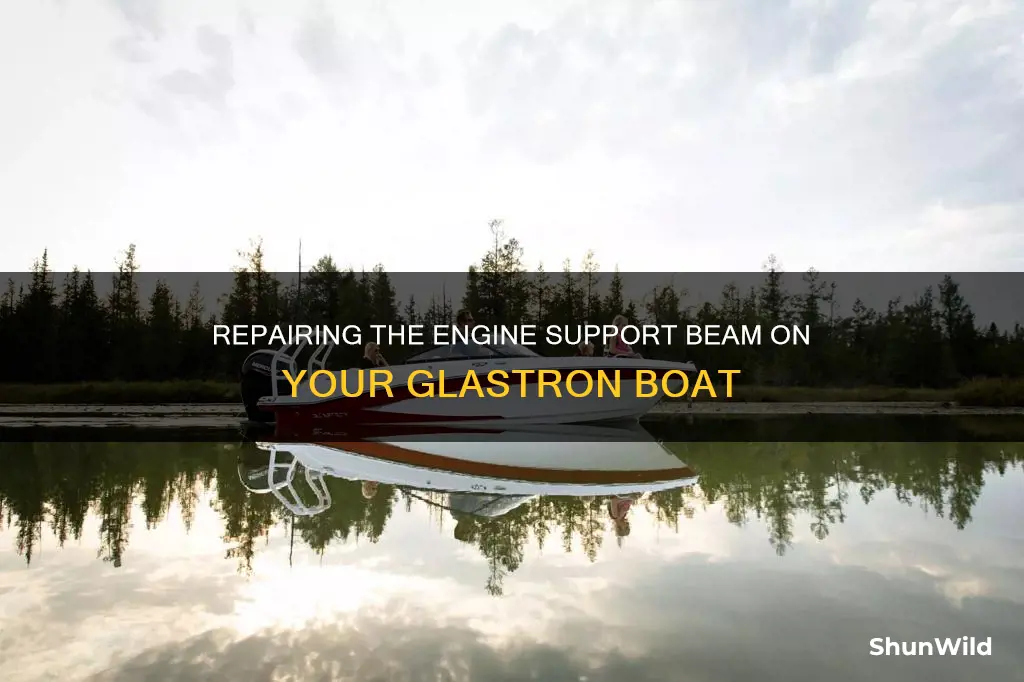
Repairing the engine support beam on a boat is a complex task that requires a good understanding of boat engineering and access to specialist tools and materials. The process involves removing the engine, assessing the damage to the support beam, repairing or replacing the beam, and reinstalling the engine. For owners of Glastron boats, which have a rich history of design, styling, performance and attention to detail, this process can be even more challenging due to the unique characteristics of these boats.
What You'll Learn
Removing the engine
Before beginning any repairs or modifications to your Glastron boat, it is important to carefully plan and gather the necessary tools and materials. In this case, you will be focusing on the process of removing the engine, which is a crucial step in gaining access to the engine support beam and making the required repairs. Removing an engine from a boat can be a challenging task, so ensure you have a clear understanding of the steps involved and take the necessary safety precautions.
The first step is to gather the required tools and materials, which may include basic hand tools such as wrenches, screwdrivers, and sockets, as well as more specialized tools like a engine hoist or jack. It is also important to have a clean and organized workspace to ensure that no tools or parts are misplaced during the engine removal process. Start by disconnecting the negative battery cable to prevent any accidental startups of the engine during the removal process.
Next, you will need to carefully disconnect and label all the hoses, wires, and cables connected to the engine. This includes fuel lines, water hoses, electrical wiring, and control cables. Labeling each connection will make it easier to reinstall the engine later and ensure that everything is properly reconnected. When disconnecting hoses, have a bucket and rags handy to catch any fluid that may spill.
Once all the connections have been disconnected, it's time to lift the engine out of the boat. This will require the use of an engine hoist or, in some cases, a strong jack and a secure lifting point on the engine. Work slowly and carefully to avoid damaging any parts of the boat or engine during this process. If using a jack, ensure it is stable and secure before lifting.
Finally, with the engine lifted and clear of the boat, you can now begin the process of repairing or replacing the engine support beam. It is important to note that this process may vary depending on the specific model of your Glastron boat and the type of engine installed. Always refer to your boat's manual and seek professional advice if you are unsure about any steps in the engine removal process.
The Boat Named 'The Etoile' and Its Famous Passenger
You may want to see also
Repairing the transom
Step 1: Measure and Support
Take measurements of all the parts around the transom, including the fiberglass thickness of the outside skin, the plywood thickness, the inside transom skin thickness, and the stringer location and thickness. Before removing any structural components, ensure that the hull is properly supported. Removing stringers or the transom without proper support can deform the hull. The best way to support the hull is to use a bunk trailer with additional blocks under the keel and transom.
Step 2: Gain Access to the Transom
To repair the transom, you need to gain access to it. Depending on the boat, you may need to cut the deck, top cap, or sidewalls. Remove the old plywood core and the inside fiberglass transom skin. You will need access to the entire transom, as well as at least 12 inches up the sides and bottom of the boat.
Step 3: Remove the Old Plywood Core
Completely remove the old plywood core using tools such as a reciprocating saw, grinder, hammer and chisel, or a flat pry bar. Be careful not to damage the outside fiberglass skin. Once the old plywood and putty are removed, make a template of the transom using cardboard, doorskin, or cheap plywood. This template will be used to cut the new transom core and to draw/cut the wide fiberglass pieces that will go between the new plywood and outer skin.
Step 4: Install the New Plywood Core
The new plywood core should be the same thickness as the original. If you are making changes to the design of the transom, you may need to adjust the thickness. Most powerboat transoms are made by laminating multiple layers of plywood. You can either bond the new core into the hull in one piece or laminate it one layer at a time. It is generally easier to laminate the core outside the boat and bond it into the hull once, but for very large transoms, this may not be possible due to weight and handling difficulties.
Step 5: Fill Gaps and Create Fillets
Before final glassing of the core, fill the gaps between the new core and the sides/bottom of the hull with putty. Then, use the same putty to create a fillet around the joint between the core and the hull. A fillet is a radius of putty that allows fiberglass to navigate around an angle. All inside corners of the transom should have a round fillet.
Step 6: Tab the Transom Core
Use 1708 Biaxial fiberglass tape to tab the transom core to the sides and bottom of the hull. This type of tape is stronger than traditional woven tape due to its fiber orientation. It is also easy to work with and compatible with epoxy. Use multiple layers of tape, depending on the specific boat. It is recommended to do the fillet and glass tabbing in one work session, a technique called "wet on wet," which results in better lamination quality and less cleanup.
Step 7: Bond the Plywood and Apply Fiberglass
Bond the plywood core in place using epoxy resin and appropriate fillers. Dry fit the first layer of plywood, applying pressure to hold it in place and conform to any curve in the transom. Drill holes through the plywood and fiberglass transom and bolt it in place. Mix epoxy and pre-coat the plywood surface that will be attached to the fiberglass transom. Apply filler to the epoxy and use a notched plastic squeegee to achieve a uniform layer. Press the first plywood layer into the epoxy and apply pressure. Use additional layers of epoxy and plywood as needed, using self-tapping screws to hold the layers in place while the epoxy cures.
Step 8: Finish with Fiberglass Reinforcement
Cover the plywood core with layers of fiberglass reinforcement and epoxy. The reinforcement can be cloth, biaxial cloth with mat, roving, or a combination of these materials. The goal is to build up a thickness equal to the original transom. Mix a little colloidal or foamed silica into the epoxy to prevent sagging. Use a grooved roller to remove any air bubbles from the fiberglass. Ensure that the fiberglass overlaps the inside of the hull around the edges of the transom, sealing the plywood core and forming a strong structural bond.
Keep Your Sperry Boat Shoes Afloat with These Tips
You may want to see also
Sanding and recoating
When sanding, it's important to use the appropriate grit sandpaper for the surface you're working on. Start with a coarser grit to remove any old paint, rust, or imperfections, then progress to finer grits to smooth out the surface and create a uniform finish. Take your time with this process, as it will impact the final result. Use a sanding block or a flat surface to ensure even pressure and avoid creating dips or grooves in the surface. Vacuum or wipe down the surface afterward to remove any dust or debris before moving on to recoating.
For recoating, select a paint that is suitable for the surface and the environment it will be exposed to. In the case of the Glastron boat, Interlux Epoxy Primekote and Perfection black topcoat were used, with the former filling gel coat imperfections and the latter providing a smooth and glossy finish. Practice using the paint on a small area or a test surface to get a feel for its application and to ensure that you're happy with the finish. Allow the paint to cure for a week to fully appreciate the final results.
When applying the paint, consider using a foam roller and a foam brush for tipping, as in the case of the deck painting. This combination can help achieve a smooth and drip-free finish, although it may not always live up to the highest standards for gloss. Take your time and work in a well-ventilated area to ensure the best results.
Remember to follow the manufacturer's instructions for the specific paint you are using, as well as any safety guidelines, to ensure a safe and successful recoating process. With attention to detail and a bit of practice, you can achieve a beautiful and long-lasting finish on your Glastron boat.
Repairing Holes in Plywood Boats: A Step-by-Step Guide
You may want to see also
Replacing the deck
The first step in replacing the deck of a Glastron boat is to carefully measure the thickness of the deck. This is an important step as cutting too deep can result in damage to the underlying support structures. Once the measurements have been taken, the old rotten deck can be cut out using a saber saw. This process typically takes about four hours for two workers on an 18-foot boat and requires the use of a crowbar, hammer, chisel, pick, and a drill in addition to the saber saw.
After the old deck has been removed, the next step is to cut new marine plywood to fit the opening. This step can be challenging, especially when matching radiuses around the bow. Once the new plywood has been cut to size, it is important to paint the underside with a thick coat of resin to protect it from moisture. Any exposed stringers or bulkheads should also be painted with resin to help prevent future rot.
The new deck can then be screwed into place, using fiberglass putty to bed it along the stringers and bulkheads. The seams are then filled with more putty and sanded down until the deck is flush and smooth. At least two layers of fiberglass should then be applied to the deck, following the manufacturer's instructions carefully.
Finally, a surface application product such as Rhino Lining, Tuffcoat Marine, or KiwiGrip can be used to finish the deck. These products offer a wide range of colors and surfaces and can be sprayed, brushed, or rolled onto the fiberglass.
Strategic Boat Navigation in Narrow Channels
You may want to see also
Installing a new engine
Step 1: Measurements and Compatibility
First, take measurements of the existing engine and its components, including the propeller shaft height, the direction of rotation of the propeller, and the propeller shaft and bearing. Ensure that the new engine's reverse clutch output and crankshaft are at the same height to avoid the engine "rising." Check the engine's manual to understand the maximum tilt when sailing and confirm that the engine can handle it. Pay attention to the direction of rotation, indicated with L or R, to ensure it matches the propeller.
Step 2: Sourcing the Engine
When sourcing a new engine, opt for a marine engine to ensure it can withstand the marine operating environment. Consider the power requirements and whether you need larger or smaller power output. Check the diameter of the exhaust manifold connection on the engine to ensure proper sizing.
Step 3: Connecting the Propeller
Determine how to connect the propeller to the reverse gear. If the brands are not interchangeable, you will need an adapter flange or a homokinetic drive. A thrust bearing with a homokinetic drive can help prevent vibration and save time during installation.
Step 4: Removing the Old Engine
Before removing the old engine, carefully disconnect all cables and components. You may need to consult a marine mechanic for this step, especially if you don't have experience with engine removal.
Step 5: Installing the New Engine
Hoist the new engine into place, ensuring it lines up with the saildrive. Drill holes in the bearers if needed.
Step 6: Connecting the Components
Connect the new engine to the calorifier, salt water system, and other necessary components. Install a new silencer/waterlock if needed.
Step 7: Testing the Engine
Once all connections are made, run the engine for the first time with a hose feeding the saltwater cooling system. Cast off and test the engine at various throttle settings to ensure it performs as expected.
Step 8: Final Adjustments
Make any necessary adjustments based on the engine's performance during the test run. Ensure that the wiring is correctly connected to charge the batteries, and consider installing a voltage-sensitive relay to manage battery charging.
Additional Tips:
- Consult a marine engineer or mechanic if you have any doubts or lack experience with engine installations.
- Take precise measurements and plan the installation carefully to avoid costly mistakes.
- Opt for marine-grade engines and components whenever possible to ensure compatibility and longevity.
- Always follow safety procedures when working with engines and boats.
The Art of Naming Your Boat: Nature's Hobby
You may want to see also