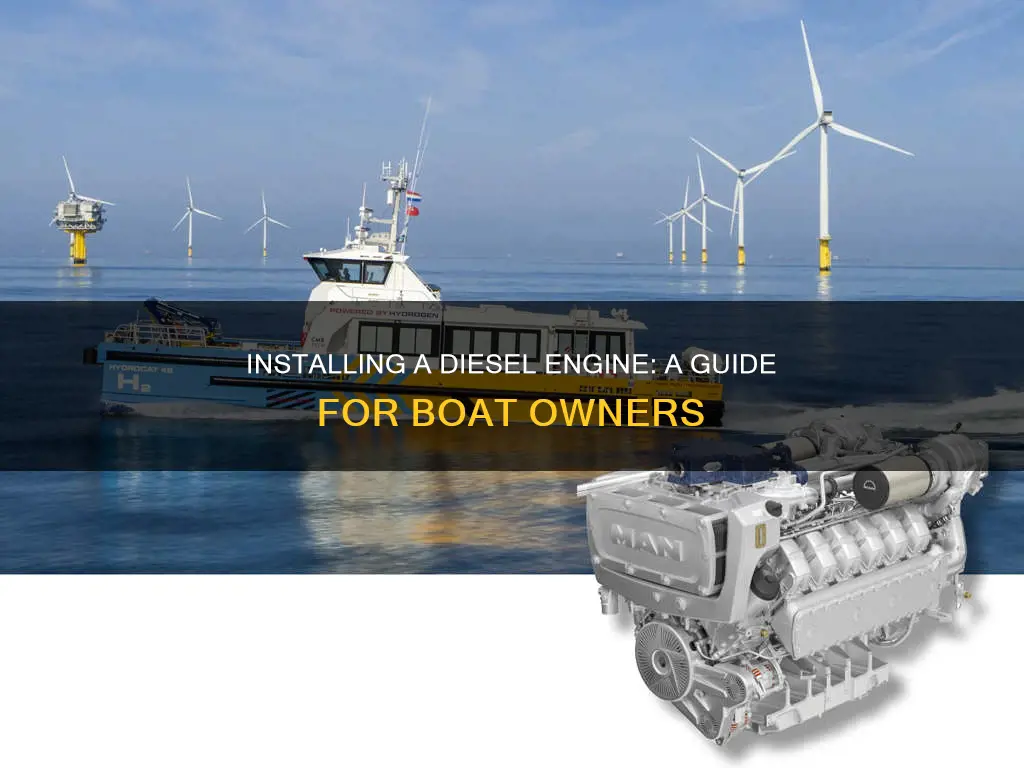
Putting a diesel engine in a boat is a complex process that requires careful consideration and planning. While it is possible to use an automotive diesel engine for a boat, there are several key factors that need to be addressed. These include the cooling system, exhaust, and transmission, which may differ from those in a car. Additionally, the installation process can be challenging, especially when it comes to fitting the engine into the boat's engine bay and ensuring proper cooling and exhaust systems. The costs of such an installation can also be high and unexpected problems may arise. However, with careful planning and execution, it is possible to successfully install a diesel engine in a boat, improving its performance and efficiency.
The cooling system
Open Circuit Cooling System
The open circuit system, also known as a raw water system, draws in seawater directly from the surrounding environment, circulates it through the engine's cooling passages, and then discharges it back into the sea. While this system is simple and cost-effective, it is susceptible to saltwater corrosion, requiring regular maintenance and inspections. Saltwater can accumulate corrosive materials, affecting engine components' efficiency and lifespan. Therefore, open circuit systems necessitate frequent maintenance to prevent engine damage.
Closed Circuit Cooling System
On the other hand, the closed circuit system utilizes a mixture of freshwater and antifreeze as the cooling medium. This mixture circulates through the engine cooling system, absorbing heat, and then passes through a heat exchanger to transfer the heat to seawater before being discharged. Closed-circuit systems offer superior corrosion protection for vital engine components but are more complex and require additional components like heat exchangers and pumps. The choice between these two systems depends on the vessel's specific requirements and the owner's maintenance preferences.
Indirect Cooling System
Another variation of a cooling system is the indirect cooling system, where raw water (seawater) enters the boat through a seacock and passes through a raw water filter to remove weeds and debris. It then circulates through hoses and a pump to a heat exchanger, where it cools the freshwater circulating around the engine. The seawater is then pumped into the exhaust system, mixing with exhaust gases and discharged into the sea. This system is similar to the cooling system found in cars.
Direct Cooling System
In contrast, the direct cooling system is more basic, where raw water is pumped directly through the engine block and back out to sea, without the use of a secondary freshwater system. While this may seem straightforward, corrosion can become a significant issue in this type of system.
Key Components of a Cooling System
Regardless of the type of cooling system, there are several key components that play a crucial role in maintaining the engine's temperature:
- Seacocks: These are through-hull devices that allow water to enter the hull from the outside. Seacocks have handles to shut off water flow in case of problems like loose hose clamps or cracked hoses.
- Sea strainers: These devices filter out debris, sand, and leaves from the raw water before it reaches the engine. They work similarly to swimming pool skimmers.
- Hoses, clamps, and belts: These components are vital to the cooling system and should be checked periodically for wear and corrosion.
- Water pump impeller: The raw water pump contains an impeller that is driven by a belt and circulates water through the system.
- Heat exchanger: This component is used in closed-circuit systems to transfer heat from the freshwater coolant to the seawater.
- Seawater pump: This pump circulates seawater through the heat exchanger and is typically driven by a belt on the engine.
Boat Disaster: Neighbor's Tree Falls, Now What?
You may want to see also
The exhaust
Firstly, a water-cooled exhaust manifold is necessary. This requires bolting a custom-built marine cylinder head to the automobile engine, as a standard automobile head won't suffice. Additionally, a wet exhaust system is preferable to a dry exhaust, as it significantly reduces noise levels. To achieve this, a water injection nipple needs to be installed on the discharge elbow from the exhaust manifold.
The sizing of the exhaust piping and muffler is also critical. Careful engineering is required to ensure that the water flow from the exhaust matches the power output of the engine. A water-lift muffler is typically set below the exhaust elbow, and the raw-water discharge from the heat exchanger is plumbed to this elbow.
Furthermore, an anti-syphon unit is an important addition to the exhaust system. This unit helps prevent the backflow of water and is usually fitted with a drain leading out of the boat.
Finally, the exhaust hose diameter should be considered. A larger engine will require more cooling water, which in turn necessitates a larger diameter exhaust hose.
In summary, the exhaust system for a diesel engine in a boat requires careful planning and engineering to ensure proper cooling, noise reduction, and the prevention of water backflow. It is important to ensure that all components are appropriately sized and fitted to avoid potential issues.
Launching a Bass Boat: A Step-by-Step Guide
You may want to see also
The transmission
The first step is to ensure that the transmission fits the engine flywheel housing. It might be possible to use an adapter between the engine and the transmission to achieve a proper fit. The transmission must also have a drive shaft that can be coupled to the engine's output shaft.
In some cases, it may be necessary to modify the engine bed and motor mounts to accommodate a different engine and transmission setup. This adjustment ensures that the new engine and transmission assembly fit correctly and securely in the boat.
Additionally, the connection between the engine and the transmission can be challenging. The flexplate, gearing, and other small components may require customisation or adaptation to work together seamlessly.
It is worth noting that marinizing an engine is generally considered easier than addressing the transmission and related components. The transmission plays a crucial role in matching the engine's output to the propulsion requirements of the boat, and any mismatch can impact the boat's performance and fuel efficiency.
When installing a diesel engine in a boat, it is important to carefully consider the transmission system and ensure that it meets the specific requirements of the engine and the boat. This may involve using adapters, customising components, or seeking out marine transmissions designed for the particular engine.
A Guide to Connecticut's Boat Registration Certificates
You may want to see also
The engine mount
Firstly, it is important to assess the compatibility of the engine with the boat. The engine mount must be designed to fit the specific model of the diesel engine being installed. This includes ensuring that the engine mount can support the weight and dimensions of the engine. It is also crucial to consider the placement of the engine within the boat and make necessary adjustments to the engine bed and mount to ensure a secure fit.
Secondly, the engine mount should be constructed using durable materials that can withstand the marine environment. Stainless steel is often a preferred choice for engine mounts due to its strength and corrosion resistance. The mount should be designed to securely hold the engine in place, accommodating for any vibrations or movements that may occur during the boat's operation.
In the case of John Willis and his pilothouse yacht, Pippin, the engine mount required significant modifications. The new engine was larger and needed to be mounted further forward, which called for a longer propeller shaft. To accommodate this change, the engineer lowered a non-structural longitudinal under-floor bulkhead and made a cutout in the transverse under-floor bulkhead. Additionally, stainless steel flat bars were machined to fit over the top of the bearers, providing a sturdy base for the new engine mountings.
It is worth noting that the engine mount should also allow for easy access to the engine for maintenance and repairs. This may involve designing removable panels or hatches that can be opened or slid out when needed.
Furthermore, the engine mount should be designed with proper ventilation and drainage in mind. This is particularly important for diesel engines, as they require adequate airflow and drainage to prevent overheating and moisture buildup.
Lastly, it is crucial to consult with experts or experienced boat builders when designing and installing the engine mount. While it may be tempting to cut costs by attempting a DIY installation, the complexities involved in engine mounting can quickly become overwhelming for novices. By seeking professional guidance, you can ensure that the engine mount is secure, safe, and compliant with marine regulations.
A Guide to Understanding Virginia Boat Titles
You may want to see also
The propeller shaft
Components of the Propeller Shaft:
- The thrust shaft is the primary shaft that emerges directly from the engine and rotates at the maximum velocity in high-speed engines.
- The intermediate shaft has no specific restriction on its number, but beyond two shafts, maintenance can become challenging due to the large catenary force acting on the entire propeller shaft.
- The tail shaft is connected to the propellers and lies encased in the stern tube. It is joined to the intermediate shaft by a gearbox, which reduces the power transmitted to the propeller.
Design and Construction:
The design and construction phase is crucial to ensure structural strength and control material fatigue. The propeller shaft bearings, in particular, require careful construction as they support the entire weight of the shafts. There are two main types: full case bearings located at the stern and half case bearings located at other positions.
Stern Tube and the Propeller Shafts:
The stern tube is a hollow, horizontal tube that serves as the primary connection between the propellers and the rest of the vessel. It houses the tail shaft and has two main purposes: withstanding load and sealing the vessel at the aft portion. The stern tube also needs to be able to effectively seal the vessel, preventing water from entering through the aft. This is achieved using seals like stuffing boxes, lip seals, and radial face seals.
Alignment:
Proper alignment of the propeller shaft is critical. With two to four shafts, each one must be centred accurately to prevent mishaps. Even a slight misalignment can cause rapid oscillations, resulting in large stresses that can permanently damage the shaft.
Propeller Choice:
The choice of propeller depends on various factors, including engine size, desired speed, and available space. Low-drag folding propellers are often preferred for their efficiency, but feathering propellers can be a good alternative if space constraints don't allow for a folding prop.
Installation:
Installing a diesel engine and propeller shaft requires careful planning and measurements. Factors to consider include shaft exit location, engine compartment space, propeller submersion depth, and fuel tank placement. Drilling a test hole can help determine the exact position of the shaft log, which then guides the rest of the installation process.
Adjusting Packing Seals: Direct Drive Boat Maintenance
You may want to see also
Frequently asked questions
In principle, a diesel engine is a diesel engine, so an automotive diesel engine will work in a boat. However, the "marinizing" process can be complicated and requires addressing key aspects such as the cooling system, exhaust, and transmission. It's also important to ensure that the engine fits within the boat's engine bay and is properly mounted.
First, remove the old engine. Then, ensure the new engine fits within the engine bay and make any necessary adjustments, such as modifying the propeller shaft or creating extra space. Install the new engine, addressing the cooling system, exhaust, and other connections. Finally, test the engine and make any necessary adjustments.
Automotive diesel engines can be cheaper and more readily available than marine engines. However, they may require significant modifications to work in a marine environment, including changes to the cooling system, exhaust, and transmission. It is also important to consider the size and weight of the engine relative to the boat.
The specific tools and supplies will depend on the engine and boat, but some common items include spanners or wrenches, wire brushes, Vaseline, fuel additives, gloves, and engine parts such as filters, belts, and gaskets. It is also important to have access to machine shops or machinists for custom fabrications.