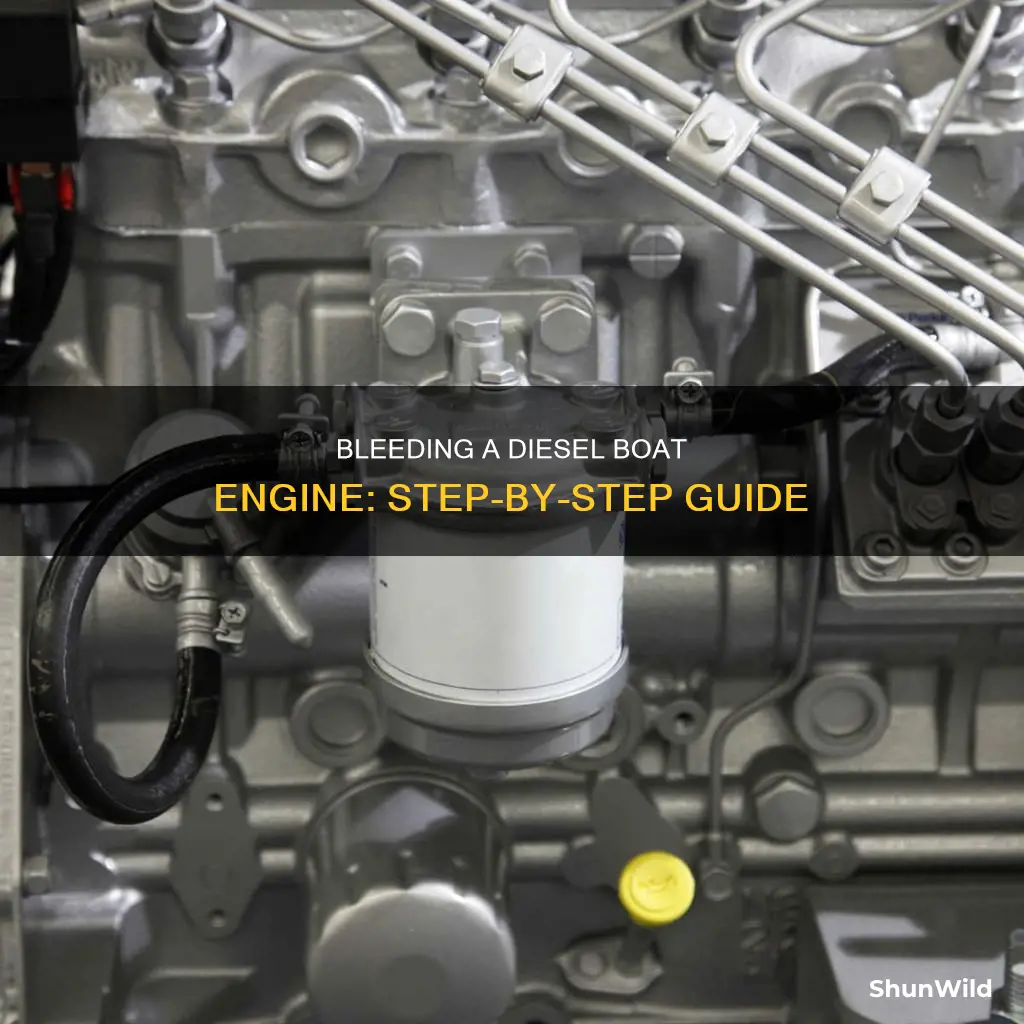
Bleeding a diesel boat engine is a crucial skill for boat owners to learn, as it can get you out of trouble without needing to resort to a mechanic. Diesel engines can be surprisingly simple to work on, and the process of bleeding one is straightforward. This process involves forcing diesel through the fuel system to push trapped air out, which will then allow the engine to start. Before attempting to bleed the air from the fuel system, it is important to determine how the air entered the system to prevent it from happening again. This guide will walk you through the steps to bleed your diesel boat engine and get it running smoothly again.
Characteristics | Values |
---|---|
Why bleed a diesel boat engine? | To remove air from the fuel system and restore fuel flow, enabling the engine to start |
When to bleed engine | When the engine won't start due to airlock, often caused by running out of fuel, leaks in fuel lines, or a fuel filter change |
Tools required | Wrench or socket set, bleeder screw key or wrench, clean rags or towels |
Step 1 | Identify how air entered the system and fix the issue to prevent reoccurrence |
Step 2 | Locate the fuel system components, including the fuel tank, fuel lines, fuel filter, and fuel injectors |
Step 3 | Turn off the engine, remove the ignition key, and locate the fuel filter |
Step 4 | Bleed the fuel filter by loosening the bleeder screw and allowing the air and fuel mixture to escape, then tighten the screw |
Step 5 | Bleed the fuel injectors by loosening the fuel line connection, cranking the engine, and tightening the connection once fuel flows steadily |
Step 6 | Start the engine and check for signs of remaining air, such as rough idle or reduced power |
Step 7 | Clean up any spilled fuel and perform ongoing maintenance, such as replacing the fuel filter |
What You'll Learn
Identify the leak
Identifying a leak in a diesel boat engine can be a challenging task, but it is important to address it promptly to prevent further issues. Here are some detailed steps to help you identify the source of the leak:
Check the Bilge
The bilge is the lowest point in your boat, so any fuel or water leak will eventually collect there. Open up the bilge and inspect for signs of fuel or water. If you find fuel floating in the bilge, it indicates a fuel leak, which could be due to a faulty fuel line or a breach in the fuel tank. Water in the bilge, on the other hand, could be rainwater or a leak from various sources, including hull penetrations below the waterline, shaft glands, transducers, or through-hulls.
Smell for Fuel Leaks
Use your sense of smell to detect fuel leaks. The sniff test is a common method, where you open the engine compartment and sniff for the distinct scent of gasoline or diesel fumes. This is most effective after refueling, as the fumes will be more concentrated. However, this method may not work if you have a cold or are unable to detect the fumes.
Visual Inspection
Conduct a thorough visual inspection of the engine and fuel lines. Look for signs of wetness, corrosion, or stains that could indicate a leak. Pay close attention to areas such as hose connections, valves, and clamps. If you notice any hissing sounds, it could indicate a fuel leak. Additionally, check the bilge water for a "rainbow effect," which occurs when petroleum products create an oily film on the water's surface, dispersing light and creating a rainbow-like effect.
Use of Paper Towels
This method is especially useful for identifying leaks in hard-to-reach places. Dry the suspected area and the surrounding surfaces with paper towels. Then, wait and inspect the area again for any signs of wetness. This will help you pinpoint the exact location of the leak.
Ultrasonic Testing
Ultrasonic testing is an advanced method that utilizes a pressure tester or a self-built device to apply pressure to the fuel tank. By applying 3 PSI of pressure, you can check for pressure loss, which indicates a leak. Soapy water can be applied to hose connections and other components to easily identify the location of the leak.
Thermal Imaging
Thermal imaging technology captures an image of the boat's fuel system, revealing "hotspots" that indicate potential leaks. This method uses thermal cameras to detect energy emitted by gas fumes, which are invisible to the human eye.
LPG Leak Down Test
If your boat has an LPG system, a leak down test is essential. Open the LPG tank manual supply valve and the electronic solenoid valve to pressurize the system, then close the tank supply valve. Observe the pressure gauge; if the pressure drops, it indicates a leak. At this point, use a non-corrosive and non-toxic leak detection fluid or detergent solution to locate the exact source of the leak.
Remember, when dealing with fuel leaks, it is crucial to act quickly to prevent safety hazards and further damage to your boat. Always exercise caution and, if needed, seek professional assistance.
Boat Safety Certificates: Legally Required or Recommended?
You may want to see also
Back off the bleed screw
To back off the bleed screw, you must first locate it. The bleed screw is usually found on top of the fuel filters fitted to the engine.
Once located, start by loosening the screw on the first filter by half a turn. You can loosen it further if required, but do not pull it out. Three to four turns is usually sufficient.
After you've loosened the bleed screw, get some rags, as the next step will be messy. You will see a mixture of air and fuel bleeding from the screw. Allow this to continue until only fuel (without air bubbles) flows from the screw.
Finally, tighten the screw while continuing to pump to maintain pressure and eliminate the chance of air re-entering the system.
Preventing Bass Boat Chine Walking: Expert Tips and Tricks
You may want to see also
Prime the diesel engine
To prime a diesel engine, you must first ensure that your primary filter is full of fuel. Drain off any water and sediment sitting at the bottom of the element holder, collecting the runoff in a suitable container.
Next, locate the lift pump, which is usually attached to the engine somewhere. Many lift pumps have a small lever that can be manually operated with a finger. With a suitable wrench, open the bleed screw on top of the secondary filter as you operate the pump. You only need to loosen the screw—do not remove it completely.
Continue pumping until the bubbles stop and clean fuel starts to emerge from the hole. Re-tighten the screw as you pump to prevent air from getting back into the fuel line.
Repeat the pumping procedure, this time releasing the fuel delivery pipe to the injector pump halfway, then tightening it as soon as fuel is ejected. As the run from the fuel lift pump to the injector pump is generally short, a couple of pumps is often all it takes.
Locate the other end of the fuel line where it connects to the injector. If your engine has more than one cylinder, you will need to repeat the loosen, pump, tighten sequence for each injector, starting with the injector closest to the injector pump.
Once complete, the engine should now start. If it doesn't start after 10 seconds or so of cranking, double-check that everything is tight and try bleeding the system once more, as even a tiny bit of air can prevent the fuel from getting through.
The SS Minnow: A Small Cruiser Ship
You may want to see also
Bleed any additional points
If your engine still won't start, you may need to bleed the injector pump and the individual injectors. This can be done using the same procedure as before.
Firstly, locate the bleed screw on the injector pump and loosen it by half a turn. Then, operate the manual fuel pump primer, keeping an eye on the bleed screw. You will know that the air has left the system when you see clean fuel, free of bubbles, being ejected. Retighten the screw as you pump to maintain pressure and prevent air from re-entering the system.
Next, locate the fuel injectors, which are usually connected to the fuel lines. Loosen the fuel line connection and crank the engine for a few seconds to allow the air to escape. Be cautious of any fuel spills. When you observe a steady flow of fuel without bubbles, tighten the fuel line connection.
Repeat this process for each injector, working from the injector closest to the fuel pump to the one farthest away. If you have a large engine, you may need to loosen the injector lines, open the throttle, and crank over the engine with the starter to force fuel through the lines. Remember to close the engine-cooling-intake seacock to prevent water from backing up into the muffler as the engine spins.
Once you have bled all the injectors, try to start your engine. If it still won't start, double-check that all connections are tight and consider bleeding the system again, as even a tiny bit of air can prevent the fuel from getting through.
Pelican Paddle Boat: How Much Does It Cost?
You may want to see also
Clean up and maintain
Once you have bled the air from your diesel engine's fuel lines, it is important to clean up any spills and maintain your engine to prevent future issues. Here are some detailed instructions for the clean-up and maintenance process:
- Contain any spills — Use oil-absorbent pads or clean rags to soak up any spilled fuel during the bleeding process. Diesel fuel is messy, smelly, and poses environmental hazards, so it is important to clean up spills properly. Place used absorbent pads or rags in a plastic bag for proper disposal.
- Dispose of waste responsibly — Ensure that you dispose of any diesel-soaked absorbent pads, rags, or other waste in accordance with local regulations. Do not pour excess diesel fuel or waste down the drain or into the environment. Contact your local waste management authority for guidance on hazardous waste disposal if needed.
- Inspect fuel lines and connections — After bleeding the engine, carefully inspect all fuel lines, connections, and components for signs of leaks or damage. Tighten any loose connections and replace any damaged parts. This will help prevent future air intrusions and ensure the proper functioning of your engine.
- Regular maintenance — Establish a solid maintenance routine for your diesel engine to keep it in optimal condition. This includes regular inspection and replacement of fuel filters, as well as checking fuel lines and connections for leaks. Refer to your owner's manual for specific maintenance recommendations for your engine.
- Prevent airlock — Airlock can occur when the diesel engine runs dry or when the fuel filter is changed. To prevent airlock, ensure that your engine never runs out of fuel. Additionally, when changing the fuel filter, fill the new filter with fuel and top it off as it is absorbed. Apply fuel to the inside of the gasket before installation to create a tight seal.
- Keep a log of maintenance — Record all maintenance activities, including dates, in a logbook. This will help you keep track of when certain tasks were last performed and identify any recurring issues. It can also be useful when selling your boat, as it demonstrates a history of proper maintenance.
- Consult a professional — If you encounter any difficulties, persistent issues, or unusual symptoms during or after bleeding your diesel engine, consult a professional diesel mechanic or contact the engine manufacturer for further assistance. They can provide expert guidance and help troubleshoot any problems.
The Boys in the Boat: Separating Fact from Fiction
You may want to see also
Frequently asked questions
Knowing how to bleed a diesel boat engine is an essential skill for boat engine owners. Bleeding the engine rids the fuel lines of air so the engine can start.
Air can enter the fuel system in several ways, most commonly by running out of fuel, from leaks in your fuel lines, or following a fuel filter change.
You will need a wrench or socket set, a bleeder screw key or wrench, and clean rags or towels.