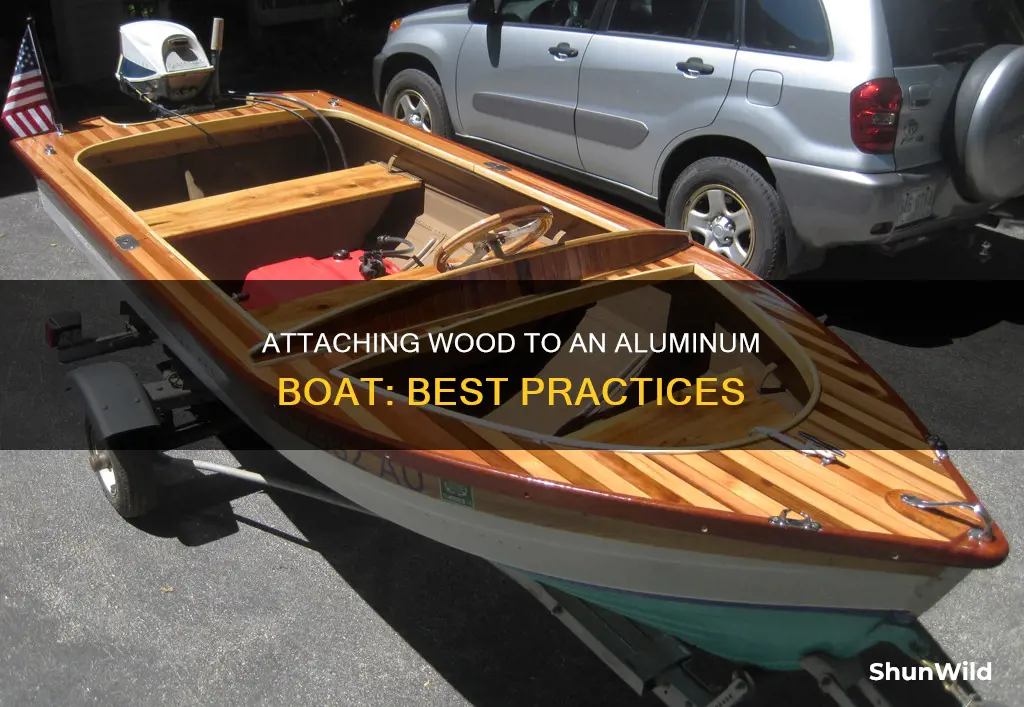
There are several ways to attach wood to an aluminum boat. One common method is to use rivets, screws, or welds. It is important to consider the environment in which the boat will be used, as certain materials may be more suitable than others to prevent corrosion. For example, using stainless rivets with large heads can provide a strong hold, while also being resistant to corrosion. Additionally, creating a barrier between the wood and aluminum, such as by using a product like plastic bunk slicks, can help prevent corrosion by keeping the two materials from touching.
What You'll Learn
Using screws to attach wood to an aluminium boat
When attaching wood to an aluminium boat, it is important to select the right type of fastener. While there are strong glues and tapes available, mechanical fastening is usually the best method. Metal fasteners are strong, long-lasting, and can be disassembled without causing damage.
Self-tapping screws are a good option for attaching wood to aluminium. They are designed to make their own hole as they are inserted, with a drill-bit-like pointed tip and a continuous thread that spans the whole length of the screw. This type of screw is ideal for joining metals to other materials such as wood or plastic. They are also less prone to loosening under the vibrations of the boat, which can be an issue with traditional fasteners.
When using self-tapping screws, it is important to stabilise the screw to prevent it from tilting during installation. You should also avoid overtightening, as this could damage the aluminium or break the screw. Drilling a pilot hole can help to ensure the screw is inserted straight and reduce the risk of damage to the material.
If you are screwing plywood to aluminium ribs, stainless steel self-tapping screws are recommended. For 1/2" marine plywood, 1" screws are sufficient, but for 3/4" plywood, you should use 1 1/4" screws. Drilling pilot holes with a 5/32" drill bit can help ensure a secure fit. Using stainless steel trim washers can also make it easier to remove the screws later if needed and create a nice finish over carpet.
For a neater finish, you can cut the plywood to size, drill pilot holes, and attach carpet before screwing the floor into place. Mark the location of the floor with a pencil, then remove it and enlarge the holes with a 3/16" drill bit. After waterproofing the plywood and attaching the carpet, use a nail or awl to punch through the carpet and mark the holes. Then screw the floor into place, using stainless steel dome head screws and trim washers.
Sailing Away: Optimal Hours for Boat Usage
You may want to see also
Using rivets to attach wood to an aluminium boat
Step 1:
Before starting the riveting process, it is important to gather the right materials and tools. You will need a rivet gun, drill, drill bits, rivets, and a rivet size guide. The type of rivets you choose is important, and you should select a size that is longer than the combined thickness of the two materials being joined. For attaching wood to aluminium, you can use aluminium or stainless steel rivets with a mild steel mandrel.
Step 2:
Prepare the wood and aluminium boat surface by cleaning and drying it thoroughly. This step is crucial to ensure that the rivets will adhere properly and prevent corrosion.
Step 3:
Drill holes through the wood and aluminium where you want to place the rivets. Make sure the holes are slightly larger than the rivet diameter to allow for easy insertion.
Step 4:
Insert the rivets through the holes in the wood and aluminium. Make sure the rivet length is appropriate for the thickness of the materials being joined.
Step 5:
Use the rivet gun to securely fasten the rivets in place. Follow the rivet gun instructions to ensure proper use.
Step 6:
Check that all rivets are securely fastened and inspect your work for any signs of corrosion or weakness.
Benefits of Using Rivets:
Rivets provide a strong and reliable connection between the wood and the aluminium boat. They are also easy to install and do not require specialised welding equipment or skills. Additionally, rivets offer excellent waterproofing and corrosion resistance, which is crucial for applications in wet or underwater environments.
Considerations:
It is important to note that improper installation or material defects can cause rivets to loosen or fail over time. Regular inspection and maintenance of the rivets are necessary to ensure the strength and reliability of the connection. Additionally, aluminium can soften when exposed to sunlight, so it is important to consider the environmental conditions when designing and selecting rivets to avoid potential issues.
St Clair Boat Races: Schedule and Highlights for the Season
You may want to see also
Welding wood to an aluminium boat
Welding aluminium boats can be challenging, especially for beginners. Aluminium has a high thermal conductivity, which means it heats up and cools down quickly, leading to warping or burn-through. To successfully weld wood to an aluminium boat, several key factors come into play:
Selecting the Right Welding Equipment
Using the appropriate welding tools is crucial. Aluminium requires specific equipment, such as a MIG or TIG welder, to ensure a stable wire feed and reduce the risk of contamination. A welder designed for aluminium welding will help you achieve solid and clean welds.
Preparing the Aluminium Surface
Proper surface preparation is essential. Before welding, thoroughly clean the aluminium surface to remove any dirt, grease, or oxide layers. Use a stainless steel brush designed for aluminium, and clean just before welding to ensure a clean weld pool and prevent contamination that can weaken the welds.
Controlling Heat Input
To manage the heat flow and create consistent welds, control the heat input by performing short welds and allowing the aluminium to cool between passes. Preheating the aluminium slightly can also aid in heat management.
Choosing the Right Filler Material
Selecting the correct filler material is vital for strong welds. The filler rod or wire should match the base material for compatibility and strength. For most marine-grade aluminium, 5356 and 4043 filler materials are commonly used.
Welding Environment
Environmental factors can impact the welding quality. Ideally, weld in a clean, controlled environment to prevent contaminants from compromising the weld. If welding outdoors, consider using a portable welding shelter to protect the area from wind, dust, and moisture, ensuring a stable welding environment.
Practicing Proper Technique
Mastering the technique of aluminium boat welding is crucial for strong and durable welds. Maintain a consistent travel speed to ensure even heat distribution, and use steady hand movements while keeping a close eye on the weld pool. Additionally, use a push technique when welding aluminium to keep the shielding gas in the weld pool and reduce contamination risks.
Gary Muehlberger's Boat: A Fateful Twist of Fate
You may want to see also
Using Velcro to attach wood to an aluminium boat
There are a few methods you can use to attach Velcro to wood. One user on a boating forum recommends using 3M 8001 product—apply it to both surfaces, let it get tacky, stick the two surfaces together, and let dry. Another user recommends stapling the Velcro down. A third user suggests using polyurethane glue, like Gorilla Glue. First, wipe the wood with acetone, then wipe the wood and Velcro with a moist towel. Spread the glue sparingly onto the Velcro, position it onto the wood, cover with wax paper, and clamp into place.
Velcro can also be glued to aluminium. One user recommends using Araldite, a two-part epoxy glue that dries semi-pliable. Another user suggests using Wanda Fix, a similar product.
Punta Gorda Boat Parade: Date and Event Details
You may want to see also
Sealing plywood to make it watertight before attaching to an aluminium boat
Sealing plywood to make it watertight before attaching it to an aluminium boat is a process that requires several steps to ensure the plywood is protected from water damage. Here is a detailed guide on how to seal plywood and make it watertight:
Step 1: Prepare the Plywood:
Start by cleaning the plywood surface with a damp cloth to remove any dust or debris. Then, use a vacuum to remove any remaining loose particles. Fill in any cracks, holes, or imperfections with a wood filler or putty, and smooth it out with sandpaper to create an even finish. Sand the plywood with 180 to 220-grit sandpaper, stroking along the grain of the wood until the surface is smooth. For the ends and sides of the plywood, use 80-grit sandpaper as these areas tend to be rougher. Finally, wipe the plywood with a damp cloth to remove any excess dust.
Step 2: Apply a Primer (Optional):
Applying a primer is optional but recommended as it enhances the plywood's resistance to water damage. Choose a primer suitable for the type of plywood you are using and follow the manufacturer's instructions for application. Allow the primer to dry completely before proceeding to the next step.
Step 3: Choose a Waterproofing Product:
Several waterproofing products are available, each with its advantages. Epoxy sealers, varnishes, water-based paints, drying oils, and liquid latex are common options. Consider the level of protection needed, ease of application, and the specific requirements of your project when selecting a waterproofing product.
Step 4: Apply the Waterproofing Solution:
Follow the manufacturer's instructions for mixing and applying the waterproofing solution. Use a brush, roller, or sprayer to apply the product, ensuring complete coverage, especially on the edges and joints, which are vulnerable to water damage. Allow the solution to dry completely, and apply additional coats if necessary.
Step 5: Seal the Edges and Joints:
Pay extra attention to the edges and joints of the plywood as these areas are highly susceptible to water damage. Generously apply the waterproofing solution along the edges, using a brush or roller to ensure it penetrates the wood fibres. Allow it to dry completely, and apply a second coat if needed.
Step 6: Maintain and Reapply Waterproofing:
To ensure lasting protection, regularly reapply the waterproofing solution. Depending on the product used, weather conditions, and exposure to moisture, reapplication is typically recommended every 1 to 3 years. Clean the plywood surface thoroughly before reapplication, and follow the same steps for applying the waterproofing solution.
By following these steps, you can effectively seal plywood and make it watertight before attaching it to your aluminium boat, ensuring the plywood is protected from water damage and prolonging its lifespan.
Boat Batteries: Understanding Marine Power Sources
You may want to see also
Frequently asked questions
There are several ways to attach wood to an aluminum boat, including using screws, rivets, or welds. Some people also recommend using Velcro for easy access and maintenance.
It is recommended to use regular exterior plywood that you seal yourself with a sealant that does not contain copper. Pressure-treated wood should be avoided as the copper content can corrode and cause holes in the aluminum boat.
It is important to consider the environment in which the boat will be used, as certain materials may corrode or loosen over time. Creating a barrier between the wood and aluminum can help prevent corrosion, and using stainless steel or aluminum rivets can reduce the risk of dissimilar metals corroding.