconnect them correctly later. After disconnecting, carefully strip the insulation from each wire. This step is essential to expose the bare copper or aluminum conductors. Use a wire stripper tool, ensuring you only remove the insulation and not the conductor. Be cautious not to damage the conductor during this process, as it will affect the wiring's performance.
For fiberglass boats, it's common to find wires with various insulation types, such as vinyl, rubber, or thermoplastic. Take care when stripping to avoid exposing the conductor too much, as this can lead to short circuits. Once all the wires are stripped, you'll have a clean and ready-to-use set of conductors for your new wiring setup. Properly managing and organizing these wires will make the next steps of soldering, splicing, or crimping much easier and more efficient.
Best Wood for Boat Trim: Choosing the Right Lumber
You may want to see also
Choose Suitable Wire: Select the appropriate gauge and type of wire for your boat's electrical needs
When rewiring a fiberglass boat, selecting the right wire is crucial for ensuring safe and efficient electrical performance. The process begins with understanding the electrical demands of your boat and the specific requirements of each circuit. Different electrical systems have varying current demands, and it's essential to match the wire gauge accordingly. For instance, higher-current circuits, such as those powering motors or large appliances, demand thicker wires to handle the load without overheating. Thinner wires, on the other hand, are suitable for lower-current applications like lighting or smaller accessories.
The type of wire also plays a significant role in the rewiring process. For fiberglass boats, it's generally recommended to use marine-grade wire, which is designed to withstand the harsh marine environment. These wires are often made with a durable insulation material that can resist moisture, salt, and temperature fluctuations. Common types of marine-grade wire include THHN (Thermo-Plastic High Heat-Resistant Nylon-Jacketed) and THWN (Thermo-Plastic High Heat-Resistant Nylon-Jacketed with a Wire Guard). THHN wire is suitable for dry environments and offers excellent heat resistance, while THWN wire is ideal for areas where moisture is a concern.
Another important consideration is the color-coding system used for marine wiring. Standard color-coding ensures that wires are identified correctly and connected to the appropriate circuits. Typically, black wires are used for power, while white or gray wires are neutral. Green or bare copper wires are often used for grounding. Adhering to these color-coding standards is essential for maintaining a safe and organized electrical system.
Additionally, it's crucial to consider the length of the wire runs. Longer runs may require additional insulation or the use of wire tracers to ensure the wires can handle the distance without significant power loss. In some cases, you might need to use wire connectors or terminals to join wires securely. Always ensure that the wire connectors are compatible with the gauge of the wires you are using.
In summary, choosing the right wire involves matching the gauge to the current demands of your boat's electrical system and selecting marine-grade wire for its durability. Understanding color-coding standards and considering wire length are also vital aspects of the rewiring process. By carefully selecting the appropriate wire, you can ensure a reliable and safe electrical system for your fiberglass boat.
Wiring a Boat Battery System: A Comprehensive Guide
You may want to see also
Grounding: Proper grounding is essential; connect the new wiring to the boat's grounding system
Grounding is a critical aspect of electrical systems in boats, especially when dealing with fiberglass vessels. Proper grounding ensures the safety of the boat and its occupants by providing a low-resistance path for electrical currents, preventing the buildup of static electricity, and protecting against electrical shocks. When re-wiring a fiberglass boat, it is essential to follow best practices for grounding to maintain a safe and efficient electrical system.
The first step is to identify the boat's existing grounding system. Most boats have a dedicated grounding wire or a grounding post, often made of a conductive material like copper or brass. This grounding point is typically connected to the boat's metal hull or a metal frame. Locate this point and ensure it is accessible for wiring connections.
Next, you'll need to connect the new wiring to the boat's grounding system. Start by stripping the insulation from the end of the new wiring and the grounding wire. Ensure both wires are clean and free of any debris. Then, connect the bare ends of the wires using a suitable grounding clip or crimp connector. This connection should be secure and provide a reliable path for electrical current. It is crucial to use the correct gauge of wire for grounding to ensure it can handle the expected current load without overheating.
After the physical connection, verify the grounding path by testing it with a multimeter. Measure the resistance between the new wiring and the grounding point to ensure it meets the safety standards. A low-resistance reading indicates a good ground connection. If the resistance is too high, you may need to re-evaluate the connection and ensure there are no loose or corroded components.
Remember, proper grounding is essential for the safety and functionality of your boat's electrical system. It helps prevent electrical fires, protects sensitive electronics, and ensures that any faults or short circuits are safely directed to the ground. Always follow the manufacturer's guidelines and consult a marine electrician if you are unsure about any aspect of the wiring process.
Boat Registration: A Quick Guide to Lookup Procedures
You may want to see also
Waterproofing: Apply marine-grade sealant to protect the wiring from moisture and corrosion
When re-wiring a fiberglass boat, ensuring the electrical system is well-protected against the marine environment is crucial. One of the most critical steps in this process is waterproofing the wiring to prevent moisture and corrosion from damaging the system. Here's a detailed guide on how to apply marine-grade sealant to achieve this:
Step 1: Prepare the Wiring and Connections
Before applying any sealant, it's essential to ensure the wiring is in good condition and all connections are secure. Check for any exposed wires, damaged insulation, or loose connections. Clean the wiring and connections to remove any dirt or corrosion. This step is vital to ensure the sealant adheres properly and provides effective protection.
Step 2: Choose the Right Marine-Grade Sealant
Select a marine-grade sealant specifically designed for underwater applications. These sealants are formulated to withstand the harsh marine environment, including exposure to saltwater, UV radiation, and temperature fluctuations. Look for products that are flexible, durable, and resistant to aging. Common types of marine-grade sealants include epoxy-based, silicone-based, and polyurethane-based options.
Step 3: Apply the Sealant
- Prime the Surface: Start by cleaning the wiring and any exposed metal surfaces. Ensure the surface is dry and free of debris. You can use a mild detergent or isopropyl alcohol for cleaning.
- Apply a Thin Layer: Using a small brush or a syringe, apply a thin, even layer of sealant along the wiring. Be generous but careful not to overfill the spaces, as this can lead to bulging or warping.
- Squeeze and Smooth: Gently squeeze the sealant into the gaps and around the wiring to fill any voids. Use a small spatula or your finger (gloved) to smooth the surface, ensuring a seamless finish.
- Follow Manufacturer's Instructions: Always refer to the sealant manufacturer's guidelines for specific application rates and drying times. Some sealants may require multiple coats for optimal protection.
Step 4: Allow Adequate Drying Time
After applying the sealant, allow sufficient time for it to cure and harden. The drying time will vary depending on the product and environmental conditions. Typically, it can take several hours to a full day for the sealant to reach its maximum strength. Avoid any pressure or weight on the sealed area during this period to ensure proper curing.
Step 5: Inspect and Test
Once the sealant is fully cured, inspect the wiring for any signs of leakage or damage. Test the electrical connections to ensure they remain functional and secure. Regularly check the sealed areas for any signs of wear or damage, especially in areas prone to vibration or movement, as this can affect the sealant's integrity over time.
By following these steps, you can effectively waterproof the wiring in your fiberglass boat, ensuring a reliable and long-lasting electrical system. Remember, proper waterproofing is a critical aspect of boat maintenance, especially in marine environments where moisture and corrosion are constant threats.
Boat Title Change: Navigating the Process and Finding the Right Location
You may want to see also
Frequently asked questions
Rewiring a boat requires a set of specialized tools and safety gear. Essential items include a voltage tester, wire strippers, crimping tools, a multimeter, and a good supply of marine-grade wiring. Additionally, ensure you have safety equipment like gloves, safety goggles, and a respirator to protect yourself during the process.
Before starting the rewire, inspect the fiberglass structure for any damage or areas that might need reinforcement. Clean the surface to ensure good adhesion of the new wiring. You may need to fill any holes or cracks with a suitable marine-grade filler and sand it smooth. Proper preparation ensures the wiring is secure and long-lasting.
When routing wiring through the hull, plan a path that minimizes the risk of damage to the fiberglass. Use appropriate-sized holes and consider using a wire guide or a wire loom to keep the wiring organized. Ensure all connections are waterproof and secure, and avoid running wires along the bottom of the boat where they might be susceptible to damage from propeller wash.