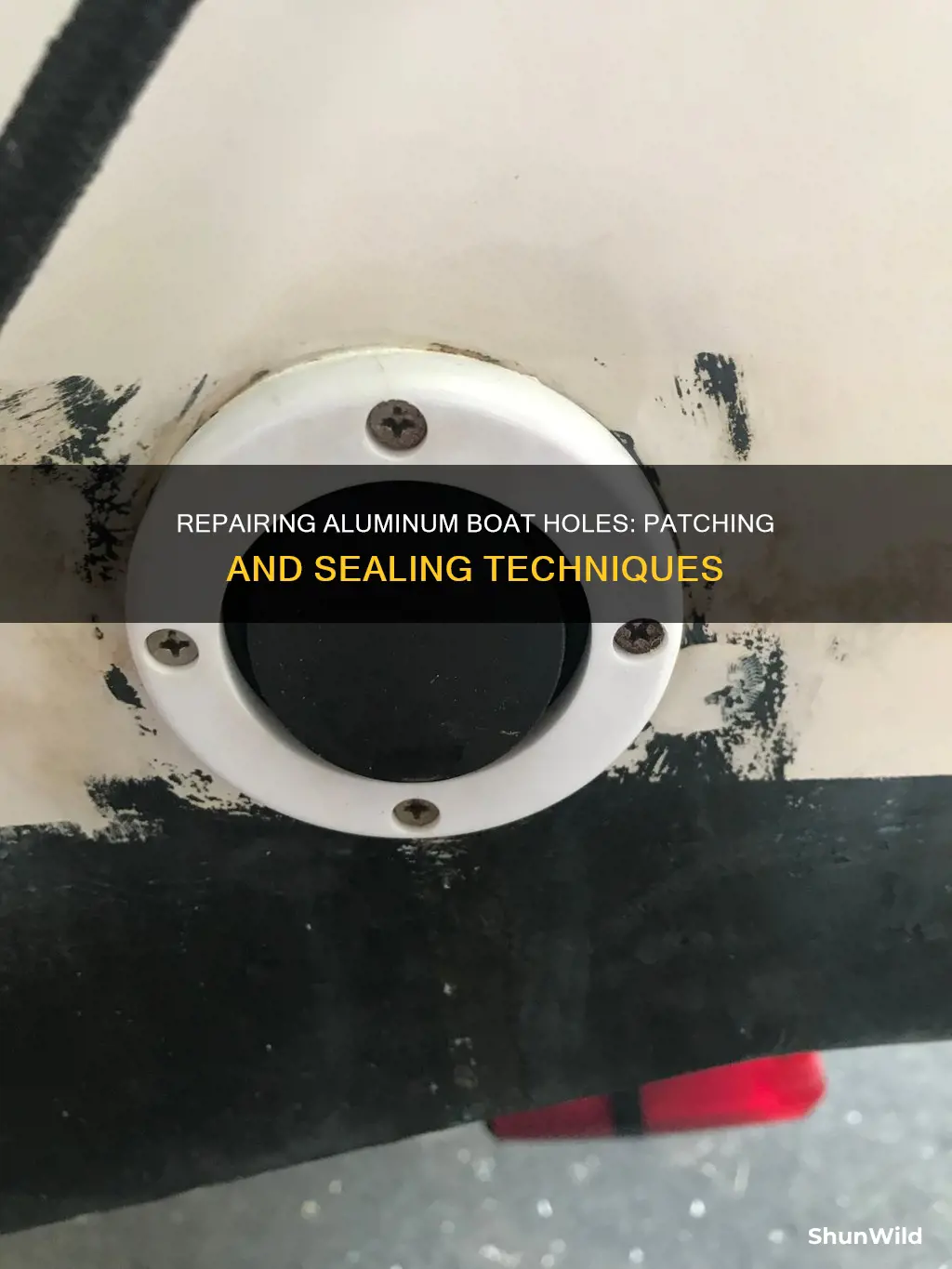
Owning a boat can be a lot of fun, but it also comes with maintenance and repairs. If you find yourself with holes in your aluminium boat, there are a few ways to fix them. You can take your boat to a welder to have the holes shut with a spot weld, or you can try to fix it yourself with an epoxy resin or putty. The latter is a more affordable option, but it's important to follow the instructions carefully and prepare the surface of the boat properly for the epoxy to adhere.
What You'll Learn
Using marine epoxy to seal holes
Sealing holes in an aluminium boat can be done in a number of ways, but one of the most popular methods is to use marine epoxy. This method is often cheaper and safer than welding and can be done without the need for professional help.
Firstly, it is important to prepare the area to be sealed. Clean the surfaces with acetone and then roughen the areas with sandpaper. Clean the areas again with acetone to ensure the surface is ready for the epoxy.
When applying the epoxy, make sure to follow the instructions on the packaging. In general, you will need to combine the two ingredients in the correct ratio (often 1:5) and use a putty knife or epoxy spreader to apply the epoxy. Work the epoxy into the scratches and small dings, and smooth it out to remove any air bubbles. Leave the epoxy to cure overnight or for the time suggested by the manufacturer.
The next day, check that the epoxy has cured properly. If it is still soft, you may need to apply heat to help it harden. Once the epoxy is cured, you can sand and paint over it if desired.
Registering Your Aluminum Boat: What You Need to Know
You may want to see also
Welding holes shut
Welding is one of the most permanent ways to seal holes in an aluminium boat. However, it can be costly and may not always be the best option. For instance, if the holes are in an area of the boat with flotation material, this could catch fire during welding. Similarly, if the holes are near the fuel tank, welding could cause an explosion.
If you do decide to weld the holes shut, it is important to find a welder with experience working with aluminium boats. One option is to take the boat to a weld shop and have a professional weld the holes shut with a TIG welder. This will likely be the most expensive option, but it will ensure that the job is done correctly and safely.
Another option is to use a brazing rod, such as Alumiweld, and a propane torch to fill the holes. This method can be purchased for around $20 and can be done at home, but it may not be as strong or permanent as a professional weld.
Before welding, it is important to clean and prepare the area around the holes. This includes hammering out the metal to close the hole as much as possible, sanding or grinding the area, and cleaning it with a solvent like acetone.
If welding is not an option, there are several other ways to seal holes in an aluminium boat. These include using epoxy putty, such as JB Weld or Marine Tex, or a marine sealant like 3M 5200. These methods are generally cheaper and easier to do yourself, but they may not be as permanent or strong as a weld.
Dream Boat Investment: What It Takes to Buy a 100K Vessel
You may want to see also
Filling holes with marine calk or silicone
Before proceeding with the application, it is essential to prepare the surface of the aluminium boat. Clean the area around the holes thoroughly to remove any dirt, grease, or debris. You can use a stainless steel brush to scrub the surface and create a smooth, even finish. Additionally, you may need to sand the area to roughen the surface, which will help the calk or silicone adhere better.
Once the surface is prepared, you can start filling the holes. If the holes are small, simply apply the marine calk or silicone directly into the holes using a caulking gun or a putty knife. Ensure that the product fills the holes completely and smoothen the surface for a neat finish. If the holes are larger, you may need to use screws or rivets in conjunction with the calk or silicone for a more secure seal.
For bigger holes, you can insert a screw or a rivet that fits snugly into the hole. Apply a generous amount of marine calk or silicone over and under the screw or rivet to create a watertight seal. Alternatively, you can coat the screw or rivet with the product before inserting it into the hole. This will ensure that the hole is properly filled and sealed.
After applying the marine calk or silicone, allow it to cure and harden according to the manufacturer's instructions. This may take several hours or even a day, depending on the product and environmental conditions. Once cured, inspect the patched area to ensure that it is securely sealed and there are no leaks. If necessary, you can sand the patched area to smoothen any rough surfaces or apply additional calk or silicone for a neater finish.
Boat Launching at Kenmore: Open or Closed?
You may want to see also
Using a TIG welder to fix small holes
Once the area is prepared, you can begin the welding process. Set up your TIG welder and heat the surrounding area to prevent the cold metal from leaching heat from your work area. Then, use the TIG welder to heat the tip of an aluminium brazing rod. Dip the rod into a jar of flux, which will liquefy at 600 degrees Celsius, and melt the flux onto the weld area. Begin depositing the rod and add more flux as needed. The flux will help with the bonding process as you apply the rod.
After welding, you'll need to smooth out the weld and apply a fairing compound to improve the hydrodynamics of the boat and create a clean finish. Sand the edges of the weld to remove any roughness, and then apply a mixture of G/flex epoxy and low-density filler to the area. This will smooth out the weld and create a fair finish.
Finally, apply a mixture of G/flex epoxy and grey pigment to the area to camouflage the repair. This will help to conceal the weld and create a more uniform appearance.
Aligning Your Boat's Drive Shaft: A Step-by-Step Guide
You may want to see also
Applying heat gun epoxy
To seal holes in an aluminium boat using a heat gun and epoxy, you will need to follow a few key steps. Firstly, you will need to shape and clean the metal surface. This involves hammering out the torn aluminium or using an auto-body or bucking dolly to get the hull back to its original shape. Any torn edges can be cut away to help the aluminium lie flat, and you can reduce the chance of further cracking by drilling stopper holes at the end of each tear. Next, use 120-grit sandpaper to soften the aluminium edges, and a coarse bristle disc to remove paint from both the inside and outside of the hull. This will create a suitable bonding surface area. Finally, abrade the surface with 80-grit sandpaper to complete the preparation.
Once the surface is prepared, you can create your patches. For the outside of the hull, cut a single piece of Episize Glass Fabric (either #743 280g/m2 or #745 10 oz, depending on your source). For the inside, cut three pieces in diminishing sizes. It is recommended that you allow for a 2-inch overlap around the hole to give your materials space to bond.
Brush both surfaces of the canoe with G/flex 650 epoxy, working the adhesive into any scratches and dings. You can fill small holes and cutaways with a thickened mixture of 406 Colloidal Silica and the residual adhesive. Lay your patch pieces on plastic and wet them thoroughly with the G/flex 650.
Apply the single patch to the outside of the hole, smoothing it into the thickened mixture. Stack the three inner patches and use a squeegee to ensure no air is trapped. Centre the stack of patches over the hole on the inside of the hull and carefully lay it into place, lightly squeegeeing over the area to remove any remaining air.
When you are satisfied with the placement and shape of your repair, leave it to cure overnight. The next day, you can ground the edges of the patches to remove any roughness and apply a mixture of G/flex and 407 Low-Density Filler to fair the patches inside and out. This will smooth the outside of your boat and provide better scuff resistance on the inside. Once the fairing mixture has cured, you can apply a mix of 503 Grey Pigment to help camouflage your repair.
Boating Near Orcas: What's the Legal Status?
You may want to see also
Frequently asked questions
The best way to seal holes in an aluminum boat is to take it to a weld shop and have the holes welded shut with a TIG welder. If this is not possible due to cost or accessibility, small holes can be filled with epoxy putty or marine epoxy.
First, hammer the aluminum out to its original shape. Cut away any torn edges to allow the aluminum to lie flat. Drill stopper holes at the end of each tear to prevent cracks from forming. Softening the edges of the aluminum with 120-grit sandpaper and using a coarse bristle disc to remove paint, creating a sound bonding surface. Finally, abrade the surface with 80-grit sandpaper.
There are several options available for marine-grade epoxies, including JB Weld, G/flex Epoxy, and PC Metal.
Mix the two-part epoxy putty by rolling equal parts of A and B together until the color is uniform. Press and smooth the putty into the hole and surrounding area, from both sides if possible. If the hole is a crack, drill small holes at each end to prevent the crack from spreading.