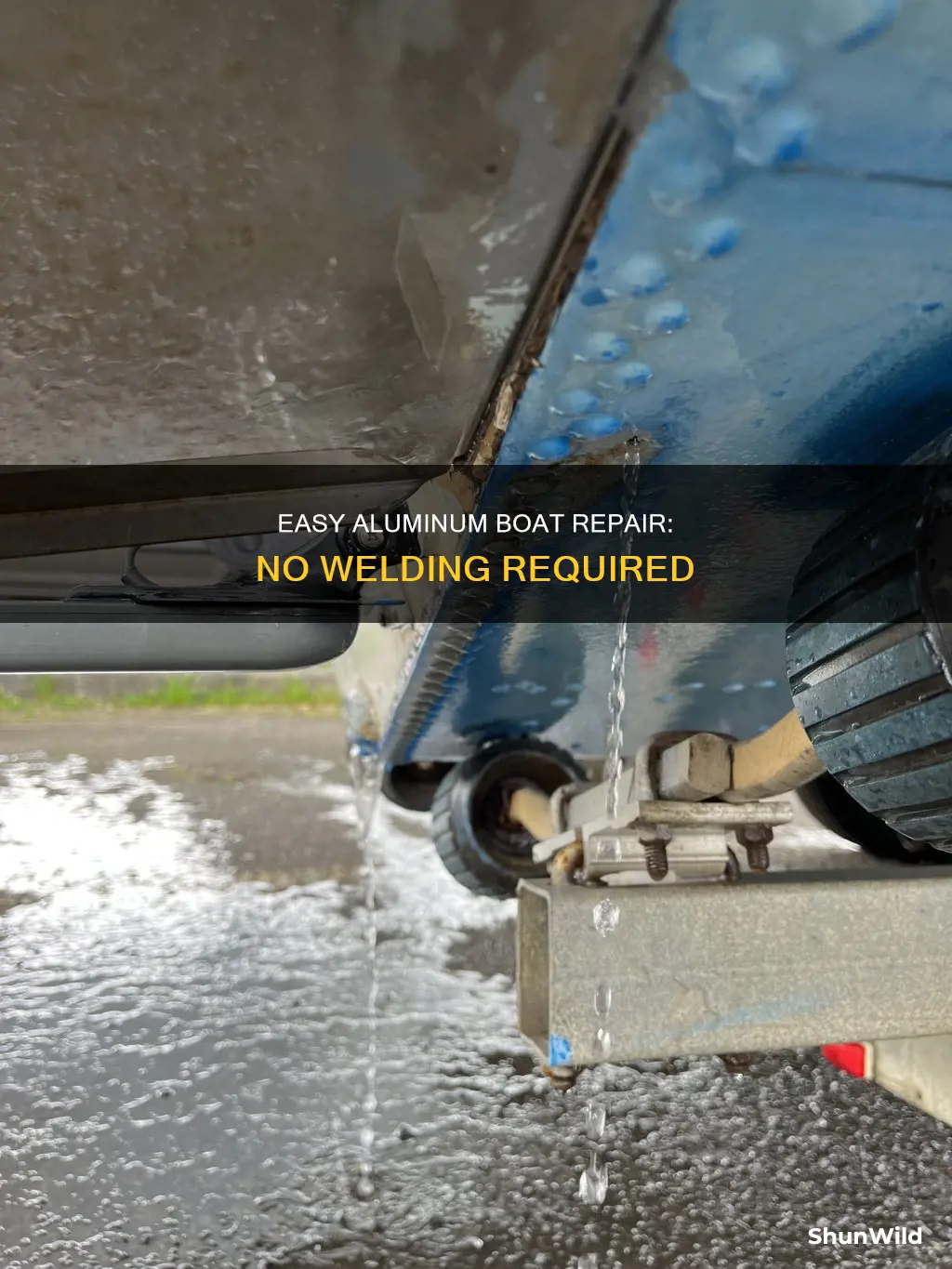
Aluminum boats are popular for their affordability, lightweight, and sturdiness. However, they do come with their own set of challenges. One of the most common issues with aluminum boats is corrosion, which can lead to leaks and costly repairs if not addressed promptly. While welding is considered the best method for permanent repairs, it is not always feasible or accessible for boat owners. In such cases, alternative repair methods can be explored, such as using epoxy or specialized repair kits that utilize brazing techniques. These methods offer temporary to long-term solutions, depending on the extent of the damage and the products used. This article will explore the various options available to repair an aluminum boat without welding, ensuring that your boat remains seaworthy and safe for your next adventure.
Characteristics | Values |
---|---|
Materials | Epoxy, JB Weld, Flex Paste, Super Alloy 5, Oxyacetylene torch, Aluminum brazing rod, Marine Tex, Acetone, Sandpaper, Marine epoxy, Putty knife, Fiberglass fiber, Fiberglass resin, Marine sealent, TIG welding |
Techniques | Brazing, Welding |
Boat Types | Aluminum boats, Aluminum pontoon boats, Airboats, Canoes, Rafts, Props, Cast aluminum outboard motors |
What You'll Learn
Use a product like Super Alloy 5
If you're looking to repair an aluminium boat without welding, a product like Super Alloy 5 can be a great solution. Super Alloy 5 is an aluminium welding and brazing rod that can be used for repairs on all types of aluminium boats. It's designed specifically for welding and brazing aluminium and offers a strong, permanent solution.
One of the key advantages of Super Alloy 5 is its ease of use, even for beginners. You don't need extensive knowledge or expensive welding equipment to use it effectively. It's a perfect colour match for aluminium, and the resulting bond is actually stronger than the parent metal. Its low working temperature of 600°F (315°C) prevents issues like sagging, warping, or wrinkling, and it flows easily to fill gaps.
To use Super Alloy 5 for aluminium boat repair, follow these steps:
- Clean the aluminium surface with an abrasive like a sanding disk or wire wheel. This ensures a proper bond.
- Heat the surrounding area to prevent the cold metal from absorbing heat from your work area.
- Use an oxyacetylene torch, oxy-MAPP gas, or oxy-propane to heat the parent metal to the working temperature of 600°F (315°C). Aluminium boats dissipate heat quickly, so preheating is crucial.
- Once the working temperature is reached, heat the tip of the Super Alloy 5 rod with the torch.
- Dip the heated rod into the Super Alloy 5 powder flux, which serves as a temperature guide and removes surface contaminants.
- Apply the flux to the repair area, and watch it transform from powder to liquid.
- Continue adding flux and the aluminium brazing rod until the hole or crack is completely filled and sealed.
- If the rod balls up, reheat the area until you reach the required temperature.
- After the repair is complete, allow it to cool, and then remove any residual flux with water and a wire brush.
Super Alloy 5 is a versatile product that can be used to repair various issues with aluminium boats, including sealing loose rivets, split seams, holes, cracks, dents, and corrosion. It's a reliable and long-lasting solution that will have your boat ready to get back into the water in no time.
Boat Repair Guide: BDO Essentials You Need to Know
You may want to see also
Seal with marine epoxy
When repairing an aluminium boat, it is important to consider the limitations of different repair methods. While welding is the best method for permanent repairs, it may not be an option for those who are not professional welders. In such cases, a metal-to-metal bond can be created using products like Super Alloy 5, which can be easily applied with an oxyacetylene torch. However, for minor and temporary repairs, epoxy is a common solution.
Epoxy is a rubbery substance that can be used to seal small holes in aluminium boats. While it is not a long-term solution and may fail unexpectedly, it can be a quick and inexpensive fix for leaks. To ensure the best results when using epoxy, proper surface preparation is key.
Firstly, the area to be repaired should be cleaned with acetone to remove any oil or grease. This step is important as even the oil from your fingers can affect the ability of the epoxy to seal the hole effectively. Next, the area should be roughened with sandpaper to create a better surface for the epoxy to adhere to. This process is known as abrading or keying and helps to create a stronger bond between the epoxy and the aluminium surface. Once the surface is prepared, the two-part epoxy putty can be mixed and applied to the hole, creating a watertight seal.
It is important to note that not all epoxies are created equal. Some epoxies may not fully cure, resulting in a rubbery patch that can be easily peeled off. This may be due to the age of the epoxy or the need for additional heat during the curing process. To avoid disappointment, it is recommended to use a marine-grade epoxy and follow the manufacturer's instructions carefully. Additionally, consider using a product like JB Water Weld, which has been known to result in a hard-as-rock finish.
Finding Leaks in Your Paddle Boat: A Step-by-Step Guide
You may want to see also
Use a metal-to-metal bond
Using a metal-to-metal bond is the best method for permanently repairing a hole or a split seam in an aluminium boat. This can be achieved through a process called brazing, which involves joining two or more aluminium pieces using a filler metal. The filler metal must be molten and free-flowing to fill the gaps between the aluminium pieces. Once the filler metal wets the aluminium joints, it is cooled to form a lasting bond.
Before beginning the brazing process, it is important to wear protective clothing, including flame-resistant clothes, shoes, and gloves. To prepare the aluminium surface for brazing, start by removing all dust from the surface and applying a degreasing solvent to clean the surface of any particles that may interfere with the bond. Continue the process by sanding, grinding, or sandblasting the joints or the area that needs repair. Having a rough surface will give the brazing filler material a better ability to form a stronger bond. Once you're done, support the pieces by clamping them together.
Next, pick your filler rod and dip it into an all-purpose flux suitable for aluminium and the surrounding temperature. Also, pour some flux between the metal pieces' joints or the area that needs repair. Take your torch and heat the joint area of the aluminium pieces until it's clear. Although hot metal appears bright orange, flux makes it clear. Simultaneously, melt the brazing metal in a metallic container and pour it into the joint or crack length. If the brazing metal starts to cool, you can move the torch to keep it molten until it fills the whole area.
After the filler has solidified, remove the flux by dipping the joint in cold water. Once it cools, you can brush the area with an emery cloth and apply a coat of rust-resistant topping to prevent corrosion. With this method, you can achieve a watertight, permanent joint that won't pop apart or peel up.
Painting Realistic Waterlines on Model Boats
You may want to see also
Repair with brazing rods
Brazing rods are a great option for repairing an aluminium boat without welding. Brazing is a technique that has many advantages over welding. Brazing equipment is inexpensive and portable, and no special skills are needed—simply follow the instructions. Repairs can be made quickly and without disassembling the boat, and the resulting bond is a permanent solution for many aluminium boat problems.
Brazing rods are an ideal solution for filling holes, dents, voids, pits, and other damage to aluminium boats. To use brazing rods, you will need an oxygen-fuel torch system. Oxyacetylene, oxy-MAPP gas, or oxy-propane is required for all aluminium boat repairs, as aluminium dissipates heat quickly. You will also need brazing rods and a jar of powdered flux. The flux not only cleans the base metal and removes impurities but also acts as a temperature guide. When the flux transforms from powder to liquid, it indicates that the aluminium has reached 600°F, and it's time to apply the brazing rod.
Before you begin, ensure the area to be repaired is thoroughly cleaned and prepared. Once the area is ready, heat the surrounding area so that the cold metal doesn't leach heat from your work area. Then, use your torch to heat the tip of the brazing rod, dip it into the flux, and melt the flux onto the weld area. Start depositing the rod and add more flux as needed. The flux will assist with the bonding process as you apply the rod.
Brazing rods are a great option for those who are not professional welders or who don't have access to welding equipment. With brazing rods, you can achieve a strong, permanent repair on your aluminium boat without the need for extensive knowledge or expensive equipment.
Exploring Alcatraz: Boat Options and More
You may want to see also
Sand, clean and use epoxy putty
To repair an aluminium boat without welding, you can use epoxy putty. This method is suitable for small holes in an aluminium boat.
First, you need to prepare the area. Hammer the area flat to close the hole as much as possible. Then, sand or grind the area and clean it with an acetone solvent. This will ensure that the putty will adhere to the surface. It is important to remove any oil or grease from the area, including any that may have transferred from your fingers.
Next, prepare the epoxy putty by mixing equal parts of Part A and Part B. Roll the putty between your fingers until the colour is uniform.
Now, you can apply the putty to the hole. Press and smooth the putty into the hole and the surrounding area, from both sides if possible. If the hole is a crack, drill a small hole at each end to prevent the crack from spreading.
Finally, allow the epoxy putty to dry and harden. This usually takes 24 hours, but check the manufacturer's instructions for the specific product you are using.
While epoxy putty can be a good solution for minor, temporary repairs, it is not a long-term solution for aluminium boats. It may eventually fail and is not as reliable as welding.
Best Boat Docking Options in California's Bay Area
You may want to see also
Frequently asked questions
You can use an epoxy putty such as JB Weld, or a product like Super Alloy 5, which is a permanent solution with a bonding strength of 30,000 psi.
First, you need to hammer the area flat, then sand or grind the area and clean with acetone. Next, mix the two-part epoxy putty until it is a uniform colour, then press and smooth it into the hole and surrounding area.
You will need an oxyacetylene torch, Super Alloy 5 powder flux, and an aluminum brazing rod. Heat the area surrounding the hole, then use the torch to heat the tip of the rod. Dip the rod into the flux and melt it onto the weld area. Start depositing the rod and add more flux as needed.
Super Alloy 5 is a stronger, permanent solution that does not require extensive knowledge or expensive equipment. It is also portable, so you can carry out repairs on the go.