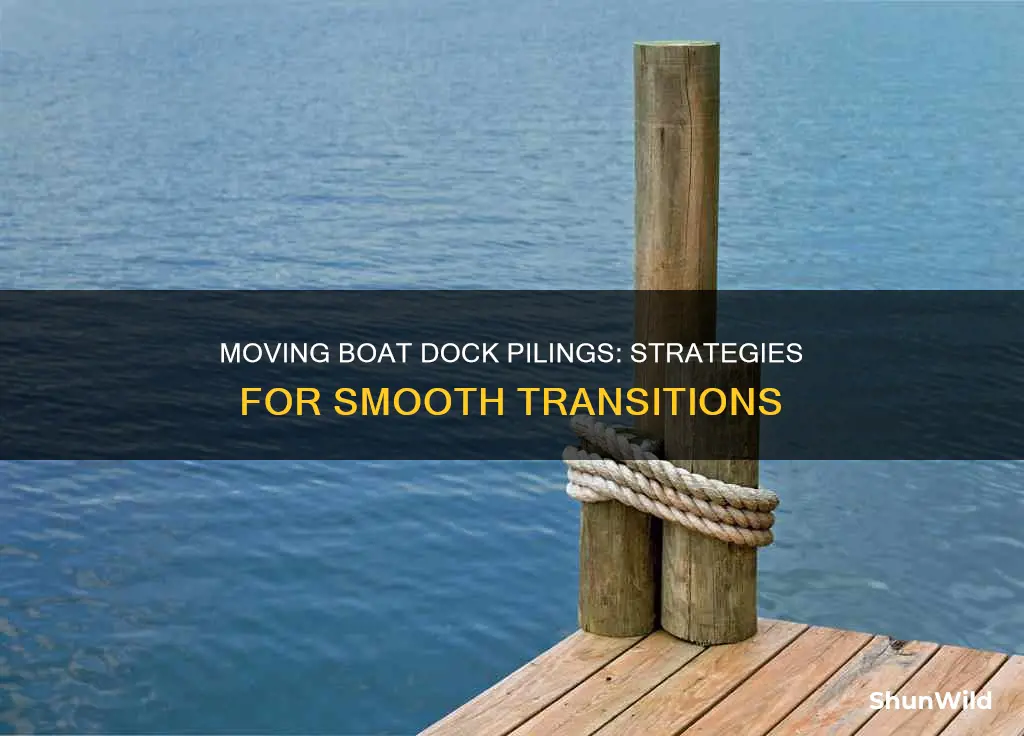
Dock pilings are essential for any waterfront infrastructure, providing support and acting as a foundation for piers, docks, and other structures. They are usually large posts or poles driven deep into the ground to create a stable and strong foundation. The process of installing dock pilings involves choosing the appropriate material, such as wood, concrete, PVC, or steel, and determining the required depth and spacing. The installation method can vary, including using water jets to dig holes or setting the pilings in concrete footers. Proper maintenance and replacement of dock pilings are crucial to ensure the safety and longevity of the waterfront structure.
Characteristics | Values |
---|---|
Purpose | Support and anchor piers, docks, and other waterfront materials |
Type of Support | Vertical |
Materials | Wood, concrete, PVC, steel, aluminium, plastic-coated wood |
Environmental Considerations | Water salinity, water depth, water currents, weather conditions |
Installation Method | Driven into the ground, set in concrete footers |
Maintenance | Replace pilings when they are bad to avoid collapsing the structure |
What You'll Learn
Using a water jet to move boat dock pilings
Water jets are a useful tool for installing dock posts in water, also known as pilings. This method is best used in sandy soil, as it involves using a high-powered water pump to blast away the sand and silt from underneath the piling, allowing it to sink into the ground. Here's a step-by-step guide on how to use a water jet to move boat dock pilings:
Step 1: Prepare the Pilings
Choose pressure-treated wood pilings that are round and cut to the appropriate height. The pilings should be tall enough to hold the dock 3-4 inches (7.6-10.2 cm) above the water, taking into account the highest water level due to tides, flooding, or heavy rainfall. Cut the pilings a little longer than needed, as you can always trim them later.
Step 2: Gather Your Tools
Rent a water jetter, also called a hydro jet, from a home improvement store. A water jetter with a 2-3 inch (5.1-7.6 cm) diameter hose will work well. Alternatively, you can use a power washer or a high-pressure garden hose, but the process may take longer. You will also need spray paint to mark the pilings at 12-inch (30 cm) intervals to monitor their depth.
Step 3: Position the First Piling
Stand the first piling in the desired spot in the water and push it a few inches into the lakebed. If possible, enlist the help of a few strong people to hold the piling in place. If the lakebed is hard or compact, use the water jetter to create a starter hole by aiming the jet at the bottom of the piling and turning on the pump.
Step 4: Use the Water Jet to Sink the Piling
With the piling in position, aim the water jetter at the bottom of the piling and turn on the pump. The force of the water will push the sand and silt out from under the piling, allowing it to sink. Guide the piling down into the ground until you reach the desired depth. If needed, attach a PVC pipe with a 1-inch (2.5 cm) diameter to the end of the hose to increase the water pressure.
Step 5: Stabilize the Piling
Once the piling has reached the desired depth, use the water jetter to push some of the dirt back around the piling to stabilize it. This step will help ensure that the piling remains securely in place.
Step 6: Repeat for Remaining Pilings
Repeat the process for the rest of your pilings, making sure to maintain consistent depth by marking them with spray paint.
Bottom Painting a Triumph Boat: A Step-by-Step Guide
You may want to see also
Attaching a floating dock to fixed pilings
Firstly, you need to determine the number and type of pilings required. Typically, three pilings set 10 feet apart are used to attach a 30' x 4' floating dock. The type of pilings can vary, with common options being wood, concrete, PVC, and steel. It is important to consider the environmental conditions, such as water salinity, depth, currents, and weather conditions, when selecting the appropriate piling material.
Once you have the required number of pilings, they need to be securely installed. This involves pounding the pilings into the seafloor or lake/river bed. Ensure that the pilings are deep enough to provide stable support for your floating dock.
Now, you can move on to attaching the floating dock to the pilings. There are several methods available, each with its advantages:
- Piling Hoop Bracket: This method utilizes a hoop bracket that slips over the piling. The bracket has pile rollers that are two inches larger than the piling diameter to prevent binding. It is affordable and durable but may not be suitable for scenarios where slide assemblies are required.
- Piling Slide Assembly: This method provides incredible stability by fixing an inner tube to each piling and an outer tube to the floating dock, allowing independent movement. It requires two pilings that cannot be set wider than the dock width.
- Seawall Slide Assembly: Similar to the piling slide assembly, but the inner tubes are affixed to an existing seawall instead of pilings.
- Small Slide Assembly: In this method, the inner tubes are affixed to an existing floating dock, which can be useful for attaching a low-profile floating dock to a higher-profile one.
- Aluminum Floating Dock Piling Hoop Bracket: This method is similar to the standard Piling Hoop Bracket but specifically uses aluminum as the material for the bracket.
When attaching the floating dock, it is crucial to consider the water levels. Measure the water level at maximum high and low tides to ensure that the floating dock is attached accordingly, allowing for vertical movement while limiting side-to-side movement.
Additionally, you can enhance the stability of your floating dock by adding weights, attaching it to the shore with gangways or ramps, or constructing a roof over the dock for extra weight.
By following these steps and choosing the appropriate attachment method, you can securely attach your floating dock to fixed pilings, ensuring its longevity and safe use.
Radar Style Guide for Boats: Choosing the Best Fit
You may want to see also
Choosing the right materials for pilings
Natural marine timber is a traditional choice for docks, but not all wood types are suitable. To withstand constant submersion in water, the wood must be either pressure-treated or made of a naturally water-resistant hardwood. Treated softwood, such as pine, is a popular choice due to its affordability and customizability, but it is susceptible to decay and marine pests. Hardwoods like Greenheart, redwood, fir, and cedar are naturally resistant to water and rot and do not require pressure treatment. However, they may need to be pre-cut and pre-drilled, and some hardwoods are too hard for standard DIY tools.
Synthetic materials, on the other hand, tend to require less maintenance and are often more durable. Fiberglass composite pilings, for example, are engineered to never rot, rust, or crumble and are ideal for low-maintenance docks. Concrete pilings, made of reinforced concrete, are resistant to decay and corrosion and are commonly used for commercial and industrial applications due to their strength and durability. However, concrete may not be the best choice for residential docks due to its appearance and installation challenges.
When selecting the right material for pilings, several factors must be considered, including environmental conditions such as water salinity, depth, and currents, as well as weather conditions and load capacity requirements. For instance, in areas with strong water currents, pilings made of steel or concrete may be more suitable as they provide a more durable foundation. Additionally, the weight of the dock and boats will determine the necessary load capacity, with wood and PVC suitable for lighter loads and concrete and steel better equipped for heavier loads.
The budget is also an essential consideration, as some materials, such as PVC and wood, are generally more affordable than metal and concrete. It is crucial to factor in not only the material costs but also the installation costs and expected lifespan of the pilings.
The Yacht's Name in Captain Ron: Unveiling the Mystery
You may want to see also
Maintaining and replacing pilings
Dock pilings are an important investment for any waterfront infrastructure. They provide support and act as a foundation for other structures and vessels. Therefore, it is crucial to regularly clean and maintain them.
- Routine and post-event inspections: Conduct annual routine inspections to record the condition of pilings, stringers, and hardware. This helps establish a baseline to monitor deterioration and perform timely maintenance. Post-event inspections are done after damaging events like hurricanes or collisions to assess the dock's integrity. While certified commercial divers can be hired for inspections, it is also possible to handle them independently.
- Removing marine growth: Pilings may appear new from the surface, but marine growth can hide severe damage underneath. Use tools like a hammer claw, spade shovel, or heavy-duty taping knife to remove oysters and barnacles.
- Checking for hardware damage: With clean pilings and bracings, inspect hardware for tightness, corrosion, and missing or protruding fasteners. Look for tiny holes from burrowing invertebrates, indicating marine borer activity.
- Addressing marine borer infestation: Marine borers, such as shipworms, pholads, gribbles, and pill bugs, can cause significant damage to pilings. If borer activity is minimal, wrapping the piling with vinyl will kill the infestation and prevent further attacks. For extensive damage, concrete jacketing can be used by encasing the piling with PVC and filling it with concrete.
- Piling replacement: If pilings are severely damaged or deteriorated, replacement may be necessary. Timber pilings can be replaced with new timber wrapped in vinyl or composite pilings made from vinyl or fiberglass.
- Seawall and bulkhead maintenance: During dock maintenance, also inspect the seawall or bulkhead for signs of cracking, corrosion, or sinkholes. Clean weepholes annually to prevent clogging and ensure proper flow.
- Identifying "fuzzy wood" and fungal decay: Saltwater penetration can cause "fuzzy wood," which appears as salt residue expanding and damaging the wood. While this is unsightly, it is not a cause for immediate concern. However, fungal rot can lead to structural failure, with wood appearing dark and brittle or bleached and spongy.
- Bottom surveys and debris removal: The sea bottom can change due to weather, tides, and currents, leading to underwater hazards. Certified divers can help identify and remove debris like submerged pilings, tree limbs, or heavy litter to ensure swimming and boating safety.
- Routine inspections: The American Society of Civil Engineers recommends routine inspections every four to five years, depending on the material of the pilings. However, inspections should be more frequent based on deterioration, anticipated use, and potential storm damage.
Launching a Boat: Like a Boss, in Easy Steps
You may want to see also
Selecting the right piling type for environmental conditions
- Water salinity: The choice between saltwater and freshwater can impact the durability of different piling materials. For example, saltwater is more corrosive than freshwater, which can lead to the degradation of materials like wood or steel. In such cases, PVC or fibreglass pilings are more suitable due to their higher corrosion resistance.
- Water depth: The depth of the water body is crucial when choosing the proper piling type. The length and diameter of pilings depend on the water depth, and different materials have varying capacities to bear loads. Concrete and steel pilings, for instance, are better suited for deeper waters and heavier loads.
- Water currents: Water currents can affect the stability of a dock, and stronger currents require pilings to be driven deeper into the earth. Steel or concrete pilings are more appropriate choices for areas with strong currents as they offer a more durable foundation.
- Weather conditions: The severity and frequency of storms, high winds, and large waves can damage pilings, especially if the material used is not sturdy enough. Steel or concrete pilings are more resilient against harsh weather conditions compared to wood or PVC.
- Load capacity: The weight of the dock, boats, and any other equipment must be carefully considered. While wood and PVC can handle lighter loads, concrete and steel pilings are designed for heavier weights.
- Soil condition: The type of soil beneath the waterbody matters. Soft soil provides less support compared to hard soil. If you want to increase the load capacity, opt for constructing your dock pilings on hard, solid soil.
- Environmental impact: Piling can affect the surrounding ecosystem, particularly in terms of noise, vibration, and ground disturbance. To minimise these effects, choose low-impact methods such as Continuous Flight Auger (CFA) piles, which produce less noise and vibration.
- Regulations and standards: Ensure that your chosen piling method complies with local regulations and standards. Some environmental regulations may require the use of environmentally friendly materials, such as PVC or fibreglass, to reduce the impact on the ecosystem.
Installing Flooring in Your Inflatable Boat: A Step-by-Step Guide
You may want to see also
Frequently asked questions
Boat dock pilings are usually secured by ropes or concrete. To move them, you will need to either untie the ropes or cut through the concrete.
If your boat dock pilings are secured by ropes, you will need to untie them. If they are secured by concrete, you will need to use a power tool such as a reciprocating saw to cut through the concrete.
Boat dock pilings are usually made of wood, concrete, PVC, or steel.
If you can see the pilings from the dock, you will be able to tell if they are secured by ropes or concrete. If you cannot see the pilings, you may need to feel around the base of the pilings to determine the type of securing mechanism.
If your boat dock pilings are secured by both ropes and concrete, you will need to first untie the ropes and then cut through the concrete using a power tool such as a reciprocating saw.