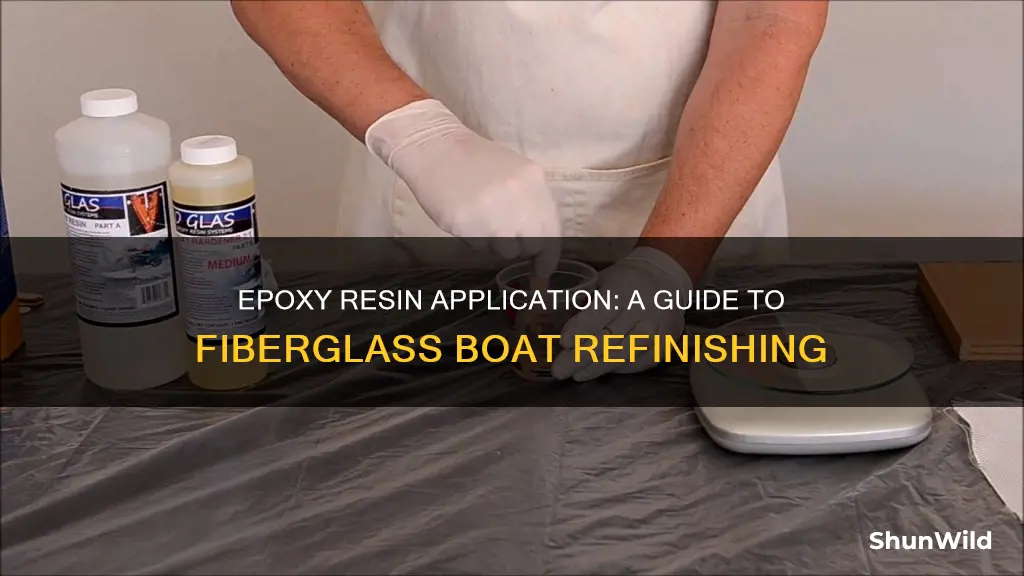
Epoxy resin is a versatile material that can be used to enhance the performance and appearance of fiberglass boats. Applying epoxy resin to a fiberglass boat involves a careful process to ensure a strong and durable bond. This guide will provide a step-by-step overview of the application process, including surface preparation, mixing and applying the epoxy, and curing techniques, to help you achieve a professional-looking finish and protect your boat's structure.
What You'll Learn
- Surface Preparation: Clean and sand the fiberglass for a smooth, dust-free base
- Mixing Epoxy: Follow manufacturer's instructions for precise resin and hardener ratios
- Application Techniques: Use a brush, roller, or sprayer for even coverage
- Curing Process: Monitor temperature and humidity for optimal curing conditions
- Finishing Touches: Sand and polish for a smooth, durable epoxy-glass bond
Surface Preparation: Clean and sand the fiberglass for a smooth, dust-free base
Before you begin the process of applying epoxy resin to your fiberglass boat, proper surface preparation is crucial to ensure a strong and durable bond. The first step in this process is to thoroughly clean the fiberglass surface. Start by rinsing the boat with clean water to remove any loose dirt, grime, or salt. Use a mild detergent or a specialized marine cleaner to further enhance the cleaning process. Pay attention to all areas, including the hull, deck, and any intricate details or crevices. Rinsing thoroughly after cleaning is essential to eliminate any detergent residue.
Once the boat is clean, it's time to focus on sanding. Sanding the fiberglass surface will create a smooth, even base for the epoxy resin. Use fine-grit sandpaper, starting with a lower grit (e.g., 400-600) to remove any remaining imperfections and roughen the surface slightly. Gradually move to higher grits (e.g., 800-1200) for a smoother finish. Ensure you work in small sections and follow the direction of the fiberglass weave to avoid creating a scratch pattern. After sanding, use a tack cloth or a damp cloth to wipe away the dust, ensuring a dust-free environment for the next steps.
The goal of this surface preparation is to create a smooth, uniform surface that the epoxy resin can easily adhere to. Proper cleaning and sanding will not only improve the bond strength but also result in a professional-looking finish. It's important to be meticulous and patient during this process, as it forms the foundation for a successful epoxy resin application. Take your time, work in a well-ventilated area, and consider wearing protective gear to ensure a safe and efficient preparation process.
Mastering the Art of Inbound Sailing: A Comprehensive Guide
You may want to see also
Mixing Epoxy: Follow manufacturer's instructions for precise resin and hardener ratios
When preparing to apply epoxy resin to a fiberglass boat, it's crucial to follow the manufacturer's instructions for mixing the epoxy resin and hardener. This ensures the correct ratio of resin to hardener is achieved, which is essential for the epoxy's structural integrity and the overall success of the repair or restoration project. The mixing process is a delicate balance, and any deviation from the recommended proportions can lead to a compromised bond or, in some cases, a hazardous reaction.
The epoxy resin and hardener are typically sold as a two-part system, with the resin being the liquid component and the hardener being a separate, often colored, powder or paste. These two components must be mixed in the exact ratio specified by the manufacturer. For example, a common ratio might be 100 parts resin to 30 parts hardener, but this can vary depending on the specific product. It's important to measure these components accurately to avoid any issues.
To begin the mixing process, you'll need to carefully measure the required amounts of resin and hardener. This can be done using measuring cups or spoons, ensuring that the units are compatible with the product's packaging. For instance, if the product requires a 1:1 ratio, you would measure out equal volumes of resin and hardener. Precision is key here; even a slight discrepancy can affect the final result.
Once the ingredients are measured, you can proceed to mix them. This is typically done by slowly adding the hardener to the resin while stirring continuously. Some manufacturers may suggest using a specific type of mixing tool, such as a stick blender or a mechanical mixer, to ensure thorough mixing. The goal is to create a smooth, homogeneous mixture without any visible separation of the two components.
After mixing, it's essential to work quickly, as epoxy resins can have a relatively short working time before they start to harden. Apply the mixed epoxy to the fiberglass boat surface promptly, ensuring that you follow the manufacturer's guidelines for application techniques and thickness. Proper mixing and application will result in a strong, durable bond, restoring the boat's structural integrity and appearance.
Is That New Boat Price Worth It?
You may want to see also
Application Techniques: Use a brush, roller, or sprayer for even coverage
When applying epoxy resin to a fiberglass boat, the choice of application technique is crucial for achieving a smooth and even finish. Here's a detailed guide on how to use brushes, rollers, and sprayers for optimal coverage:
Brush Application:
Start by ensuring the surface is clean and free of any debris. Dip your brush into the epoxy resin, allowing the excess to drip off. Begin applying the resin in a thin, even layer, working in small sections. Use long, smooth strokes, following the direction of the fiberglass weave. This method is ideal for intricate areas and provides excellent control. For larger surfaces, use a wider brush to cover more area at once. Remember to keep the brush moist with resin at all times to avoid lap marks. After applying, allow the resin to flash off slightly before adding another coat to ensure a seamless bond.
Roller Technique:
Rollers are excellent for achieving a smooth, uniform finish over larger areas. Load the roller with the epoxy resin, ensuring it's evenly coated. Start rolling in a 'W' or 'M' pattern, applying light pressure to create a consistent layer. Keep the roller moist and avoid overloading it to prevent dripping. For best results, use a roller with a suitable nap length for the thickness of your resin. This technique is efficient and provides a professional-looking finish, especially when used with a sprayer for a seamless transition between sections.
Spraying Epoxy Resin:
Spraying is a popular choice for many DIY enthusiasts as it provides a fast and even coverage. Use a high-quality airbrush or spray gun designed for epoxy resins. Thinning the resin to the manufacturer's recommended consistency is essential for optimal spray performance. Hold the spray gun 6-8 inches from the surface and apply an even, light coat. This method allows for quick coverage and is excellent for large, flat areas. However, it requires practice to avoid overspray and ensure a smooth finish. Always follow the safety guidelines when using spray equipment.
Each of these techniques offers a unique approach to applying epoxy resin, catering to different skill levels and project requirements. Practice and patience are key to mastering the art of resin application, ensuring a beautiful and durable finish for your fiberglass boat. Remember to always wear appropriate personal protective equipment (PPE) when handling epoxy resins.
Butter Boat Mechanics: How Does It Work?
You may want to see also
Curing Process: Monitor temperature and humidity for optimal curing conditions
The curing process of epoxy resin on a fiberglass boat is a critical step that requires careful monitoring of environmental conditions. Temperature and humidity play a significant role in the resin's ability to cure properly, ensuring a strong and durable bond between the epoxy and the fiberglass. Here's a detailed guide on how to monitor these factors for optimal results:
Temperature Control:
- Ideal temperature range: Epoxy resins typically cure best within a specific temperature range. This range can vary depending on the specific epoxy system used, but generally, a temperature between 68°F and 82°F (20°C to 28°C) is recommended. Warmer temperatures can accelerate the curing process, while cooler temperatures might slow it down.
- Monitoring: Place a reliable thermometer in the area where the epoxy will be applied. Ensure it is positioned away from direct sunlight or heat sources to get an accurate reading of the ambient temperature. If possible, use a data logger to record temperature changes over time, especially if the curing process takes an extended period.
- Adjusting: If the temperature is too low, you can use a heat gun or a heat lamp to gently warm the area. For higher temperatures, ensure proper ventilation to prevent overheating, which can cause the resin to become brittle or yellow.
Humidity Management:
- Optimal humidity: Epoxy resins require low humidity conditions to cure effectively. High humidity can cause the resin to become tacky or slow down the curing process, leading to potential issues like blushing or delamination. Aim for a relative humidity (RH) of below 60%.
- Measuring: Use a hygrometer to measure the humidity levels in the curing area. Place it in the same location as the thermometer to ensure consistent conditions. Hygrometers can provide real-time data, allowing you to make immediate adjustments if needed.
- Control: If humidity is too high, consider using a dehumidifier to reduce moisture in the air. Ensure proper ventilation to allow any excess moisture to escape. In dry environments, you might need to increase humidity slightly, but always monitor and control it to maintain the desired range.
During the curing process, it's essential to maintain a consistent and controlled environment. Regularly check the temperature and humidity levels, especially if the boat is in a variable climate or exposed to outdoor conditions. Adjustments can be made to the epoxy application process or the boat's storage location to accommodate different environmental factors.
Remember, proper temperature and humidity control is crucial for achieving a high-quality, long-lasting bond between the epoxy resin and the fiberglass boat. This attention to detail will contribute to a successful restoration or customization project.
Glastron Boats: Worth the Buy?
You may want to see also
Finishing Touches: Sand and polish for a smooth, durable epoxy-glass bond
When it comes to finishing the epoxy-glass bond on your boat, the final touches are crucial for both aesthetics and durability. Sanding and polishing are essential steps to ensure a smooth, seamless surface that not only looks great but also provides a strong and long-lasting bond. Here's a detailed guide on how to achieve this:
Sanding Process:
Start by using a coarse-grit sandpaper (around 40-60 grit) to remove any excess epoxy and roughen the surface of the fiberglass. This initial step is vital as it creates a better adhesion base for the epoxy. Work in small sections, gently sanding the applied epoxy to ensure an even finish. Remember to follow the direction of the fiberglass weave to avoid any unwanted patterns or marks. After the initial sanding, rinse the boat thoroughly to remove any dust or debris.
Proceed with a finer-grit sandpaper (80-120 grit) to refine the surface. This step will help to create a smoother transition between the epoxy and the fiberglass. Pay close attention to any areas where the epoxy might have pooled, as these spots may require extra sanding to ensure an even thickness. Always sand with the grain of the fiberglass to maintain its integrity. Once you've achieved a consistently smooth surface, wipe away any remaining dust with a tack cloth.
Polishing for a Professional Finish:
For the final polish, use a very fine-grit sandpaper (150-220 grit) or a polishing compound. This step will enhance the surface's shine and further improve the bond's strength. You can also use a power drill with a polishing attachment for a more efficient process. Work in circular motions, ensuring you cover the entire surface evenly. The goal is to create a mirror-like finish, which will not only look impressive but also provide a protective layer against UV rays and environmental damage.
After polishing, inspect the boat's surface for any remaining imperfections. If you notice any small scratches or imperfections, carefully touch them up with a small amount of epoxy and a fine-grit sandpaper. This final sanding will help blend the repairs seamlessly with the surrounding surface. Always ensure you wipe away any excess epoxy promptly to avoid smudges.
By following these detailed sanding and polishing techniques, you'll create a flawless epoxy-glass bond that is not only visually appealing but also highly durable, ensuring your boat's longevity.
How to Access Your Boat Radio: Cover Opening Directions
You may want to see also
Frequently asked questions
Before applying epoxy, ensure the boat's surface is clean, dry, and free from any contaminants. Remove any old paint, gelcoat, or debris using a scraper or sandpaper. It's crucial to have a smooth and clean surface for proper adhesion.
Selecting the appropriate epoxy is essential. Consider factors such as the desired hardness, flexibility, and chemical resistance. For marine applications, opt for a two-part epoxy system with a suitable viscosity for the job. Consult the epoxy manufacturer's guidelines for specific recommendations based on your boat's material and intended use.
While it is possible to apply epoxy directly to fiberglass, using a suitable primer can significantly improve adhesion and durability. A fiberglass primer will help create a bond between the epoxy and the boat's surface, ensuring a stronger and more long-lasting finish. Always follow the primer manufacturer's instructions for optimal results.
You will need a range of tools for the job, including epoxy resin and hardener, mixing containers and tools, a stir stick or spatula, gloves, and protective eyewear. Additionally, consider using a brush or roller for application, depending on the desired finish. Ensure you have proper ventilation in the workspace to avoid inhaling fumes.
Achieving a smooth finish is crucial for a professional-looking result. Start by carefully mixing the epoxy according to the manufacturer's instructions. Apply thin, even coats, allowing each layer to cure slightly before adding more. Use a heat gun or lamp to speed up the curing process and ensure a seamless bond between coats. Practice good technique and take your time to avoid air bubbles and imperfections.