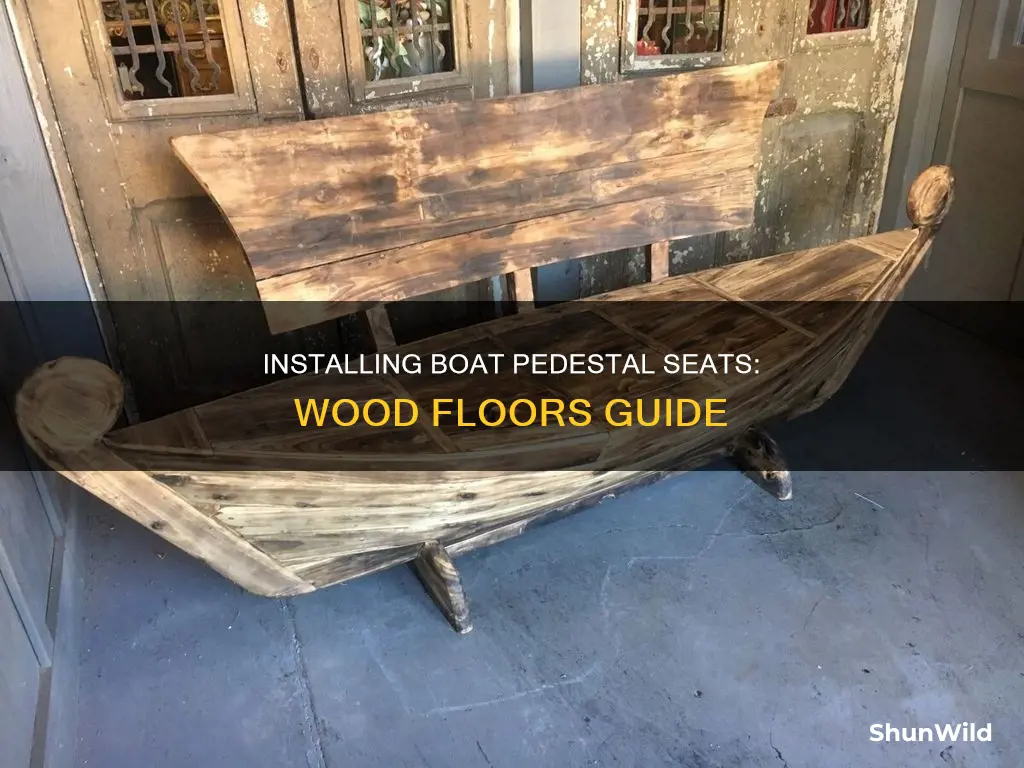
Boat seat pedestals can be a tricky installation, and there are several methods to consider. The first step is to decide where to position the seat base, ensuring it is not too far back or too close to the wheel or tiller. The next step is to determine the type and solidity of the decking under the seat, as well as any structures under the deck. Some boats have thin decking, which may be cored or not. It is important to check for supporting structures such as beams or ridges under the deck. If there is no access to under the deck, one can install an inspection port to get a better view. Once the location is decided, it is important to use the right size and type of fasteners for the decking material. For example, bolts are often better than screws because washers and nuts can be added. Screws can weaken the decking over time and work loose. It is also important not to place the end of a screw or bolt too close to the hull.
Characteristics | Values |
---|---|
Installation method | Bolts, screws, or adhesive |
Materials | Plywood, fiberglass, washers, nuts, bolts, backing washers, backing plates, machine screws, marine caulk, adhesive/sealant, epoxy, wood filler, stainless steel screws, T-nuts, blind rivets, threaded inserts, pop rivets, contact cement, hole saw, wire, anti-seize compound, inspection port, inspection mirror, fasteners |
Considerations | Positioning of the seat, type and solidity of the decking, structures under the deck, access to underneath the deck, safety, leakage, corrosion, weight, stability |
What You'll Learn
- Using bolts and nuts instead of screws to secure the seat pedestal to the floor
- Using a nut plate to spread the force over a large area
- Using aluminium or plywood as a backing plate
- Using marine caulk or adhesive/sealant to seal the screw holes
- Drilling pilot holes to prevent the base from getting jostled out of position
Using bolts and nuts instead of screws to secure the seat pedestal to the floor
When installing boat pedestal seats on wooden floors, it is crucial to ensure a secure and robust attachment to withstand the stress and forces exerted while boating. While screws are commonly used, they may not always provide adequate strength and durability, especially if the floor is thin or weak. Here are some detailed instructions and considerations for using bolts and nuts instead of screws to secure the seat pedestal to the floor:
Choosing the Right Hardware
Select appropriate bolts, nuts, and washers for your application. Stainless steel machine screws, flat-head screws, washers, and locknuts are commonly recommended for their strength and corrosion resistance. The size of the bolts and nuts should correspond to the dimensions of your seat pedestal and floor thickness.
Inspecting the Floor
Before beginning the installation, carefully inspect the wooden floor to determine its thickness and condition. Ensure there are no underlying structures or obstructions beneath the floor that may interfere with your installation. This step is crucial for planning the placement of bolts and nuts without compromising the integrity of the floor.
Reinforcing the Floor
If the wooden floor is thin or weak, consider reinforcing it by attaching a backing plate or an additional layer of plywood. This will distribute the load over a larger area and provide a more robust base for your bolts. You can attach this reinforcement using epoxy or by bolting it through the floor, ensuring a smooth finish on the deck.
Drilling and Attaching the Pedestal
Once you have prepared the floor, position the seat pedestal where you want it. Drill holes through the mounting holes of the base. If you are using a backing plate, ensure it is securely attached beneath the floor, aligning with the mounting holes. Insert bolts from the top, through the seat pedestal and floor, and secure them with washers and nuts underneath. Tighten the nuts using a wrench to ensure a firm connection.
Sealing and Finishing
After securing the seat pedestal, apply a marine-grade caulk or adhesive/sealant to the screw holes to prevent water ingress and corrosion. Follow the manufacturer's instructions for curing time before using the boat. This will help maintain the integrity of your installation and protect the wooden floor.
Using bolts and nuts instead of screws provides a more robust and reliable attachment for your boat pedestal seats. It ensures that the seats can withstand the forces exerted during boating and reduces the likelihood of the seats working loose over time. Remember to choose appropriate hardware, inspect and reinforce the floor if necessary, and always seal your work for a long-lasting installation.
Columbus' Historic Voyage: The Ships that Sailed
You may want to see also
Using a nut plate to spread the force over a large area
If you have a thinner floor, using a nut plate to spread the force over a large area is a good idea. Instead of using 1/16th aluminum, use 1/2 or 5/8ths aluminum. Then, use a tap and drill set to make a pair of holding holes for the nut plate. Secure the nut plate under the floor with screws. Place the pedestal base over the nut plates and drill and tap the first hole for the pedestal seat. Drill and tap the hole for the next seat base directly across from the first. Use stainless machine screws to secure the base to the floor. Drill and tap the remaining holes for the pedestal seat base. It is a good idea to use anti-seize compound on the stainless fasteners to prevent the aluminum from seizing up on the bolts and preventing their future removal.
Finding Electrical Drains: A Boat Owner's Guide to Troubleshooting
You may want to see also
Using aluminium or plywood as a backing plate
When installing boat pedestal seats on wood floors, it is important to consider the type of decking and its solidity. If your boat has thin fibreglass decking, you may need to reinforce it with a backing plate made of aluminium or plywood. This will provide more support and help prevent the screws from pulling out.
To use aluminium or plywood as a backing plate, follow these steps:
First, cut a piece of aluminium or plywood that is slightly larger than the seat base. For aluminium, use a sheet with a thickness of at least 1/16". For plywood, a thickness of 3/4" is recommended, although 1/2" can also work. Coat the plywood with a sealer like Spar Urathene or exterior-grade spar urethane to protect it from moisture.
Next, attach the backing plate to the underside of the floor. You can use stainless steel screws and contact cement, or epoxy for plywood. If you are using aluminium, you can also use rivets to secure the backing plate to the floor. Make sure the backing plate is securely attached and won't move when you install the seat pedestal.
Now, mark the centre hole for the pedestal base. You can use a hole saw or a drill to make the hole. If using a drill, drill a series of holes that fit snugly around the stem of the pedestal. Coat the inside of the hole with a sealer like Spar Urathene.
Once the centre hole is done, mark and drill the holes for the pedestal base mounting. Use a drill bit that is the appropriate size for your bolts or screws. You can now attach the seat pedestal base to the backing plate with stainless steel bolts and washers. Use a healthy amount of marine caulk or adhesive/sealant on the screw holes to prevent leaks.
Finally, install your boat seat onto the pedestal, following the manufacturer's instructions. Make sure to wait for the caulk or adhesive to cure completely before using the seat.
Walking on Water: Racing Boat Techniques
You may want to see also
Using marine caulk or adhesive/sealant to seal the screw holes
Once you've drilled the holes for your boat's pedestal seat, the next step is to seal the screw holes with an appropriate marine caulk or adhesive/sealant. This is an important step to ensure that your boat seat is securely fastened and to prevent water ingress, which can lead to corrosion and damage to the decking.
There are several types of marine caulks and adhesives available, each with its own advantages and considerations. Here are some options to consider:
Polyurethane Marine Adhesive/Sealant: Polyurethane-based products offer excellent adhesive strength and can be used for both above and below the waterline applications. They are suitable for hull-to-deck joints and through-hull fittings. However, they are not recommended for bonding with certain plastics like ABS, Lexan, or other similar materials.
Silicone Sealant: Silicone is a flexible and versatile option. It is often used for isolating metals to prevent electrolysis and reduce vibration. Silicone works well for sealing plastics, but it requires compression to maintain adhesion. It's important to note that neat caulk lines are crucial when working with silicone as it cannot be painted over.
Polyether Sealant: Polyether is chemically resistant and is not affected by teak oil or cleaners. It remains permanently flexible and can be sanded and painted over. However, certain formulations can attack some plastics, so be sure to read the label carefully before use.
When selecting a marine caulk or adhesive/sealant, consider factors such as compatibility with materials, resistance to UV rays and saltwater, flexibility, and ease of application. These factors will ensure optimal performance and a strong, watertight seal.
After applying the marine caulk or adhesive/sealant to the screw holes, allow it to cure completely according to the manufacturer's instructions before using your boat. This will ensure that the seal is fully effective and that your boat seat is securely fastened.
Natalie Maines' Boat: A Chaotic Adventure
You may want to see also
Drilling pilot holes to prevent the base from getting jostled out of position
Drilling pilot holes is an important step in the process of installing boat pedestal seats on wood floors. It ensures that the base remains securely in position and prevents the wood from splitting or cracking. Here are some detailed instructions to help you drill pilot holes effectively:
Selecting the Right Drill Bit:
Choose a drill bit that matches the size of your screws. For screws, select a bit that corresponds to the inner diameter of the threaded portion, excluding the threads. This ensures that the pilot hole is wide enough for the screw to fit snugly without being too loose.
Measuring and Marking the Pilot Hole Location:
Carefully measure and mark the location of the pilot hole before drilling. Measure across the workpiece, making short lines at the intersection points. This intersection is the centre point for the pilot hole. You can also use a pencil or tape to mark the spot, or create an "X" with painter's tape for added protection against cracking.
Installing the Drill Bit:
Insert the selected drill bit into the chuck of your drill, ensuring it is fully seated and tightened securely. Adjust the drill's setting to the drill icon and ensure it is set to forward drilling.
Drilling the Pilot Hole:
Wear protective eyewear to shield yourself from any debris or sawdust. Align the drill perpendicular to the surface, using a speed square as a guide. Start drilling slowly and gradually increase the speed as you gain control. Continue drilling until the pilot hole reaches the desired depth, which should match the length of your screw.
By following these steps, you can effectively drill pilot holes to prevent the base of your boat pedestal seats from getting jostled out of position during installation. This technique will also help prevent damage to the wood floor and ensure a secure fit for your screws.
Compliance Label Number: Locating It on Your Boat
You may want to see also
Frequently asked questions
You can take a thin rigid piece of wire and run it through the holes to measure the length of wire where it bottoms out. If it doesn't go through the hole, you can calculate a rough dimension of deck to hull by measuring from the top of the gunnel to the bottom of the hull, then to the top of the deck.
You can use plywood for the boat floor.
You should use stainless steel bolts.
The height of the pedestal depends on your helm-seating situation and personal height.
Check under the deck for interference before drilling. For a deck less than 3/4-inch thick, use a backing plate, which can be fashioned from a 3/8-inch-thick plate of aluminum, pre-drilled to the hole pattern on the base. Drill the mounting holes through the deck. Bed around the base and dab each hole with marine sealant. Secure the base with bolts, washers, and nuts.