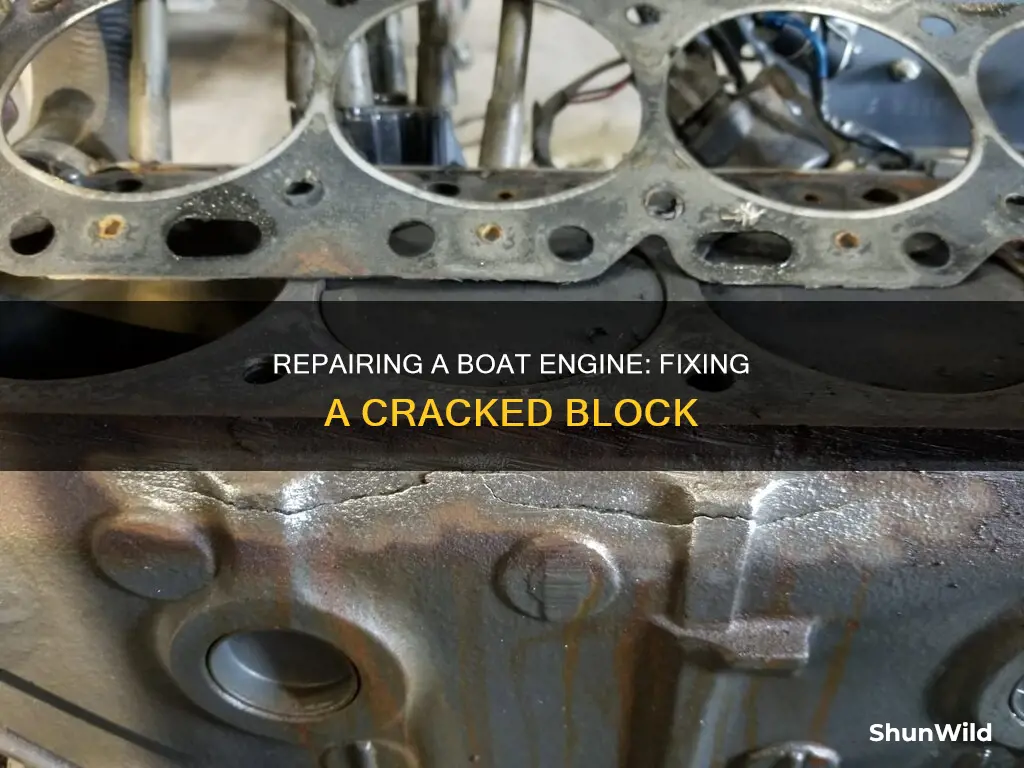
A cracked engine block on a boat can hinder its performance and cause several issues, including engine smoke, overheating, and compromised performance. While some people have had success using JB Weld or other epoxies to seal external cracks, this is not always effective for internal cracks or high-pressure areas. For a proper repair, it is recommended to replace the block or get a new engine. However, if the crack is not too severe, repairs such as pinning, gluing, and welding can be done by a professional to seal the damage and prevent coolant or oil leaks.
Characteristics | Values |
---|---|
Signs of a cracked engine block | Visible engine smoke, overheating of the engine, compromised performance |
Cause of a cracked engine block | Excess heat, poor storage, malfunctioning water pump, manufacturer error |
Fix for a cracked engine block | Pinning, glueing, welding, replacement block, new engine |
What You'll Learn
Welding a cracked block
Welding a cracked engine block is a challenging task and should be done with caution. It is important to note that welding is not always the best method to fix a cracked engine block, and in some cases, it may be more feasible to replace the block or engine altogether. However, if the crack is accessible and not too severe, welding can be a viable option. Here is a step-by-step guide on how to weld a cracked engine block:
Step 1: Clean and Prepare the Surface
Before beginning the welding process, it is crucial to clean and prepare the surface of the engine block. Use a grinding or sanding disk to create a bright, shiny surface around the crack. This will ensure optimal penetration of the weld. Make sure to remove any oil, grease, or contaminants from the area to be welded.
Step 2: Pre-heat the Engine Block
Gently pre-heat the engine block before welding. This step is important as it helps remove moisture from the cast iron, preventing pinholes and porosity in the weld. Preheating also reduces the risk of thermal shock, which can cause the metal to crack further. Use a propane torch or other suitable heating equipment to gradually heat the area around the crack.
Step 3: Drill Holes at the End of the Crack
To prevent the crack from propagating further, it is recommended to drill holes at the ends of the crack. This technique, known as "drilling stop holes," provides a mechanical barrier that stops the crack from growing and helps to relieve stress in the metal.
Step 4: Set Up Your Welding Equipment
Ensure you have the appropriate welding equipment and consumables for welding cast iron. A standard arc welder can be used, along with cast iron welding rods, such as Muggy Weld 77 or similar products. Set your welding machine to the recommended amperage settings for cast iron welding.
Step 5: Begin Welding
Start the welding process by tack welding a mild steel plate over the crack to provide additional support. Weld side to side, moving along the crack, to prevent the cast iron from overheating. Ensure that you weld past the ends of the crack to ensure that there are no cracks at the start or end of the weld.
Step 6: Monitor the Welding Process
Keep a close eye on the welding process and adjust your amperage as needed. If the welding rod undercuts, turn down the amperage. If the rod appears ropey or lacks penetration, increase the amperage. It is crucial to maintain a consistent weld pool and avoid overheating the cast iron.
Step 7: Post-weld Cleaning and Inspection
After completing the weld, allow the engine block to cool gradually. Clean the welded area to remove any slag or spatter. Inspect the weld closely to ensure that it is strong and free of defects. You can also magnaflux the block to check for any cracks or imperfections.
Remember, welding a cracked engine block is a complex task and should only be attempted by those with the necessary skills and experience. If you are unsure, it is always best to consult a professional engine repair specialist.
Bass Boat Capacity: How Many People Can Fit Comfortably?
You may want to see also
Using epoxy to seal cracks
If you notice any of the symptoms of a cracked engine block, such as visible smoke in the cabin, engine overheating, compromised performance, or an oil or coolant leak, you should take immediate action to prevent further damage. While not all cracks are repairable, you can try to seal minor cracks with epoxy to prevent coolant or oil leaks. Here are some detailed instructions on using epoxy to seal cracks in your boat engine block:
Step 1: Clean and Prepare the Surface
Before applying any epoxy, it is crucial to ensure that the surface is thoroughly cleaned and prepared. Use a grinder to rough up the area around the crack, creating a textured surface for the epoxy to adhere to. Make sure the area is completely degreased and free of any contaminants. This step is essential for achieving a strong bond.
Step 2: Choose the Right Epoxy
Not all epoxies are created equal. For sealing cracks in a boat engine block, you need a high-temperature epoxy that can withstand the extreme conditions. Look for products specifically designed for marine use, as they will be able to handle the heat and pressure. Some recommended options include JB Weld, Marine Tex, and Lock n Stitch.
Step 3: Mix and Apply the Epoxy
Carefully follow the instructions provided with your chosen epoxy for mixing and application. Typically, you will need to mix the epoxy resin and hardener in the correct ratio, creating a uniform mixture. Apply the epoxy to the crack, making sure to fill it completely. You may need to use a putty knife or similar tool to work the epoxy into the crack and create a smooth finish.
Step 4: Allow the Epoxy to Cure
Once the epoxy is applied, it's crucial to give it enough time to cure properly. Refer to the manufacturer's instructions for the recommended curing time. Do not disturb or subject the engine to stress during this period. After the epoxy has cured, you may need to sand or paint the area for a smooth and protected finish.
Step 5: Test and Monitor
After the repair, it is essential to test and monitor the engine's performance. Conduct a pressure test to ensure that the crack has been successfully sealed and there are no leaks. Keep a close eye on the engine's temperature, oil levels, and overall performance during its initial operation. If any issues persist or new symptoms arise, consult a professional marine mechanic for further diagnosis and repair.
While using epoxy to seal cracks in a boat engine block can be a temporary solution, it is important to recognize that a cracked engine block is a severe issue. For more extensive damage or internal cracks, it is advisable to seek professional assistance and consider a block replacement or engine rebuild.
Finding Negative Blocks in Boat Wiring: A Comprehensive Guide
You may want to see also
Signs of a cracked engine block
A cracked engine block is one of the most serious issues you can face as a boat or car owner. While it is uncommon, it is important to know the signs to look out for so that you can get the necessary solutions. Here are some of the key symptoms of a cracked engine block:
Visible Engine Smoke
If you start seeing smoke in the cabin or steam coming from the exhaust pipe, it could be a sign that your boat or car engine block has cracks. This is caused by oil or coolant leaking through the crack and mixing with the antifreeze. When the contaminated antifreeze is burned during the combustion process, it produces smoke or steam, which may have a sweet odour.
Overheating Engine
Antifreeze leaks caused by cracks in the engine block can lead to engine overheating. The reduced antifreeze levels disrupt the circulation, causing temperatures to rise. Therefore, if you suspect a fault with the block, check your engine's temperature.
Oil or Coolant Leaks
One of the most noticeable signs of a cracked engine block is a leak. Keep an eye out for any small or large puddles of oil or coolant under your vehicle. A cracked engine block can result in both internal and external leaks, depending on the location of the crack.
Discoloured Oil
Check the colour of your oil if you suspect a cracked engine block. A crack can allow oil or coolant to seep out and mix with the antifreeze. If the crack is deep, the antifreeze will mix with the oil, resulting in a milky-white appearance.
Compromised Performance
A cracked engine block will affect the engine's efficiency, leading to reduced power and increased fuel consumption. You may also experience rough running and misfiring due to a loss of compression caused by the crack.
Launching a Duffy Boat: A Beginner's Guide to Getting Started
You may want to see also
Causes of a cracked engine block
A cracked engine block is a serious issue that can be caused by a variety of factors. Here are some common causes of a cracked engine block:
Excess Heat and Overheating
One of the most common causes of a cracked engine block is excess heat. This is usually due to an issue with the engine's coolant system. When the coolant fails to circulate properly, certain sections of the engine overheat and expand, while cooler areas remain unchanged. This contrast in temperatures causes thermal stress, which can lead to cracks in the engine block.
Water Pump Failure
Water pump failure is another possible cause of a cracked engine block. The water pump plays a crucial role in circulating coolant throughout the engine. If the water pump malfunctions, it can hinder coolant flow, leading to severe overheating. This, in turn, can result in cracks forming in the engine block.
Poor Storage and Maintenance
Improper storage and maintenance of your boat during the fall or winter seasons can contribute to engine block cracks. If the cooling system is not properly drained and filled with antifreeze, water can freeze and expand, exerting pressure on the engine block and causing cracks.
Manufacturing Defects
In some cases, engine block cracks may be attributed to manufacturing defects. Improper casting during the injection moulding process can result in thinning of the metal in certain regions. When the engine heats up, these thinner sections may not withstand the high temperatures, leading to the formation of cracks.
Contaminants in Metal
Contaminants introduced during the manufacturing process can also cause engine block cracks. These contaminants can weaken the metal, making it more susceptible to cracking, especially when exposed to high temperatures or thermal stress.
Insufficient Antifreeze in Cold Conditions
In extremely cold conditions, insufficient antifreeze in the cooling system can lead to engine block cracks. Without enough antifreeze, water in the system can freeze and expand, exerting pressure on the engine block and causing cracks.
Who Really Owns the Sunday Money Boat?
You may want to see also
Replacing the engine block
If your boat engine block is cracked, you may be able to repair it without replacing the entire engine. However, if the crack is internal, you will need a new engine block.
Before attempting any repairs, it is important to determine the extent of the damage and whether the crack is internal or external. One way to do this is to perform a compression test. If the crack is limited to the water jacket, it may be possible to repair it without replacing the entire engine block.
Another option for repairing a cracked engine block is to use a process called "cold welding" or "lace welding". This involves drilling and tapping a series of holes, installing plugs, and then drilling partially into the plugs and the crack to seal it. This method is often used by machine shops that specialize in heavy and industrial diesel repair.
If the crack is external and not too severe, it may be possible to repair it by grinding the area around the crack, cleaning and drying it, and then using an epoxy or welding rod to seal the crack. This method has been successful for some boat owners, but it is important to note that cast iron is difficult to weld, and improper welding can cause more cracks.
When repairing a cracked engine block, it is crucial to ensure that the repair can withstand high temperatures and pressure. One product that has been recommended by boat owners for sealing cracks and holes is JB Weld, a type of epoxy that can withstand high temperatures. Other products that have been used successfully include Marine Tex, a two-part epoxy repair putty, and nickel-based welding rods.
In some cases, the best option may be to replace the engine block or the entire engine, especially if the crack is internal or if there are other signs of damage, such as contaminated antifreeze or milky-white oil due to antifreeze mixing with oil.
It is always recommended to consult a professional marine mechanic or engineer if you are unsure about the best course of action or if you do not have experience with engine repairs. They can help assess the damage, recommend the best repair option, and perform the necessary repairs to ensure the safety and proper functioning of your boat's engine.
Speed Boat Brands: The Ultimate Guide to Choosing the Best
You may want to see also
Frequently asked questions
Some signs of a cracked engine block are visible smoke in the cabin, engine overheating, compromised performance, and oil leaking.
If the cracks are not too severe, you can seal the damage to prevent coolant or oil from leaking. However, it is recommended to consult a professional to handle your boat engine problems.
Welding a cracked cast iron block is not recommended as it can cause more cracks. Replacement of the block or a new engine is often suggested.
Excess heat is the most common cause of a cracked engine block. This can be due to a problem with the coolant or a malfunctioning water pump. Poor storage and improper casting during injection molding can also lead to cracks.
Proper maintenance and winterizing are key to preventing cracks in your boat engine block. This includes draining the water and filling the system with antifreeze to prevent water from freezing and expanding, which can lead to cracks.