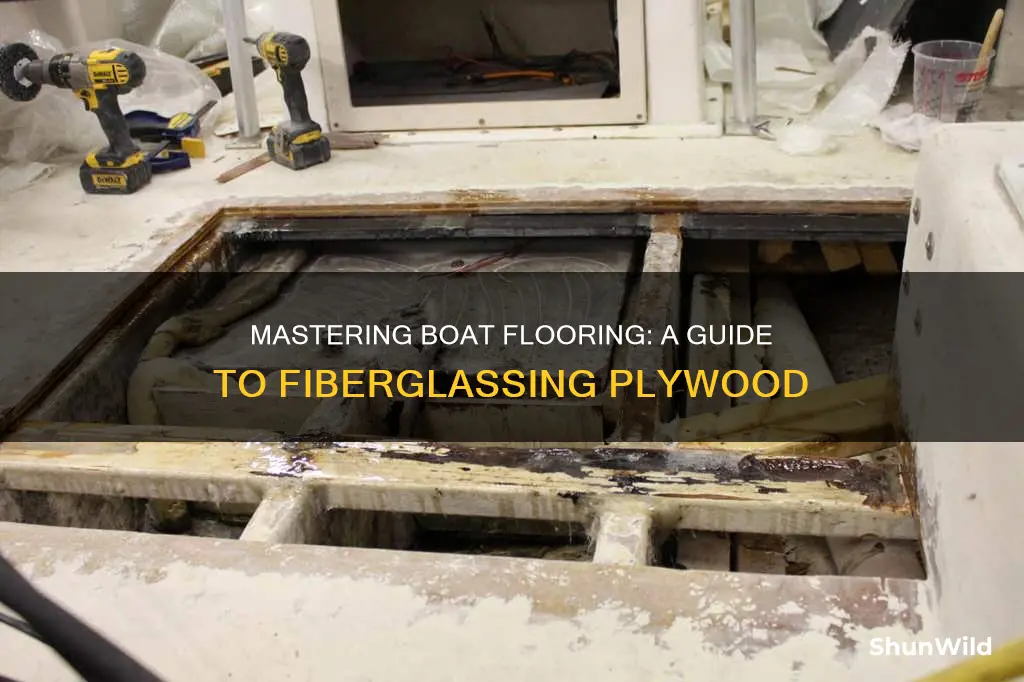
Fiberglassing plywood for boat flooring is a popular choice for boat owners who want a durable and lightweight surface. This process involves applying a layer of fiberglass over a plywood base to create a smooth, seamless, and waterproof surface. The key to a successful installation is proper preparation and attention to detail. In this guide, we'll walk you through the steps to ensure a professional-looking finish, including how to prepare the plywood, apply the fiberglass, and finish with a protective coating.
What You'll Learn
- Prepare the Plywood: Clean and sand the plywood surface for a smooth bond
- Choose the Right Fiberglass: Select a suitable fiberglass cloth and resin for boat flooring
- Apply Resin and Fabric: Layer resin and fiberglass cloth, following a wet layup technique
- Cure and Sand: Allow the fiberglass to cure, then sand for a smooth finish
- Finish and Seal: Apply a marine-grade sealant and consider a non-skid surface for safety
Prepare the Plywood: Clean and sand the plywood surface for a smooth bond
Preparing the plywood for boat flooring is a crucial step to ensure a strong and durable bond between the material and the boat's structure. This process involves cleaning and sanding the surface to create a smooth and even base for the fiberglass application. Here's a detailed guide on how to achieve this:
Cleaning the Plywood: Start by thoroughly cleaning the plywood surface to remove any dirt, dust, or debris. Use a pressure washer or a high-pressure hose to rinse the entire area, ensuring you remove any loose particles. For a more thorough clean, especially if the plywood has been previously used, you can use a mild detergent mixed with water. Apply the solution and scrub the surface gently with a soft brush or sponge. Rinse thoroughly afterward to eliminate any residue. This step is essential to prevent any contaminants from affecting the bonding process.
Sanding the Surface: Once the plywood is clean, it's time to smooth it out. Start with a coarse-grit sandpaper (around 40-60 grit) to remove any remaining imperfections, old paint, or previous finishes. Work in small sections, sanding with the grain of the wood to avoid creating new scratches. After removing the bulk of the imperfections, switch to a finer grit (80-120 grit) to achieve a smoother finish. Carefully sand along the edges and curves of the plywood to ensure a consistent surface. This process helps to create a uniform base for the fiberglass, allowing for better adhesion and a seamless finish.
As you sand, take the time to inspect the plywood for any remaining defects. Fill any small holes or imperfections with a wood filler or epoxy putty, ensuring they are level with the surface. Once filled and dried, sand these areas again to create a smooth transition. Proper sanding and preparation will result in a high-quality bond and a professional-looking boat floor.
Remember, the goal is to create a smooth, clean, and uniform surface for the fiberglass to adhere to. This process might take some time and effort, but it is a critical step to ensure the longevity and structural integrity of your boat's flooring.
Waterless Boat Race Mystery at Dixie Speedway
You may want to see also
Choose the Right Fiberglass: Select a suitable fiberglass cloth and resin for boat flooring
When it comes to fiberglassing plywood for boat flooring, selecting the right materials is crucial for a durable and long-lasting finish. Here's a guide to help you choose the appropriate fiberglass cloth and resin for this project:
Fiberglass Cloth:
- Choose a suitable fiberglass cloth based on the specific requirements of your boat flooring. For boat applications, you typically want a cloth that is strong, flexible, and resistant to abrasion. The most common choice is a woven fiberglass cloth, often referred to as 'woven glass' or 'glass cloth'.
- Consider the weave pattern; a plain weave is ideal for boat flooring as it provides a smooth surface and allows for easy application of resin. You can find fiberglass cloths in various weights, with higher weights offering more strength. For boat flooring, a medium to heavy-weight cloth (typically 4 to 6 oz per square yard) is recommended to ensure structural integrity.
- Look for a cloth that is heat-resistant to handle the curing process without distortion. Some manufacturers offer specialized boat-grade cloths with added features like UV resistance or fire retardancy, which can be beneficial for outdoor applications.
Resin Selection:
- Resin is a critical component in the fiberglassing process, providing structural strength and bonding the fiberglass to the plywood. For boat flooring, a suitable resin system is essential to withstand the marine environment.
- Epoxy resins are commonly used in boat construction due to their excellent bonding properties and ability to form a strong, durable bond with the fiberglass cloth. Choose an epoxy resin with a suitable viscosity for the job; a low-viscosity resin will flow easily, making it ideal for filling and smoothing, while a higher viscosity can provide better control during application.
- Consider the curing time and temperature of the resin system. Fast-curing resins can speed up the project, but they may require more careful handling. Some resins are designed to cure at room temperature, while others need heat curing, so choose one that aligns with your project timeline and capabilities.
When selecting both the fiberglass cloth and resin, it's essential to consider the specific conditions your boat will face. Marine environments can be harsh, so choosing materials with added protection against UV rays, chemicals, and abrasion is beneficial. Additionally, ensure that the products you choose are compatible with each other to achieve the best results. Proper preparation of the plywood substrate and careful application techniques will also contribute to a successful fiberglass boat flooring project.
Restoring a Graded Boat Hull: A Step-by-Step Guide
You may want to see also
Apply Resin and Fabric: Layer resin and fiberglass cloth, following a wet layup technique
The process of applying resin and fabric to create a sturdy boat floor involves a technique known as wet layup, which requires careful preparation and attention to detail. Here's a step-by-step guide to help you master this method:
Preparing the Work Area: Begin by setting up your workspace in a well-ventilated area, as working with resin can release fumes. Ensure you have a clean, flat surface to lay out your materials. Gather all the necessary tools and supplies, including the chosen resin, fiberglass cloth (often referred to as cloth or weave), a spray bottle or brush for resin application, and any additional tools like a roller or squeegee for smoothing.
Mixing and Preparing the Resin: Follow the manufacturer's instructions to mix the resin and hardener accurately. Proper mixing is crucial for achieving the desired consistency and strength. Typically, you'll need to measure and mix the resin and hardener in the correct ratio. Stir the mixture thoroughly to ensure a uniform blend. If you're using a spray bottle, lightly mist the resin onto the cloth, ensuring an even coating. Alternatively, you can brush or roll the resin to achieve the desired thickness.
Laying the Fiberglass Cloth: Cut the fiberglass cloth to the appropriate size, slightly larger than the area you intend to cover. This extra fabric will allow for overlap and ensure a strong bond. Place the cloth over the prepared plywood, ensuring it is centered and smooth. Start at one edge and work your way across, using the wet layup technique. Apply the resin to the cloth, allowing it to saturate the fibers. Then, using your hands or a roller, smooth out any air bubbles and ensure the cloth is tightly adhered to the plywood. Repeat this process, overlapping the cloth slightly, until the entire area is covered.
Curing and Reinforcing: After completing the layup, cover the entire area with a plastic sheet or tarpaulin to protect it from dust and debris. Allow the resin to cure according to the manufacturer's instructions. This curing process can take several hours or even days, depending on the type of resin used. Once cured, inspect the work and consider adding additional layers or reinforcement where necessary, especially in high-stress areas like corners or edges.
Finishing Touches: Once satisfied with the strength and appearance, carefully remove the plastic covering. You might need to sand the surface to achieve a smooth finish. This step is crucial for ensuring a professional-looking boat floor. Finally, apply any desired finishes or coatings to protect the fiberglass and plywood, providing a durable and aesthetically pleasing boat floor.
Mastering Sailboat Rigging: A Step-by-Step Guide to Success
You may want to see also
Cure and Sand: Allow the fiberglass to cure, then sand for a smooth finish
The process of curing and sanding the fiberglass is a crucial step in creating a smooth and durable boat flooring surface. After applying the fiberglass layers, it's essential to allow the material to cure properly to ensure its strength and integrity. The curing time can vary depending on the type of fiberglass and the ambient temperature, but it typically takes a few days to fully cure. During this time, it's important to avoid any heavy pressure or impact on the surface to prevent any damage. Once cured, the fiberglass will be hard and rigid, providing a strong foundation for the boat's flooring.
Sanding is the next critical step to achieve a smooth and professional finish. Start with a coarse-grit sandpaper (around 40-60 grit) to remove any excess fiberglass and create a rough surface for the next layer. Gradually progress to finer grits (80-120 grit) to refine the surface and create a smooth base for the final finish. It's important to sand with the direction of the fiberglass weave to avoid any unwanted scratches or imperfections. Take your time and be thorough, ensuring an even and consistent surface.
After sanding, inspect the surface for any remaining imperfections or rough spots. If needed, repeat the sanding process with finer grits until you achieve a smooth and seamless finish. Remember, the goal is to create a surface that is ready for the final flooring material, such as marine carpet or wood veneer. Proper curing and sanding will ensure that the boat flooring is not only aesthetically pleasing but also functional and long-lasting.
Take note of any specific requirements or recommendations provided by the fiberglass manufacturer, as different brands may have unique curing and sanding instructions. Always wear appropriate personal protective equipment (PPE) when working with sandpaper and fiberglass to ensure a safe and healthy working environment. With patience and attention to detail, you'll be able to create a high-quality boat flooring surface that will withstand the test of time.
Paddling Adventure: Age Limit for Boat Fun
You may want to see also
Finish and Seal: Apply a marine-grade sealant and consider a non-skid surface for safety
When it comes to finishing and sealing your boat flooring, using a marine-grade sealant is crucial to ensure durability and protection against the harsh marine environment. Start by cleaning the surface of the fiberglass plywood thoroughly to remove any dirt, debris, or old sealant. This step is essential for proper adhesion. Prepare the sealant by mixing it according to the manufacturer's instructions, ensuring you have the right consistency for your specific application. Marine-grade sealants are designed to withstand UV radiation, saltwater, and varying temperatures, making them ideal for boat applications.
Apply the sealant generously to the entire surface of the plywood, following the manufacturer's guidelines for coverage and thickness. Pay close attention to the edges and corners, as these areas require extra protection. Use a paintbrush or a roller to ensure an even and smooth application. Allow the sealant to cure according to the product's instructions, which may involve multiple coats and drying times. This process creates a protective barrier that seals the plywood, preventing water absorption and potential damage from moisture.
In addition to sealing, consider enhancing the safety and functionality of your boat floor. A non-skid surface is essential to provide traction and prevent accidents. You can achieve this by applying a non-skid coating or material over the sealed plywood. There are various non-skid options available, such as non-skid paints, tapes, or mats, each with different textures and adherence properties. Choose a product suitable for marine environments, ensuring it is resistant to fading and wear. Apply the non-skid surface evenly, following the manufacturer's instructions for best results.
For a more permanent solution, you can sand the sealed plywood surface slightly to create a rough texture, which will provide better grip. After sanding, wipe away the dust and apply the non-skid material. This process ensures a secure and safe walking surface, reducing the risk of slips and falls on board. Regularly inspect and maintain the non-skid coating to ensure its effectiveness, especially in areas with high foot traffic.
Remember, the finish and sealing process is a critical step in boat flooring installation, as it provides protection, durability, and safety. By using marine-grade sealants and non-skid surfaces, you create a robust and reliable boat floor that can withstand the challenges of marine environments while ensuring a comfortable and secure experience for passengers and crew.
Unleash the Speed: 50 HP Boat's Top Performance
You may want to see also
Frequently asked questions
Fiberglassing plywood is a process of reinforcing wooden panels with fiberglass to create a strong, lightweight, and durable surface for boat flooring. This technique enhances the structural integrity of the boat, provides a smooth and impact-resistant floor, and can improve the overall aesthetics of the interior.
Fiberglass offers several advantages for boat flooring. It is lightweight, making it easier to install and reducing the overall weight of the vessel. Fiberglass is also highly durable, resistant to moisture, and can withstand the harsh marine environment. Additionally, it provides a smooth and seamless surface, which is essential for comfort and safety during navigation.
Proper preparation is crucial for a successful fiberglass job. Start by cleaning the plywood surface to remove any dirt or debris. Then, use a wood filler or putty to fill any holes, cracks, or imperfections. Sand the surface gently to create a smooth and even base for the fiberglass. Ensure the plywood is dry and free of any moisture before proceeding.
For boat flooring, it is recommended to use a lightweight fiberglass cloth and a low-viscosity epoxy resin. Lightweight fiberglass cloth, such as 4-ounce or 6-ounce cloth, provides strength without adding excessive weight. A low-viscosity resin allows for easier application and better adhesion to the plywood. Follow the manufacturer's instructions for mixing and applying the resin and fiberglass.
While regular fiberglass cloth can be used, specialized boat flooring cloth is often preferred. Boat flooring cloth is typically made with a higher glass content and a more flexible weave, allowing for easier application and a smoother finish. It is designed to conform to the curves and contours of the boat's interior, ensuring a professional-looking result. Specialized cloth may also offer better adhesion to the resin.