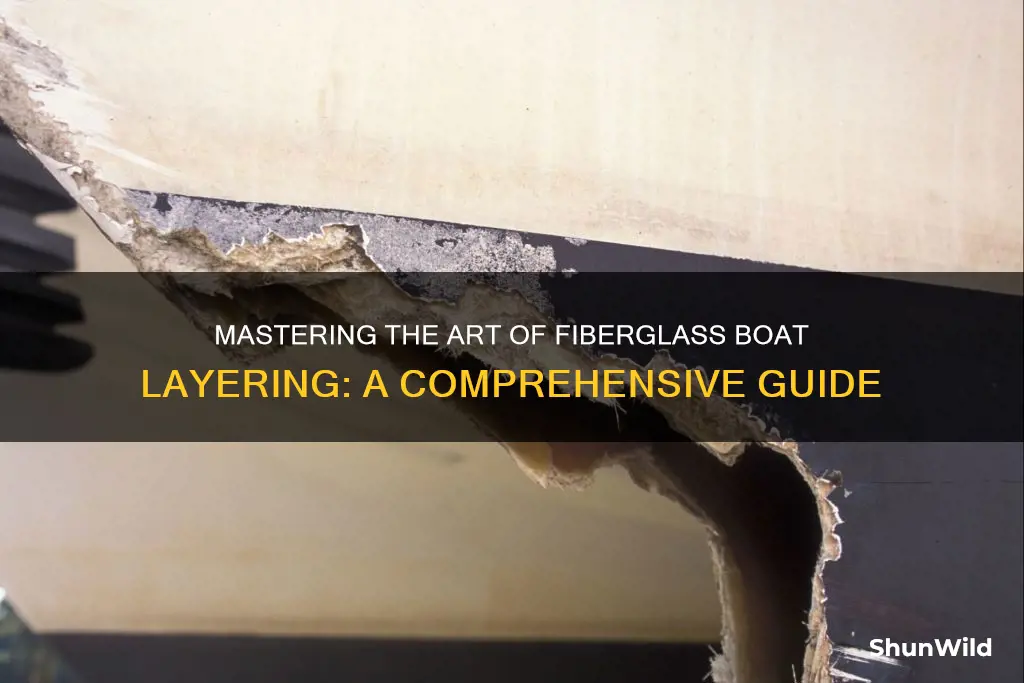
Layering fiberglass is a crucial step in boat construction, requiring precision and attention to detail. This process involves carefully applying multiple layers of fiberglass cloth and resin to create a strong, lightweight structure. Each layer must be meticulously prepared, ensuring proper adhesion and alignment, and the entire process demands a steady hand and a keen eye for detail. Understanding the techniques and materials involved in layering fiberglass is essential for creating a durable and aesthetically pleasing boat hull.
What You'll Learn
- Preparation: Clean and prepare the surface for optimal bonding
- Material Selection: Choose the right fiberglass type and thickness
- Laying Technique: Apply layers evenly, starting with a base coat
- Reinforcement: Use glass tape for added strength and structural support
- Finishing: Sand and fair for a smooth, professional finish
Preparation: Clean and prepare the surface for optimal bonding
Before you begin the process of layering fiberglass onto your boat, proper preparation is crucial to ensure a strong and durable bond. The key to a successful repair or reinforcement is a clean and smooth surface that promotes optimal adhesion. Here's a step-by-step guide to preparing the area for the fiberglass application:
Step 1: Remove Old Material (if applicable)
If you're repairing an existing fiberglass structure, the first step is to carefully remove any damaged or old fiberglass layers. This process, known as "peeling back," requires patience and precision. Use a sharp utility knife or a specialized fiberglass removal tool to carefully lift and peel away the old material. Ensure you don't damage the underlying structure or create new imperfections. It's essential to work systematically, following the direction of the existing layers to avoid uneven removal.
Step 2: Clean the Surface
Once the old fiberglass is removed, thorough cleaning of the surface is necessary. Start by rinsing the area with a high-pressure water spray to remove any loose debris and contaminants. Then, use a mild detergent or a specialized fiberglass cleaner to wash the surface. Ensure you scrub the entire area to remove any dirt, grease, or old adhesive residue. Rinse thoroughly with clean water to eliminate any cleaning product residue. The goal is to create a clean, grease-free surface that will allow the fiberglass to bond effectively.
Step 3: Inspect and Repair
After cleaning, inspect the prepared surface for any remaining imperfections or damage. Fill any holes or gaps with a suitable fiberglass repair compound or putty. Smooth it out and ensure it is level with the surrounding surface. Allow the filler to cure according to the manufacturer's instructions. This step is vital to creating a seamless and structurally sound foundation for the fiberglass layers.
Step 4: Sanding and Etching
Sanding the surface is essential to create a rough texture that will enhance bonding. Use fine-grit sandpaper (e.g., 600-grit) to gently sand the entire area, removing any remaining smooth surfaces. This process etches the glass fibers into the surface, providing a mechanical bond. Ensure you work in a well-ventilated area and wear protective gear, as fiberglass dust can be inhaled. After sanding, wipe away any dust with a damp cloth to ensure a clean surface before the next step.
By following these preparation steps, you'll create an ideal environment for the fiberglass to bond securely, ensuring a strong and long-lasting repair or reinforcement for your boat. Proper preparation is often the most critical aspect of a successful fiberglass project.
Boston Bomber's Boat Hideout: What Happened?
You may want to see also
Material Selection: Choose the right fiberglass type and thickness
When it comes to layering fiberglass for a boat, material selection is a critical aspect that can significantly impact the boat's performance, durability, and overall appearance. The right choice of fiberglass type and thickness will ensure a strong, lightweight, and aesthetically pleasing structure. Here's a detailed guide on how to choose the appropriate materials for your boat's fiberglass layers:
Fiberglass Types:
- E-Glass (E-Glass Fiberglass): This is the most common and widely used type of fiberglass. E-Glass offers excellent strength and stiffness, making it ideal for structural applications. It is versatile and can be used for both hull and deck construction. E-Glass fibers are typically combined with a resin system to create a strong and durable composite material.
- S-Glass (S-Glass Fiberglass): S-Glass is known for its exceptional strength and flexibility. It is often used in high-performance boats and applications requiring superior impact resistance. S-Glass fibers have a higher modulus of elasticity, providing excellent structural integrity. However, it is more expensive than E-Glass and may not be necessary for all boat projects.
- AR-Glass (Aramid Fiberglass): Aramid fibers, such as Kevlar, offer an incredible strength-to-weight ratio. They are lightweight and provide excellent impact and abrasion resistance. AR-Glass is often used in specialized boat applications, such as racing boats or areas requiring impact protection.
Choosing the Right Thickness:
The thickness of the fiberglass layers is a crucial consideration. It determines the boat's structural integrity and its ability to withstand various loads and environmental conditions. Here's a breakdown:
- Hull Construction: For the hull, a combination of E-Glass and S-Glass is often used. A thicker layer of E-Glass (around 0.0625 to 0.125 inches) provides structural strength, while S-Glass can be used in specific areas for added impact resistance. The thickness may vary depending on the boat's size and intended use.
- Deck and Superstructure: The deck and superstructure typically require a thinner layer of fiberglass. A thickness of around 0.03125 to 0.0625 inches is common. This thinner layer provides protection and adds structural integrity without adding excessive weight.
- Reinforcement: In areas requiring additional strength, such as stringers, bulkheads, or step areas, consider using thicker layers or reinforcing with additional layers of fiberglass. This ensures the boat's structural integrity in critical areas.
When selecting the fiberglass type and thickness, consider the boat's design, intended use, and environmental factors. Consulting with experienced boat builders or fiberglass specialists can provide valuable insights to ensure the best material choices for your specific project. Remember, the goal is to create a lightweight, strong, and durable boat structure that meets your performance and aesthetic requirements.
Boat Wash: Choosing the Best for Your Vessel
You may want to see also
Laying Technique: Apply layers evenly, starting with a base coat
When preparing to lay fiberglass for a boat, one of the most critical steps is ensuring that the layers are applied evenly and with precision. This process begins with a base coat, which serves as the foundation for the entire structure. Here's a detailed guide on how to achieve this:
Start by preparing the surface of the boat where the fiberglass will be applied. Ensure the area is clean, smooth, and free from any debris or contaminants. Repair any existing damage or imperfections to create a solid base. The key to a successful layup is a well-prepared surface that allows the fiberglass to bond effectively.
Now, it's time to apply the base coat. This initial layer is crucial as it provides the initial strength and structure to the boat. Use a high-quality epoxy resin specifically designed for marine applications. Carefully follow the manufacturer's instructions for mixing and application. Start by brushing the resin onto the prepared surface, ensuring complete coverage. Pay attention to the edges and corners, as these areas require extra care and precision.
As you apply the base coat, maintain a consistent thickness across the entire surface. Aim for a smooth, even layer without any visible brush marks. This initial layer acts as a barrier, preventing the subsequent layers from sticking to the underlying surface, which can lead to imperfections. Allow the base coat to cure according to the manufacturer's guidelines, ensuring it reaches the required hardness before proceeding.
Once the base coat is cured, inspect the surface for any imperfections or areas that require additional work. This is the time to make any necessary adjustments, ensuring the surface is ready for the next layer. Remember, the goal is to create a seamless and structurally sound boat, so attention to detail at this stage is essential.
Boat Rides in Niagara Falls: October Operations?
You may want to see also
Reinforcement: Use glass tape for added strength and structural support
When it comes to reinforcing the structural integrity of a boat with fiberglass, one of the most effective techniques is the use of glass tape. This method is particularly useful for adding strength and support to specific areas that may require additional reinforcement, such as joints, seams, or areas prone to stress. Glass tape, also known as fiberglass tape, is a versatile material that can be easily layered onto the existing fiberglass structure to provide a strong and durable bond.
The process of using glass tape for reinforcement involves carefully applying the tape to the desired areas, ensuring that it is properly aligned and secured. It is important to use a tape that is specifically designed for marine applications, as it will have the necessary adhesive properties and flexibility to withstand the harsh marine environment. Before applying the tape, it is recommended to clean the surface thoroughly to remove any dirt, grease, or old adhesive residue. This ensures a strong bond between the tape and the existing fiberglass.
Start by cutting the glass tape to the appropriate length and width, allowing for some excess to facilitate the layering process. Begin by applying a thin layer of epoxy resin over the area to be reinforced, ensuring complete coverage. Then, carefully lay the glass tape onto the resin, starting from one end and working your way to the other. Use a rolling pin or a similar tool to smooth out any air bubbles and ensure a tight bond between the tape and the resin. Repeat this process, layering the tape in multiple directions to create a strong and reinforced structure.
For optimal results, it is crucial to follow the manufacturer's instructions for the specific glass tape being used. Different tapes may have varying application techniques and curing times. Properly curing the glass tape layers is essential to achieve the desired strength and structural support. After the initial cure, additional layers of tape can be applied to further enhance the reinforcement, especially in high-stress areas.
By incorporating glass tape into your fiberglass boat construction or repair, you can significantly improve the overall strength and durability of the vessel. This method allows for targeted reinforcement, ensuring that specific areas receive the necessary support without adding excessive weight. Remember, proper preparation, precise application, and adherence to manufacturer guidelines are key to achieving a successful and long-lasting reinforcement using glass tape.
The Maverick Crab Boat: What Went Wrong?
You may want to see also
Finishing: Sand and fair for a smooth, professional finish
When it comes to finishing the fiberglass layers on your boat, achieving a smooth and professional-looking surface is essential. This process involves careful sanding and fairing techniques to ensure a seamless and aesthetically pleasing result. Here's a detailed guide on how to achieve that flawless finish:
Sand and Smoothen: After the fiberglass layers are applied and cured, it's time to start the finishing process. Begin by using a coarse-grit sandpaper (around 40-60 grit) to remove any excess resin, air bubbles, or imperfections from the surface. This initial sanding will create a rough texture, preparing the surface for further refinement. Work in small sections, gently rubbing the sandpaper over the fiberglass, following the natural curves and contours of the boat's shape. Rinse the boat periodically to remove sand dust and ensure a thorough clean. After this initial sanding, rinse the boat thoroughly to remove any debris and dry it completely.
Fine-Grit Sanding: Proceed with a finer-grit sandpaper (100-150 grit) to refine the surface further. This step will create a smoother and more even texture, ready for the final fairing. Again, work in small sections, applying gentle pressure to avoid damaging the fiberglass. Pay close attention to any areas where the fiberglass layers meet or intersect, as these spots may require extra care. You can also use a power sander with a fine-grit disc for faster and more efficient sanding, especially on larger surfaces. Ensure you wear protective gear, including a dust mask and safety goggles, during this process.
Fairing for a Professional Finish: Fairing is a crucial step to achieve a smooth and professional finish. It involves shaping and smoothing the surface using various tools and compounds. Start with a fairing compound, which can be a liquid or a paste, and apply it to the sanded surface. Use a putty knife or a fairing tool to spread the compound evenly, following the direction of the fiberglass weave. Then, use a smooth, damp cloth or a fairing pad to gently rub the compound, removing any high spots and creating a seamless transition between the layers. This process requires patience and a keen eye for detail.
Final Touches: Once the fairing is complete, inspect the surface closely. Use a fine-grit sandpaper (180-220 grit) to remove any remaining imperfections and create a smooth, glossy surface. This final sanding will prepare the fiberglass for painting or further customization. After sanding, wipe down the entire boat with a clean, damp cloth to remove any residue and ensure a pristine base for the next steps in your boat's customization journey.
Remember, the key to a successful finish is patience and attention to detail. Take your time with each step, and don't rush the sanding and fairing processes. This will ensure a professional-grade result that showcases the beauty of your boat's fiberglass construction.
Exploring the Docking Locations of Dexter's Boat
You may want to see also
Frequently asked questions
Proper surface preparation is crucial for a successful fiberglass repair or installation. Start by thoroughly cleaning the area to remove any dirt, grease, or old paint. Use a wire brush or sandpaper to roughen the surface, creating a key for the fiberglass to adhere to. Fill any holes or imperfections with a suitable filler, such as epoxy or polyester resin, and sand it smooth once cured. Ensure the surface is dry and free of any contaminants before proceeding.
The choice of fiberglass depends on various factors, including the structural requirements, environmental conditions, and aesthetics. For structural applications, consider using woven fiberglass cloth, which provides excellent strength and durability. For cosmetic purposes or areas with less structural demand, you can opt for non-woven or mat fiberglass, which offers a smoother finish. Always refer to the manufacturer's guidelines and select the appropriate thickness and type of fiberglass for your specific project.
Achieving a smooth finish is essential for the overall appearance and performance of the boat. Start by applying a thin layer of resin as a primer to the prepared surface. Then, carefully lay the fiberglass cloth, ensuring it is properly saturated with resin and smooth against the surface. Use a rolling pin or a tool to remove any air bubbles and wrinkles. Build up the layers gradually, allowing each layer to cure before adding more, to avoid any imperfections. Practice good craftsmanship and take your time to achieve a professional-looking result.