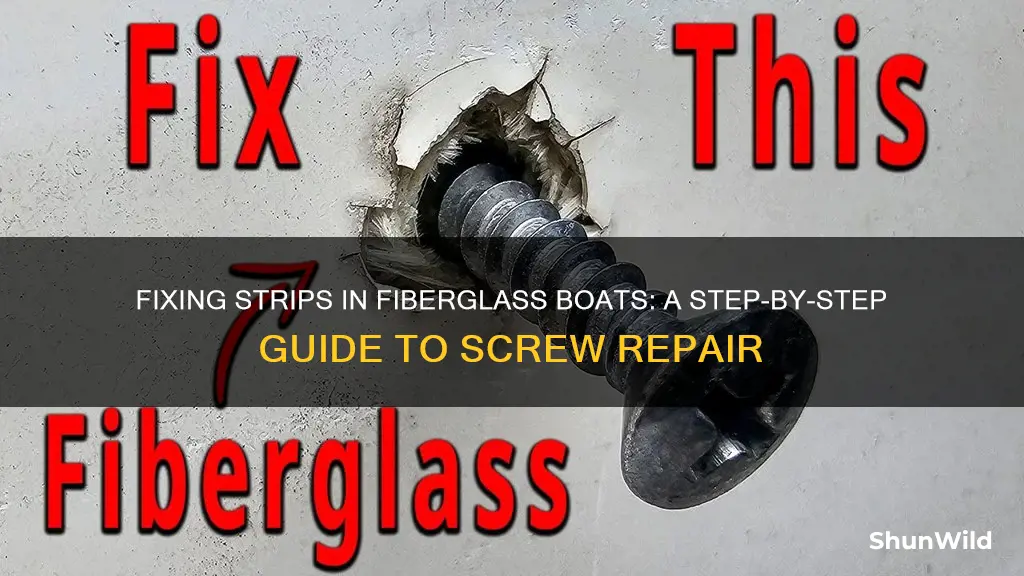
Repairing stripped screws in a fiberglass boat can be a challenging task, but with the right tools and techniques, it is possible to restore the boat's integrity. This guide will provide a step-by-step approach to fixing stripped screws, ensuring your boat remains safe and functional. From identifying the issue to choosing the appropriate repair method, you'll learn how to tackle this common problem effectively.
What You'll Learn
Identify the type of screw and damage
When dealing with stripped screws in a fiberglass boat, the first step is to accurately identify the type of screw and the extent of the damage. This is crucial as it will guide your repair approach. Screws in boats can vary widely, from small machine screws to larger hardware used for structural support. Identifying the specific type is essential because different screws may require unique repair methods. For instance, a stripped head machine screw might need a different strategy compared to a stripped screw in a critical structural component.
The damage to the screw can range from a minor strip near the head to a complete strip where the screw has been pulled out of the material. In some cases, the screw might still be partially visible, while in others, it may have been completely removed, leaving a deep hole in the fiberglass. Understanding the severity of the damage is key to choosing the right repair technique.
For a minor strip near the head, you might be able to use a screw extractor to remove the damaged screw and then insert a new one. This process involves using a specialized tool to grip the remaining part of the screw and pull it out. Once the old screw is removed, you can apply a small amount of epoxy or a specialized adhesive to the threads and insert a new screw, ensuring it is tight enough to hold.
If the screw has been completely stripped and removed, you'll need to fill the hole with a suitable material. Fiberglass resin, mixed with a hardener, can be used to create a strong, durable repair. After the resin has cured, you can sand it smooth and then re-install the screw. It's important to ensure that the new screw is tight enough to prevent further stripping.
In cases where the screw damage is extensive, or if you're unsure about the repair process, consulting a professional marine repair technician is highly recommended. They can provide expert advice and ensure the repair is done correctly, maintaining the structural integrity of your boat.
The Ultimate Guide to Inflatable Boat Care and Maintenance
You may want to see also
Use a screw extractor to remove the screw
When dealing with stripped screws in a fiberglass boat, using a screw extractor is a crucial step in the repair process. This method allows you to safely and effectively remove the damaged screw without causing further damage to the boat's surface. Here's a step-by-step guide on how to use a screw extractor for this task:
Start by gathering the necessary tools, including a screw extractor, which is a specialized tool designed for removing screws that have become stripped or damaged. These tools often come in various sizes and shapes to accommodate different screw head types. You'll also need a pair of pliers or a screw driver to grip the extractor. Ensure you have a steady hand and a well-lit workspace for better visibility.
Place the screw extractor onto the head of the stripped screw. The extractor should fit snugly over the screw's head, providing a secure grip. Apply gentle but firm pressure to the extractor while turning it counterclockwise. The goal is to loosen the screw without applying excessive force, as this might damage the surrounding fiberglass. If the screw is stubborn, you can use the pliers or screwdriver to provide additional leverage, but be cautious not to scratch the boat's surface.
As you turn the extractor, you should feel the screw backing out. If it doesn't come out immediately, don't force it. Instead, try to wiggle the extractor gently to break the screw free from the threads. Once the screw is loose, carefully remove it from the boat.
After removing the screw, inspect the damage. If the screw is completely stripped, you might need to consider other repair methods, such as using a screw insert or replacing the screw entirely. In some cases, you can re-thread the screw with a specialized thread-locking compound to ensure a secure hold. Always follow the manufacturer's instructions for any repair materials you use.
Remember, patience and precision are key when using a screw extractor. Take your time, and don't rush the process to avoid causing further damage to your fiberglass boat. With practice, you'll become more adept at removing stripped screws and restoring your boat to its original condition.
Understanding Boat Locks: A Mechanism Explained
You may want to see also
Apply a bonding agent to the threads
When dealing with stripped screws in a fiberglass boat, applying a bonding agent to the threads is a crucial step in the repair process. This technique helps to create a strong bond between the screw and the material, ensuring a secure hold and preventing further stripping. Here's a detailed guide on how to effectively apply the bonding agent:
Start by carefully examining the stripped screw and its surrounding area. Ensure that the screw is completely removed from the boat's structure, leaving only the threads exposed. It's important to work in a clean and dust-free environment to avoid any contamination. Gather the necessary materials, including the bonding agent, a small brush or applicator, and a fine-grit sandpaper.
The bonding agent, often a specialized epoxy-based compound, is designed to adhere to various materials, including fiberglass. Carefully read the manufacturer's instructions for application guidelines. Typically, you will need to mix the bonding agent with a hardener to create a viscous paste. Wear gloves and protective gear to avoid skin contact with the chemicals.
Using the brush or applicator, carefully apply a thin layer of the bonding agent to the threads of the screw. Ensure complete coverage, including the entire length of the threads and any exposed metal. Take your time with this step, as a thorough application is essential for a strong bond. Allow the bonding agent to sit for a few minutes, following the recommended curing time on the product's packaging.
Once the bonding agent has cured, inspect the application. If needed, gently sand the area with the fine-grit sandpaper to create a smooth surface. This step ensures that the screw head and threads are ready for rethreading or the installation of a new screw. Properly applied bonding agents can provide a reliable and long-lasting repair for stripped screws in fiberglass boats.
Repairing Polyester Boat Covers: A Comprehensive Guide
You may want to see also
Insert a new screw and tighten carefully
When dealing with stripped screws in a fiberglass boat, a common and effective solution is to insert new screws and tighten them carefully. This process requires precision and attention to detail to ensure a successful repair without causing further damage. Here's a step-by-step guide to help you through this task:
Start by gathering the necessary tools and materials. You'll need a set of screwdrivers, preferably a flathead and a Phillips head, in various sizes. Ensure you have the correct size that matches the screw you're replacing. Additionally, get a new screw that is compatible with the existing hardware. It's crucial to use a screw of the same material and dimensions as the original to maintain structural integrity.
Locate the stripped screw and assess the damage. Carefully remove any remaining threads of the old screw, being cautious not to strip the surrounding material further. If the screw is completely stripped, you might need to cut it out with a small saw or a specialized screw extraction tool. Once the old screw is removed, you should see a small hole or cavity where the screw was inserted.
Now, it's time to insert the new screw. Carefully align the threads of the new screw with the corresponding threads in the boat's material. Apply a small amount of thread locker to the threads of the new screw, especially if it's a critical load-bearing area. This step ensures that the screw doesn't come loose over time. Gently but firmly insert the screw, turning it by hand until it is fully seated.
The final step is to tighten the screw carefully. Use a screwdriver that matches the screw's head type (flathead or Phillips) and apply firm, even pressure. Avoid over-tightening, as this can damage the surrounding material. The goal is to secure the screw firmly without causing any cracks or permanent deformation. Once tightened, test the screw's strength by applying gentle pressure to ensure it holds securely.
Fixing Boat Engine Block: DIY Guide to Engine Maintenance
You may want to see also
Fill any remaining gaps with putty and sand
After you've carefully removed the damaged screw and any remaining threads, it's time to fill the gap and prepare for the repair. This step is crucial to ensure a strong and durable fix. Here's a detailed guide on how to proceed:
Start by cleaning the area around the screw hole. Use a fine-grit sandpaper to gently smooth out any rough edges and ensure the surface is as flat as possible. This preparation step is essential to create a seamless bond between the putty and the fiberglass. Take your time with this process to avoid any uneven surfaces that could affect the final result.
Once the area is clean and smooth, it's time to fill the gap. You can use a two-part epoxy putty for this purpose. Mix the putty according to the manufacturer's instructions, ensuring you have the right consistency for the job. Too soft a putty might not provide adequate support, while too hard a putty could be difficult to work with. Aim for a putty that is pliable yet firm.
Apply the putty to the prepared area, pressing it firmly into the screw hole and around the remaining threads. Use a putty knife or a similar tool to ensure the putty is evenly distributed and fills the entire gap. Take care not to apply too much pressure, as this could cause the putty to extrude or distort the fiberglass surface.
Allow the putty to cure according to the manufacturer's instructions. This process might take several hours or even overnight, depending on the product. Once cured, the putty will provide a strong, durable fill for the screw hole, ready for the final steps of your repair.
Remember, this process requires patience and attention to detail. Take your time to ensure a smooth and even fill, as this will contribute to a successful and long-lasting repair.
Zinc's Protection of Aluminum Boat Plates: Effective Solution?
You may want to see also
Frequently asked questions
Removing a stripped screw from a fiberglass boat can be challenging, but it's not impossible. You can try using a screw extractor or a specialized tool like a screw puller. If the screw is deeply embedded, you might need to carefully cut it out with a sharp blade or a specialized screw removal kit. It's important to be gentle to avoid further damage to the fiberglass.
Repairing a stripped screw hole in fiberglass typically involves filling the hole with a suitable epoxy putty or a fiberglass repair kit. Clean the area, apply the epoxy, and then fill the hole with a mixture of fiberglass cloth and resin. Once it's set, sand it down to a smooth finish and prime or paint the area to match the surrounding surface.
Yes, you can use alternative screws, but it's crucial to choose the right type. For fiberglass boats, consider using stainless steel or monel screws, which are corrosion-resistant and less likely to strip. Ensure the screw head is slightly smaller than the original to avoid further stripping. You might also need to adjust the screw length to fit the thickness of the fiberglass.
Absolutely! A temporary solution is to use a drop of epoxy or a small amount of super glue to secure the screw in place. This will provide some hold while you work on a more permanent repair. However, keep in mind that this is a short-term fix, and it's essential to address the issue properly to ensure a long-lasting repair.