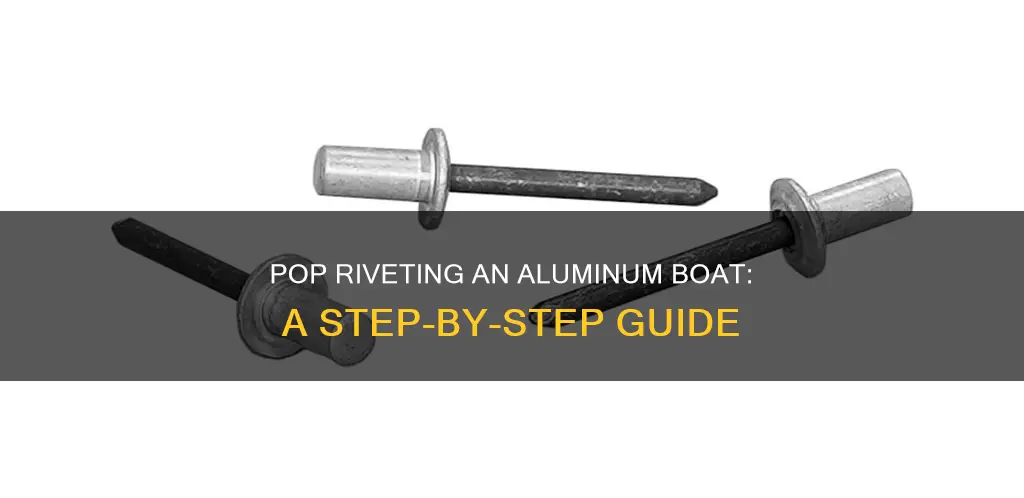
Pop rivets, also known as blind rivets, are a popular choice for fastening aluminium boats due to their ease of installation, versatility, and temporary fastening capabilities. They are widely used for hull repairs, attaching accessories, and other applications where access to both sides of the joint is limited. When dealing with aluminium boats, it is crucial to select rivets that are specifically designed for use with aluminium or other compatible materials to ensure a secure and long-lasting bond. Additionally, corrosion resistance is a key consideration to prevent structural damage caused by water exposure. This guide will explore the process of popping rivets in an aluminium boat, including the tools and techniques required, and provide valuable insights into choosing the right type of rivets for optimal performance and durability.
Characteristics | Values |
---|---|
Boat Type | Aluminium |
Rivet Type | Pop |
Repair Type | Replacing rivets |
Rivet Properties | Waterproof, corrosion-resistant, strong, durable, vibration-resistant |
Installation Process | Drill out old rivets, insert and secure new rivets with a rivet gun |
Ease of Installation | Quick and easy, no specialised skills or equipment needed |
Material Compatibility | Aluminium, steel, plastics, fibreglass |
Corrosion Resistance | Stainless steel, aluminium with anti-corrosion coatings |
Strength and Load Capacity | High tensile and shear strength |
Size and Shape | Right size for application, shape allows for proper installation and secure fit |
Seal Type | Water-tight seal |
What You'll Learn
- Choosing the right rivets: consider material, corrosion resistance, strength, and size
- Creating a water-tight seal: prevent leaks, maintain structural integrity, and enhance performance
- Closed-end rivets: a sealed, closed structure at the connection point
- Solid rivets: a strong, permanent, and vibration-resistant fastening solution
- Pop/open-end rivets: easy to install, versatile, but not fully watertight
Choosing the right rivets: consider material, corrosion resistance, strength, and size
When it comes to choosing the right rivets for an aluminium boat, there are several factors to consider, including material, corrosion resistance, strength, and size.
Firstly, it is important to choose rivets made of aluminium or another compatible material. Aluminium boats require rivets specifically designed for use with aluminium. Using rivets made for other materials may result in an insecure bond.
Next, consider corrosion resistance. Boats are often exposed to water, which can cause corrosion if the rivets are not resistant. Choose rivets made of corrosion-resistant materials such as stainless steel or aluminium with anti-corrosion coatings to prolong the boat's lifespan and prevent structural damage.
The strength and load capacity of the rivets are also crucial. Aluminium boats are subjected to various loads and stresses, including waves, wind, and impacts. Select rivets with sufficient strength and load capacity to withstand these forces. Weak rivets may fail under pressure, compromising the boat's integrity and posing safety risks.
Size and shape are equally important. Choose rivets that are the right size for the application and have a shape that allows for proper installation and a secure fit. Improperly sized or shaped rivets may not create a tight seal, leading to leaks or loosening over time.
Additionally, consider the type of rivet based on the specific requirements of the application. Solid rivets, for instance, offer high strength and durability but require access to both sides of the joint during installation. Open-end rivets are easy to install but may not provide a fully watertight seal. On the other hand, closed-end rivets are designed for watertight applications but are more expensive.
Finally, when replacing rivets, follow a careful process to ensure a secure and watertight installation. Prepare the work area, identify damaged rivets, drill out the old rivets, remove them, and prepare the new rivets by selecting the appropriate size and type. Insert the new rivets, and secure them with a rivet gun or suitable tool to create a watertight seal.
Repairing Boat Heat Exchangers: A Step-by-Step Guide
You may want to see also
Creating a water-tight seal: prevent leaks, maintain structural integrity, and enhance performance
Creating a water-tight seal is essential to prevent leaks, maintain structural integrity, and enhance the performance of an aluminum boat. Here are some detailed instructions and considerations to achieve that:
Choosing the Right Rivets:
Select closed-end rivets, also known as sealing blind rivets, which are specifically designed to prevent water and air penetration. These rivets form a sealed closure head, ensuring that moisture doesn't enter the joints and reducing the risk of leaks. The closed-end design also prevents corrosion by keeping corrosive substances out of the joint, which is crucial for extending the life of the boat.
Preparing the Rivets and Surfaces:
Ensure that the rivet size matches the hole size in the boat material. The hole may need to be drilled slightly larger to accommodate the rivet stem. Clean the area around the hole with a brush to remove any debris or residue. Apply a sealant or waterproof coating to the rivet stem and the hole. This extra step will enhance the watertight seal and protect against corrosion.
Installing the Rivets:
Use a pop-rivet tool to install the closed-end rivets. Place the rivet into the hole and push it in, then use the pop-rivet tool to secure it in place. Ensure that the rivet is properly installed and seated to create a smooth, closed head. This installation method is quick and easy, and it doesn't require specialized welding equipment or skills.
Maintenance and Inspection:
Regularly inspect and maintain the rivets according to the manufacturer's recommendations. Check for any signs of corrosion, fatigue cracks, or loosening of the rivets. Proper maintenance will help identify potential issues and ensure the long-term reliability of the watertight seal.
Alternative Methods:
If you're unable to find closed-end rivets or prefer alternative solutions, there are a few other methods to create a watertight seal. One option is to use a product like 3M sealant or marine silicone sealant around the rivets on the outside of the hull. Another method is to replace the rivet with a larger-sized one, using a sealant like Dicor caulking. Additionally, you can use an epoxy product, such as J-B Weld or Muggyweld, to seal the rivets and prevent leaks.
Remember, creating a water-tight seal is crucial for the safety and longevity of your aluminum boat. By following these instructions and choosing the right materials, you can effectively prevent leaks, maintain the structural integrity, and enhance the performance of your vessel.
Boat Docking Options in Dry Tortugas: What You Need to Know
You may want to see also
Closed-end rivets: a sealed, closed structure at the connection point
When it comes to aluminium boats, secure connections are critical. As boats are in constant contact with water, corrosion and water resistance are key factors to consider when choosing rivets for connections. This is where closed-end rivets come in.
Closed-end rivets, also known as sealing blind rivets, are specifically designed to prevent water and air from passing through or around them. This makes them ideal for joining materials in an aluminium boat, where you may not always have access to both sides of the connection point. The unique feature of closed-end rivets is that they form a sealed, closed structure at the connection point, ensuring a watertight seal. This is achieved through the two parts of the closed-end rivet: the rivet stem and the closed head. The rivet stem is the part that passes through the material and secures the connection, while the closed head forms a sealed closure at the end of the rivet, preventing moisture and other corrosive substances from entering the joint.
The sealed closure head of closed-end rivets offers several benefits for aluminium boats. Firstly, it provides excellent waterproofing by preventing moisture penetration, which is crucial for applications in wet or underwater environments. Secondly, the closed head also enhances corrosion resistance by creating a barrier against corrosive substances, thus increasing the service life of the connection. Additionally, the closed head provides additional support and reinforcement, making the connection stronger and more reliable, which is particularly advantageous for high-stress applications.
Another advantage of closed-end rivets is their aesthetic appeal. The smooth closed head creates a consistent and refined appearance on the hull surface, which is especially important for high-end yachts and commercial vessels. Furthermore, closed-end rivets offer high sealing performance, preventing the leakage of liquids or gases, thus enhancing the safety and longevity of aluminium boats. In terms of installation, closed-end rivets are convenient and efficient, requiring no special tools or techniques, making them a preferred choice in the shipbuilding industry.
Show Boat: A Musical Journey on Racial Issues
You may want to see also
Solid rivets: a strong, permanent, and vibration-resistant fastening solution
Solid rivets are one of the most reliable and robust fastening solutions available. They are widely used in applications where safety and reliability are crucial, such as aircraft assembly. Solid rivets are also popular for their tamper-proof and vibration-resistant qualities.
Solid rivets are formed from a smooth, cylindrical shaft with a head. During installation, the end of the shaft expands, creating a "shop head" that securely fastens objects in place. This process ensures a strong, permanent joint.
The strength of solid rivets lies in their classic design, which has been trusted for decades. They are considered one of the most tamper-proof and vibration-resistant fasteners available. This makes them ideal for applications where security and stability are of utmost importance.
Solid rivets are available in various head shapes and materials, including solid steel and aluminium. Steel rivets offer incredible strength, while aluminium rivets are lightweight and corrosion-resistant. The versatility of solid rivets makes them suitable for a wide range of projects.
When choosing solid rivets for an aluminium boat, it is essential to consider corrosion and water resistance. Solid rivets' secure connection and corrosion resistance can help extend the life of the boat by preventing severe corrosion. Additionally, the lightweight nature of aluminium rivets aligns with the goal of maintaining the lightweight characteristics of aluminium boats.
Do Boat Trailers Need Temporary License Plates Post-Purchase?
You may want to see also
Pop/open-end rivets: easy to install, versatile, but not fully watertight
Pop/open-end rivets are a common choice for boat repairs and other applications. They are highly versatile, easy to install, and provide a reliable, high-strength connection. However, they are not fully watertight, which can be a significant drawback for certain projects, especially those involving boats.
Open-end rivets are hollow and pre-assembled onto a headed pin or mandrel. After installation, they resemble tubular rivets, but with the mandrel head remaining inside the rivet body. They are available in various metals, such as aluminum, carbon steel, stainless steel, and steel, making them suitable for a wide range of applications.
One of the key advantages of open-end rivets is their ease of installation. They can be installed quickly and easily using specialised riveting tools, and they do not require skilled operators. Additionally, they are strong and reliable, offering a wide load spread and strong, low-cost fastening. They are also versatile, with various head styles available, including dome, large flange, and countersunk options.
However, one of the main disadvantages of open-end rivets is their lack of sealing properties. They are not fully watertight, and in applications where the prevention of liquid, gas, or contaminant penetration is crucial, open-end rivets may not provide an adequate seal. This makes them less suitable for boats and other water-related projects.
For projects that require a fully watertight seal, closed-end rivets are a better option. Closed-end rivets have a unique, cup-shaped end configuration that creates a complete seal, preventing liquid or gas penetration. They are also suitable for a wide range of applications and provide a reliable, high-strength connection. Additionally, they offer excellent sealing performance and corrosion resistance, making them ideal for use in marine environments.
While open-end rivets are a versatile and cost-effective option for many projects, they may not be the best choice for aluminium boats due to their lack of full watertight capabilities. In this case, closed-end rivets or specialised sealing blind rivets would be a more suitable alternative to ensure a fully watertight seal.
Opening a Boat Dealership: A Comprehensive Guide
You may want to see also
Frequently asked questions
It is crucial to choose the right type of rivets for aluminum boats. The choice of rivets can impact the strength, durability, and performance of the boat. Consider factors such as material compatibility, corrosion resistance, strength, load capacity, size, and shape. Use rivets specifically designed for aluminum or compatible materials, ensure corrosion resistance, and select the appropriate size and shape for a tight seal.
A watertight seal is essential to prevent leaks, maintain structural integrity, enhance performance, and ensure the safety of the occupants. Water entering the boat can lead to damage, corrosion, and stability issues. It can also compromise buoyancy and safety in challenging conditions.
Closed-end rivets offer several advantages, including strong and permanent fastening, waterproof capabilities, vibration resistance, and versatility with various materials. The closed-end design prevents loosening and provides a secure joint, making them ideal for marine applications where moisture resistance is crucial.
To replace rivets, first secure the boat and gather the necessary tools and materials. Identify damaged or loose rivets, especially near stress points. Drill out the old rivets, being careful not to damage the surrounding area. Remove the old rivets, prepare the new ones, and insert them into the pre-drilled holes. Use a rivet gun or tool to deform the rivet body and create a secure fastening, ensuring a watertight seal. Repeat this process for all damaged rivets.