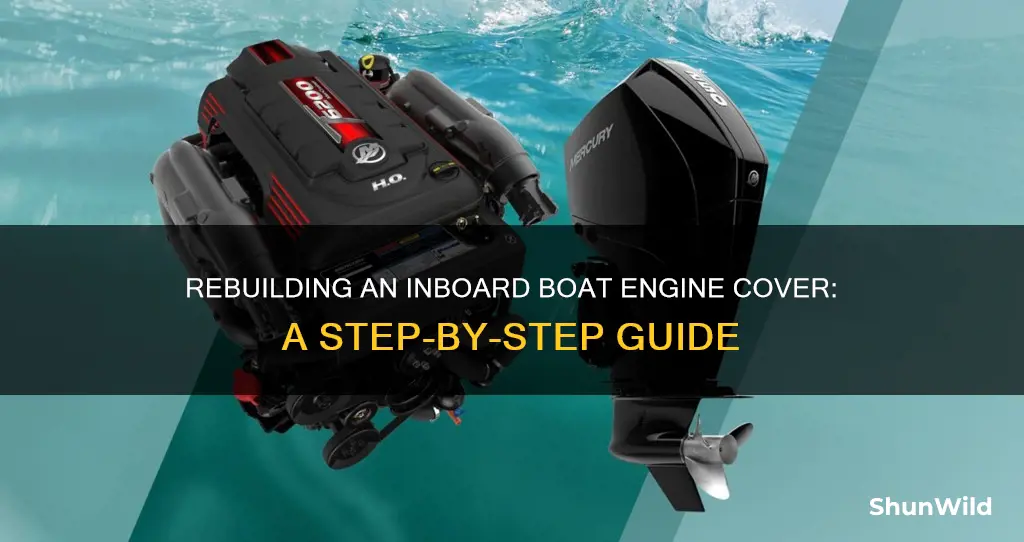
Rebuilding an inboard boat engine is a complex process that requires careful consideration and planning. It involves disassembling the engine, inspecting and repairing individual components, and reassembling the engine to restore it to its original specifications. This process can be undertaken by skilled boat owners or qualified mechanics, and it offers a cost-effective alternative to replacing the engine entirely. This paragraph aims to provide an introduction to the topic of rebuilding an inboard boat engine, covering the key aspects and considerations for those seeking to undertake this challenging but rewarding project.
How to Rebuild an Inboard Boat Engine Cover
Characteristics | Values |
---|---|
Materials | Plywood, fibreglass, resin, stainless steel, foam insulation, cloth, gelcoat, roller |
Tools | Belt sander, medium grit sandpaper, cordless drill, circular saw or table saw |
Steps | Measure, cut, sand, reinforce, attach hinges, drill, bolt, ventilate, finish |
What You'll Learn
Measuring and cutting plywood to the correct specifications
To rebuild an inboard boat engine cover, you will need to measure and cut plywood to the correct specifications. Here is a step-by-step guide to help you through the process:
Step 1: Measure the Opening
First, you need to determine the size of the opening above the engine. Measure both the width and length of the opening. If you are making a flush engine cover, deduct 5/8 inch from each measurement to allow for the fiberglass. For a raised cover, add 1 inch to each measurement to ensure the bottom edges of the cover rest on the deck.
Step 2: Choose the Right Plywood
Select a plywood sheet that matches the thickness specified in your boat engine cover plans. For example, you may need a 1/2-inch or 3/4-inch marine-grade plywood sheet.
Step 3: Prepare the Plywood for Cutting
Examine the plywood sheet for any imperfections or irregularities. Identify two adjacent edges that are straight and form a 90-degree angle. Start your measurements from this corner, as it will serve as your reference point.
Step 4: Mark Your Cut Lines
Using your measurements, mark the cut lines on the plywood sheet. Measure from the reference corner to the cut line at both ends of the sheet. Use a square to connect the marks and create a straight cut line.
Step 5: Set Up a Straightedge
Determine the distance between the saw blade and the straightedge of your saw. You can do this by measuring the distance or using the saw to nick the cut line and marking the edge of the saw base. This step ensures that your cut will be straight and accurate.
Step 6: Put on Safety Gear
Before cutting, don protective gear, including a breath mask, earplugs, and safety goggles. This will safeguard you from wood dust, loud noises, and flying debris.
Step 7: Cut the Plywood
Using a circular saw or a table saw, carefully cut the plywood along the marked cut lines. Ensure that your blade is set to a depth that is slightly greater than the thickness of the plywood. This will ensure a clean cut.
Step 8: Sand and Finish the Edges
Once the plywood is cut to size, you may need to sand the edges to smooth out any roughness or splinters. You can use a belt sander with medium grit sandpaper for this step.
By following these steps, you will be able to measure and cut plywood accurately for your inboard boat engine cover project, ensuring that it fits perfectly over your engine.
Fixing Leaks in an Aluminum Boat: A Step-by-Step Guide
You may want to see also
Applying layers of fibreglass to the plywood
When applying fibreglass to plywood, you must follow a few important steps to ensure the best results. Firstly, safety is paramount. Wear safety glasses, latex or vinyl gloves, and a respirator to protect yourself from the fibreglass and resin. Coveralls can also be worn to protect your skin and clothing. Ensure you are working in a well-ventilated area.
The next step is surface preparation. Use a solvent like Acetone to wipe down the plywood surface, removing any dust or grease. This step is crucial for strong adhesion. Cut the fibreglass cloth slightly larger than the plywood surface. You can join several pieces together if necessary.
Now, prepare the resin. Measure out the resin and use a catalyst quantity chart to determine how much catalyst to add. Mix thoroughly with a stir stick for several minutes. For larger quantities, use a power mixer and a drill.
Spread a thin layer of resin onto the plywood with a brush or roller. Place the fibreglass cloth onto the resin-coated plywood and allow the resin to soak into the cloth. Add more resin if needed and use a roller to remove any trapped air bubbles. Ensure the cloth is completely saturated with resin.
For the next layer, apply resin to the fibreglass, then add another layer of fibreglass cloth. Ensure the seams do not line up with the previous layer. Apply resin to the final layer of fibreglass and allow the entire project to harden overnight.
Finally, trim off any excess fibreglass from the edges of the plywood and sand the surface as needed.
Lewes Fire Boat: What Happened to Delaware's Watercraft?
You may want to see also
Sanding the fibreglass cover
Assessing the Surface:
Before you begin sanding, it is important to thoroughly clean the fibreglass surface and allow it to dry completely. Carefully inspect the cover for any flaws, gouges, or uneven areas. Determine the level of smoothness required for your desired finish.
Selecting Sandpaper:
For sanding fibreglass, aluminium oxide and silicon carbide sandpapers are the best options. Commonly used grit sizes include 80, 100, and 120. Start with a coarser grit (80 or 100) to remove heavy oxidation or surface defects, and then progress to finer grits (120 and 220) to smooth the surface for better paint adhesion.
Sanding Technique:
When sanding, always use straight, even strokes in a consistent direction. Apply moderate pressure and let the sandpaper do the work. Avoid applying too much pressure, as this can cause uneven scratches that will require additional sanding. Frequently switch the direction of your strokes to ensure even sanding.
If using power tools, such as a belt sander, use variable speed settings to control the rate of abrasion. Move slowly over the surface to avoid removing too much material. For hard-to-reach areas, such as around hardware, logos, or stripes, switch to hand sanding.
Process Checkpoints:
Frequently stop to wipe clean the sanded areas and inspect them for smoothness. Ensure that all imperfections are removed and that there are no uneven spots that might be visible under the finish. Once the entire surface meets your smoothness standards, use a tack cloth to remove all dust before moving on to the next step, such as applying a polishing compound or finish.
Additional Tips:
- Wet sanding is a technique where you lubricate the sanding process with water to achieve an ultra-smooth finish. It helps reduce scratches and swirl marks and allows for better control.
- When using power tools, consider using a common heavy-duty sander/polisher with a rectangular piece of fibreglass or Lexan™ mounted on a standard round foam backup pad to prevent gouging the surface.
- Always wear a dust mask and safety glasses when sanding fibreglass to protect yourself from airborne fibreglass dust.
Mending Boat Cushion Seams: Quick Fix Guide
You may want to see also
Positioning and drilling holes for stainless steel butt hinges
To position and drill holes for stainless steel butt hinges when rebuilding an inboard boat engine cover, follow these steps:
Firstly, you will need to purchase a pair of stainless steel butt hinges and a cordless drill with a screw tip attachment. You will also need stainless steel bolts with flat washers and nuts. Ensure you are wearing safety gear, including a dust mask and safety glasses, before you begin.
Now, you can position the hinges. Place a pair of stainless steel butt hinges along one edge of the cover, ensuring that the hinge pins are aligned at the outside edge of the cover. Each hinge should be positioned 2 inches from the respective end of the cover.
Once the hinges are in the correct position, you can begin drilling. Drill pilot holes for the stainless steel bolts at each of the pre-drilled holes in the hinge butts. The size of the pre-drilled holes in the hinge butts will determine the size of the pilot holes and stainless steel bolts.
After drilling the pilot holes, insert the stainless steel bolts into the pre-drilled holes in the hinge butts and through the pilot holes in the cover. Secure the bolts with flat washers and nuts on the underside of the cover. Tighten the nuts with a socket and ratchet.
By following these steps, you will have accurately positioned and drilled holes for stainless steel butt hinges when rebuilding an inboard boat engine cover.
Valor's Owner: Unveiling the Mystery of Below Deck's Vessel
You may want to see also
Finishing the cover with non-slip deck surfacing
To finish the cover with non-slip deck surfacing, you can use a variety of materials and textures. Here are some options:
Non-Slip Marine Deck Coverings
Non-slip deck coverings are elastic and anti-slip. They are simple to apply and adapt well to the shape of the hull. The PVC material is resistant to saltwater, UV rays, and temperature changes. It also provides good insulation and reduces glare. This type of covering is available in different colours and patterns, such as grey and white stripes, brown stripes, or dark stripes.
3M Safety-Walk 700
This grip tape offers extremely good traction and is easy to apply as it is peel-and-stick. However, it may start to peel up at the corners after a couple of years, requiring replacement. It is available in a variety of widths and lengths.
Diamond Non-Skid
This pattern is commonly used by fishermen as it is easy to clean and provides good traction when dry. It loses some grip when wet as it tends to retain some moisture.
SeaDek
SeaDek is a faux teak decking material made from EVA foam. It provides good traction, especially when tested across the grain. It is also lightweight and resistant to staining. However, the caulking channels can collect dirt and require proper cleaning.
Teak
Untreated teak offers excellent traction, especially when tested across the grain and when wet. However, it tends to take longer to dry than other materials and is heavy and expensive.
Boat Carpet
Boat carpet retains its non-skid qualities when wet, but it is slow to dry, which can lead to wet feet and an increased chance of slipping.
When choosing a non-slip surface for your inboard boat engine cover, consider factors such as traction, water retention, ease of application and maintenance, weight, cost, and aesthetics.
Three Rivers Boat Show: What Went Wrong?
You may want to see also
Frequently asked questions
Rebuilding an engine can save you money versus replacing it with a new one. It also means you're using the same engine that the boat was designed for, and you probably already have a stockpile of spares for your old engine.
It's not a new engine, so if there are fundamental flaws, they may still show up. The success of a rebuild depends on the quality of the workmanship by the rebuilder. You also won't have any of the advantages of newer engines.
You can make a flush or raised inboard engine cover using fibreglass and marine hardware. You will also need a belt sander with medium-grit sandpaper, stainless steel butt hinges, a cordless drill with a screw tip attachment, and stainless steel bolts with flat washers and nuts.