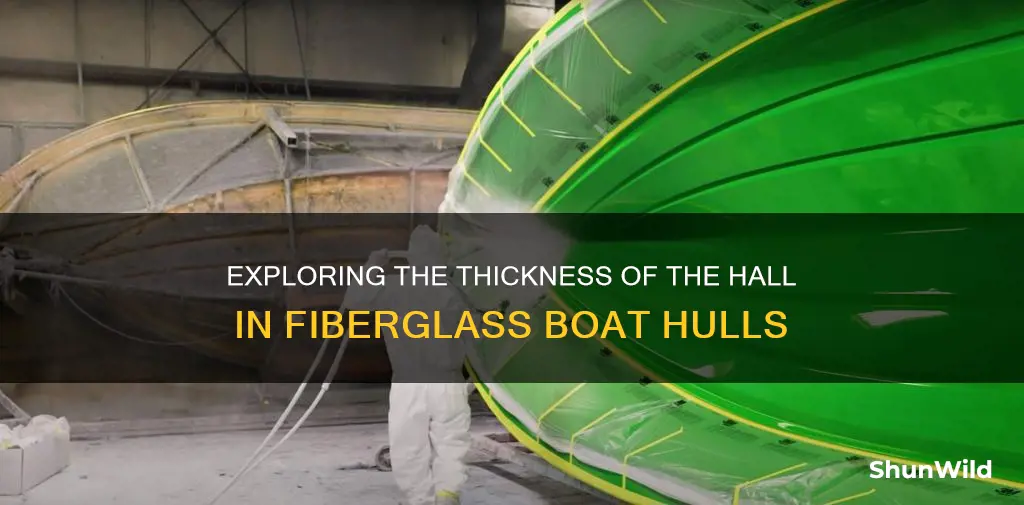
When it comes to fiberglass boat hulls, the thickness of the hull, including the hall (a term often referring to the hull's structural core), is a critical factor in determining the boat's strength, durability, and overall performance. The hall's thickness can vary depending on the specific design, intended use, and manufacturing process. Understanding this dimension is essential for boat owners, manufacturers, and enthusiasts to ensure the vessel's structural integrity and safety on the water. This paragraph sets the stage for a detailed exploration of the factors influencing the hall's thickness and its implications for fiberglass boat hulls.
Characteristics | Values |
---|---|
Standard Thickness | 1/8 inch (3.175 mm) to 3/8 inch (9.525 mm) |
Thickness Range | Varies depending on the boat's size, design, and intended use |
Factors Affecting Thickness | - Boat size and weight - Type of fiberglass used - Structural requirements - Waterline load - Environmental conditions |
Advantages of Thicker Hulls | Increased strength, durability, and structural integrity |
Thinner Hulls | Lighter weight, potentially better fuel efficiency, and easier to handle |
Industry Standards | Typically, 1/4 inch (6.35 mm) for smaller boats and 3/8 inch (9.525 mm) for larger, heavier vessels |
Customization | Thickness can be adjusted based on specific boat requirements and builder preferences |
What You'll Learn
- Fiberglass Thickness Variations: Hall thickness varies by boat design and size
- Reinforcement Techniques: Reinforcement methods impact hall thickness
- Weight Considerations: Thicker halls provide more structural integrity but increase weight
- Cost Implications: Thicker halls can significantly increase manufacturing and maintenance costs
- Safety Standards: Compliance with safety regulations dictates minimum hall thickness
Fiberglass Thickness Variations: Hall thickness varies by boat design and size
The thickness of the hall, or hull, on a fiberglass boat is an important consideration in boat construction and design. The hall is the structural element that forms the bottom and sides of the boat, and its thickness can vary significantly depending on the specific boat design and size. This variation in thickness is crucial to ensure the boat's structural integrity, stability, and overall performance.
In general, the hall thickness is determined by the boat's intended use, load-bearing capacity, and structural requirements. Smaller boats, such as dinghies or smaller recreational vessels, often have thinner halls compared to larger boats like yachts or commercial vessels. This is because smaller boats typically carry less weight and are designed for lighter use, so thinner halls can provide sufficient structural support without adding excessive weight. For instance, a typical fiberglass dinghy might have a hall thickness of around 1/8 inch to 3/16 inch, which is relatively thin but adequate for its intended purpose.
As boat size increases, so does the required hall thickness. Larger boats need thicker halls to withstand greater loads, including the weight of the boat itself, passengers, fuel, and equipment. For example, a cruising yacht may have a hall thickness of 3/16 inch to 1/2 inch or more, depending on its size and the materials used in its construction. Thicker halls in larger boats provide increased strength and rigidity, ensuring the vessel can handle the stresses of sailing and cruising.
The design of the boat also plays a significant role in determining hall thickness. Different boat designs have unique structural needs. For instance, a catamaran, with its two hulls, may require thicker halls to distribute the loads evenly and maintain stability. In contrast, a monohull design might have thinner halls in certain areas, such as the keel, while thicker halls in other areas, like the gunwale, to provide the necessary structural support.
Additionally, the type of fiberglass used can influence hall thickness. Different fiberglass composites have varying properties, and the choice of material can impact the overall thickness required. For example, a boat builder might opt for a thicker hall when using a high-strength, low-weight fiberglass composite to ensure optimal performance and safety.
In summary, the thickness of the hall on a fiberglass boat is a critical aspect of boat design and construction. It varies based on boat size, intended use, and structural requirements. Understanding these variations is essential for boat builders and owners to ensure the vessel's safety, durability, and overall performance.
Understanding Boat Toilets: A Guide to Marine Sanitation
You may want to see also
Reinforcement Techniques: Reinforcement methods impact hall thickness
Reinforcement techniques play a crucial role in determining the thickness of the hull on a fiberglass boat. The hull, which forms the main structure of the vessel, needs to be reinforced strategically to ensure its strength, durability, and overall safety. The thickness of the hull is a critical factor in achieving these goals, as it directly influences the boat's ability to withstand various loads and environmental conditions.
One common reinforcement method is the use of stringers and frames. Stringers are longitudinal members running along the hull, providing additional strength and stability. They are typically placed at regular intervals and can be made of various materials, such as wood, aluminum, or even fiberglass itself. By adding these stringers, the hull's structural integrity is enhanced, allowing for a thinner yet stronger hull design. Frames, on the other hand, are transverse members that provide lateral support. They are often used in conjunction with stringers to create a robust framework, ensuring the hull can handle the stresses of sailing and cruising.
Another reinforcement technique involves the use of bulkheads and chines. Bulkheads are vertical partitions within the hull that prevent the spread of damage in the event of a collision or grounding. They are strategically placed to provide additional strength and safety. Chines, which are curved or angled members, are often used in conjunction with bulkheads to further reinforce the hull's structure. These techniques help distribute the forces acting on the hull, reducing the likelihood of structural failure.
The choice of reinforcement materials is also essential. Modern fiberglass boats often utilize advanced composites, such as carbon fiber or Kevlar, which offer exceptional strength-to-weight ratios. These materials can be strategically placed in critical areas, such as the hull's bottom or sides, to reinforce weak points and improve overall structural integrity. Additionally, the use of epoxy resins and specialized bonding techniques ensures that the reinforcement materials are securely integrated into the hull, creating a seamless and robust structure.
In summary, reinforcement techniques significantly impact the thickness of the hull on a fiberglass boat. By employing stringers, frames, bulkheads, and chines, along with advanced composite materials, boat manufacturers can create sturdy and safe vessels. These reinforcement methods allow for a thinner yet stronger hull design, ensuring optimal performance and longevity in various marine environments. Understanding these techniques is vital for anyone involved in the design, construction, or maintenance of fiberglass boats.
Gaff Rigged Boats: Upwind Sailing Explained
You may want to see also
Weight Considerations: Thicker halls provide more structural integrity but increase weight
When it comes to fiberglass boat hulls, the thickness of the hall (also known as the stringer or bulkhead) is a critical factor in determining the boat's structural integrity and overall weight. The hall is a structural component that runs along the length of the hull, providing support and strength to the boat's frame. While thicker halls offer enhanced structural benefits, they also contribute to the boat's overall weight, which is an important consideration for boat owners and builders.
The primary reason for the weight increase with thicker halls is the additional material required to achieve the desired thickness. Fiberglass, being a lightweight composite material, can be manipulated to create a sturdy structure, but it also needs reinforcement in certain areas. The hall, being a critical structural element, often requires a specific thickness to withstand the stresses and loads experienced during boating. As the thickness increases, so does the amount of material used, leading to a higher overall weight for the boat. This is especially significant in fiberglass boats, where weight management is crucial for performance and fuel efficiency.
However, the trade-off between structural integrity and weight is a delicate balance. Thicker halls provide more robust support, especially in areas prone to stress, such as the hull's sides and bottom. This added strength can enhance the boat's ability to handle rough waters, heavy loads, or even accidental impacts. For example, a thicker hall along the hull's sides can better distribute the forces exerted by waves, preventing excessive flexing or deformation of the fiberglass structure. Similarly, a robust hall at the bottom of the hull can provide additional protection against damage from rocks, coral, or other underwater obstacles.
Despite the benefits of increased structural integrity, the weight implications cannot be overlooked. Every additional pound on a boat affects its performance, fuel consumption, and overall handling. For instance, a heavier boat may require more powerful engines to achieve similar speeds, leading to increased fuel costs. Additionally, the extra weight can make the boat feel sluggish and less responsive, especially in lighter wind or calm conditions. Therefore, boat designers and builders must carefully consider the hall's thickness, balancing the need for structural strength with the practical constraints of weight.
In summary, the thickness of the hall in a fiberglass boat hull is a critical design choice. While thicker halls offer improved structural integrity, they also contribute to the boat's weight, impacting performance and fuel efficiency. Finding the optimal thickness involves understanding the specific requirements of the boat's intended use, the materials available, and the trade-offs between strength and weight. By carefully considering these factors, boat manufacturers can create vessels that are both sturdy and efficient, ensuring a safe and enjoyable boating experience.
Stern-In Docking: Mastering the Art of Boat Control
You may want to see also
Cost Implications: Thicker halls can significantly increase manufacturing and maintenance costs
The thickness of the hall, or the hull, on a fiberglass boat is a critical design consideration that impacts both the manufacturing process and long-term maintenance. While a thicker hull offers enhanced structural integrity and potentially better performance, it also brings a range of cost implications that boat manufacturers and owners must carefully evaluate.
One of the primary cost factors is the manufacturing process itself. Creating a thicker hull requires more material, which translates to higher raw material costs. Fiberglass, the primary material used for boat hulls, is typically supplied in rolls or sheets, and the thicker the desired hall, the more material is required. This increased material usage directly impacts production costs, as manufacturers need to purchase larger quantities of raw materials and may also need to adjust their production techniques to accommodate the thicker dimensions.
Additionally, the manufacturing process itself may become more complex and time-consuming. Thicker hulls often require more intricate molding techniques, additional layers of fiberglass, and potentially more skilled labor. This complexity can lead to extended production times, further increasing manufacturing costs. The challenge lies in balancing the structural benefits of a thicker hall with the practical and financial constraints of the manufacturing process.
From a maintenance perspective, thicker halls can also present cost implications. Over time, thicker hulls may require more frequent inspections and repairs due to the increased stress and potential for damage. The thicker material can make it more challenging to access certain areas of the hull for maintenance, potentially requiring specialized equipment and techniques. This can result in higher maintenance costs, especially for boat owners who may need to engage professional services for repairs and upkeep.
Furthermore, the thicker hall's design may impact the boat's performance and fuel efficiency. A thicker hull can affect the boat's weight distribution and hydrodynamics, potentially leading to increased fuel consumption. While this is a secondary consideration, it highlights the need for a comprehensive cost-benefit analysis, ensuring that the structural advantages of a thicker hall outweigh the potential drawbacks in terms of operational expenses.
In summary, while thicker halls offer improved structural integrity, the cost implications are significant. Manufacturers must carefully manage raw material usage, production techniques, and labor costs to ensure that the thicker design is feasible within their budget constraints. For boat owners, understanding the maintenance requirements and potential performance trade-offs associated with thicker hulls is essential to making informed decisions regarding their vessel's design and upkeep.
Best Transom Transducer Placement for Bass Boats
You may want to see also
Safety Standards: Compliance with safety regulations dictates minimum hall thickness
The thickness of the hull, particularly the hall, is a critical factor in ensuring the safety and structural integrity of a fiberglass boat. Compliance with safety regulations is essential to guarantee that the vessel can withstand various operating conditions and potential impacts. These regulations dictate minimum hall thickness to provide a robust and secure foundation for the boat's structure.
Safety standards for boat hulls are set by maritime authorities and organizations to minimize the risk of accidents and ensure the well-being of passengers and crew. The hall, being a structural element that connects the hull to the deck, plays a vital role in distributing loads and maintaining the boat's shape. Therefore, adhering to the prescribed minimum thickness is imperative.
The minimum hall thickness is determined based on several factors, including the boat's size, intended use, and expected environmental conditions. For instance, commercial vessels or those operating in rough waters may require thicker halls to withstand the demands of their specific environments. These regulations are designed to account for potential hazards, such as collisions, grounding, or extreme weather events, ensuring that the boat can absorb and distribute forces effectively.
Compliance with these safety standards is not just a legal requirement but also a fundamental aspect of responsible boat ownership and operation. By adhering to the minimum hall thickness, boat manufacturers and owners can significantly reduce the likelihood of structural failures, which could lead to dangerous situations. Regular inspections and maintenance are also crucial to identify and address any potential issues related to hall thickness or other structural components.
In summary, understanding and meeting the safety regulations regarding hall thickness is essential for the overall safety of a fiberglass boat. It ensures that the vessel can handle various challenges and provides a secure environment for passengers and crew. Boat owners and operators should familiarize themselves with these standards to maintain compliance and promote a safer boating experience.
Exploring the Beam and Draft of Sail Boats
You may want to see also
Frequently asked questions
The thickness of the hull on a fiberglass boat can vary depending on the specific design, intended use, and manufacturing process. Generally, the hull thickness ranges from 1/4 inch (6.35 mm) to 3/4 inch (19.05 mm) or even thicker for heavy-duty or custom-built boats.
Hull thickness plays a crucial role in a boat's performance and safety. Thicker hulls provide better structural integrity, making the boat more rigid and less prone to flexing or deforming under pressure. This can result in improved handling, reduced vibration, and enhanced stability, especially in rough waters.
Yes, a thicker hull offers several benefits. It can increase the boat's buoyancy, making it more stable and less likely to sink. Thicker hulls also contribute to better insulation, reducing noise and vibrations from the water, and providing a more comfortable ride for passengers.
In some cases, boat owners or manufacturers can modify the hull thickness. This might involve adding additional layers of fiberglass or composite materials during the construction process. However, significant changes to the hull thickness should be done by professionals to ensure structural integrity and safety.
Thicker hulls generally add more weight to the boat, which can affect its overall performance and fuel efficiency. Heavier boats may require more powerful engines to achieve similar speed and acceleration. Balancing the hull thickness with other design factors is essential for optimal boat performance.