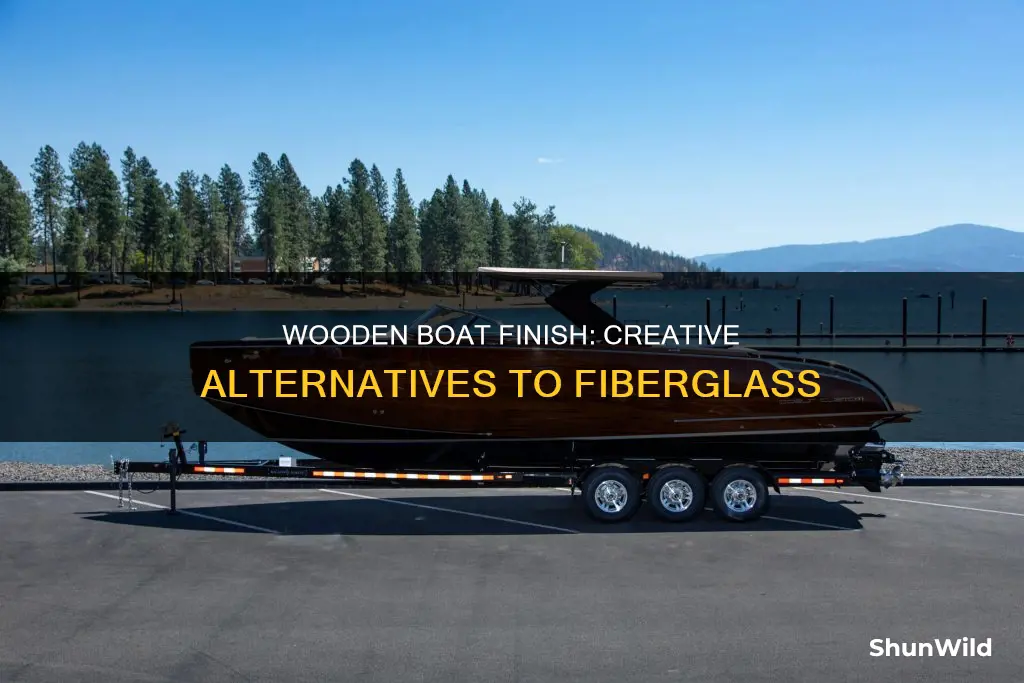
Finishing a wood-stripped boat without using fiberglass presents a unique challenge, but it can be achieved with careful planning and the right materials. This method involves ensuring the boat's structural integrity and aesthetics through various techniques, such as using traditional wood joinery, applying marine-grade paint or varnish, and employing innovative methods to reinforce weak spots. The process requires a deep understanding of wood properties and the ability to work with different wood types to create a sturdy and visually appealing vessel. By exploring these alternatives, boat builders can achieve a high-quality finish while maintaining the classic, timeless look of a wood-stripped boat.
What You'll Learn
- Wooden Planking: Use traditional wooden planks and screws for a classic, durable finish
- Epoxy Resin Bonding: Bond wood with epoxy for a strong, waterproof seal
- Canvas or Fabric Covering: Cover the boat with canvas or fabric for a lightweight, flexible exterior
- Paint and Stains: Apply paint or stains to enhance wood's natural beauty and protect it
- Fiberglass Alternatives: Explore natural fibers like hemp or flax for a sustainable, eco-friendly approach
Wooden Planking: Use traditional wooden planks and screws for a classic, durable finish
Wooden Planking: A Timeless and Practical Approach
Finishing a wood-stripped boat without using fiberglass is a rewarding endeavor that can result in a classic and durable vessel. One of the most traditional and effective methods is wooden planking, which involves using sturdy wooden planks and screws to create a strong and long-lasting hull. This technique has been used for centuries and offers a unique aesthetic appeal that many enthusiasts appreciate.
To begin, you'll need to carefully select the right type of wood. Hardwoods like oak, mahogany, or cedar are excellent choices due to their strength and natural resistance to rot and decay. The planks should be cut to size, ensuring a precise fit for the boat's hull. Each plank should be carefully shaped and planed to create a smooth surface, allowing for a seamless bond when joined.
The process starts with laying the planks along the hull, starting from the keel and working upwards. Use screws or nails to secure each plank, ensuring a tight fit. It's crucial to maintain a consistent angle and pressure when driving the screws to avoid damaging the wood. Consider using a mallet or a specialized tool to ensure a secure hold without splitting the wood. As you progress, fill the gaps between the planks with wood filler or putty, creating a smooth and continuous surface.
Once the planks are securely fastened, it's time for the final touches. Sand the entire hull to achieve a smooth finish, removing any rough edges or excess filler. Pay close attention to the joints and ensure a consistent texture. You can then apply a suitable wood sealer or varnish to protect the planks and enhance their natural beauty. This step is essential to ensure the longevity of the boat and provide a professional-looking finish.
Wooden planking offers a traditional and authentic approach to boat restoration or construction. It requires skill and attention to detail but results in a sturdy and visually appealing vessel. With proper care and maintenance, a wood-planked boat can last for generations, providing a unique and timeless experience on the water.
Installing a Steering Wheel on Your Aluminum Boat: A Guide
You may want to see also
Epoxy Resin Bonding: Bond wood with epoxy for a strong, waterproof seal
Epoxy resin bonding is an excellent method to create a strong and durable bond between wood components in a boat, offering a waterproof seal that is essential for any watercraft. This technique is particularly useful for those looking to finish a wood-stripped boat without using traditional materials like fiberglass. Here's a step-by-step guide to achieving a successful epoxy bond:
Preparation: Begin by ensuring the wood surfaces are clean, smooth, and free from any debris or old finishes. Use sandpaper to gently roughen the wood, creating a slightly textured surface. This process allows the epoxy to adhere better. Remove any dust or particles with a tack cloth or a damp cloth to ensure a clean bonding surface.
Mixing the Epoxy: Follow the manufacturer's instructions to mix the epoxy resin and hardener. Typically, you'll need to measure and combine the correct proportions of each component. Stir the mixture thoroughly to ensure a consistent blend. It's crucial to use the right ratio to achieve optimal curing and bonding properties.
Application: Apply the epoxy resin to the prepared wood surfaces using a brush, roller, or spray gun. Start with a small section at a time to maintain control. For best results, work in a well-ventilated area or outdoors. Apply a thin, even coat, ensuring complete coverage. Pay attention to any gaps or joints, as these areas may require additional epoxy to create a seamless bond.
Clamping and Curing: After applying the epoxy, immediately clamp the wood pieces together to initiate the bonding process. Clamping creates pressure, ensuring good adhesion. Keep the clamped assembly in a warm, dry place to accelerate curing. The epoxy will start to harden, and over time, it will form a strong, flexible bond. Allow sufficient curing time, typically several hours to a full day, depending on the epoxy type.
Finishing Touches: Once cured, carefully remove the clamps. Inspect the bond for any imperfections and touch up any areas that may require additional epoxy. Sand the surface gently with fine-grit sandpaper to create a smooth finish. This step ensures the final surface is ready for further customization, such as painting or adding additional boat components.
Epoxy resin bonding provides a reliable and long-lasting solution for joining wood in a boat, offering excellent resistance to water and impact. This method allows for creative customization, as the epoxy-bonded wood can be shaped and finished in various ways, providing a unique and personalized boat interior or exterior.
The Art of Balancing Boats: Secrets to Safe Sailing
You may want to see also
Canvas or Fabric Covering: Cover the boat with canvas or fabric for a lightweight, flexible exterior
If you're looking to finish your wooden strip boat without using fiberglass, one popular and effective method is to cover the exterior with canvas or fabric. This technique provides a lightweight, flexible, and aesthetically pleasing finish. Here's a step-by-step guide to help you achieve a successful canvas or fabric covering:
Preparation: Before you begin, ensure that the wooden boat is thoroughly cleaned and free from any debris or old paint. Sanding the surface is crucial to create a smooth and even base for the fabric. Pay attention to the edges and corners, as these areas require extra care to ensure a neat finish. Consider using a power sander for larger surfaces and a finer sandpaper for more delicate areas.
Fabric Selection: Choose a suitable fabric that is durable and weather-resistant. Canvas is an excellent option due to its strength and flexibility. Opt for a weight that complements your boat's design; lighter canvases are ideal for smaller boats, while heavier ones can handle larger vessels. Ensure the fabric has a tight weave to prevent water seepage and consider treating it with a water-repellent finish for added protection.
Fabric Application: Start by measuring and cutting the fabric to fit each section of the boat's exterior. For larger areas, you might need to piece together multiple fabric panels. Begin at the bottom of the boat and work your way up, ensuring that each panel overlaps the previous one to create a seamless appearance. Use a strong adhesive or fabric tape to secure the fabric to the wood, being mindful of the tension to avoid wrinkles.
Sealing and Finishing: To enhance the boat's durability, consider adding a layer of marine-grade adhesive or epoxy to bond the fabric to the wood. This step is crucial for creating a robust and long-lasting finish. After the adhesive has cured, you can further protect the boat by applying a marine-grade varnish or paint to the fabric-covered surface. This additional layer will provide UV protection and add to the overall aesthetics.
By following these steps, you can create a unique and functional boat exterior using canvas or fabric, all without the need for fiberglass. This method offers a lightweight alternative that is both cost-effective and environmentally friendly.
The Art of Naming Boats: A Guide to Boat Naming Etiquette
You may want to see also
Paint and Stains: Apply paint or stains to enhance wood's natural beauty and protect it
When restoring a wood-stripped boat, applying paint or stains is an excellent way to enhance the natural beauty of the wood while providing essential protection. This process not only revitalizes the boat's appearance but also safeguards the wood from the elements, ensuring its longevity. Here's a step-by-step guide to achieving a professional finish:
Preparation: Begin by ensuring the wood is clean and free from any dirt or debris. Use a mild detergent and water solution to wash the surface, then rinse thoroughly and allow it to dry completely. This step is crucial as it ensures the paint or stain adheres properly. After drying, inspect the wood for any minor imperfections, such as scratches or small holes. Fill these areas with a wood filler or putty, sanding them smooth once dry. This preparation process will create a smooth and even surface for the finish.
Choosing the Right Paint or Stain: Select a paint or stain that is specifically designed for marine environments. Look for products that are UV-resistant, as this will help protect the wood from fading and deterioration caused by sunlight. Consider the color and finish you desire. Natural wood stains will enhance the grain and texture of the wood, providing a subtle yet beautiful look. On the other hand, solid-color paints offer more coverage and can be used to create a uniform appearance, which is especially useful for larger boat surfaces.
Application Techniques: The application method will depend on your preference and the desired finish. For a smooth and seamless look, consider using a brush. Start by applying thin, even coats, allowing sufficient drying time between each layer. This technique ensures a uniform coverage without any visible brush strokes. For smaller, intricate areas, a small brush or a foam roller can be used for more precise application. When staining, work in the direction of the wood grain to avoid any unwanted patterns. For painting, use long, even strokes, especially when working on vertical surfaces.
Multiple Coats and Protection: Apply multiple thin coats of paint or stain to achieve the desired depth and color. This process also adds an extra layer of protection. After the final coat is dry, consider adding a protective topcoat, such as a clear varnish or sealant. This topcoat will provide an additional barrier against moisture, UV rays, and general wear and tear, ensuring the wood remains in optimal condition.
By following these steps, you can effectively transform and protect a wood-stripped boat using paint or stains, all without the need for fiberglass. This method not only preserves the boat's natural beauty but also ensures its durability and longevity, making it a popular choice for boat restoration enthusiasts.
Unveiling the Power of Boat Exhaust Systems: A Deep Dive
You may want to see also
Fiberglass Alternatives: Explore natural fibers like hemp or flax for a sustainable, eco-friendly approach
The world of boat restoration and construction is increasingly embracing sustainable and eco-friendly practices, and one of the most exciting alternatives to traditional fiberglass is the use of natural fibers like hemp and flax. These plant-based materials offer a unique blend of strength, flexibility, and environmental benefits, making them an ideal choice for finishing a wood-stripped boat.
Hemp and flax fibers have been used for centuries in various industries, including shipbuilding, due to their exceptional properties. These natural fibers are known for their high tensile strength, which means they can provide excellent structural support without adding excessive weight to the boat. When woven or mat-formed, these fibers create a sturdy and lightweight composite material, perfect for reinforcing wooden structures. For instance, you can create a hemp or flax mat by soaking the fibers in a natural resin, such as linseed oil, and then carefully laying and pressing them onto the wooden hull. This process forms a strong, flexible layer that can be sanded and finished to match the boat's existing surface.
One of the most significant advantages of using natural fibers is their sustainability. Unlike fiberglass, which often relies on non-renewable resources and can be energy-intensive to produce, hemp and flax are renewable crops that require fewer resources to cultivate. They also have a lower environmental impact during processing and manufacturing, making them an excellent choice for those seeking an eco-conscious approach to boat restoration. Additionally, natural fibers can provide a unique aesthetic appeal, offering a rustic and organic finish that contrasts beautifully with the smooth, polished wood of the boat.
To begin the process, you'll need to source high-quality hemp or flax fibers, ensuring they are free from impurities. These fibers can be purchased in various forms, such as rope, yarn, or pre-made mats, depending on your preference and the specific requirements of your project. It is essential to prepare the fibers by soaking them in a natural resin, such as linseed oil or hemp oil, to create a cohesive and durable composite material. The resin acts as a binder, allowing the fibers to bond with the wooden surface and providing additional protection against the elements.
When applying the natural fiber composite, it's crucial to follow a systematic approach. Start by carefully preparing the wooden surface, ensuring it is clean, smooth, and free from any debris. Then, apply a thin layer of the resin mixture, allowing it to penetrate the wood's pores. Next, lay the fibers in a specific pattern, ensuring they are evenly distributed and securely bonded to the underlying wood. This process may require multiple layers and careful attention to detail to achieve the desired strength and finish. Finally, sand the surface to create a smooth, seamless integration between the natural fibers and the wooden hull.
By exploring natural fibers like hemp or flax, boat enthusiasts can embrace a sustainable and eco-friendly approach to finishing their wood-stripped vessels. This method not only preserves the boat's original beauty but also contributes to a greener and more environmentally conscious future for the maritime industry. With careful preparation and attention to detail, these natural composites can provide a strong, flexible, and aesthetically pleasing finish, ensuring the boat's longevity and a reduced environmental footprint.
Fueling a Pontoon Boat: Dockside Tips and Tricks
You may want to see also
Frequently asked questions
There are several options for boat construction without fiberglass. One popular choice is epoxy resin, which can be used to bond wood strips together and create a strong, lightweight structure. Other materials include balsa wood, which is lightweight and easy to work with, and various types of foam cores, such as polystyrene or polyurethane foam, which provide buoyancy and insulation.
To maintain structural integrity, focus on proper bonding techniques. Use high-quality epoxy resins and ensure that all wood strips are clamped tightly together during the curing process. Reinforce critical areas like the hull bottom and sides with additional layers of wood strips and epoxy. Regularly inspect and maintain the boat to identify and repair any potential issues promptly.
Sanding is crucial for achieving a smooth surface. Start with coarse-grit sandpaper to remove any roughness and then progress to finer grits for a smoother finish. After sanding, consider using a wood filler or putty to fill any small gaps or imperfections. Once dry, sand again to ensure a seamless surface. Finally, apply a suitable wood finish, such as varnish or paint, to protect the wood and enhance its appearance.
Waterproofing is essential to prevent leakage. Apply a layer of marine-grade epoxy resin over the entire hull to create a barrier against water intrusion. Pay close attention to seams and joints, using tape or additional epoxy to ensure a watertight seal. Consider adding a layer of cloth or fiber glass cloth to reinforce weak areas and provide additional protection. Regularly inspect and maintain the boat's seams to address any potential leaks.
Traditional boat-building techniques, such as wood stripping, offer a more sustainable and environmentally friendly approach. Wood is a natural resource that can be sourced responsibly, and the boat-building process often involves less waste compared to some modern materials. Additionally, wood-stripped boats can be lighter, providing better fuel efficiency and reduced environmental impact.