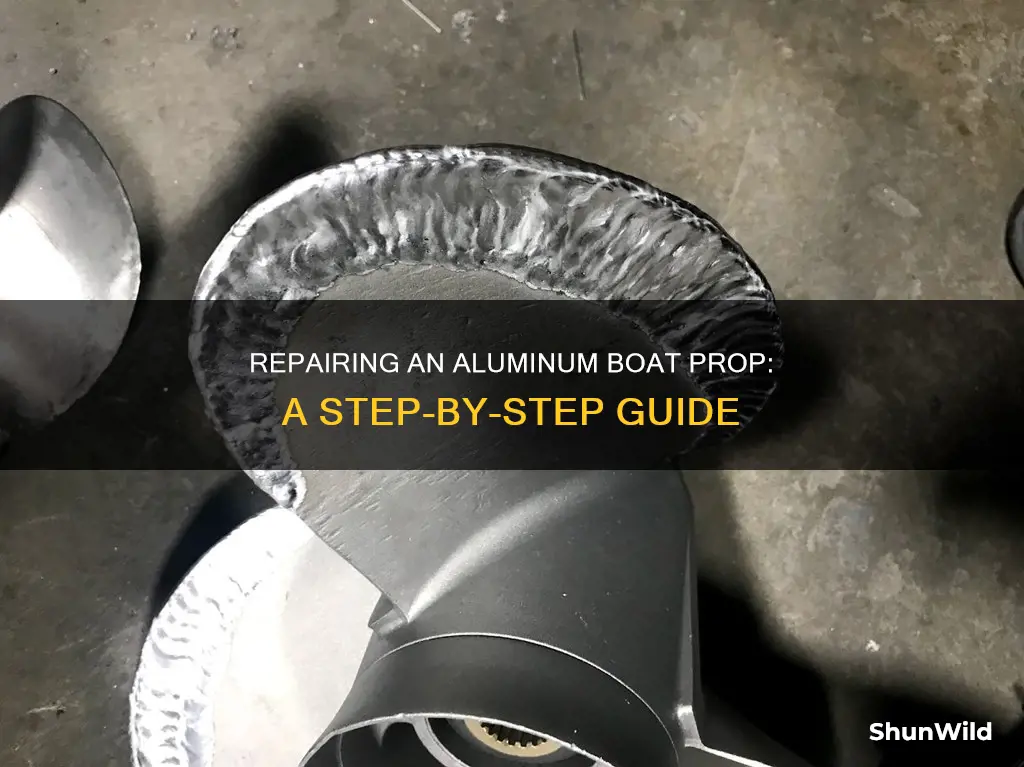
Repairing an aluminium boat propeller can be a tricky endeavour. While some suggest that it is cheaper to buy a new propeller than to repair an old one, others have had success with welding and epoxy. The process of repairing a propeller involves removing it from the boat, welding it, shaping it with a grinder, sanding it, priming it, and finally, painting it. The cost of repairing an aluminium prop can vary depending on the extent of the damage, with some repairs costing as little as $48, while others can cost upwards of $200. It is important to consider the balance of the propeller after repairing, as improper balancing can lead to vibrations and damage to the boat. Overall, while repairing an aluminium boat prop can be a challenging task, it is possible to achieve satisfactory results with the right tools and techniques.
Repairing an Aluminum Boat Propeller
Characteristics | Values |
---|---|
Cost | $35-45 for repairs; $140-$170 for a new one |
Repair method | Welding, epoxy, or tuning |
Time | 7-10 business days |
Tools/Materials | Aluminum welding wire, marine primer, paint, grinder, sandpaper, tack cloth |
What You'll Learn
Removing the propeller
To repair your aluminium boat propeller, you'll first need to remove it from the boat. Here's a step-by-step guide on how to do this safely and efficiently:
Before beginning any work on your boat, it's important to ensure you have a clear and safe work area. Make sure the boat is securely docked or lifted out of the water, and all necessary tools and safety equipment are within easy reach.
Now, let's get started:
- Place a suitable container under the propeller shaft to catch any falling grease or water. This will help keep the work area clean and prevent any mess from spreading.
- Loosen the propeller nut by turning it counterclockwise with a suitable wrench or socket. You may need to apply some penetrating oil to the nut beforehand to make it easier to turn. Be cautious and avoid applying excessive force, as the nut is usually quite tight.
- Once the nut is loose, continue turning it by hand until you can remove it completely. Set the nut and any washers aside in a safe place, as you will need to reinstall them later.
- Gently pull the propeller shaft towards the back of the boat. This will disengage the propeller from the shaft. If the shaft is difficult to pull, you may need to use a gentle tapping motion with a rubber mallet to loosen it. Be careful not to damage the shaft or the propeller during this process.
- With the propeller disengaged, carefully remove it from the shaft. Set it aside in a safe place, making sure to protect the blades from any potential damage.
- Clean the propeller shaft and inspect it for any signs of damage or corrosion. If the shaft is damaged, it may need to be repaired or replaced before reinstalling the propeller.
Now that you have successfully removed the propeller, you can begin the repair process. Remember to wear appropriate safety gear, including gloves and eye protection, during all stages of the repair work.
Maverick Crab Boat: Who Owns This Fishing Vessel?
You may want to see also
Welding the propeller
Welding an aluminium boat propeller is a highly skilled job. It requires a steady hand and a good eye for detail, as the welder must be able to imagine the original shape and curvature of the propeller. The process involves using a TIG welding machine to build up the edge of the propeller, bead by bead, until it is back to its original shape.
Firstly, place the propeller on a flat, sturdy surface with the damaged side facing up. It is important to wear the proper safety equipment, including a welding hood and gloves, before beginning the welding process. Set your TIG machine to basic aluminium settings and ensure that the welding wire is being correctly fed into the machine.
When welding, start on the left of the damage if you are right-handed, or vice versa if you are left-handed. Work in a zigzag motion, moving the weld puddle back and forth to build up the filler. Once you have finished welding, allow the weld to cool completely before using a grinder to shape the weld and blend it with the shape of the propeller. Sand the propeller with 120-grit sandpaper until it is dull, then wipe it down with a tack cloth to remove any dust or fingerprints.
Next, spray three coats of aluminium oxide primer on the propeller, waiting 30 minutes between each coat and three hours for the primer to dry completely. Finally, apply three to five coats of paint, waiting at least 15 minutes between each coat and leaving the propeller untouched for a full day to allow the paint to dry.
It is important to note that welding an aluminium boat propeller requires practice and should not be attempted on an expensive boat prop without prior experience. It is recommended to start by practising on new 1/8" aluminium strips and then progress to scrap aluminium parts from a junkyard before attempting to weld a propeller.
The Ownership Mystery of Donna Kay Boat
You may want to see also
Sanding the propeller
Before sanding, it is important to protect yourself by wearing the appropriate safety gear, including gloves, eye protection, and a respirator. Once you are geared up, you can begin sanding the propeller with 120-grit sandpaper. Apply firm, even pressure and work your way across the entire propeller until it is dull and free of any shine. This process will likely create a lot of dust, so take breaks as needed and use a tack cloth to wipe down the propeller and remove any dust particles or fingerprints.
It is important to be thorough during the sanding process, as this will impact the final finish of your propeller. Take your time and ensure that you sand all the surfaces, paying extra attention to the welded areas. Once you are satisfied with the smoothness of the propeller, use a clean cloth to remove any remaining dust.
After sanding, you may choose to repeat the process with a finer grit sandpaper, such as 220-grit, to further refine the finish. This step is optional but can help create an even smoother base for the primer and paint to adhere to. Once you have finished sanding, it is important to clean the propeller with a suitable solvent to remove any oils or residue. This will ensure that the paint will adhere properly and create a long-lasting finish.
Finally, before applying the primer, inspect the propeller for any imperfections or blemishes. Run your hand over the surface to feel for any areas that may require additional sanding. It is better to spend a little extra time on the sanding process than to rush it and be left with an uneven or imperfect finish.
Alabama Boat Fight: What Caused the Conflict?
You may want to see also
Painting the propeller
Preparation
Before painting, ensure that the propeller is clean and free of any debris, wax or oils. Use a strong cleaner or degreaser, such as Simple Green or Castrol degreaser, and scrub the propeller with a pad. Wash the propeller with a 50/50 solution of vinegar and water or acetone to ensure the paint will adhere well. Dry the propeller thoroughly.
Priming
Wearing clean rubber gloves, apply a primer to the propeller. It is important to choose a primer suitable for aluminium, such as aluminium etching paint, zinc phosphate primer or zinc chromate primer. Ensure the primer is compatible with your chosen paint. Warm the primer in the sun or a warm place, along with the propeller, and place the propeller on a broomstick, suspending it horizontally. Spray the primer onto the propeller, starting and finishing with the edges to ensure they get two coats. Apply two coats of primer, allowing each coat to dry for at least 30 minutes. Leave the primer to dry completely for a few hours or overnight.
Painting
Again, warm the paint and propeller in the sun or a warm place. Choose a paint suitable for aluminium propellers, such as Trilux Primer and Lower Unit/Prop paint. Place the propeller back on the broomstick and spray the paint onto the propeller, applying three to five coats. Allow each coat to dry for at least 15 minutes and leave the propeller for a full day to dry completely before handling.
Tips
- It is important not to touch the propeller with your bare hands after cleaning and before painting, as this can affect the adhesion of the paint.
- The sun can help the paint and primer to dry and bake on effectively, so it is beneficial to keep the propeller in direct sunlight during the process if possible.
- For best results, use a light coating of paint, followed by another coat while the first is still tacky, and apply a possible third coat.
The Perfect Flat Floor: Boat Edition
You may want to see also
Propeller repair shops
- Services Offered: Propeller repair shops specialize in repairing and refurbishing damaged propellers. They can handle various types of damage, from minor dings and chips to more extensive repairs like welding and rebalancing. They may also offer additional services such as skeg repair, prop customization, and propeller sales.
- Experience and Expertise: Reputable propeller repair shops, such as Soderbloom's Prop Repair, have decades of experience in the industry. Their proven results and expertise ensure that your aluminium propeller can be restored to its former glory. These shops understand the unique characteristics of aluminium props and can provide durable and reliable repairs.
- Process and Turnaround Time: The repair process typically involves assessing the damage, performing the necessary repairs, and refinishing the propeller. Some shops may offer quick turnaround times, with repairs completed within a few days. During the repair process, the propeller may undergo welding, painting, and balancing to ensure it functions optimally.
- Cost-Effectiveness: Repairing a damaged propeller is often significantly more cost-effective than purchasing a new one. Propeller repairs can cost 50% to 75% less than the price of a new propeller. Shops may provide quotes and estimates before commencing the repair work, ensuring transparency in pricing.
- Shipping Options: Some propeller repair shops offer convenient shipping services. For example, Soderbloom's Prop Repair provides customers with a UPS label to ship their damaged propeller for repair, making the process more accessible for those not located nearby. This option simplifies the logistics of getting your propeller to the shop and back to you.
- Propeller Sales and Customization: In addition to repairs, many propeller shops also offer propeller sales and reconditioned propellers. They provide a range of propeller types and brands to choose from. Some shops even provide prop customization services, allowing you to modify your propeller to meet specific needs, such as improving hole shot, speed, or addressing cavitation issues.
When choosing a propeller repair shop, it is essential to consider their reputation, experience, and the range of services they offer. Reading customer testimonials and reviews can also provide valuable insights into the quality of their work and customer satisfaction.
Repairing Vinyl Boat Cushions: Fixing Tears and Rips
You may want to see also
Frequently asked questions
Repairing an aluminum boat prop is often not worth it as it is cheaper to buy a new one. However, if you want to repair it, you can weld it yourself or get it repaired at a local shop.
The cost of repairing an aluminum boat prop can vary depending on the damage, size of the prop, and whether you go through a third party or directly to a repair shop. The cost can range from $48 to $200.
The repair time can vary depending on the severity of the damage and the availability of the repair shop. On average, it takes about 7-10 business days to repair a propeller.
The process involves removing the propeller, welding or filling in the damaged area, sanding, painting, and allowing adequate time for the repairs to dry and harden.
No, not all aluminum boat props are repairable. If half or more of the blade is missing, it is often beyond repair. In such cases, it is recommended to replace the propeller entirely.