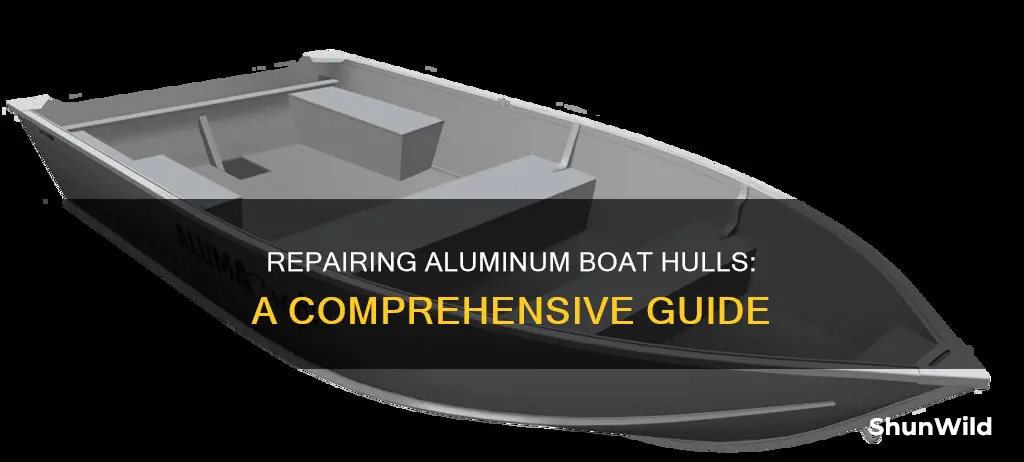
Repairing an aluminium boat hull can be a challenging task, requiring specific tools and expertise. The process involves identifying the source of the leak, assessing the extent of the damage, and determining the appropriate repair method. While some minor repairs can be done at home, more extensive damage may require the expertise of a qualified welder or metalworker. In this case, it is essential to carefully select a repair specialist with experience in working with aluminium boats to ensure a successful and safe repair.
Characteristics | Values |
---|---|
Repair Difficulty | Repairing an aluminum boat hull is difficult and requires proper training and equipment. |
Repair Technique | Welding, brazing, or using epoxy to fill gaps or holes. |
Required Tools/Materials | Hammer, soft-headed hammer, dollies, hydraulic jack, sealant/caulk, epoxy, acetone, sandpaper, propane catalytic heater, putty knife, etc. |
Cost | Depending on the extent of the damage, repairs can range from $150 to $1000 or more. |
Common Issues | Leaking seams or rivets, tears, cracks, dents, pinhole leaks, etc. |
Precautions | Aluminum is easily distorted and can become brittle if overheated. Proper heating and hammering techniques are critical. |
What You'll Learn
Repairing a leaking seam or rivet
Before you can repair a leaking seam or rivet, you must first identify the exact location of the leaks. To do this, you can either beach your boat and gradually slide it into the water, marking the leaking rivets as you move along, or get the boat off the ground, fill it to the waterline with water, and mark the leaks. Once you have identified the leaks, mark them with a waterproof marker.
Using epoxy to repair leaks
One way to repair leaking seams or rivets is to use a strong epoxy designed for use with metals, such as WEST SYSTEM G/flex®. To use this method, you will need to clean the area around the leaks and use a wire brush to abrade the surface. Then, mix the G/flex resin and hardener in a measuring pot and extract the mixture into a syringe. Heat the area around the leaks to 80-100°C using a propane torch or heat gun to force out moisture and thin out the epoxy. Fill the seams and rivets with the epoxy while the aluminium is still warm, using the heat gun to maintain the necessary heat and direct the epoxy into the affected areas. Keep applying heat to the treated area until the epoxy has gelled, then continue to apply heat at a lower setting until it has fully cured, or allow it to cure slowly at room temperature.
Rebucking (tightening) a rivet
To rebuck a rivet, you will need a helper or long arms. One person holds a buck (an anvil-like hunk of steel) tightly against the flat side of the rivet, while the other hammers the crimped end. You can use a ball-peen hammer to retighten the rivet head, and a sledgehammer as the buck. Be careful not to hammer too hard, as old aluminium rivets can split or break under heavy force. If the rivet does break, you will need to source a solid aluminium replacement. To remove the old rivet, file or grind off one head, or drill it out, being careful not to enlarge the hole. When seated, the new rivet's unpeened (headless) end should protrude by about 2/3 of its diameter. Drill a hole just larger than the rivet's diameter in a hardwood dowel or steel bar, then put the rivet in place and slip the dowel over the unpeened end. A solid hammer blow will cinch the rivet in place.
Other methods
As a temporary solution until you can install a new rivet, you can use a small stainless steel machine screw with an acorn nut, along with flexible marine epoxy or sealant, to help the repair last longer. Pop rivets are another option, but standard ones are useless below the waterline as they have a hole through them. If you can only access one side of the hull, you can try a closed-end pop rivet, but these can be difficult to source.
Bass Pro Boat Financing: Is It a Good Deal?
You may want to see also
Straightening a dented hull
If the dent is inward, your assistant will need to hold a hand anvil against the outside of the dent while you hammer lightly from the inside, tapping and straightening the bent aluminum until it's close to its original shape. This process may need to be repeated several times to get the hull back to its original profile. Aluminum becomes work-hardened when bent, so be careful not to hammer too hard or the molecules will distort further, and the metal will become brittle and crack easily.
If the dent cannot be removed with light hammering, you will need to apply heat to the area to relax the molecules. Use a propane torch to heat the dented area, and then use a soft-headed hammer to gently tap the metal back into shape.
Once the hull is straight, you can prepare the area for sealing. If there is a hole or crack, use epoxy to fix a strip of scrap metal to the outside of the puncture to create a stable place for the brazen rod material to settle. If there is a crack, use a drill and cone bit to cut the crack into a V-shaped channel, with the small end of the V being the crack itself. For a simple hole, grind away just enough for the brazen rod material to bind to. Sand the area with 220-grit sandpaper.
Now you are ready to apply the brazen rod. Heat up the area around the puncture and use a wire brush to rough up the surface. Hold the heat on the puncture and apply the tip of the HTS-2000 brazing rod to the sides of the puncture, allowing it to melt and flow into the gap. Make sure the material overlaps itself and fills the gap entirely. As it cools, use a wire brush to scrape away slag and residue.
Finally, use a flat file to remove any excess brazen rod material that extends past the aluminum panel, being careful not to dig into the brazen weld. Your hull is now straightened and sealed!
Best Places to Dock Your Boat in San Diego Bay
You may want to see also
Filling a hole with marine epoxy
Filling a hole in an aluminium boat hull with marine epoxy is a straightforward process, but it requires careful preparation and the right tools. Here is a step-by-step guide:
Step 1: Prepare the Area
Before applying epoxy, it is essential to prepare the area around the hole. Clean the surrounding surface and use a tool like a dremel to grind the edges of the hole at an angle. This process helps the epoxy adhere better to the surface. It is also recommended to clean both sides of the hull with acetone to ensure a grease-free surface.
Step 2: Apply Tape and Epoxy
As a precautionary measure, place a piece of duct tape or masking tape on one side of the hole. This will prevent the epoxy from sagging or dripping through the hole. On the other side of the hole, apply a generous amount of marine epoxy, ensuring it fills the hole completely. It is recommended to use a quick-setting epoxy to avoid sagging on vertical surfaces.
Step 3: Allow the Epoxy to Set
Once the epoxy is applied, let it set and cure. The curing time will vary depending on the type of epoxy used, but it typically takes several hours or even overnight. Refer to the manufacturer's instructions for the specific epoxy you are using.
Step 4: Remove Tape and Apply Additional Epoxy
After the epoxy has set, carefully remove the tape from the other side of the hole. Inspect the epoxy application and, if needed, apply an additional coat of epoxy to both sides of the hole. This ensures a strong and uniform bond.
Step 5: Sand and Smooth the Repaired Area
Once the epoxy has fully cured, you may need to sand the edges of the repaired area to remove any roughness or unevenness. Use fine-grit sandpaper and gently sand the area until it is smooth and level with the surrounding hull. This step helps create a seamless repair and improves the overall finish.
Step 6: Apply a Fairing Compound (Optional)
If desired, you can apply a fairing compound, such as a mixture of G/flex epoxy and a low-density filler, to the repaired area. This will enhance the smoothness of the hull, improve hydrodynamics, and provide additional scuff resistance. Sand the fairing compound once it has cured for a flawless finish.
Step 7: Final Touches and Painting
With the hole filled and smoothed, your aluminium boat hull is now structurally sound and watertight. If desired, you can apply a coat of paint that matches the colour of your boat to the repaired area for a seamless finish. Ensure that you use a paint suitable for aluminium boats and follow the manufacturer's instructions for application.
Repairing Rocker Switches: Bass Boat Maintenance Guide
You may want to see also
Welding a tear
Preparation
First, assess the damage. Take measurements of the tear, including its length and width. The size and location of the tear will impact the repair process and cost. It is important to determine whether the tear is on a flat surface or along the curved hull. If the tear is along the curved hull, a patch with gentle angles and round ends should be used to avoid sharp 90-degree stress points that could lead to future cracks.
Next, clean the aluminium surface thoroughly to remove any dirt, grease, or oxide layers. Use a stainless steel brush specifically designed for aluminium, and ensure you clean just before welding to prevent contamination.
Welding Process
When welding aluminium, it is crucial to control the heat input due to its high thermal conductivity. Use short welds and allow the metal to cool between passes to avoid warping or burn-through. Preheating the aluminium slightly can help manage heat flow and create more consistent welds.
Use a MIG or TIG welder, which is specifically designed for aluminium welding, to ensure solid and clean welds. Maintain a consistent travel speed to distribute heat evenly along the weld. Practice steady hand movements and keep a close watch on the weld pool.
Use a push technique instead of a pull technique when welding. This helps to keep the shielding gas in the weld pool and reduces the risk of contamination.
Filler Material
Choose a filler rod or wire that matches the base material to ensure compatibility and strength. For most marine-grade aluminium, 5356 and 4043 filler materials are commonly used. Check the specifications of your aluminium and select the appropriate filler to complement it.
Welding Environment
Weld in a clean, controlled environment to prevent contaminants from compromising the weld. If welding outdoors, consider using a portable welding shelter to protect the area from wind, dust, and moisture. This helps to maintain a stable welding environment and improves the overall quality of the welds.
Post-Weld
After welding, you may need to sand down the metal for a neat finish. Ensure that the weld is watertight by testing the boat before use.
It is important to note that welding aluminium boats can be challenging, and it is always recommended to seek the help of a qualified welder or a specialised welding service if you are unsure or uncomfortable with the process.
Applying Aluma Hawk Boat Paint: A Step-by-Step Guide
You may want to see also
Repairing pitted or pin-holed surfaces
Before applying any products, clean the surfaces with acetone and roughen the areas with sandpaper. If you're using a marine epoxy, combine the two ingredients according to the instructions (usually a 1:5 ratio) and use a putty knife to apply it. Make sure to spread the epoxy over and into the holes, and leave it to dry for 24 hours. If the epoxy doesn't set, you may need to apply heat with a propane catalytic heater.
Another option for repairing pitted or pin-holed surfaces is to use a product like JB Water Weld. This putty-like epoxy is easy to apply and shape with your fingers, and it sets hard. After applying the epoxy, you can add another layer of protection with Flex Paste, a rubbery finish that can be applied with a small putty knife.
Boat Seats: Do They Include Bases?
You may want to see also
Frequently asked questions
Put the boat in water and observe carefully. You could also put water inside the boat and see where it escapes from.
You will need to use additional rivets in combination with a sealant product.
You can use a high build epoxy primer such as Tuff Stuff, Hawk Epoxy, or G/Flex 650 Epoxy.
Have an assistant hold a hand anvil against the outside of the dented area while you hammer lightly at the dent from the inside, tapping and straightening the bent aluminum until it’s close to its original shape.
Figure out its approximate dimensions and use epoxy to fix some scrap metal to the outside of the puncture. This will create a stable place for the brazen rod material to settle.