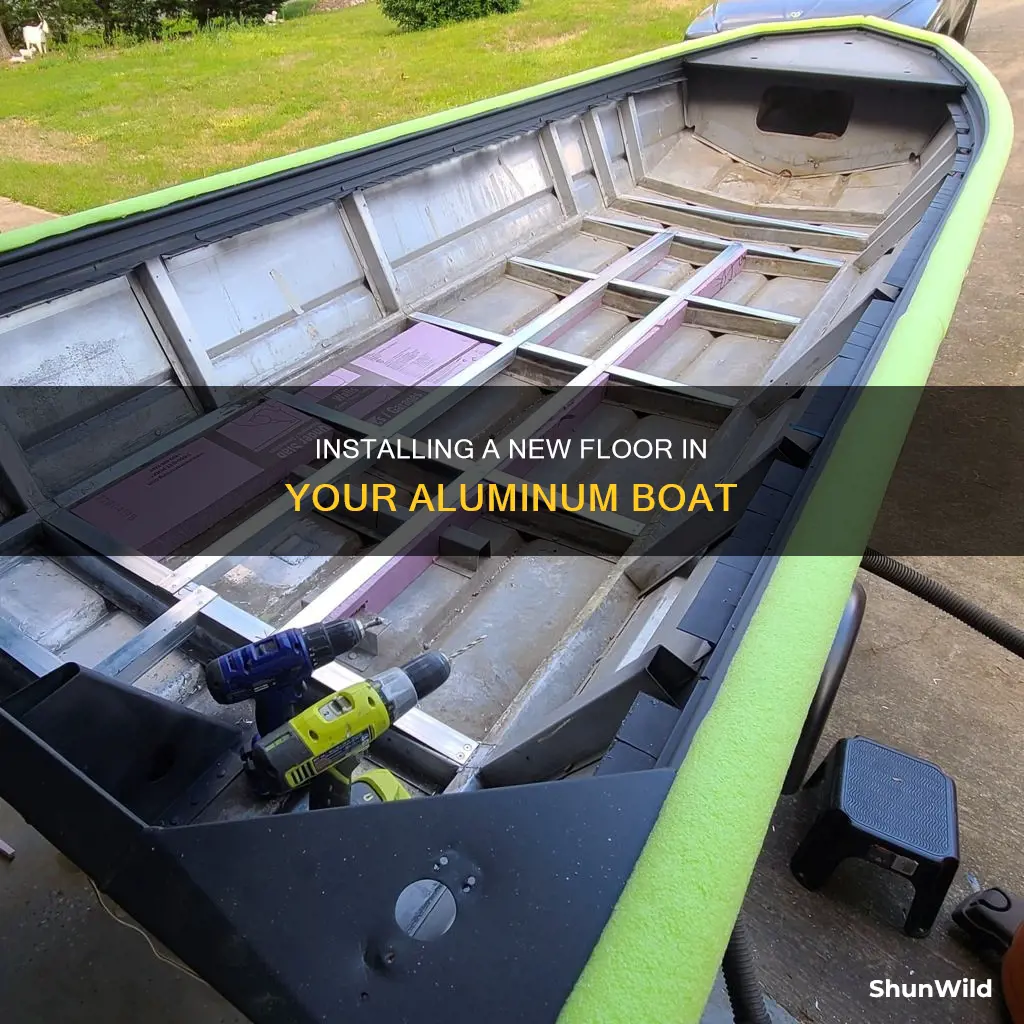
Boat floors are bound to show signs of wear and tear over time, and replacing them is a big decision. While it is possible to do it yourself, it is recommended to get professional help for a more precise installation. There are several options for boat flooring materials, each with its own advantages and disadvantages. For example, while wood is a traditional boat floor material, it is not waterproof or slip-resistant and requires regular maintenance. On the other hand, foam flooring is water-resistant, UV-resistant, and non-absorbent, making it a more lightweight and low-maintenance option.
What You'll Learn
Removing the old floor
The first step in replacing the floor of your aluminum boat is to remove the damaged boat floor. If your boat has bench-style seats, you will need to remove these to access the floor. Start by removing the rivets that attach the seats to the hull. The easiest way to do this is by drilling them out. You can use an 11/64” drill bit for a 3/16” rivet, and insert a small tapered punch in the hole to break off the head of the rivet. Once the rivets are drilled out, remove any remaining screws along the base of the seats and storage compartments. The seats and compartments should then lift right out. Make sure to mark and tape any foam pieces together for easy reassembly.
If your boat has a live well, you will also need to remove the hose clamps and hoses before removing the well itself. Now that you have access to the floor, you can start removing the fasteners holding the plywood floor in place. Again, these are likely to be rivets or screws. Take care not to damage the floor covering, as you may be able to reuse it. It is recommended to wear leather gloves when handling the old floor, as there may be loose staples or rusty rivets.
Once all the fasteners are removed, lift the old floor out of the boat. This is easier with an extra pair of hands, as the floor can be heavy and awkward to carry. Now, you can decide whether to reuse the floor covering or not. If you plan to reuse it, clean it with a pressure washer and/or scrub brush. If not, you can use it as a template for cutting your new floor covering.
Floor Covering Removal
If you are reusing the floor covering, clean it now. Remove any remaining staples and pieces of rotted plywood that may be stuck to it. If you are not reusing it, lay it out and flatten any creases and folds. You can do this by laying 2x4 boards on top of it with a little weight. Now, set the floor covering up on a couple of sawhorses with the bottom side up. Remove the staples around the perimeter of the old floor, and slowly work the floor covering loose using a wide putty knife. Depending on the type and amount of glue used, this may be more or less difficult.
Best Places to Sell Boat Engines
You may want to see also
Choosing the right material
When it comes to choosing the right material for a new floor in an aluminium boat, there are several options available. Each material has its own advantages and disadvantages, so it's important to consider factors such as cost, durability, weight, and ease of installation before making a decision.
One of the most popular choices for boat flooring is plywood, specifically marine-grade plywood. It is a superior product that offers greater strength and rigidity compared to other types of plywood. While it is more expensive, it can provide a long-lasting and durable solution for your boat floor. If cost is a concern, exterior-grade plywood can also be used, but it's important to seal it properly with epoxy resin to ensure its longevity.
Another option is to use aluminium for the boat floor. Aluminium is a lightweight and durable material that can provide a strong and rigid surface. It is more expensive than plywood but may be worth considering if weight is a concern. Additionally, aluminium can be welded or riveted in place, providing a secure and permanent solution.
For those seeking a more cost-effective option, carpet-covered pressure-treated plywood can be a good choice. This combination offers a sturdy and affordable floor for your boat. However, it is important to note that the chemicals used in pressure-treated plywood may not react well with aluminium over time, so it's essential to take this into consideration.
If you're looking for a lightweight and easy-to-install option, structural foam covered with carpet or vinyl can be a great choice. This material is available at most home improvement stores and is easy to cut and install. It provides a comfortable and grippy surface while also being durable and long-lasting.
When making your decision, it's important to keep in mind the specific needs and requirements of your boat. Consider factors such as the frequency of use, the type of water you'll be navigating, and your budget. By carefully weighing the pros and cons of each material, you can choose the right option for your aluminium boat floor.
The Best Seat to Row a Boat
You may want to see also
Sealing the plywood
Step 1: Gather Materials and Prepare the Surface
Before you begin, make sure you have all the necessary materials, including soft cloths or paper towels, clear penetrating epoxy, and a foam brush or roller. Start by cleaning the surface of the plywood with a paper towel or soft cloth dipped in acetone to remove any grease or stains. Allow the acetone to dry completely for 1-2 hours.
Step 2: Sand the Plywood
Sand both sides of the plywood, including the edges, with 80-grit sandpaper. This step is crucial to ensure the surface is smooth and ready for sealing. Once you're done sanding, wipe away all the dust and particles with a soft cloth.
Step 3: Apply the First Coat of Sealant
For the sealant, we recommend using clear, penetrating epoxy as it penetrates deep into the wood, dries transparent, and requires less maintenance than other types of sealants. Dip your foam brush or roller into the epoxy and apply it to the wood, starting with the top and side edges and then moving to the front face. Allow the epoxy to dry completely before flipping the plywood over and applying it to the bottom edge and back.
Step 4: Add Additional Coats
To maximise the lifespan of your plywood, it's important to apply multiple coats of sealant. A good rule of thumb is to add as many coats as there are layers of plywood. For example, if your plywood has 7 layers, apply 7 layers of sealant. Gently scuff the surface with sandpaper between each coat to ensure maximum adhesion, and don't forget to wipe off any dust before adding the next layer.
By following these steps and allowing adequate drying time between coats, you will effectively seal the plywood for your aluminium boat, ensuring it can withstand moisture and water exposure for years to come.
Exploring Lakes: Choosing the Right Boat
You may want to see also
Attaching the floor
Now that you have the new plywood floor cut and dry-fit, there are a few things you’ll need to do before permanently installing it. These steps will help ensure your new floor is strong, secure, and will last for many years.
Firstly, seal the plywood floor. This is important to significantly extend the life of the plywood. If you are making any splices, seal all the surfaces before joining the pieces together. Use good-quality oil-based paint for this. Apply two coats to all surfaces, top and bottom, allowing 24 hours for the paint to dry between coats.
If you have splices, join the pieces of plywood together using a 1/8” thick, 2” aluminium strap, secured with large flange rivets to the underside of the floor. Space the rivets about 6 to 8 inches apart. Do not let the aluminium strap touch any of the keel or cross-member supports. You want the floor to sit as flat as possible with no potential for wear spots.
To make the splice, start with the plywood upside down, sitting on sawhorses and a couple of 2x4s for support. Pre-drill the aluminium strap with the rivet holes. With the aluminium strap in place on the plywood, drill the rivet holes through the plywood. Before beginning to rivet, lift the aluminium strap and put a small dab of marine silicone in and around each hole in the plywood before placing the strap back in place. Now you can start installing the rivets from the underside of the plywood. Be sure to put a small dab of silicone on the holes in the plywood before inserting the rivet. I also used washers on the aluminium strap side to help ensure a good connection. Once the rivets are in, wipe any excess silicone that may have squeezed out from under the rivet flange. This will leave a nice smooth surface.
From this point forward, get help when handling the floor. Although the joint in a boat floor rebuild is solid, it is best not to put any undue stress on it. Besides, at this point, the floor is quite large and awkward for one person to handle.
If you are installing a new floor covering, place the new floor covering, face-up, on a smooth surface, and set the new floor on top of it, also face up. If you have a splice in the plywood with rivets on the underside, you may want to flip both the floor covering and the floor over. This will help prevent the rivets from damaging the floor covering.
Once the floor is on the floor covering, draw a line 5 or 6 inches along the perimeter of the plywood floor. This should be plenty for wrapping around the edges and securing it. Set the plywood floor on sawhorses, face-up, while you cut the floor covering out.
Now you’re ready to glue the flooring onto the new plywood floor. Apply the appropriate glue for the type of floor covering you’re using, per the manufacturer’s instructions. Lay the new floor covering, face-up, on top of the glue. A helping hand is really nice for getting the floor covering in place. Most manufacturers recommend rolling, or pressing, the entire surface into the glue for proper bonding.
Wrap the excess floor covering around and under the edges of the plywood floor and staple it to the underside. Do this in a few locations around the perimeter of the plywood. At this point, it’s much easier to flip the entire floor over to finish securing the floor cover.
Continue wrapping and stapling the floor covering around the entire perimeter of the plywood. At the corners of the floor, you will need to fold the covering over prior to stapling it for a nice clean finish. I recommend using stainless steel staples. They will last much longer than regular metal staples. The new floor is now ready to be installed!
While you’re waiting for the paint to dry, in between coats, you can prepare the bottom of the boat for installing the new floor. Start by thoroughly cleaning the inside of the boat. A pressure washer works great for this. They can easily remove years of nasty dirt and debris.
Next, you’ll want to remove the old rivet pins that are left after drilling out the rivet heads to remove the old floor. A few may fall out, but the majority will remain in the floor supports. You may need to use a combination of pliers or a hammer and tapered punch to remove them all. This will allow the new floor to set down evenly on all the existing floor supports.
Another useful tip is to mark the location of the hull cross-members on the side of the boat. Be sure they’re high enough that you’ll be able to see them once the new floor is set in place. This, along with your diagram, will be helpful when installing the pop rivets to secure the new floor. Also, this will be your last opportunity to get measurements for any floor supports and rivet hole locations.
With the boat floor removed, now is the ideal time to thoroughly inspect the bottom of the boat. Look for loose rivets, that may be leaking, and signs of damage from hitting objects in the water.
The easiest way to do this is to partially fill the boat with water. Put just enough water to cover the rivets in the bottom of the boat. Never completely fill a boat sitting on a trailer with water. That much water would be very heavy and could cause damage to the trailer and/or the bottom of the boat.
Remember that the seats that were removed for the project add structural support to the boat’s hull. Plus, they are designed to keep water out, not in. That much internal water force and reduced structural strength could allow the boat to deform or bend.
With water in the bottom of the boat, crawl under the boat and look for any signs of water leaking. If you do find any issues, circle the leaking rivet(s) or damaged spot(s) with a permanent marker. Then drain the water and make repairs as needed. Now is the time to make the repairs while the floor is removed.
A leaking rivet can easily be repaired with the tools available for this project. We’ve already gone over how to remove (drill out) rivets, and will be covering the installation of solid rivets below.
If you find a crack or other type of damage that may require welding, hire a qualified welder for the job. Welding on thin aluminium is difficult and usually requires special welding equipment.
This is probably the most exciting part of the project. Laying the new floor into place in the bottom of the boat. You’ll definitely want some help lifting and installing the new floor into the boat.
If you are
The Intriguing Question: Boats Dock, But Do They Land?
You may want to see also
Reinstalling seats and storage
Once the new floor has been installed, you can now reinstall your boat seats and any other storage compartments you had to remove. As long as you used the same thickness of plywood, the rivet holes should line up fairly well. The aluminium seats may flex a little, but they should move into place relatively easily.
The best way to do this is to align one boat seat flange rivet hole to the boat hull rivet hole at a time. Once the holes are aligned, you can install the solid rivets one at a time. To help with the alignment, use at least one small, tapered punch. Simply put the end of the tapered punch in the hole on the seat flange and then into the corresponding hole in the boat's hull. As you push it in, the taper aligns the two holes perfectly.
If you have a loose fit between the seat flange and the hull, you’ll need to use a screw and nut. Insert the screw as described above and then thread the nut all the way onto it. Snug the nut and screw up until the seat and hull surfaces meet. Now, align the other two holes using the tapered punch. Even if you have two punches, you may want to have a 3/16” nut and screw handy to deal with any loose fit-ups.
Once you get the holes lined up, you can begin riveting. If you are new to installing solid rivets, don’t worry. The process is pretty straightforward and actually easy to do.
Before starting, there are a couple of things you need to do first. Number one is to set the pressure regulator on the air compressor to the recommended pressure for the air chisel/hammer. Then install the rivet set tool into the air hammer.
If you have an old chisel tool for your air hammer, it is possible to make your own rivet set tool. It’s fairly easy to make and can save you from having to buy one. Below is a short video showing how to do this.
The second item I highly recommend is to wear hearing protection. An air hammer on an aluminium boat creates quite a bit of noise. And be sure to wear a pair of safety glasses, too.
Once you have the holes in the seat flange and the boat hull lined up and pulled together using your tapered punch and a 3/16” screw and nut, you’re ready to start riveting. Put a small dab of marine silicone around the hole on the outside of the boat’s hull to help ensure a watertight seal.
Insert the rivet into the hole and hold it in place, against the hull, with the air hammer and rivet tool. Place the bucking tool (hammer) on the end of the rivet inside the boat. Be sure to hold it square to the rivet shaft, so it peens it evenly.
When using the air hammer, just use 4 or 5 short, one or two-second bursts to set the rivet. When finished, the diameter of the peened end of the rivet should be roughly 1.5 times the diameter of the rivet shaft. The height of the peened end of the rivet should be roughly 1/2 the diameter of the rivet. Over-tightening the rivet can damage the pieces being fastened together.
Boat Painting: A Step-by-Step Guide to Success
You may want to see also
Frequently asked questions
There are several options for fasteners that you can use to attach a new floor in an aluminum boat, including screws, rivets, and welding. The type of fastener you choose will depend on factors such as the intended use of the boat and the ease of maintenance. For example, if you anticipate needing to remove the floor for maintenance, screws or rivets may be a better option than welding.
When selecting a material for your new boat floor, consider factors such as cost, durability, and ease of installation. Plywood, aluminum, vinyl, and marine carpet are all popular options for boat flooring materials. Marine foam, in particular, has been praised for its performance, comfort, and protection.
Replacing the floor in an aluminum boat can be a DIY project, but it is important to note that it may be a challenging task that requires a variety of tools and careful planning. If you decide to take on this project yourself, be sure to follow a detailed guide and take the necessary safety precautions.