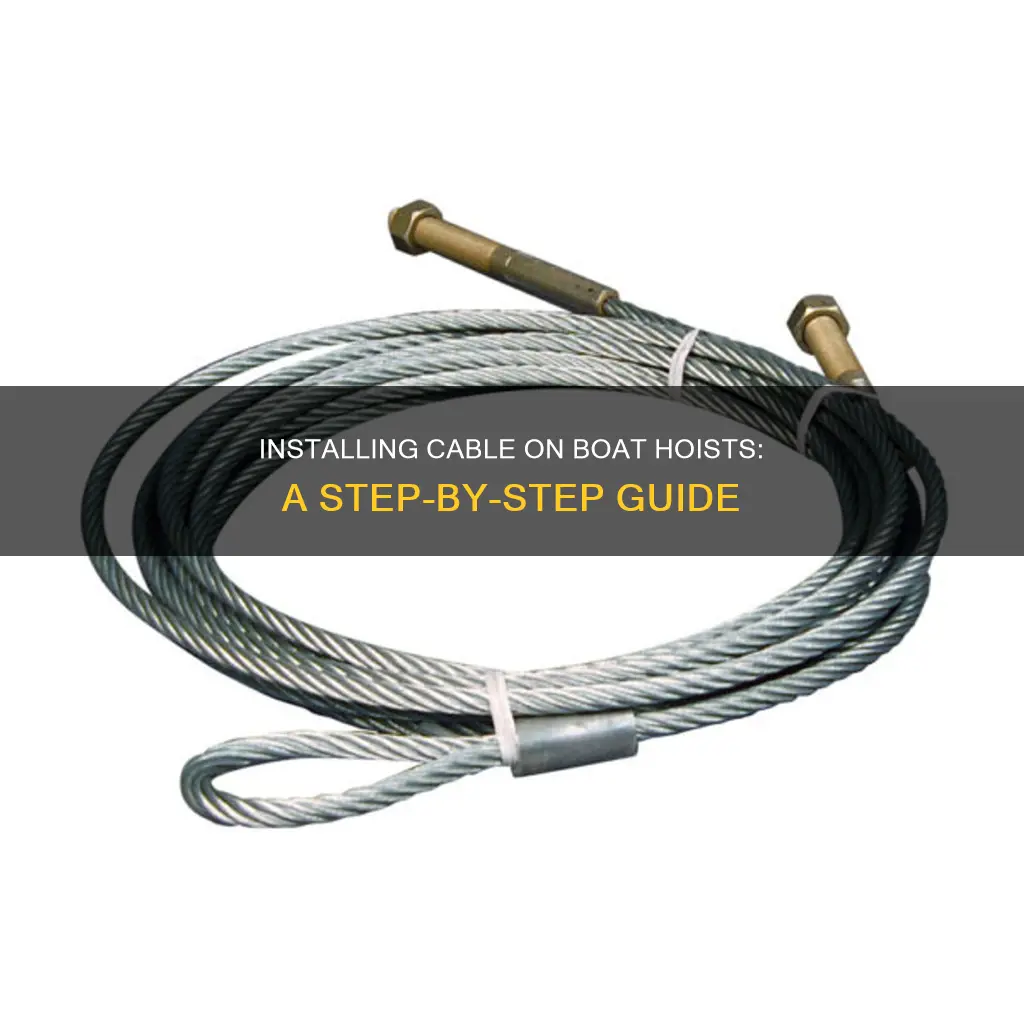
Boat lift cables are an essential component of a boat lift, allowing the boat to be raised and lowered. They are also called hoist wires or cables and connect the lifting mechanism to the cradles that pick up the boat. Boat lift cables will always wear down over time and will eventually need to be replaced.
There are many types of boat lift cables, with some made from galvanized steel cable and others from 300 series stainless steel cable. The type of cable, how well it is maintained, and how often it is used will determine how long it lasts.
It is important to consult a professional and licensed boat lift technician before buying or installing a new boat lift cable. If you are curious about how to install a boat lift cable yourself, this will depend on the type of boat lift you own.
What You'll Learn
Types of Boat Lift Cables
Boat lift cables are essential components in a boat lift, allowing boats or watercraft to be raised and lowered. They are typically made from either stainless or galvanized steel, with different constructions like 7x19 or 6x36, affecting their flexibility and strength. Here is a detailed overview of the types of boat lift cables:
Galvanized Steel Cable
Galvanized steel cable is more flexible and softer than stainless steel cable. This makes it more resistant to work hardening and abrasion damage. However, the galvanized coating does not provide adequate protection against cable corrosion, making it unsuitable for saltwater or long-term submersion in freshwater. Galvanized steel cable is more affordable and an excellent option for freshwater boat lifts.
Stainless Steel Cable
Stainless steel cable offers superior corrosion resistance compared to galvanized cable, making it ideal for saltwater boat lifts. It is blended with chromium oxide, which regenerates its protective properties when exposed to oxygen. However, stainless steel is more prone to work hardening and abrasion damage. It is also more expensive, as it can lift less weight compared to galvanized cable of a similar size.
Cable Construction
Boat lift cables also vary in construction, with different diameters and strand configurations. Cables with larger diameters can carry more weight, with typical diameters being 5/16″ and 3/8″. The strand configuration can be 7 x 19 or 6 x 36, with the latter resulting in a more flexible cable due to its thinner strands.
Maintenance and Replacement
Boat lift cables require proper maintenance and lubrication to prolong their lifespan. It is important to routinely inspect the cables for signs of damage, such as rust spots, kinks, or broken strands. Additionally, cables should be cleaned and lubricated according to the manufacturer's instructions. Despite maintenance, boat lift cables will eventually need to be replaced due to wear and tear. The replacement interval depends on the type of cable, maintenance, and usage frequency.
Boat Trailer Fenders: Necessary or Not?
You may want to see also
How to Install Boat Lift Cables
Boat lift cables are crucial components that enable you to raise and lower your boat. Over time, these cables will wear down and need to be replaced. The process of installing new boat lift cables depends on the type of boat lift you own. Here is a step-by-step guide on how to install replacement boat lift cables:
- Secure the Cradle Beams: Use nylon strapping to tie the cradle beams to the top beam channel. Some installers may use chains or other strapping, or they may use a barge to support the cradle beams and bunks.
- Remove Old Cables: With the cradle beams securely held, cut and remove the worn-out lift cables.
- Install New Cables: Start by identifying the cable winder. Insert the fused end of the new cable into the larger hole and then through the smaller hole. Pull the fused end through until the copper stop bottoms out.
- Route the Cables: Follow the cable routing diagram provided by the manufacturer to ensure proper routing of the new cables.
- Repeat for Remaining Cables: On a typical 4-post lift, you will have four sets of cables, two for each top beam, and one for each winder. Elevator lifts usually have two sets of cables, one for each powerhead.
- Remove Support Strapping: Once all new cables are installed, remove the support strapping and gently lower the cradles into the water.
- Raise the Lift: As you raise the lift, watch the new cables to ensure they are winding properly on the winders. Continue raising until the cradles are out of the water.
- Adjust Cable Length: Use a wedge lock to adjust the cable length so that the cradle beams and bunks are level. Loosen the internal wedge to feed the cable through, then pull down on the cables to lock the wedge and secure them in place.
- Test the Lift: Run the lift up and down a few times to ensure everything is functioning correctly. Do not load the boat until you are satisfied that the lift is operating properly.
Important Tips:
- Safety First: Always work in a safe manner and only use the appropriate equipment and tools.
- Follow Instructions: Carefully follow the manufacturer's instructions, including diagrams and drawings, for a smooth installation.
- Maintenance: Regularly inspect and maintain your boat lift cables to prolong their lifespan. Look for signs of damage, such as rust, kinks, or broken strands. Use a penetrating lubricant to protect the cable strands from abrasion and corrosion.
- Replacement Interval: It is recommended to replace lift cables every two years or after 200 up-and-down cycles, whichever comes first.
SpongeBob's Unique Boat Invention: A Bizarre Creation
You may want to see also
Maintenance Practices after Installation of New Boat Lift Cable
Boat lift cables are important components of a boat lift. They are responsible for connecting the lifting mechanism to the cradles that pick up the boat. Over time, the cables will wear down and need to be replaced. To ensure the safety and longevity of your boat lift, it is crucial to perform regular maintenance on the cables. Here are some maintenance practices to follow after installing new boat lift cables:
- Routine Inspections: Regularly inspect the cables for any signs of damage or wear and tear. Look for rust spots, kinks, broken strands, fraying, or any other abnormalities. Pay close attention to the areas near the winch, as this is a common area for cable damage.
- Proper Lubrication: Use a penetrating chain and cable spray lubricant to protect the internal strands of the cable from abrasion and the outer strands from corrosion. Do not use grease, as it can trap moisture and accelerate deterioration. Lubricate pulleys and other moving parts to ensure smooth operation and prevent seizing.
- Rinsing and Cleaning: Rinse your boat lift with fresh water after each use to remove salt deposits and prevent corrosion. This is especially important if your boat is exposed to saltwater, as saltwater can accelerate rust and corrosion on metal parts.
- Tension Adjustment: Ensure that all cables have equal tension and are aligned properly on the pulleys. Adjust the cable tension as needed to maintain proper balance.
- Prompt Replacement: If you notice any signs of wear and tear, don't delay in replacing the cables. It is recommended to replace stainless steel cables every two years, even if they appear to be in good condition.
- Professional Consultation: If you are unsure about the condition of your cables or need assistance with maintenance, consult a professional boat lift technician for guidance and advice.
By following these maintenance practices, you can extend the lifespan of your boat lift cables, ensure the safety of your boat, and avoid costly repairs or accidents. Remember that proper maintenance is essential to keep your boat lift functioning optimally and protect your investment.
The Mystery of Pinwheel Tuna Boat Ownership Unveiled
You may want to see also
Common Problems During the Installation of a Boat Lift Cable
Boat lift cables are crucial components of a boat lift, and improper installation or inadequate maintenance can lead to catastrophic failure. Here are some common problems and issues that may arise during the installation process:
- Improper Winding: One of the most frequent issues is improper winding of the cables on the winch drum, resulting in "backlash," where the cables become tangled or snagged. This can cause uneven wear and damage to the strands. It is important to ensure that the cables wind neatly and tightly within the grooves of the winder.
- Cable Tension: Boatlift cables require proper tension to function correctly. Without sufficient tension, cables can unravel on the drum, leading to a "backlash" similar to that on a fishing reel. When re-tightening loose cables, they may become flat, snagged, or tangled, resulting in uneven wear.
- Cable Corrosion: Corrosion is a significant problem, especially for galvanized cables. Over time, the protective galvanizing coating can wear off, leading to corrosion and potential cable failure. Corrosion may not always be visible, and it can occur internally within the cable as well.
- Boat Positioning: Improper positioning of the boat on the lift can overload the cable system and cause damage. It is important to distribute the weight evenly by positioning the stern about 12"-18" from the lift rack.
- Fraying and Damage: Regular visual inspections are necessary to check for fraying, kinks, broken strands, or other signs of damage. Frayed cables can compromise the strength and integrity of the lift, increasing the risk of failure.
- Unusual Noises: Pay attention to any unusual sounds, such as grinding or scraping, during the operation of the lift. These sounds may indicate internal damage or wear to the cables.
- Performance Issues: A worn-out cable can lead to sluggish operation or uneven lifting, affecting the stability and safety of the boat lift.
To avoid these common problems, it is important to follow the manufacturer's instructions, perform regular inspections, and address any signs of wear or damage promptly. Proper maintenance and timely replacement of boat lift cables are crucial to ensure the safety and functionality of your boat lift.
Odysseus' Vessel: Unraveling the Hero's Nautical Legend
You may want to see also
When to Replace Boat Lift Cables
Boat lift cables are essential components that bear the bulk of the strain of keeping your boat out of the water. They will wear down over time and will eventually need to be replaced. The timing of this replacement depends on several factors, including the type of cable, the type of lift, maintenance, and frequency of use. Here are some key points to consider when deciding if it's time to replace your boat lift cables:
- Visual Inspection: Keep an eye out for any signs of damage or wear on the cables. Look for rust spots, kinks, broken strands, or any other abnormalities. If you notice any of these issues, it's best to replace the cables as soon as possible.
- Maintenance: Proper maintenance can help extend the life of your cables. Regularly clean and lubricate the cables according to the manufacturer's instructions. Use penetrating oil instead of grease, as grease can trap moisture and accelerate deterioration.
- Replacement Intervals: Even with proper maintenance, cables will eventually need to be replaced. Your boat lift manufacturer will likely recommend specific replacement intervals, which you should follow even if the cables appear to be in good condition. For galvanized cables, it is generally recommended to replace them every two years or after 200 cycles, whichever comes first. Stainless steel cables can last up to twice as long.
- Type of Cable: The type of cable you have will impact its longevity. Galvanized cables are more prone to wear and corrosion, especially when used in saltwater or submerged for long periods in freshwater. Stainless steel cables offer better corrosion resistance and can last longer.
- Frequency of Use: The more often you use your lift, the faster the cables will wear down. If you use your lift frequently, inspect the cables regularly and be prepared to replace them more often.
- Winding and Alignment: Ensure that the cables are winding properly on the winders and are aligned correctly on the pulleys. Improper winding or alignment can cause premature wear and increase the risk of failure.
- Safety: Remember that faulty or worn-out cables can lead to catastrophic failure, potentially damaging your vessel. When in doubt, it's always better to replace the cables sooner rather than later to avoid the risk of dropping your boat or causing personal injury.
Paddle Boat Registration in Oregon: What's the Law?
You may want to see also
Frequently asked questions
The cables on your boat lift will need to be replaced when you notice signs of damage or wear such as rust, kinks, broken strands, or any other irregularities. It is important to routinely inspect the cables for any of these issues. Additionally, the cables should be replaced every two years or after 200 up-and-down cycles, whichever comes first.
Boat lift cables can be made from galvanized steel or stainless steel, each offering varying levels of corrosion resistance and strength. Galvanized steel cables are more flexible and affordable, while stainless steel cables offer superior corrosion resistance, particularly in saltwater environments.
Safety should be the top priority when installing a new boat lift cable. Ensure you are using the right equipment and tools, and carefully follow the relevant instructions and drawings for your specific boat lift model. Always review your work to ensure a complete and secure installation.