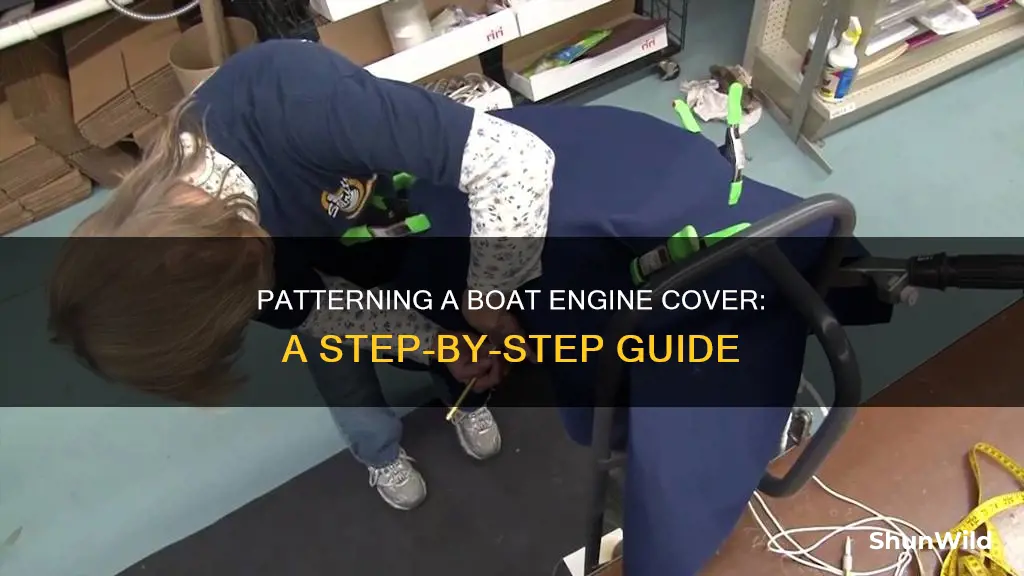
Whether you own a recreational boat or a commercial vessel, an engine cover is essential. In this guide, we will explore the process of patterning an engine cover for a boat, from choosing the right materials to the final installation. We will also discuss the benefits of making your own custom cover and provide step-by-step instructions for a DIY project. By the end of this guide, you should be able to confidently pattern an engine cover that fits your boat perfectly and protects it from the elements.
Characteristics | Values |
---|---|
Engine cover type | Inboard, outboard, powerboat |
Materials | Thick steel plate, heavy composite materials, reinforced fiberglass, stainless steel, canvas, Sunbrella acrylic, heavy canvas, marine-grade plywood |
Tools | Belt sander, cordless drill, sewing machine, scissors, spring clamps, sailmaker's palm |
Techniques | Pattern darting, sewing, stitching, basting, gluing, drilling |
What You'll Learn
Using fibreglass and marine hardware
To pattern an engine cover for a boat using fibreglass and marine hardware, you can follow these steps:
Firstly, you will need to take measurements. Measure the width and length of the opening above the engine, deducting 5/8 inch from each measurement to allow for the fibreglass. These measurements will be used to cut a piece of plywood that will serve as the mould for your engine cover. Cut the plywood using a circular saw or table saw.
Next, you will apply reinforced fibreglass to the plywood mould. Refer to the instructions provided with your fibreglass kit. Apply three layers of fibreglass to the surface and sides of the plywood, allowing it to harden completely before removing the mould. Once the fibreglass has hardened, use a belt sander with medium grit sandpaper to smooth out any rough edges and surfaces.
Now, you can attach the hinges and bolts to secure the engine cover in place. Position a pair of stainless steel butt hinges along one edge of the cover, with the hinge pins aligned at the outside edge, and drill pilot holes for the bolts. Insert stainless steel bolts into the pre-drilled holes, securing them with flat washers and nuts on the underside of the cover.
For a raised engine cover, you will need to make a three-sided cover using marine-grade plywood. Measure the opening above the engine, adding 1 inch each way to allow for the bottom edges to rest on the deck. Cut the front and sides of the cover according to your measurements, and assemble them with wood glue and wood screws. Stand the three-sided structure and re-check your dimensions for uniformity. Cut a plywood top to fit flush with the outside edges of the structure, and attach it with wood glue and screws.
Apply a layer of fibreglass to the sides and top of the raised cover, again following the instructions provided with your fibreglass kit. Allow the fibreglass to harden completely before sanding any imperfections with medium grit sandpaper.
Finally, drill 1-inch ventilation holes along the upper edges of the cover, approximately 6 inches apart and 3 inches below the surface. Your fibreglass and marine hardware engine cover is now complete and ready to be set in place over your boat's engine.
Remember to wear a dust mask and safety glasses when sanding fibreglass to protect yourself from any harmful fibres or particles.
Boat Race Results: Lock Haven's Dash for Cash
You may want to see also
Sewing it together
Sewing a boat engine cover together requires a lot of preparation and the right tools. You will need a sewing machine, such as the Sailrite Ultrafeed LSZ-1, which offers both straight and zigzag stitching. A powerful motor and cogged belt drive will prevent slippage and stalling. A "walking presser foot" is also important as it grips the fabric and moves bulky seams past the needle.
For the fabric, Sunbrella acrylic is a good choice as it is breathable, helping to combat mould, and is resistant to UV rays, water, and mildew. It doesn't shrink or stretch and is pliable, making it easy to handle during the sewing process. It is also good for beginners as both sides are identical, so you don't have to worry about which side is the "inside" or "outside". You will also need sturdy thread, such as V-69 polyester sailmaker's thread, which is high-strength and resistant to sunlight, saltwater, and mildew.
Before you start sewing, practice on scrap material to get a feel for controlling the speed of the machine and sewing straight lines. Learn how to use forward and reverse to over-stitch the thread at the start and end of a seam. Chalk is a good marking tool as it stays on when you need it to and rubs off when you don't. You can also use double-sided basting tape to hold seams together as you sew, but be aware that it can gum up some needles.
When you are ready to start sewing, begin by sewing the 3 main pieces together first. After sewing the first time, use a technique called "top stitching", where you hold the seam down and sew over it again. Then, sew on the rectangular pieces that will be folded in half to create two layers, and then sew these to the appropriate seams on the main pieces. Leave these pieces extra-long and sew them on 90% of the way, then fold and cut the excess before finishing the seam. This reduces the need for precision in cutting and sewing. Sew on the zipper, being careful to leave enough space to be able to zip it later.
Next, sew on the edge skirting, which are very long pieces. You can make a sub-assembly by flipping the bottom seam up and sewing it, then sewing the two sides over. Sew these onto the main pieces, leaving them a foot too long, and then shorten them as needed. Sew a bungee cord into the bottom skirt, folding the bottom skirt up about 2 inches to make a pocket for the bungee. Add some small reinforcement pieces in the rear corners to prevent the corners of the boat from wearing through. Sew a reinforcement in the middle of the cover to hold it up using a halyard so that water flows off of it and doesn't puddle on the boat.
Finally, sew a small piece of velcro to the strip going around the mast. At this point, you are finished with the sewing and can move on to finishing the bungee and adding snaps.
Repairing Cosmetic Boat Damage: A Step-by-Step Guide
You may want to see also
Creating a pattern
- Taking Measurements: Begin by taking accurate measurements of the engine compartment. Measure the width and length of the opening above the engine, considering any necessary deductions for the type of cover you plan to create (flush or raised). These measurements will serve as the basis for your pattern.
- Preparing the Pattern Material: Use a large piece of pattern material, such as Tyvek®, heavy craft paper, or plastic. Spread it out flat on a work surface, ensuring it is smooth and free of creases. You will be transferring the measurements from step 1 onto this material to create your pattern.
- Transferring Measurements: Using a ruler or a straight edge, carefully mark the dimensions of the engine compartment onto the pattern material. Add any necessary allowances for seams, hems, or other features, such as those suggested in the sources. You may also want to add extra material for adjustments, as it is better to have a slightly larger pattern than one that is too small.
- Cutting and Refining: Cut out the pattern pieces from the material. At this stage, you may want to label each piece to ensure proper assembly later on. Refine the edges of the pattern pieces to ensure they are smooth and accurate. You can use a sharp craft knife or scissors for this step.
- Darts and Adjustments: Depending on the shape of your engine compartment, you may need to create darts or adjustments in your pattern. Darts are folds or tucks in the pattern material that help it conform to the contours of the engine compartment. Mark the locations for darts, following the curve of the engine cover, and make creases or folds as needed. This step may require some trial and error to achieve a snug fit.
- Finalizing the Pattern: Once you are satisfied with the fit of the pattern, including any necessary darts, transfer the pattern to a fresh piece of material. Make any necessary adjustments to ensure the pattern lies flat and true. Label all pieces and make notes on the placement of darts or other adjustments.
Zolatone Coating for Aluminum Boats: Best Product Options
You may want to see also
Installing snaps and poles
When installing snaps and poles for a boat engine cover, there are a few different approaches you can take, depending on your preferences and the materials you are working with. Here is a step-by-step guide:
Preparing the Cover
Before you begin installing snaps, it is important to prepare the canvas cover. This involves reinforcing the area where the snap will be installed to ensure it can withstand the stress without ripping. If you are working with a canvas cover, you can reinforce the area by sewing on a patch. Mark the spot where you will be installing the snap, and use a sharp pencil or chalk to outline the fastener. This will guide you during the installation process.
Installing Snaps
The most common type of boat snap is the Dot® Fastener. To install this type of snap, you will need a snap setter tool. While there are a variety of tools available, professionals typically use the Pres-n-Snap® tool built by Hoover. This tool is designed to provide a professional-grade crimp for your snaps. Other options include anvil-style set tools and vice grip tools, which can be quicker and require no hammering.
When installing the snaps, follow the instructions provided with your chosen tool. Ensure that the snaps are securely attached to the cover, as they will need to withstand some stress when fastening the cover to the boat.
Installing Poles
Boat cover support poles are essential to prevent water from pooling on the cover. Adjustable aluminum poles are a popular choice, as they can be collapsed for easy storage and adjusted to the desired height. When installing the poles, consider the type of base you will need. Options include a rubber boot base for a small footprint or a larger round pyramid base for added stability. The base can also be enlarged by screwing it into the deck or another stable surface using the included stainless steel base screws.
To enhance the stability of the poles, consider using straps. Some pole sets come with straps, while others may require you to purchase them separately. The straps help to keep the poles upright, especially during high winds or when putting the cover on. For larger boats or in areas with strong winds, multiple poles and straps may be necessary.
By following these steps and choosing the appropriate tools and materials, you can successfully install snaps and poles for your boat engine cover, ensuring a secure and water-resistant fit.
Finding the Boat Key: RE8's Essential Item Locations
You may want to see also
Finishing touches
Once you've completed the basic structure of your engine cover, it's time to add the finishing touches! Here are some detailed instructions to guide you through the process:
Sewing and Snaps
Use a heavy-duty single stitch machine or an industrial straight stitch machine to sew the pieces of your engine cover together. Start by sewing the three main pieces together, using a "top stitching" technique where you hold the seam down and sew over it again. Next, sew the bow and shroud snap edges, followed by the zipper flap edges. Remember to use a quality 18-20 size needle to prevent bending or breaking during sewing.
Zipper Installation
When installing the zipper, pay attention to the direction of your stitching to ensure the zipper will function properly. Sew about 5 or 6 inches of the zipper, then bury the needle, lift the foot, and pass the zipper pull under the foot to the already sewn area. Finish sewing the remainder of the zipper.
Edge Skirting
Sew the edge skirting onto the main pieces. These pieces can be quite long, so you may want to create sub-assemblies by flipping the bottom seam up and sewing it first, then sewing the two sides. The skirting pieces will likely be a foot or so too long, so you can shorten them as needed.
Bungee Cord Installation
Sew a bungee cord into the bottom skirt of the cover. Fold the bottom skirt up about 2 inches to create a pocket for the bungee. You can use 1/4 inch bungee cord and attach bungee hooks and stainless steel rings at the bow and side shrouds. Leave some extra bungee cord for now, as you will adjust the tension later.
Snaps and Poles
Install snaps at each shroud, the mast, and above and below the zipper. You can use a snap fastener tool or pliers to attach them. Additionally, install adjustable support poles in the interior to prevent water pooling on the cover.
Final Adjustments
Finally, put the cover on your boat and adjust the bungee cord tension to ensure a snug fit. Congratulations, you've now completed your engine cover!
Fixing a Boat: Is It Really That Challenging?
You may want to see also
Frequently asked questions
You will need a fiberglass kit, a belt sander with medium-grit sandpaper, stainless steel butt hinges, a cordless drill with a screw tip attachment, stainless steel bolts with flat washers and nuts, and 3/4-inch marine-grade plywood.
Measure the width and length of the opening above the engine. Deduct 5/8 inch from each measurement for fiberglass.
Cut a piece of plywood to the corrected measurements as the fiberglass mold. Apply three layers of reinforced fiberglass to the surface and sides of the plywood mold. Allow the fiberglass to harden and remove the plywood mold. Sand the rough edges and surface of the fiberglass cover. Position the stainless steel butt hinges along one edge of the cover and drill pilot holes for the stainless steel bolts. Insert the bolts and tighten with washers and nuts.
For a flush cover, finish with a non-slip deck surface. For a raised cover, finish with auto primer and paint.